2009年2月アーカイブ
Failure
製造した品目や購入する品物が品質基準からはずれることをいい、基準外となった品物を不良品と呼ぶ。 不良は、製品の機能に及ぼす影響の重要度により、次のように分類される。
●致命不良:ガス器具のガスもれや自動車のブレーキの欠陥などのような、使用者に危険であったり、製品の機能そのものが失われるといった致命的な欠点をいう。
●重不良:電気器具の断線などのような、製品が目的通り機能せず、使用できない原因となる欠点をいう。
●軽不良:製品性能を悪くしたり、効率を下げる原因となるような欠点をいう。また、製品寿命を短くするような場合もこれに含まれる。
●微不良:軽不良のような製品の寿命や性能、効率への影響はまったくないが、外装のキズ、塗装ムラといった製品規格や仕様に合致しないような欠点をいう。
製造した品目や購入する品物が品質基準からはずれることをいい、基準外となった品物を不良品と呼ぶ。 不良は、製品の機能に及ぼす影響の重要度により、次のように分類される。
●致命不良:ガス器具のガスもれや自動車のブレーキの欠陥などのような、使用者に危険であったり、製品の機能そのものが失われるといった致命的な欠点をいう。
●重不良:電気器具の断線などのような、製品が目的通り機能せず、使用できない原因となる欠点をいう。
●軽不良:製品性能を悪くしたり、効率を下げる原因となるような欠点をいう。また、製品寿命を短くするような場合もこれに含まれる。
●微不良:軽不良のような製品の寿命や性能、効率への影響はまったくないが、外装のキズ、塗装ムラといった製品規格や仕様に合致しないような欠点をいう。
検査数量により分類される検査の1つの方法で、適当なサンプルを摘出して行う検査のことをいう。この方法は、抜取検査のように確率基準にこだわらず行われ、品質が安定している品目や、それほど重要でない品目に用いられる。
関連用語: 検査
関連用語: 検査
検査場所により分類される検査方法の1つで、検査員が適時、製造現場を巡回して品目を検査する方法をいう。したがって、一定の検査工程は設けられない。これは、検査場所への品目の移動が不要となり、製造リードタイムの短縮につながる。
関連用語: 検査
関連用語: 検査
Inspection between Processes
製造過程で行われる検査のことで、ある工程から次の工程へ移る際に行う内作品の検査をいう。これは、不良品が次の工程に流れて損失を生じることを防ぐための目的で行われる。
関連用語: 検査
製造過程で行われる検査のことで、ある工程から次の工程へ移る際に行う内作品の検査をいう。これは、不良品が次の工程に流れて損失を生じることを防ぐための目的で行われる。
関連用語: 検査
Claim
出荷した製品が、規格外の品質であったり、またそのものがもっている機能を十分果たさない場合に発生する顧客の不満をいう。クレームは、顕在クレームと潜在クレームとに分けられる。顕在クレームとは、顧客から販売店やメーカーに持込まれたクレームであり、潜在クレームとは、顧客の不満が販売店やメーカーに持込まれずに顧客に内在しているクレームである。前者は、顧客の対応やその原因分析および品質改善が必要となり、後者は、市場調査などにより顧客の内在している不満を顕在化し製品に反映することが必要となる。
出荷した製品が、規格外の品質であったり、またそのものがもっている機能を十分果たさない場合に発生する顧客の不満をいう。クレームは、顕在クレームと潜在クレームとに分けられる。顕在クレームとは、顧客から販売店やメーカーに持込まれたクレームであり、潜在クレームとは、顧客の不満が販売店やメーカーに持込まれずに顧客に内在しているクレームである。前者は、顧客の対応やその原因分析および品質改善が必要となり、後者は、市場調査などにより顧客の内在している不満を顕在化し製品に反映することが必要となる。
Control Chart
品質管理図の略で、品物の寸法、硬さ、キズ、歩留などの特性を調べることによって、そのものが属している品物の集団についての情報を手軽にかつ経済的に得るための道具である。管理図の目的は、生産の条件を安定した状態、つまり統計的管理状態に保つことにある。このため、上方と下方の管理限界を設け、管理状態がこの内側にあり安定しているか、それとも線の外側に出ていて異常な状態かを見分ける。管理図は、管理しようとする品質特性によって、図のように分けられる。
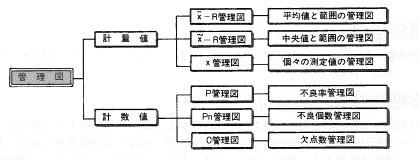
品質管理図の略で、品物の寸法、硬さ、キズ、歩留などの特性を調べることによって、そのものが属している品物の集団についての情報を手軽にかつ経済的に得るための道具である。管理図の目的は、生産の条件を安定した状態、つまり統計的管理状態に保つことにある。このため、上方と下方の管理限界を設け、管理状態がこの内側にあり安定しているか、それとも線の外側に出ていて異常な状態かを見分ける。管理図は、管理しようとする品質特性によって、図のように分けられる。
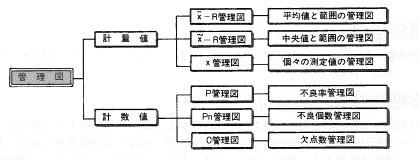
x-R Chart
x-R(エックス・バー・アール)管理図は、工程で管理する品質特性値が長さ、重量、時間、電気抵抗、引張りの強さ、純度などの場合に用いる。平均値の変化を管理するためにx管理図を使い、バラツキの変化を管理するためにR管理図を使用する。x-R管理図は、次の手順で作成する。
①データのとり方:検査ロット(k)をつくり、各ロットから4~5個の試料(n)をとり品質特性値を測定する。
②平均値xと範囲Rの計算:ロットごとの平均値xと範囲Rを求める。
③管理限界の計算:管理限界線として中心線(CL)、上方管理限界(UCL)、下方管理限界(LCL)を計算する。またこの時、x-R管理図の管理限界係数を使用する。
④x-R管理図の見方:各ロットの点が管理限界内にあれば、製造工程は統計的管理状態であり、点が限界の外に出たら異常が発生したと判定し原因を調べ処置する。x管理図で管理限界より外に点が出た場合、長さ7以上の連が現われた場合、それに7点連続して上昇したり、下降したりしている場合などはすべて異常であり、作業方法の変更や工具・機械の摩耗等の原因が考えられる。またR管理図で点が上方限界を超えた場合はバラツキが大きくなったことを示している。原因を早急に見つけ、将来同じことが発生しないよう処置をとることが大切である。
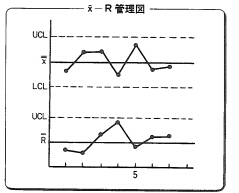
関連用語: 管理図
x-R(エックス・バー・アール)管理図は、工程で管理する品質特性値が長さ、重量、時間、電気抵抗、引張りの強さ、純度などの場合に用いる。平均値の変化を管理するためにx管理図を使い、バラツキの変化を管理するためにR管理図を使用する。x-R管理図は、次の手順で作成する。
①データのとり方:検査ロット(k)をつくり、各ロットから4~5個の試料(n)をとり品質特性値を測定する。
②平均値xと範囲Rの計算:ロットごとの平均値xと範囲Rを求める。

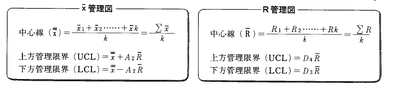
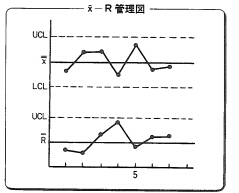
関連用語: 管理図
Line
設備の編成形式の1つで、各機械設備における仕事(ジョブ)の作業時間が同じ場合、その流れを1つとして編成した工程もしくはショップをいう。これは、ジョブの流れが一定で、たえず繰返し生産が行われ、かつ生産量が多い場合に有効である。ショップ内の流れの管理はほとんど必要なくなるが、製品の多様化への対応は難しくなる。また、投入サイクルタイムと各作業時間は一致し、ジョブの投入順序がそのまま完成順序となる。
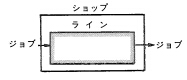
関連用語: 工程
設備の編成形式の1つで、各機械設備における仕事(ジョブ)の作業時間が同じ場合、その流れを1つとして編成した工程もしくはショップをいう。これは、ジョブの流れが一定で、たえず繰返し生産が行われ、かつ生産量が多い場合に有効である。ショップ内の流れの管理はほとんど必要なくなるが、製品の多様化への対応は難しくなる。また、投入サイクルタイムと各作業時間は一致し、ジョブの投入順序がそのまま完成順序となる。
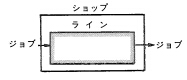
関連用語: 工程
Preventive Maintenance PM
"設備の予防医学"といわれる。すなわち、人間の病気予防と同じで、故障の発生する前に予備品の交換を行い、故障を防ぐ方法である。まず、日常保全(清掃、給油、小修正など)を行って設備の劣化を遅らせるとともに、運転ミスをなくす努力や訓練が必要である。さらに、定期点検を実施して劣化の傾向を把握し、部品や工具の修理、交換や予備品の整備を計画的に行わなければならない。事故が発生してから修理する事後保全に比べて、一般に経済的である。予防保全は、保全費と劣化損失との和を最小にすることで、経済性の向上が図られる。
予防保全(PM:Preventive Maintenance)は、1951年(昭和26年)にアメリカから導入され、現在では生産保全(PM:Productive Maintenance)へと進展している。
関連用語: 設備保全
"設備の予防医学"といわれる。すなわち、人間の病気予防と同じで、故障の発生する前に予備品の交換を行い、故障を防ぐ方法である。まず、日常保全(清掃、給油、小修正など)を行って設備の劣化を遅らせるとともに、運転ミスをなくす努力や訓練が必要である。さらに、定期点検を実施して劣化の傾向を把握し、部品や工具の修理、交換や予備品の整備を計画的に行わなければならない。事故が発生してから修理する事後保全に比べて、一般に経済的である。予防保全は、保全費と劣化損失との和を最小にすることで、経済性の向上が図られる。
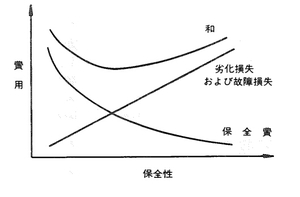
関連用語: 設備保全
Maintenance Prevention MP
設備は、故障しない設備が望ましい。また、故障した場合には、速やかに修理できることが望ましい。これらの要件に対し、設備を計画する段階から考慮し、信頼性の高い、保全性のすぐれた設備の設計、製作、設置を行う方法を保全予防という。改良保全から発展した保全の方法である。
関連用語: 設備保全
設備は、故障しない設備が望ましい。また、故障した場合には、速やかに修理できることが望ましい。これらの要件に対し、設備を計画する段階から考慮し、信頼性の高い、保全性のすぐれた設備の設計、製作、設置を行う方法を保全予防という。改良保全から発展した保全の方法である。
関連用語: 設備保全
Split Order
オーダー分割によって発生した新しいオーダーをいう。分割オーダーは、元のオーダーとは別オーダーとして、通常のオーダーと同様に扱うが、分割されたという実績を把握するために、旧オーダーのオーダー番号が識別できるよう、オーダーの項目内容としてもつ。
関連用語: オーダー
オーダー分割によって発生した新しいオーダーをいう。分割オーダーは、元のオーダーとは別オーダーとして、通常のオーダーと同様に扱うが、分割されたという実績を把握するために、旧オーダーのオーダー番号が識別できるよう、オーダーの項目内容としてもつ。
関連用語: オーダー
Loading 山積
負荷とは、作業量のことで、各品目を製造するために必要な工程に作業量を割り振ることを負荷山積という。
負荷山積は、単に山積とも略され、製造計画の能力所要量計画(CRP:Capacity Requirements Planning)の中に位置付けられる。これはMRPにおいて計画された各品目を受け、これを製造するための工程にまず展開する。このことは一般に工程展開といわれる。次に展開された工程に負荷の山積を行う。山積は通常、時間で積まれ、段取時間と実作業時間がその対象となる。実作業時間は、製造ロットの単位で設定されている場合と、品目1単位当たりの実作業時間で設定されている場合がある。前者はそのままの時間を負荷として積むが、後者は製造数と実作業時間を掛けて、製造単位当たりの実作業時間を算出して山積を行う。
また、算出された負荷を積む対象期間の決め方には、最早開始日と最遅開始日の方法がある。このどちらかの基準日を選択して山積することにより、工程別、期間別に負荷を積むことができる。
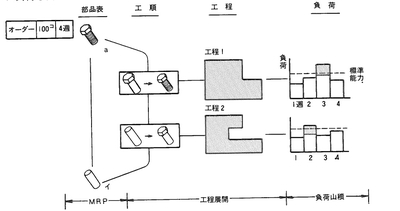
関連用語: 能力所要量計画
負荷とは、作業量のことで、各品目を製造するために必要な工程に作業量を割り振ることを負荷山積という。
負荷山積は、単に山積とも略され、製造計画の能力所要量計画(CRP:Capacity Requirements Planning)の中に位置付けられる。これはMRPにおいて計画された各品目を受け、これを製造するための工程にまず展開する。このことは一般に工程展開といわれる。次に展開された工程に負荷の山積を行う。山積は通常、時間で積まれ、段取時間と実作業時間がその対象となる。実作業時間は、製造ロットの単位で設定されている場合と、品目1単位当たりの実作業時間で設定されている場合がある。前者はそのままの時間を負荷として積むが、後者は製造数と実作業時間を掛けて、製造単位当たりの実作業時間を算出して山積を行う。
また、算出された負荷を積む対象期間の決め方には、最早開始日と最遅開始日の方法がある。このどちらかの基準日を選択して山積することにより、工程別、期間別に負荷を積むことができる。
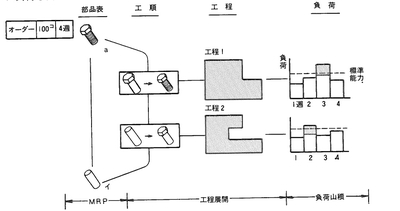
関連用語: 能力所要量計画
Standard Capacity
通常、工程ででき得る能力をいう。一般に"時間"で表わされる。標準能力は、工程における機械の能力(機械能力)や人の能力(人的能力)に従って設定される。機械能力は、工程に設置されている機械の台数と、機械の1日当たりの標準稼働時間とを掛け合わせて求めることができる。また、人的能力は、工程の作業員と、作業員の1日当たりの標準作業時間とを掛け合わせて求められる。
状況に応じて、機械の能力か人の能力かのどちらかが制約となるが、この制約となる工程能力が標準能力として設定される。たとえば、機械設備や金型などの数に限りがある場合、機械能力が制約となり、標準能力として設定されることが多い。また、組立工程のような一般に手作業が主体となる工程や、熟練工を要する工程などでは、通常、人的能力が制約となり、これが標準能力として設定される。
関連用語: 能力所要量計画
通常、工程ででき得る能力をいう。一般に"時間"で表わされる。標準能力は、工程における機械の能力(機械能力)や人の能力(人的能力)に従って設定される。機械能力は、工程に設置されている機械の台数と、機械の1日当たりの標準稼働時間とを掛け合わせて求めることができる。また、人的能力は、工程の作業員と、作業員の1日当たりの標準作業時間とを掛け合わせて求められる。
状況に応じて、機械の能力か人の能力かのどちらかが制約となるが、この制約となる工程能力が標準能力として設定される。たとえば、機械設備や金型などの数に限りがある場合、機械能力が制約となり、標準能力として設定されることが多い。また、組立工程のような一般に手作業が主体となる工程や、熟練工を要する工程などでは、通常、人的能力が制約となり、これが標準能力として設定される。
関連用語: 能力所要量計画
Capacity Requirements Planning CRP
資材計画(MRPや部品展開)で計画された製造オーダーは、通常、製造部を総括管理している管理課とか管理担当係に提出され、まず能力と負荷の検討が行われる。この製造オーダーは、資材計画で、生産日程を基に部品表を使って得た品目単位のオーダーである。したがって、この段階では、工程という概念はまだない。しかし、実際にものをつくるには、いくつかの工程を経てつくられる。能力所要量計画とは、製造オーダーを基に、各工程に対する負荷を把握し、調整を行って、工程単位の作業を計画することをいう。
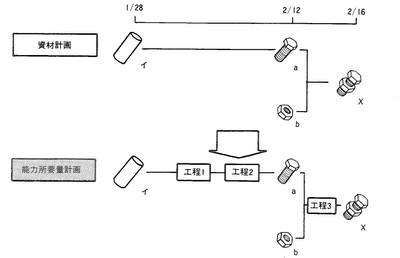
能力所要量計画をより現実に合ったものにするには、現状を反映した能力設定が必要となる。この計画では、次の3つの能力を使用する。
●標準能力:通常工程ででき得る能力。標準能力は普通、工程単位に設定する。この時、朝礼や休憩などの余裕時間や出勤率が考慮される。また、能力を日別に登録する場合もある。
●最大能力:工程で最大限に発揮し得る能力。最大能力の設定には2つの方法がある。1つは実績値を基に設定する方法であり、他の1つは過負荷の許容度として設定するやり方である。
●設定能力:標準、最大の能力と負荷の関連で設定した能力。設定時には、残業、シフトそれに人員の移動による増減などを考慮する。
能力所要量計画は、大きく次の4つの機能に分けられる。
●工程展開:MRPでの計画は品目レベルのものである。実際の作業指示は、各工程に対して行うため、この品目レベルの計画を工程レベルに分解しなければならない。この工程に分解する機能が工程展開である。
●負荷山積(山積):工程展開でづくられたオーダーは作業オーダーと呼ばれる。この作業オーダーには工程展開時に算出した作業時間が登録されている。この作業時間を負荷として当該工程の負荷を期間別に算出する。この機能が負荷山積である。
●負荷調整 (山崩):負荷調整は、最早開始日(部材が揃い、最も早く作業が開始可能な期日)と最遅開始日(納期割れを起こさない最も遅い期日)の範囲で行う。
●能力調整:負荷調整だけでは解决できない場合、残業、シレト、応援などの能力調整を考慮する。
これら一連の機能と計画担当者の判断で能力所要量計画は行われる。この計画にてつくられた作業オーダーは、作業指示計画へと引き継がれる。
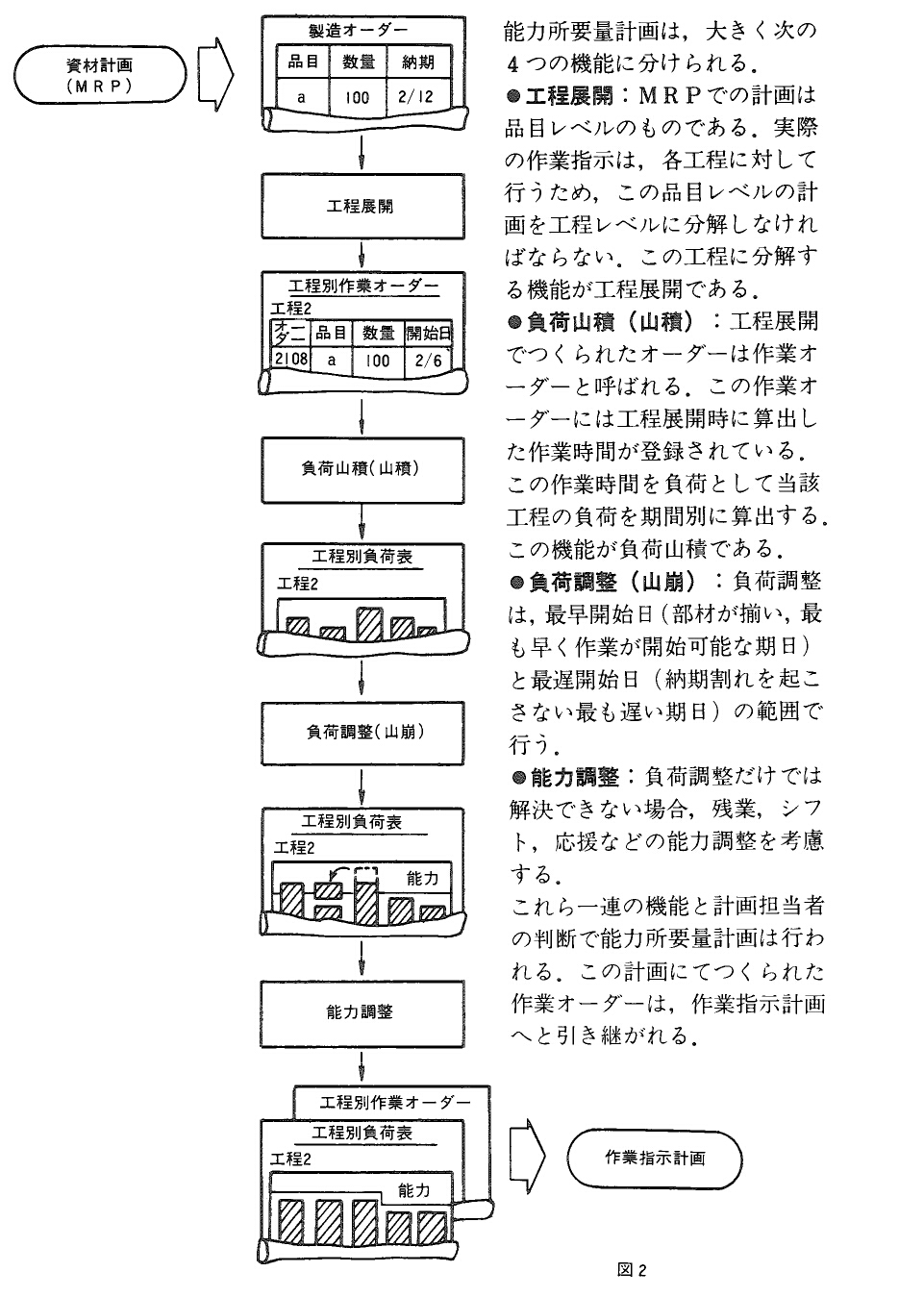
資材計画(MRPや部品展開)で計画された製造オーダーは、通常、製造部を総括管理している管理課とか管理担当係に提出され、まず能力と負荷の検討が行われる。この製造オーダーは、資材計画で、生産日程を基に部品表を使って得た品目単位のオーダーである。したがって、この段階では、工程という概念はまだない。しかし、実際にものをつくるには、いくつかの工程を経てつくられる。能力所要量計画とは、製造オーダーを基に、各工程に対する負荷を把握し、調整を行って、工程単位の作業を計画することをいう。
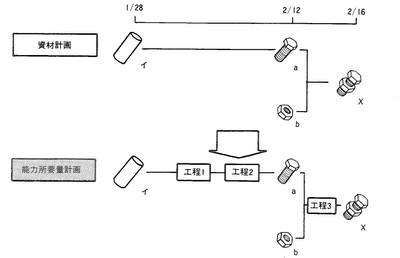
能力所要量計画をより現実に合ったものにするには、現状を反映した能力設定が必要となる。この計画では、次の3つの能力を使用する。
●標準能力:通常工程ででき得る能力。標準能力は普通、工程単位に設定する。この時、朝礼や休憩などの余裕時間や出勤率が考慮される。また、能力を日別に登録する場合もある。
●最大能力:工程で最大限に発揮し得る能力。最大能力の設定には2つの方法がある。1つは実績値を基に設定する方法であり、他の1つは過負荷の許容度として設定するやり方である。
●設定能力:標準、最大の能力と負荷の関連で設定した能力。設定時には、残業、シフトそれに人員の移動による増減などを考慮する。
能力所要量計画は、大きく次の4つの機能に分けられる。
●工程展開:MRPでの計画は品目レベルのものである。実際の作業指示は、各工程に対して行うため、この品目レベルの計画を工程レベルに分解しなければならない。この工程に分解する機能が工程展開である。
●負荷山積(山積):工程展開でづくられたオーダーは作業オーダーと呼ばれる。この作業オーダーには工程展開時に算出した作業時間が登録されている。この作業時間を負荷として当該工程の負荷を期間別に算出する。この機能が負荷山積である。
●負荷調整 (山崩):負荷調整は、最早開始日(部材が揃い、最も早く作業が開始可能な期日)と最遅開始日(納期割れを起こさない最も遅い期日)の範囲で行う。
●能力調整:負荷調整だけでは解决できない場合、残業、シレト、応援などの能力調整を考慮する。
これら一連の機能と計画担当者の判断で能力所要量計画は行われる。この計画にてつくられた作業オーダーは、作業指示計画へと引き継がれる。
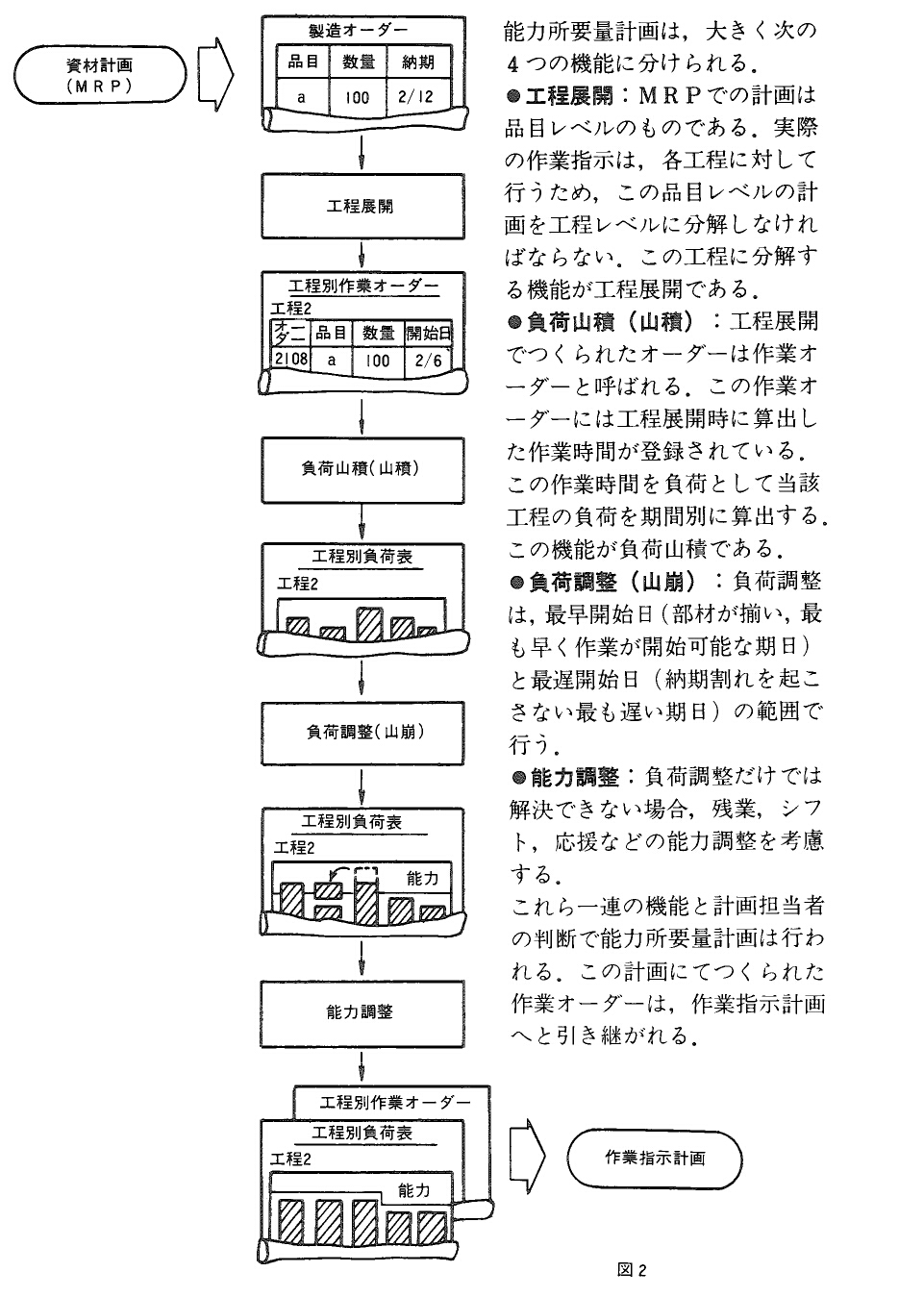
Capacity
ある一定期間内に、工程において生産可能な作業量のことで、通常"時間"で表わされる。
能力には、次のようなものがある。
●標準能力:通常工程ででき得る能力。
●最大能力:工程で最大限に発揮し得る能力。
●設定能力:標準、最大の能力と負荷の関連で設定した能力。
能力の制約条件としては、台数の限られた機械や設備、それに金型などがある。また、特殊な技能をもつ要員や外注もこれに含まれる。能力が、"生産可能な作業量"であるのに対し、"課せられた作業量"を負荷といい、同じく時間で表現される。
生産計画にて立案された製品やサービスパーツなどの生産日程は、通常、生産能力計画(RCP:Rough-cut Capacity Planning)により、ボトルネックとなる重要工程の能力/負荷の検討が行われ、実現可能な生産日程に調整されてMRPに入力される。この時、参照される工程マスターには、標準能力、最大能力などが登録されている。また、MRP実行後には、各工程単位での能力所要量計画(CRP:Capacity Requirements Planning)が行われる。
関連用語: 能力所要量計画、生産能力計画
反意語: 負荷
ある一定期間内に、工程において生産可能な作業量のことで、通常"時間"で表わされる。
能力には、次のようなものがある。
●標準能力:通常工程ででき得る能力。
●最大能力:工程で最大限に発揮し得る能力。
●設定能力:標準、最大の能力と負荷の関連で設定した能力。
能力の制約条件としては、台数の限られた機械や設備、それに金型などがある。また、特殊な技能をもつ要員や外注もこれに含まれる。能力が、"生産可能な作業量"であるのに対し、"課せられた作業量"を負荷といい、同じく時間で表現される。
生産計画にて立案された製品やサービスパーツなどの生産日程は、通常、生産能力計画(RCP:Rough-cut Capacity Planning)により、ボトルネックとなる重要工程の能力/負荷の検討が行われ、実現可能な生産日程に調整されてMRPに入力される。この時、参照される工程マスターには、標準能力、最大能力などが登録されている。また、MRP実行後には、各工程単位での能力所要量計画(CRP:Capacity Requirements Planning)が行われる。
関連用語: 能力所要量計画、生産能力計画
反意語: 負荷
検査場所により分類される検査の1つの方法で、一定の場所に位置を定めて行う検査のことをいう。これは、品目を1ヵ所に集めて検査した方が経済的な場合、試験のための特殊な設備が必要な場合、および検査時間が長い場合の時、などに用いられる。
関連用語: 検査
関連用語: 検査
ある工程で通常行われる作業が、他の工程でも同じ作業が行える場合、その代行可能な工程を代替工程という。ある工程で過負荷が生じた場合に、他の工程を代替工程として使用するといったケースが多い。また、代替可能な工程が外注業者の時には、その外注業者も代替工程として扱う。代替工程の情報としては、代替工程番号のほかに、その工程を使用した場合の作業時間などが設定される。
関連用語: 工程
関連用語: 工程
設備の劣化によって発生する故障、停止、性能低下の原因を取り除き、修復する活動をいう。
設備保全においては、次の3点を考慮する必要がある。
●いかに故障が起きないようにするか、いかに劣化を防止するかといった信頼性の向上を図る。
●点検・修理をしやすくし、故障時の修復作業の徹底を図るなど、保全性を向上させる。
●保全費や劣化損失などの保全のための費用が最小となるよう、経済性の向上を図る。
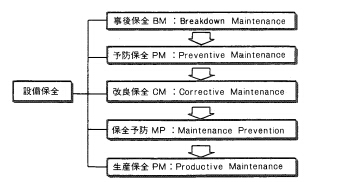
設備保全には図に示す5つの方式があり、時代とともにその形態も移り変わっている。1951年に予防保全がアメリカから導入される以前は事後保全の時代であったが、1950年代には予防保全から改良保全、保全予防へと発展し、1960年代には、これらを統合した生産保全の時代へと進展した。
設備保全においては、次の3点を考慮する必要がある。
●いかに故障が起きないようにするか、いかに劣化を防止するかといった信頼性の向上を図る。
●点検・修理をしやすくし、故障時の修復作業の徹底を図るなど、保全性を向上させる。
●保全費や劣化損失などの保全のための費用が最小となるよう、経済性の向上を図る。
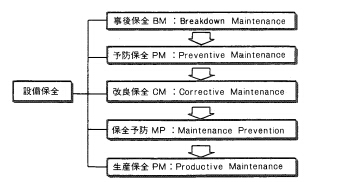
設備保全には図に示す5つの方式があり、時代とともにその形態も移り変わっている。1951年に予防保全がアメリカから導入される以前は事後保全の時代であったが、1950年代には予防保全から改良保全、保全予防へと発展し、1960年代には、これらを統合した生産保全の時代へと進展した。
Manufacturing Order
品目を製造する際に必要となるオーダーである。自社内で製造する品目については内作オーダーといい、外注業者で製造する品目については外注オーダーという。製造オーダーは、製造指図書として手配される。
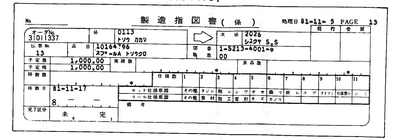
関連用語: オーダー
品目を製造する際に必要となるオーダーである。自社内で製造する品目については内作オーダーといい、外注業者で製造する品目については外注オーダーという。製造オーダーは、製造指図書として手配される。
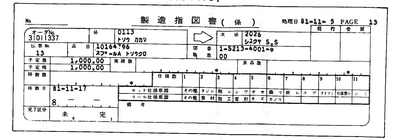
関連用語: オーダー
Bottleneck Process
一般に、製品は工場内の数多くの工程を経てつくられる。しかし、能力計画などを行う際には、これらすべての工程について行っていたのでは、大変な時間と費用がかかってしまう。重要工程とは、重点的に計画と統制を必要とする製品製造過程でのボトルネック工程をいい、台数の限られた機械設備、金型、それに特殊な技能を必要とする工程などがこれに当たる。このような工程をあらかじめ重要工程として設定し、この工程を重点的に管理することで、すべての工程を一律に行うよりも効果的な管理が可能となる。
関連用語: 工程
一般に、製品は工場内の数多くの工程を経てつくられる。しかし、能力計画などを行う際には、これらすべての工程について行っていたのでは、大変な時間と費用がかかってしまう。重要工程とは、重点的に計画と統制を必要とする製品製造過程でのボトルネック工程をいい、台数の限られた機械設備、金型、それに特殊な技能を必要とする工程などがこれに当たる。このような工程をあらかじめ重要工程として設定し、この工程を重点的に管理することで、すべての工程を一律に行うよりも効果的な管理が可能となる。
関連用語: 工程
Total Days of Operations Remaining
製造オーダーが完了するまでに必要とする各工程の作業時間を日数に換算した値で、作業の余裕率をみるスラックタイム係数の算出に用いられる。
関連用語: スラックタイム係数
製造オーダーが完了するまでに必要とする各工程の作業時間を日数に換算した値で、作業の余裕率をみるスラックタイム係数の算出に用いられる。
関連用語: スラックタイム係数
Operation Order Release Planning
能力所要量計画にて、作業オーダーによる負荷や能力を検討した結果、自工場でやるべき作業の計画を行う。 工程ごとに、次のようなことを検討する。
●すでに指示済の作業オーダーに遅れはないか。
●遅れがあるとすれば、どの程度の影響か。
●今回の作業オーダーの開始日をいつにするか。
●部材は予定通り引当されているか。
●欠品は何で、どの程度の影響なのか。
●部材の出庫指示はいつにするか。
●図面や治工具の手配はどうか。
●作業オーダーの納期は大丈夫か。
これらが決定、確認された確定オーダーは、作業順序計画へと引き継がれる。
能力所要量計画にて、作業オーダーによる負荷や能力を検討した結果、自工場でやるべき作業の計画を行う。 工程ごとに、次のようなことを検討する。
●すでに指示済の作業オーダーに遅れはないか。
●遅れがあるとすれば、どの程度の影響か。
●今回の作業オーダーの開始日をいつにするか。
●部材は予定通り引当されているか。
●欠品は何で、どの程度の影響なのか。
●部材の出庫指示はいつにするか。
●図面や治工具の手配はどうか。
●作業オーダーの納期は大丈夫か。
これらが決定、確認された確定オーダーは、作業順序計画へと引き継がれる。
Final Inspection
製造過程における検査の1つで、製造工程の最終段階で行う検査を指す。これは、完成品が製品としての要求事項を満足しているか否かの判別がなされ、顧客に対する信用の低下や各種の問題、損失を未然に防ぐために行われる。製造過程には、そのほかに、受入検査や工程検査があるが、これらは購入原材料や加工部品、組立品など構成品を対象とした検査で完成品の検査ではない。最終検査では顧客の要求も含め製品全体を検査する。
関連用語: 検査
製造過程における検査の1つで、製造工程の最終段階で行う検査を指す。これは、完成品が製品としての要求事項を満足しているか否かの判別がなされ、顧客に対する信用の低下や各種の問題、損失を未然に防ぐために行われる。製造過程には、そのほかに、受入検査や工程検査があるが、これらは購入原材料や加工部品、組立品など構成品を対象とした検査で完成品の検査ではない。最終検査では顧客の要求も含め製品全体を検査する。
関連用語: 検査
Interoperation Transport Time
移動時間ともいわれ、前工程が完了してから次の工程に運搬され、到着するまでに要する時間である。これは、機械の配置によっては、ほとんど無視できる場合もあるが、一般的には、運搬の不備により仕掛を停滞させたり、破損等の不良をつくったり、直接工の生産性の低下の原因を招いたりもする。このため、運搬距離を最短にし、運搬量を一定にして、かつ運搬作業の機械化、自動化を図ることが要求される。この時間の中には、運搬時間のほかに運搬待ち時間も含まれる。
関連用語: 製造リードタイム
移動時間ともいわれ、前工程が完了してから次の工程に運搬され、到着するまでに要する時間である。これは、機械の配置によっては、ほとんど無視できる場合もあるが、一般的には、運搬の不備により仕掛を停滞させたり、破損等の不良をつくったり、直接工の生産性の低下の原因を招いたりもする。このため、運搬距離を最短にし、運搬量を一定にして、かつ運搬作業の機械化、自動化を図ることが要求される。この時間の中には、運搬時間のほかに運搬待ち時間も含まれる。
関連用語: 製造リードタイム
Process,Routings
同じような機能や能力をもっている機械設備や人の集まりを指す。一般に作業指示の対象となり、これを受けて職長や差立係の判断で、その作業を、誰がどの機械設備で行うかを割付ける。
工程の種類には、大別して、加工、検査、運搬、停滞の4つがある。
●加工:切削や組立、分解などが含まれる。
●検査:良品、不良品の判定を行う工程で、一般に量と質の検査がある。
●運搬:工程間の移動をいい、人による場合と、コンベアなど機械による場合とがある。
●停滞:保管や工程待ちなどの仕掛状態をいう。
また、工程の編成には、ジョブショップ(機能別配置)、GTショップ(ジョブフロー)、フローショップ(製品別配置)、ラインがあり、工程の呼び名としては、前工程、後工程、重要工程、代替工程、初工程、最終工程などがある。生産管理の情報システム面において"工程"といった場合、加工や検査など現場の工程に固有な情報をまとめたマスターを指す。工程のデータ内容には、工程番号、工程名称、標準能力、最大能力などがある。
同じような機能や能力をもっている機械設備や人の集まりを指す。一般に作業指示の対象となり、これを受けて職長や差立係の判断で、その作業を、誰がどの機械設備で行うかを割付ける。
工程の種類には、大別して、加工、検査、運搬、停滞の4つがある。
●加工:切削や組立、分解などが含まれる。
●検査:良品、不良品の判定を行う工程で、一般に量と質の検査がある。
●運搬:工程間の移動をいい、人による場合と、コンベアなど機械による場合とがある。
●停滞:保管や工程待ちなどの仕掛状態をいう。
また、工程の編成には、ジョブショップ(機能別配置)、GTショップ(ジョブフロー)、フローショップ(製品別配置)、ラインがあり、工程の呼び名としては、前工程、後工程、重要工程、代替工程、初工程、最終工程などがある。生産管理の情報システム面において"工程"といった場合、加工や検査など現場の工程に固有な情報をまとめたマスターを指す。工程のデータ内容には、工程番号、工程名称、標準能力、最大能力などがある。
Assemblies
品目を生産過程(組立、加工など)別に捉えた時の呼び方であり、製品や部品などにつけられる名称である。また、組立作業の状況をより詳細に管理するため、組立品に到る前段階に半組立品という状態の品目設定をする場合もある。
関連用語: 半組立品
品目を生産過程(組立、加工など)別に捉えた時の呼び方であり、製品や部品などにつけられる名称である。また、組立作業の状況をより詳細に管理するため、組立品に到る前段階に半組立品という状態の品目設定をする場合もある。
関連用語: 半組立品
Manufactured Goods
品目を作業形態(組立など)別に捉えた時の呼び方であり、主に、素材を加工した後の部品を指すことが多い。一般に生産のための作業は加工、組立の順に行われている。
関連用語: 組立品
品目を作業形態(組立など)別に捉えた時の呼び方であり、主に、素材を加工した後の部品を指すことが多い。一般に生産のための作業は加工、組立の順に行われている。
関連用語: 組立品
Capacity Requirements Planning 能力所要量計画
Capacity Requirements Planningの略で、普通、能力所要量計画といわれている。これは、MRPで計画された各品目を工程に展開し、各工程に負荷山積して、能力とのバランスを調整する機能である。一般に、能力所要量計画を行うには、MRPで計画された製造オーダー、作業する工程の順序を示した工順と工程内容を記録した工程マスターを使用する。詳細は、能力所要量計画を参照。
Capacity Requirements Planningの略で、普通、能力所要量計画といわれている。これは、MRPで計画された各品目を工程に展開し、各工程に負荷山積して、能力とのバランスを調整する機能である。一般に、能力所要量計画を行うには、MRPで計画された製造オーダー、作業する工程の順序を示した工順と工程内容を記録した工程マスターを使用する。詳細は、能力所要量計画を参照。
Lot Production
生産方式を生産の連続性の面から捉えた場合、連続して生産するほど需要が多くなく、かといって注文ごとに生産するほど数量が少なくない場合に、ある数量にまとめ、ロットにして生産する方式を一般にロット生産という。この方式を受注の時期でみた場合、見込生産と受注生産の両方式で発生する。しかし、品種と数量の面で捉えると中品種中量生産となる。この方式では、ロットによる断続的な生産になるため、機械設備の稼働率を上げることが課題となる。このため段取等の準備回数を少なくするため勢い、ロットサイズが大きくなる可能性がある。これにより、過剰在庫となる危険性を含んでいる。ロット生産では、準備作業時間を短くして、ロットサイズをより小さくし、生産の流れ化をつくることがポイントとなる。
関連用語: 生産方式
生産方式を生産の連続性の面から捉えた場合、連続して生産するほど需要が多くなく、かといって注文ごとに生産するほど数量が少なくない場合に、ある数量にまとめ、ロットにして生産する方式を一般にロット生産という。この方式を受注の時期でみた場合、見込生産と受注生産の両方式で発生する。しかし、品種と数量の面で捉えると中品種中量生産となる。この方式では、ロットによる断続的な生産になるため、機械設備の稼働率を上げることが課題となる。このため段取等の準備回数を少なくするため勢い、ロットサイズが大きくなる可能性がある。これにより、過剰在庫となる危険性を含んでいる。ロット生産では、準備作業時間を短くして、ロットサイズをより小さくし、生産の流れ化をつくることがポイントとなる。
関連用語: 生産方式
Continuous Production
生産方式を生産の連続性の面から捉えた場合、特定の製品専用の機械設備を設置し、一定期間繰返して連続的に生産する方式を連続生産と称している。この方式を受注の時期で捉えると見込生産となり、製品の種類と生産量からみると少品種多量生産となる。つまり、事前に製品仕様を決定し、同一品種を大量に生産して、その後注文を受け付けることとなる。この方式では、一定の高い生産性が見込め作業の流れ化が可能となり顧客への納入が迅速な反面、数量や品種に対する需要の変化への順応性に欠ける。
関連用語: 生産方式
生産方式を生産の連続性の面から捉えた場合、特定の製品専用の機械設備を設置し、一定期間繰返して連続的に生産する方式を連続生産と称している。この方式を受注の時期で捉えると見込生産となり、製品の種類と生産量からみると少品種多量生産となる。つまり、事前に製品仕様を決定し、同一品種を大量に生産して、その後注文を受け付けることとなる。この方式では、一定の高い生産性が見込め作業の流れ化が可能となり顧客への納入が迅速な反面、数量や品種に対する需要の変化への順応性に欠ける。
関連用語: 生産方式
見込生産形態での生産計画を示し、狭義の見込生産計画と広義のものとに分けられる。狭義の意味での見込生産計画は、型や製品グループなどの単位で計画された生産量計画を基に、生産計画を立案する。これは、基準生産日程計画(MPS:Master Production Schedule)などとも呼ばれ、生産量に対し、在庫や受注残を考慮して、製品別、期間別の生産計画を作成する。
関連用語: 見込生産計画(広義)
関連用語: 見込生産計画(広義)
Make to Stock
生産方式を受注の時期で捉えた場合、生産をしてから注文を受け付ける方式を一般に見込生産と称している。この方式では、事前に顧客のニーズを把握して仕様を決め、これに基づいて設計、購買および製造の順で生産を行い、製品完成後に注文に引当てる。また、一度設計が行われた後は、その製品寿命を終えるまで、購買と製造を繰返す。このことから繰返し生産などとも呼ばれる。
見込生産では、受注と生産が直接的に関連していない。このため生産計画は、需要予測を基に設定された数量により立案する。また、需要と生産との間に製品在庫というクッションがあるため、工場では、周期変動や季節変動を平準化し、安定した生産を行うことが可能となる。
関連用語: 生産方式
反意語: 受注生産
生産方式を受注の時期で捉えた場合、生産をしてから注文を受け付ける方式を一般に見込生産と称している。この方式では、事前に顧客のニーズを把握して仕様を決め、これに基づいて設計、購買および製造の順で生産を行い、製品完成後に注文に引当てる。また、一度設計が行われた後は、その製品寿命を終えるまで、購買と製造を繰返す。このことから繰返し生産などとも呼ばれる。
見込生産では、受注と生産が直接的に関連していない。このため生産計画は、需要予測を基に設定された数量により立案する。また、需要と生産との間に製品在庫というクッションがあるため、工場では、周期変動や季節変動を平準化し、安定した生産を行うことが可能となる。
関連用語: 生産方式
反意語: 受注生産
Anticipated Stock Planning
製品の需要は変動するのが常である。需要の変動は、クーラーやヒーターのように季節によって起こるものもあれば、自転車や学習机のように入学の時期によって大きく左右するものもある。しかし、このような大きな需要の変動に対し、生産が柔軟に対応することはその能力の面から非常に難しい。見越計画とは、高需要期の計画数を低需要期に移して、生産し、在庫することにより生産の平均化、安定化を図ろうとする計画である。この時、先行生産されたものは在庫となるため、生産量は、在庫費用と能力増強のための費用とのバランスのうえで設定される必要がある。
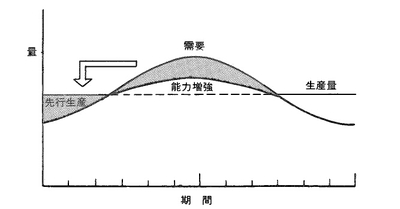
関連用語: 見込生産計画(広義)
製品の需要は変動するのが常である。需要の変動は、クーラーやヒーターのように季節によって起こるものもあれば、自転車や学習机のように入学の時期によって大きく左右するものもある。しかし、このような大きな需要の変動に対し、生産が柔軟に対応することはその能力の面から非常に難しい。見越計画とは、高需要期の計画数を低需要期に移して、生産し、在庫することにより生産の平均化、安定化を図ろうとする計画である。この時、先行生産されたものは在庫となるため、生産量は、在庫費用と能力増強のための費用とのバランスのうえで設定される必要がある。
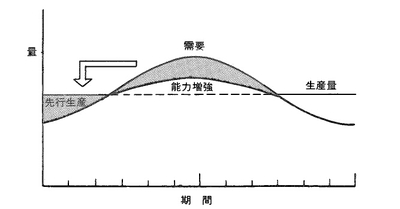
関連用語: 見込生産計画(広義)
Bill of Materials B/M、P/L
工場には製品をつくるために必要な部品や原材料など、いろいろな品目が存在する。部品表とは、製品と組立品、組立品と部品それに部品と原材料といった品目と品目の関連を示した一覧表のことをいう。部品表は、その情報のもち方からみてサマリ一部品表とストラクチャ部品表とに分けられ、用途別にみると設計部品表、生産部品表、計画部品表、スペア部品表などがある。また、部品表の表現方法で捉えると、一段階部品表、多段階部品表、集合部品表がある。
一般に部品表は、Bill of Materials を略してB/Mといわれ、これを表示した一覧表をパーツリスト(Parts List)といい、どちらも部品表と呼ばれる。B/Mと称した場合、部品表としてのマスターデータを指す場合が多い。
部品表は、親品目と子品目の関連を示すために、品目データと製品構成データの2つのマスターデータで表現される。
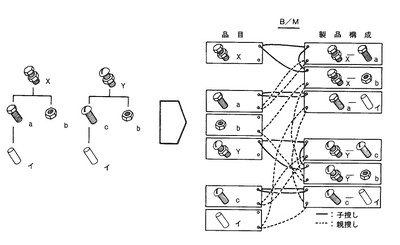
●品目データ:製品、組立品、部品、原材料など、品目に固有な情報をまとめたものであり、品目番号や品目名称それにリードタイムなどの項目から成る。
●製品構成データ:親品目と子品目の関連で決まる情報をまとめたもので、親品目番号、子品目番号、原単位などから成る。
このようにしてつくられた部品表は、製造企業のほとんどの部門において用いられる。たとえば設計部門では、類似製品の設計や設計変更の影響把握などに使われ、生産技術部門では、工順の検討やリードタイムの見直しなどに用いられる。また、MRPではこの部品表を駆使して部品や材料の手配計画を行う。次に部品表の主な用途を示す。
関連用語: 展開手法
工場には製品をつくるために必要な部品や原材料など、いろいろな品目が存在する。部品表とは、製品と組立品、組立品と部品それに部品と原材料といった品目と品目の関連を示した一覧表のことをいう。部品表は、その情報のもち方からみてサマリ一部品表とストラクチャ部品表とに分けられ、用途別にみると設計部品表、生産部品表、計画部品表、スペア部品表などがある。また、部品表の表現方法で捉えると、一段階部品表、多段階部品表、集合部品表がある。
一般に部品表は、Bill of Materials を略してB/Mといわれ、これを表示した一覧表をパーツリスト(Parts List)といい、どちらも部品表と呼ばれる。B/Mと称した場合、部品表としてのマスターデータを指す場合が多い。
部品表は、親品目と子品目の関連を示すために、品目データと製品構成データの2つのマスターデータで表現される。
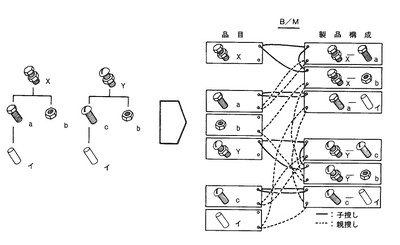
●品目データ:製品、組立品、部品、原材料など、品目に固有な情報をまとめたものであり、品目番号や品目名称それにリードタイムなどの項目から成る。
●製品構成データ:親品目と子品目の関連で決まる情報をまとめたもので、親品目番号、子品目番号、原単位などから成る。
このようにしてつくられた部品表は、製造企業のほとんどの部門において用いられる。たとえば設計部門では、類似製品の設計や設計変更の影響把握などに使われ、生産技術部門では、工順の検討やリードタイムの見直しなどに用いられる。また、MRPではこの部品表を駆使して部品や材料の手配計画を行う。次に部品表の主な用途を示す。
関連用語: 展開手法
Parts Oriented Production System
生産方式を引当の対象から捉えた場合、部品中心生産とは、あらかじめ標準となる部品やユニットなどをつくっておき、顧客からの注文に対して個々にこの部品を払い出し、組み合せて多様な注文への対処をする方式である。あらかじめつくっておく標準部品を緩衝部品とか中間仕込品などと呼び、政策的な在庫品となる。この部品は、図のように需要予測を基にした見込生産によってつくられ、また緩衝部品から製品までの生産は実際の受注により製作される。つまり、部品中心生産システムは緩衝部品を境として、見込生産と受注生産とが共存する複合生産システムである。この生産方式では、緩衝部品の位置を適切に設定することにより、製品の多様化と短納期に対応することができ、かつ製品引当生産方式より在庫の低減が図れる。また、この生産システムのポイントとしては、緩衝部品の標準化を図り、品目の管理点数を極力少なくすることと、この緩衝部品の需要予測の精度を高めることがあげられる。なお、MRPは、緩衝部品より下の見込生産の中の資材計画として主に使われる。
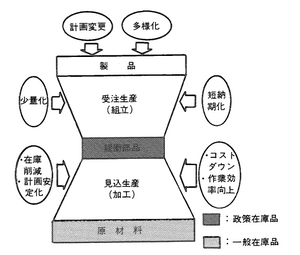
関連用語: 生産方式
生産方式を引当の対象から捉えた場合、部品中心生産とは、あらかじめ標準となる部品やユニットなどをつくっておき、顧客からの注文に対して個々にこの部品を払い出し、組み合せて多様な注文への対処をする方式である。あらかじめつくっておく標準部品を緩衝部品とか中間仕込品などと呼び、政策的な在庫品となる。この部品は、図のように需要予測を基にした見込生産によってつくられ、また緩衝部品から製品までの生産は実際の受注により製作される。つまり、部品中心生産システムは緩衝部品を境として、見込生産と受注生産とが共存する複合生産システムである。この生産方式では、緩衝部品の位置を適切に設定することにより、製品の多様化と短納期に対応することができ、かつ製品引当生産方式より在庫の低減が図れる。また、この生産システムのポイントとしては、緩衝部品の標準化を図り、品目の管理点数を極力少なくすることと、この緩衝部品の需要予測の精度を高めることがあげられる。なお、MRPは、緩衝部品より下の見込生産の中の資材計画として主に使われる。
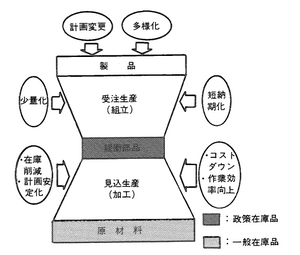
関連用語: 生産方式
生産方式を受注の時期で捉えた場合、中間部品を見込で生産しておき、注文を受け付けてから製品を生産する方式を部品仕込生産といい、部品中心生産と同義で使われることが多い。この方式は見込生産と受注生産の折衷方式で、見込生産より製品在庫は少なくなるが顧客リードタイムは長くなる。また、受注生産より中間部品の在庫は多くなるが、顧客リードタイムは短くなる。
関連用語: 生産方式
関連用語: 生産方式
工場における生産管理システムは、各種の計画機能が必要であり、各計画ごとに生産活動に必要な日程化が行われている。生産計画では製品レベルの計画、資材計画では部品や原材料の計画、そして購買計画では業者に対する計画が、一方製造計画では工程ごと、作業者ごとの計画がそれぞれ行われる。これら一連の計画を通常、日程計画と称し、その計画の期間と計画密度の細かさによって上流から順に大日程計画、中日程計画、小日程計画と呼んでいる。
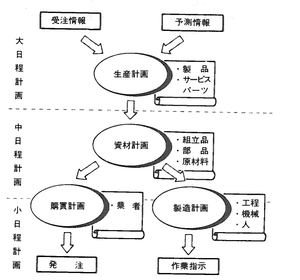
関連用語: 生産日程
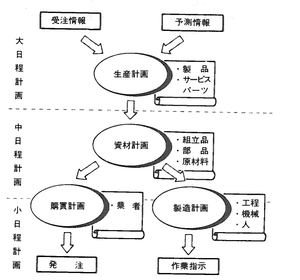
関連用語: 生産日程
月次計画などとも呼ばれ、通常毎月立案され、計画期間としては、2~3ヵ月がその範囲となる。また、この計画により、日常の生産活動は行われ、これを基にして各職場の作業も計画される。MRPにより立案された資材計画それに製造と購買の計画は中日程計画に含まれる。
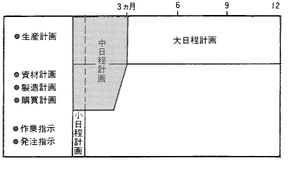
関連用語: 日程計画
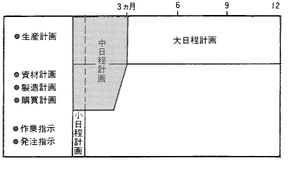
関連用語: 日程計画
生産をその種類と生産量で捉えた場合、多品種少量生産とは、かなり多くの品種をもち、1品種当りの生産数量が少ない生産方式をいう。実際的に、受注型でかつ個別生産を行う場合は多品種少量生産になることが多い。
関連用語: 生産方式
関連用語: 生産方式
販売計画を基にして半年から1年くらいの長期にわたり、製品グループや製品それに大わくとしての金額、数量を定めた計画を指し、工場の増設や長期的な能力、資材調達および資金計画などに使われる。
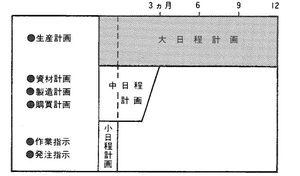
関連用語: 日程計画
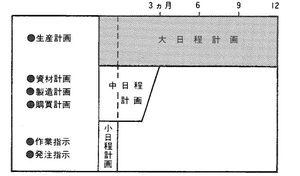
関連用語: 日程計画
製品をつくるために、部品や原材料の調達は、通常設計が完了し、部品表がつくられてから、これを使って手配が行われる。しかし、受注生産などにおいて、設計が完了してからでは間に合わない品目、つまりリードタイムが非常に長い部品や材料は、設計が完了する前に、いままでの経験を生かし、先行して手配しておくことがある。このような手配の方法を先行手配という。この場合、MRPにより手配計画を行うのではなく、人手によって行う。
生産方式を引当の対象から捉えた場合の呼び方で、あらかじめ、標準的な製品をつくっておき、顧客からの注文に対し、この製品を引当て、納入する方式である。これは、見込生産で、かつ連続的な生産が可能な場合に多く見られる。この場合、販売よりも設計、生産が先行するため、的確な需要予測、新製品開発期間の短縮などがとくに課題となる。
関連用語: 生産方式
関連用語: 生産方式
Product Manufacturing Order
顧客に対する製品履歴管理を行うために必要なオーダーで、製品の品名、製造日(完成日)、数量などのほかに、図面番号なども付される。製品製造オーダーを管理することで、顧客からのクレーム対処や、設計変更の顧客への反映が的確に行える。
関連用語: オーダー
顧客に対する製品履歴管理を行うために必要なオーダーで、製品の品名、製造日(完成日)、数量などのほかに、図面番号なども付される。製品製造オーダーを管理することで、顧客からのクレーム対処や、設計変更の顧客への反映が的確に行える。
関連用語: オーダー
Products Group グループ品目
類似の製品を集めグループ化したものを製品グループという。一般に、見込で製品の生産計画を立案する場合、数多くの製品を個々に計画するよりもグループ計画した方が精度も良い。そのため生産計画は製品系列別とか、類似機能別に立案されるのが一般的である。
類似の製品を集めグループ化したものを製品グループという。一般に、見込で製品の生産計画を立案する場合、数多くの製品を個々に計画するよりもグループ計画した方が精度も良い。そのため生産計画は製品系列別とか、類似機能別に立案されるのが一般的である。
Products
製造企業が生産過程で扱う品目の中の最後に位置するものであり、その企業の性格を特徴付けるものである。製造企業におけるすべての活動は製品を基点に始まるといえる。生産計画では製品の生産日程を立案し、資材計画では製品をつくるための構成品の手配をMRPにより計画している。製品がどのような構成品、原材料から成り立っているかを知るには、設計部門から提供された部品表により判別でき、いつ、どのくらいつくるかは、計画部門の作成した生産計画が基になる。
関連用語: 製品グループ
製造企業が生産過程で扱う品目の中の最後に位置するものであり、その企業の性格を特徴付けるものである。製造企業におけるすべての活動は製品を基点に始まるといえる。生産計画では製品の生産日程を立案し、資材計画では製品をつくるための構成品の手配をMRPにより計画している。製品がどのような構成品、原材料から成り立っているかを知るには、設計部門から提供された部品表により判別でき、いつ、どのくらいつくるかは、計画部門の作成した生産計画が基になる。
関連用語: 製品グループ
Production Plan
季節変動などを考慮してつくられた見越計画と、販売部門から提示された販売計画を基に型や製品グループなどの単位で、月別の生産量を計画することをいう。
季節変動などを考慮してつくられた見越計画と、販売部門から提示された販売計画を基に型や製品グループなどの単位で、月別の生産量を計画することをいう。
Production System
製造企業の生産形態は、企業規模や業種により実に様々な形をとる。たとえば、大型モーターや船舶のように顧客仕様に基づいて一品一様で生産するものもあれば、家電製品のように、ある限定された品種を多量に生産するものもある。しかし、近年顧客ニーズの多様化、短納期化などの要求が強まるにつれ、販売の変化に対し、柔軟にかつ迅速に対応できる生産形態が望まれている。これは企業規模や業種よりもむしろ、各製造企業の生産のやり方、つまり生産方式に対する考え方(コンセプト)により生産形態が決まることが多くなってきている。
生産方式は、その観点の違いにより、いろいろな呼び方がある。その主なものを次に示す。
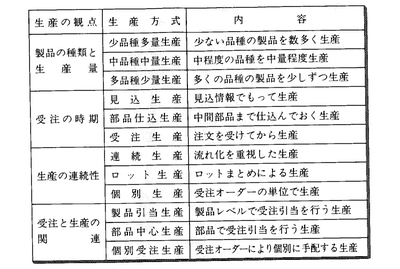
製造企業の生産形態は、企業規模や業種により実に様々な形をとる。たとえば、大型モーターや船舶のように顧客仕様に基づいて一品一様で生産するものもあれば、家電製品のように、ある限定された品種を多量に生産するものもある。しかし、近年顧客ニーズの多様化、短納期化などの要求が強まるにつれ、販売の変化に対し、柔軟にかつ迅速に対応できる生産形態が望まれている。これは企業規模や業種よりもむしろ、各製造企業の生産のやり方、つまり生産方式に対する考え方(コンセプト)により生産形態が決まることが多くなってきている。
生産方式は、その観点の違いにより、いろいろな呼び方がある。その主なものを次に示す。
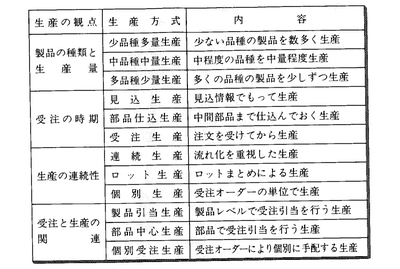
Rough-cut Capacity Planning RCP
普通、RCPと呼ばれ、生産計画に対する工場での生産能力の妥当性をみるために行う計画で、見込生産と受注生産の両方で使用することが可能である。これは、工場の中のボトルネックとなる工程、つまり重要工程を工程順序を参照して展開をし各重要工程の負荷量が能力に見合うか否かを計画するものである。
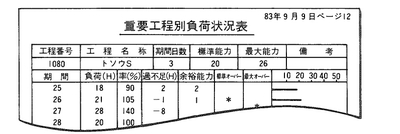
この計画により、生産計画や能力の見直しを行い、見込生産ではMRPへ、受注生産では最終組立計画へ結合される。生産能力計画を実行すると、一般的には上に示すような、重要工程別負荷状況表が作成される。
普通、RCPと呼ばれ、生産計画に対する工場での生産能力の妥当性をみるために行う計画で、見込生産と受注生産の両方で使用することが可能である。これは、工場の中のボトルネックとなる工程、つまり重要工程を工程順序を参照して展開をし各重要工程の負荷量が能力に見合うか否かを計画するものである。
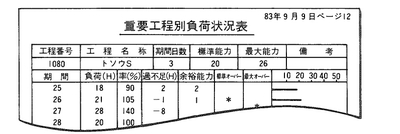
この計画により、生産計画や能力の見直しを行い、見込生産ではMRPへ、受注生産では最終組立計画へ結合される。生産能力計画を実行すると、一般的には上に示すような、重要工程別負荷状況表が作成される。
Production Schedule 日程計画
製品、組立品および加工品などの生産活動をある期間をとって日程化したものである。生産活動に関する日程化は生産計画、資材計画および製造計画などの各計画フェーズで実施される。日程化された生産活動は、そのままオーダーとなって現場に出ていくものや購買の手配をされるものもある。一般に生産日程には、見込生産日程、受注生産日程があり、製品や組立品などの各品目レベルごとに作成される。 MRPは、生産計画で示された製品の生産日程を基に、その製品以下の各品目について生産日程を作成する。また、生産日程は日程計画と同義で用いられる場合もある。
製品、組立品および加工品などの生産活動をある期間をとって日程化したものである。生産活動に関する日程化は生産計画、資材計画および製造計画などの各計画フェーズで実施される。日程化された生産活動は、そのままオーダーとなって現場に出ていくものや購買の手配をされるものもある。一般に生産日程には、見込生産日程、受注生産日程があり、製品や組立品などの各品目レベルごとに作成される。 MRPは、生産計画で示された製品の生産日程を基に、その製品以下の各品目について生産日程を作成する。また、生産日程は日程計画と同義で用いられる場合もある。
小日程計画とは、週間計画などとも呼ばれ、立案された中日程計画を基にして、かつ現状の作業の進度状況および計画の変更などを考慮して実際的な作業の割付けを行うための予定をいう。計画期間としては旬間や週間が普通であるが、近年、そのサイクルはどんどん短くなってきている。小日程計画では、中日程計画で決められた"何を、いくつ、いつまでに"という事項を受けて、"誰が、何を、いくつ、いつまでに、どの機械をつかってどのくらいの時間をかけて"つくるかを個人別の計画表として作成する。
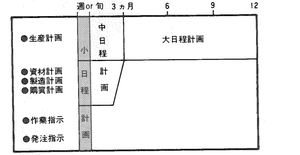
関連用語: 日程計画
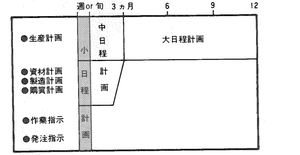
関連用語: 日程計画
Resource Requirements Planning RRP
この計画は、RRP(Resource Requirements Planning)ともいわれ、生産量計画を基に機械設備、作業者、資金に代表される生産資源の所要量を計画する。具体的には、生産計画の月別に計画された生産量を基に、製品負荷輪郭を参照して、各資源の期間別所要量を算出する。この資源所要量計画により、生産計画、操業度計画および資金計画の見直しを行う。図に示されるZの生産量計画は9月より連続して各月に計画されており、各月の生産量計画はZの製品負荷輪郭を基にした必要資源への負荷となって表われている。たとえば、Zの11月の生産量による各資源に対する負荷は、その製品負荷輪郭によって資源R1の11月、資源R2の10月、資源R3の9月にそれぞれ表われる。
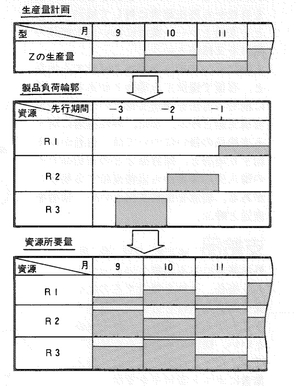
関連用語: 見込生産計画(広義)
この計画は、RRP(Resource Requirements Planning)ともいわれ、生産量計画を基に機械設備、作業者、資金に代表される生産資源の所要量を計画する。具体的には、生産計画の月別に計画された生産量を基に、製品負荷輪郭を参照して、各資源の期間別所要量を算出する。この資源所要量計画により、生産計画、操業度計画および資金計画の見直しを行う。図に示されるZの生産量計画は9月より連続して各月に計画されており、各月の生産量計画はZの製品負荷輪郭を基にした必要資源への負荷となって表われている。たとえば、Zの11月の生産量による各資源に対する負荷は、その製品負荷輪郭によって資源R1の11月、資源R2の10月、資源R3の9月にそれぞれ表われる。
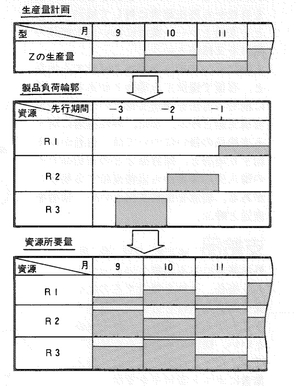
関連用語: 見込生産計画(広義)
Finished Product
一般の製造企業において、製品という言葉の意味は広い。生産された製品は、そのまま出荷されるものもあれば、その製品がある製品やオプション部品などと組み合わされて別の製品として出荷されることもある。最終製品とは、製造企業の生産過程で最後に位置する製品のことである。
関連用語: 製品
一般の製造企業において、製品という言葉の意味は広い。生産された製品は、そのまま出荷されるものもあれば、その製品がある製品やオプション部品などと組み合わされて別の製品として出荷されることもある。最終製品とは、製造企業の生産過程で最後に位置する製品のことである。
関連用語: 製品
Final Assembly Schedule
受注生産計画の中の1計画機能で、各受注オーダーをラインに割り振り、その組立の開始日と終了日を計画することをいう。
受注生産計画の中の1計画機能で、各受注オーダーをラインに割り振り、その組立の開始日と終了日を計画することをいう。
Job Production
生産方式を生産の連続性の面から捉えた場合、ある程度異なる製品が生産可能な汎用の機械設備を設置し、注文に合わせて個別に生産する方式を個別生産という。一般に、この方式を受注の時期で捉えると受注生産となり、製品の種類と生産量から捉えると多品種少量生産となる。つまり、個々の注文を受付けてから製品の仕様を決定し、顧客ごとに異なる製品を個別に生産し、納入することになる。 この方式では、数量や品種に対する顧客の要望に比較的対応可能となる反面、作業の流れ化がしにくく、生産性を高めることが難しい。このため、現場の監督者や作業者は管理と生産技術面の高度な能力が要求される。
関連用語: 生産方式
生産方式を生産の連続性の面から捉えた場合、ある程度異なる製品が生産可能な汎用の機械設備を設置し、注文に合わせて個別に生産する方式を個別生産という。一般に、この方式を受注の時期で捉えると受注生産となり、製品の種類と生産量から捉えると多品種少量生産となる。つまり、個々の注文を受付けてから製品の仕様を決定し、顧客ごとに異なる製品を個別に生産し、納入することになる。 この方式では、数量や品種に対する顧客の要望に比較的対応可能となる反面、作業の流れ化がしにくく、生産性を高めることが難しい。このため、現場の監督者や作業者は管理と生産技術面の高度な能力が要求される。
関連用語: 生産方式
Job Order Production
生産方式を引当の対象から捉えた場合、顧客からの個々の注文を受け、それから仕様を決めて、ものの手配を行い生産する方式で、製品や部品への引当はほとんどない。これは、受注生産で、かつ個別に生産する場合に多く見られ、多品種少量生産の形態をとる。この場合、受注状況が不安定になりやすく、操業度の変動が大きい。このため、受注量の安定化と設計の自動化、部品の標準化を図り、かつ生産段階での進度管理、総合的な納期管理を重点として、工場の稼働率を向上させることが必要となる。
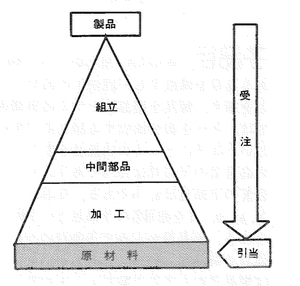
関連用語: 生産方式
生産方式を引当の対象から捉えた場合、顧客からの個々の注文を受け、それから仕様を決めて、ものの手配を行い生産する方式で、製品や部品への引当はほとんどない。これは、受注生産で、かつ個別に生産する場合に多く見られ、多品種少量生産の形態をとる。この場合、受注状況が不安定になりやすく、操業度の変動が大きい。このため、受注量の安定化と設計の自動化、部品の標準化を図り、かつ生産段階での進度管理、総合的な納期管理を重点として、工場の稼働率を向上させることが必要となる。
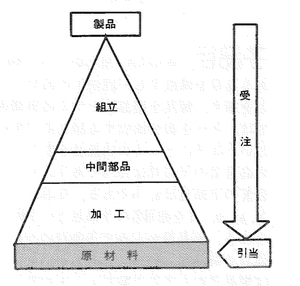
関連用語: 生産方式
Emergency Order 特急オーダー
緊急の受注などにより、通常のリードタイムより短い納期で生産する時に必要なオーダーである。この時のリードタイムは、緊急リードタイムと呼ばれ、あらかじめ設定されているリードタイム率(短縮率)を用いて計算される。
緊急の受注などにより、通常のリードタイムより短い納期で生産する時に必要なオーダーである。この時のリードタイムは、緊急リードタイムと呼ばれ、あらかじめ設定されているリードタイム率(短縮率)を用いて計算される。
Resource Requirements Planning 資源所要量計画
Resource Requirements Planningの略で、一般に資源所要量計画と訳されている。資源所要量計画を参照。
Resource Requirements Planningの略で、一般に資源所要量計画と訳されている。資源所要量計画を参照。
Forecast Model
予測に関し、その測定の構造を要因の効果や誤差に分析し、式で表現したものである。予測モデルは、一度設定されると変更されないことが多く、それが長期にわたった場合、全く使いものにならないこともある。モデルはそのつど得られる新しいデータを基に更新されることが望ましい。
予測に関し、その測定の構造を要因の効果や誤差に分析し、式で表現したものである。予測モデルは、一度設定されると変更されないことが多く、それが長期にわたった場合、全く使いものにならないこともある。モデルはそのつど得られる新しいデータを基に更新されることが望ましい。
Forecast Method
需要予測のための基本となる分析には、市場がその主な対象となる。市場は不確定要素を多くはらみ、かつ開放された経済の活動の場である。このためその分析には、統計理論的分析、経済理論的分析が必要となる。また、経済指標に関連付けた外部のマクロ的分析と企業内を中心とし、市場や商品を対象としたミクロ的分析も必要となる。各企業で用いられている需要予測のほとんどは、製品別需要予測で、これは時系列分析と単純相関分析が基本となる。さらに需要予測を行うための手法として、主に移動平均法、指数平滑法が使われる。
需要予測のための基本となる分析には、市場がその主な対象となる。市場は不確定要素を多くはらみ、かつ開放された経済の活動の場である。このためその分析には、統計理論的分析、経済理論的分析が必要となる。また、経済指標に関連付けた外部のマクロ的分析と企業内を中心とし、市場や商品を対象としたミクロ的分析も必要となる。各企業で用いられている需要予測のほとんどは、製品別需要予測で、これは時系列分析と単純相関分析が基本となる。さらに需要予測を行うための手法として、主に移動平均法、指数平滑法が使われる。
Error in Forecast
予測は、仮定と不確定要素のうえに立てられている。このことから予測には予測値と実績値の差、つまり予測誤差がつきまとう。通常、予測誤差は、正規分布をなし、その分布の度合は、一般に平均絶対偏差(MAD)で表わされる。
関連用語: MAD
予測は、仮定と不確定要素のうえに立てられている。このことから予測には予測値と実績値の差、つまり予測誤差がつきまとう。通常、予測誤差は、正規分布をなし、その分布の度合は、一般に平均絶対偏差(MAD)で表わされる。
関連用語: MAD
Irregular Component
予測における時系列分析での変動要素の1つで、傾向、循環および季節の各変動では説明できない変動を示す。一般に、識別が難しい多くの因子の存在や各々の関連から偶発的に生じる変動を指す。
関連用語: 時系列分析
予測における時系列分析での変動要素の1つで、傾向、循環および季節の各変動では説明できない変動を示す。一般に、識別が難しい多くの因子の存在や各々の関連から偶発的に生じる変動を指す。
関連用語: 時系列分析
Sales Forecast
企業の販売意欲を示すものである。一般に需要と販売は表裏一体であり、需要がなければ販売はない。しかし、潜在需要があっても販売力がなければ実際の需要とはならない。したがって販売予測は、需要予測を基に、自社の販売能力を考慮し、その方法の改善を含めたうえでの立案が望ましい。
企業の販売意欲を示すものである。一般に需要と販売は表裏一体であり、需要がなければ販売はない。しかし、潜在需要があっても販売力がなければ実際の需要とはならない。したがって販売予測は、需要予測を基に、自社の販売能力を考慮し、その方法の改善を含めたうえでの立案が望ましい。
Tracking Signal
予測誤差の分布は通常正規分布をなし、このような状態の時は、うまく予測が行われていると、みなしてよい。しかし、あらゆる場合に正規分布をなすとは限らない。トラッキングシグナルとは、予測誤差が正の値にかたよったり、負の値にまとまったりして、偏りが大きくなったことを判別するために用いられ、前頁の式にて算出される。
たとえば、次のようなF1とF2の予測誤差が発生した場合、いずれも平均絶対偏差(MAD)は45である。しかし、トラッキングシグナルはF1が0.22、F2が6となり、F1の予測の方が優れていると同時に、F2の予測は実績データの分析と予測モデルの見直しが必要となる。
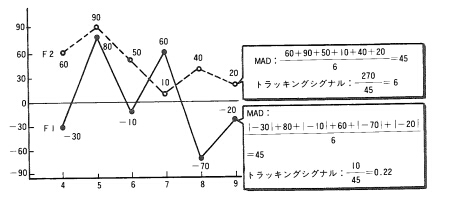
関連用語: 予測誤差
予測誤差の分布は通常正規分布をなし、このような状態の時は、うまく予測が行われていると、みなしてよい。しかし、あらゆる場合に正規分布をなすとは限らない。トラッキングシグナルとは、予測誤差が正の値にかたよったり、負の値にまとまったりして、偏りが大きくなったことを判別するために用いられ、前頁の式にて算出される。
トラッキングシグナル=累積予測誤差/平均絶対偏差
たとえば、次のようなF1とF2の予測誤差が発生した場合、いずれも平均絶対偏差(MAD)は45である。しかし、トラッキングシグナルはF1が0.22、F2が6となり、F1の予測の方が優れていると同時に、F2の予測は実績データの分析と予測モデルの見直しが必要となる。
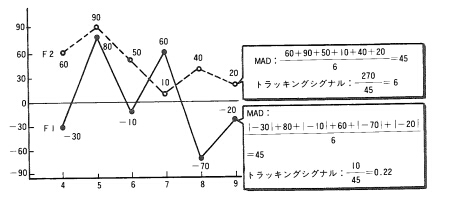
関連用語: 予測誤差
Independent Demand Items
工場では、製品、組立品、部品、それに原材料など、数多くの品目を扱っている。これらの品目を需要の観点で捉えると、他の品目とは無関係に、独立して需要が発生する品目と、他の品目に従属して需要が設定される品目とがある。前者を独立需要品目といい、後者を従属需要品目と呼ぶ。 一般に、独立需要品目とは、他の需要とは直接的な関連をもたず予測でのみ、その需要が求められる品目を指す。 このような品目には、製品やサービス部品などがあり、通常、販売部門で扱う品目が対象となる。これは顧客から個々の品目1つひとつに対して需要が発生するのであって、品目同士お互いに需要の関連はもっていない。独立需要品目は、予測や生産計画で対象となる品目である。
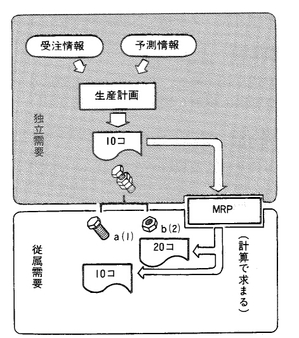
関連用語: 需要特性、独立需要
反意語: 従属需要品目
工場では、製品、組立品、部品、それに原材料など、数多くの品目を扱っている。これらの品目を需要の観点で捉えると、他の品目とは無関係に、独立して需要が発生する品目と、他の品目に従属して需要が設定される品目とがある。前者を独立需要品目といい、後者を従属需要品目と呼ぶ。 一般に、独立需要品目とは、他の需要とは直接的な関連をもたず予測でのみ、その需要が求められる品目を指す。 このような品目には、製品やサービス部品などがあり、通常、販売部門で扱う品目が対象となる。これは顧客から個々の品目1つひとつに対して需要が発生するのであって、品目同士お互いに需要の関連はもっていない。独立需要品目は、予測や生産計画で対象となる品目である。
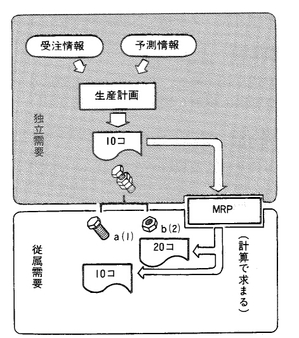
関連用語: 需要特性、独立需要
反意語: 従属需要品目
Statistical Forecast
時系列データを用いて統計的手法により予測を行うことである。
時系列データを用いて統計的手法により予測を行うことである。
Demand Filter
予測値と実績値の差としての予測誤差は通常正規分布をなし、極端に大きな値や小さな値をとることは、きわめてまれである。デマンドフィルターとは、一般に予測値に対して±4MADに設定され、実際にこれ以上の値が発生した時は、実績データを分析し、予測モデルの適合性を見直すことが必要となる。
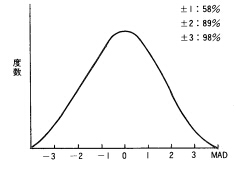
関連用語: 予測誤差
予測値と実績値の差としての予測誤差は通常正規分布をなし、極端に大きな値や小さな値をとることは、きわめてまれである。デマンドフィルターとは、一般に予測値に対して±4MADに設定され、実際にこれ以上の値が発生した時は、実績データを分析し、予測モデルの適合性を見直すことが必要となる。
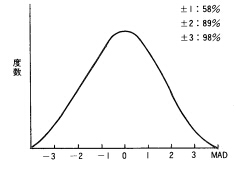
関連用語: 予測誤差
Cycle Movement
予測における時系列分析での変動要素の1つで、景気変動などとも呼ばれ、一般に3年から15年くらいで繰返される周期的な変動である。また、この周期の平均は3年から5年くらいであるが、特に波動の長いものは、傾向変動として捉えてもよい。なお、約40ヵ月の波動をキチンの波または在庫循環、10年前後をジュグラーの波、半世紀を超える波動をコンドラチェフの波と呼ぶ。
関連用語: 時系列分析
予測における時系列分析での変動要素の1つで、景気変動などとも呼ばれ、一般に3年から15年くらいで繰返される周期的な変動である。また、この周期の平均は3年から5年くらいであるが、特に波動の長いものは、傾向変動として捉えてもよい。なお、約40ヵ月の波動をキチンの波または在庫循環、10年前後をジュグラーの波、半世紀を超える波動をコンドラチェフの波と呼ぶ。
関連用語: 時系列分析
Dependent Demand Item
品目を需要の観点で捉えると、他の品目とは無関係に独立して需要が発生する品目と、他の品目に従属して需要が設定される品目とがある。前者を独立需要品目といい、後者を従属需要品目と呼ぶ。一般に、従属需要品目とは、製品やサービスパーツなどの独立需要品目を基に、順次計算によって需要が求められる品目を指す。このような品目には、組立品、半組立品、加工部品、購入部品それに原材料までが含まれる。これらの品目は、必ず上位品目をもち、その上位品目の所要量を基にして、所要量計算を行うことで要求量が設定される。このような従属需要品目は、部品中心生産方式などの特殊な例を除いて、一般的には、MRPでの計画対象品目となる。
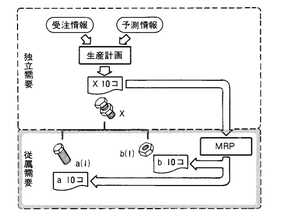
関連用語: 需要特性、従属需要
反意語: 独立需要
品目を需要の観点で捉えると、他の品目とは無関係に独立して需要が発生する品目と、他の品目に従属して需要が設定される品目とがある。前者を独立需要品目といい、後者を従属需要品目と呼ぶ。一般に、従属需要品目とは、製品やサービスパーツなどの独立需要品目を基に、順次計算によって需要が求められる品目を指す。このような品目には、組立品、半組立品、加工部品、購入部品それに原材料までが含まれる。これらの品目は、必ず上位品目をもち、その上位品目の所要量を基にして、所要量計算を行うことで要求量が設定される。このような従属需要品目は、部品中心生産方式などの特殊な例を除いて、一般的には、MRPでの計画対象品目となる。
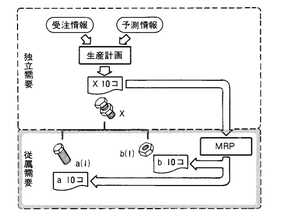
関連用語: 需要特性、従属需要
反意語: 独立需要
Exponential Smoothing Method
指数型の加重移動平均法であり予測手法としてよく用いられる。指数平滑法には、単純指数平滑法、二重指数平滑法、三重指数平滑法、多重指数平滑法などがある。
関連用語: 予測手法
指数型の加重移動平均法であり予測手法としてよく用いられる。指数平滑法には、単純指数平滑法、二重指数平滑法、三重指数平滑法、多重指数平滑法などがある。
関連用語: 予測手法
Time Series Analysis
予測方法の1つで、過去数年間の販売実績や価格傾向などを分析し、この推移を基に、将来の変化を予測することをいう。
時系列分析の手順は、次のように行われる。
①過去の時系列データをグラフ化して、その傾向線を表わす。
②傾向線が妥当か否か検討する。
③傾向線の式を定め、その係数を導く。
一般に、時系列は、傾向変動、循環変動、季節変動、不規則変動の4つの変動要素から構成されている。
予測方法の1つで、過去数年間の販売実績や価格傾向などを分析し、この推移を基に、将来の変化を予測することをいう。
時系列分析の手順は、次のように行われる。
①過去の時系列データをグラフ化して、その傾向線を表わす。
②傾向線が妥当か否か検討する。
③傾向線の式を定め、その係数を導く。
一般に、時系列は、傾向変動、循環変動、季節変動、不規則変動の4つの変動要素から構成されている。
Trend
予測における時系列分析での変動要素の1つで、長期にわたる一方的な上昇あるいは下降の傾向を表わす要素を示す。循環変動でも、その同期が15年とか20年とかいった長期的なものも傾向変動として捉えることが多い。このように傾向変動は、人口の移動、ニーズの変化などの長期的要因により大きく左右してくる。
関連用語: 時系列分析
予測における時系列分析での変動要素の1つで、長期にわたる一方的な上昇あるいは下降の傾向を表わす要素を示す。循環変動でも、その同期が15年とか20年とかいった長期的なものも傾向変動として捉えることが多い。このように傾向変動は、人口の移動、ニーズの変化などの長期的要因により大きく左右してくる。
関連用語: 時系列分析
Group Item
予測精度向上のために設けられる品目であり、ある系列に属する品目をグループ化したものである。予測は個々の品目に対してでなく、そのグループに対して行われる。
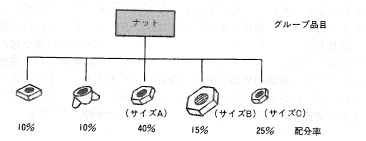
予測精度向上のために設けられる品目であり、ある系列に属する品目をグループ化したものである。予測は個々の品目に対してでなく、そのグループに対して行われる。
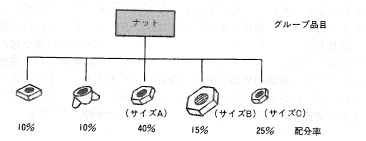
Seasonal Variation
予測における時系列分析での変動要素の1つで、製品の生産や販売が、その製品の特性により、季節に対応してある一定の傾向で変化することをいう。また、年間の稼働日を考えてみた場合、各月の休日、祝日はまちまちである。したがって、各月の稼働日もいろいろであり、正月休みのある1月と7月では稼働日の数に3~4日の差がある。1ヵ月30日に対する4日は10%以上の割合を占め、決して無視できない値である。これら年間を通じての稼働日の変化も季節変動という。
たとえば、インフルエンザが流行するのは冬、とくに1~2月であり、薬の販売量も需要期に一致し、その時期急激に増えるのが一般的である。しかし、生産面でみると、そのピークは販売のそれよりも早くおとずれるようになる。
このように、全く同じ製品を扱った時でも季節変動という捉え方をする場合には、生販別々に把握する必要がある。
予測における時系列分析での変動要素の1つで、製品の生産や販売が、その製品の特性により、季節に対応してある一定の傾向で変化することをいう。また、年間の稼働日を考えてみた場合、各月の休日、祝日はまちまちである。したがって、各月の稼働日もいろいろであり、正月休みのある1月と7月では稼働日の数に3~4日の差がある。1ヵ月30日に対する4日は10%以上の割合を占め、決して無視できない値である。これら年間を通じての稼働日の変化も季節変動という。
たとえば、インフルエンザが流行するのは冬、とくに1~2月であり、薬の販売量も需要期に一致し、その時期急激に増えるのが一般的である。しかし、生産面でみると、そのピークは販売のそれよりも早くおとずれるようになる。
このように、全く同じ製品を扱った時でも季節変動という捉え方をする場合には、生販別々に把握する必要がある。
Lead Time 手番、先行日数
オーダーを発行してから作業がなされ、そのオーダーが完了するまでの期間をいい、先行日数とか手番などともいわれる。通常、日数で表現される。
一般に次のようなものがある。
●ペーパーリードタイム
●購買リードタイム
●製造リードタイム
●外注リードタイム
リードタイムは部品表に登録するが、この時、部品表の品目に設定するか、製品構成にもたせるかによって、その意味合いはかなり違ってくる。ほとんどの製造業では、上位品目をつくる時点ですべての下位品目が、そろっていると仮定して、資材計画が行われる。この場合は図1で示すように、リードタイムは各品目に設定される。
また、船舶などの大型製品や特殊な製品を扱う製造企業、それに、製造や組立のリードタイムが非常に長い場合などは、図2で示すように、品目と品目の関連を示す製品構成にリードタイムを設定する。このようにすることで、部材の在庫期間が短縮でき、製造や組立の計画をより細かく行うことが可能となる。しかし、このような考慮は、一般の製造業では、ほとんど払わなくてよい。リードタイムの長さからいって、それほど神経質になる必要もないし、あまり長いリードタイムの場合は、図3で示すように、中間に管理品目を設定するのが普通である。
このようにして設定されたリードタイムを用いて、オーダーの予定開始日を算出する。
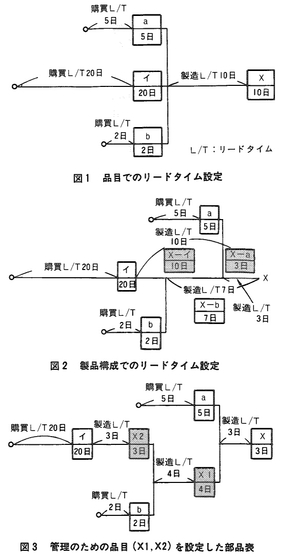
関連用語: リードタイム計算
オーダーを発行してから作業がなされ、そのオーダーが完了するまでの期間をいい、先行日数とか手番などともいわれる。通常、日数で表現される。
一般に次のようなものがある。
●ペーパーリードタイム
●購買リードタイム
●製造リードタイム
●外注リードタイム
リードタイムは部品表に登録するが、この時、部品表の品目に設定するか、製品構成にもたせるかによって、その意味合いはかなり違ってくる。ほとんどの製造業では、上位品目をつくる時点ですべての下位品目が、そろっていると仮定して、資材計画が行われる。この場合は図1で示すように、リードタイムは各品目に設定される。
また、船舶などの大型製品や特殊な製品を扱う製造企業、それに、製造や組立のリードタイムが非常に長い場合などは、図2で示すように、品目と品目の関連を示す製品構成にリードタイムを設定する。このようにすることで、部材の在庫期間が短縮でき、製造や組立の計画をより細かく行うことが可能となる。しかし、このような考慮は、一般の製造業では、ほとんど払わなくてよい。リードタイムの長さからいって、それほど神経質になる必要もないし、あまり長いリードタイムの場合は、図3で示すように、中間に管理品目を設定するのが普通である。
このようにして設定されたリードタイムを用いて、オーダーの予定開始日を算出する。
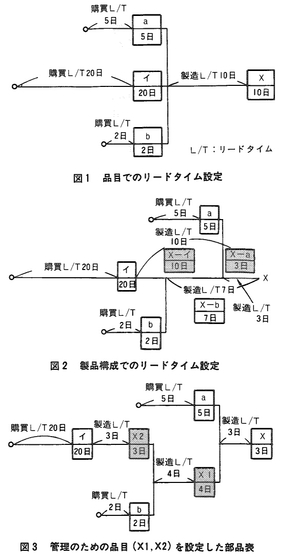
関連用語: リードタイム計算
Reservation
受注予定のことをいい、引合によって生産検討が行われた後に確認される。
製造部門は、予約が近く受注に結び付くことを考えて、資材や作業者、機械設備などの資源を確保し、場合によっては、ある程度の作業を開始する。しかし、予約は必ずしも受注になるとは限らない。受注に結びつかない予約が多い場合には、受注管理が繁雑になり、製造部門は混乱するため、予約の解除が必要となる。予約を受け付けてから一定期間内に受注が成立しない場合には、予約を自動的に解除するというケースが多い。
関連用語: 請納期
受注予定のことをいい、引合によって生産検討が行われた後に確認される。
製造部門は、予約が近く受注に結び付くことを考えて、資材や作業者、機械設備などの資源を確保し、場合によっては、ある程度の作業を開始する。しかし、予約は必ずしも受注になるとは限らない。受注に結びつかない予約が多い場合には、受注管理が繁雑になり、製造部門は混乱するため、予約の解除が必要となる。予約を受け付けてから一定期間内に受注が成立しない場合には、予約を自動的に解除するというケースが多い。
関連用語: 請納期
Quotations
顧客もしくは販売部門からの仕様、価格、納期、数量に関して、生産可能か否かの問合せをいう。生産部門では、問合せによって得られた引合情報を基に、生産および納入の可否を検討する。検討内容には、次のようなものがある。
●標準品かどうか。
●特注品の場合、当社の技術で生産できるか、また、外部(外注や他工場)から技術的な応援がすぐ得られるか。
●組立に、とくに必要な中間仕込品(主要部材)に余裕があるか、あるいは、すぐ調達可能か。
●組立工程の能力(機械設備や作業者など)に余裕があるか、あるいは、外部の生産能力が使用できるか。
●見積価格はどうか。
関連用語: 請納期
顧客もしくは販売部門からの仕様、価格、納期、数量に関して、生産可能か否かの問合せをいう。生産部門では、問合せによって得られた引合情報を基に、生産および納入の可否を検討する。検討内容には、次のようなものがある。
●標準品かどうか。
●特注品の場合、当社の技術で生産できるか、また、外部(外注や他工場)から技術的な応援がすぐ得られるか。
●組立に、とくに必要な中間仕込品(主要部材)に余裕があるか、あるいは、すぐ調達可能か。
●組立工程の能力(機械設備や作業者など)に余裕があるか、あるいは、外部の生産能力が使用できるか。
●見積価格はどうか。
関連用語: 請納期
Due Date; Delivery Date
購買オーダーおよび外注オーダーにおいて納期とは、部品や原材料など、業者に品目を納めさせる期日のことであり、製造オーダーにおいては、製品や組立品など、製造される品目を完成させる期日のことである。しかし、一般的に納期といった場合は、製品などを親企業や顧客に納める期日のことをいう。
関連用語: リードタイム計算
購買オーダーおよび外注オーダーにおいて納期とは、部品や原材料など、業者に品目を納めさせる期日のことであり、製造オーダーにおいては、製品や組立品など、製造される品目を完成させる期日のことである。しかし、一般的に納期といった場合は、製品などを親企業や顧客に納める期日のことをいう。
関連用語: リードタイム計算
Shipping Lead Time
出荷計画、顧客の注文などにより、工場あるいは倉庫に対して出荷指示がなされる。この出荷指示が行われてから、品物が梱包され、出荷されるまでの時間を出荷リードタイムという。
関連用語: リードタイム
出荷計画、顧客の注文などにより、工場あるいは倉庫に対して出荷指示がなされる。この出荷指示が行われてから、品物が梱包され、出荷されるまでの時間を出荷リードタイムという。
関連用語: リードタイム
Shipping Planning
受注オーダーの中から、近い期日に出荷が予定されているオーダーを対象として出荷計画を行う。これには、出荷予定表が用いられる。この出荷予定表を基に、次のように出荷計画が進められる。
●製品製造オーダーの確認:受注オーダーと関連する製品製造オーダーの作業状況をチェックし、出荷が可能か否かを確認する。
●顧客情報の確認:顧客に対する納入日、納入数、納入場所などの確認を行い、出荷指図書を作成する。
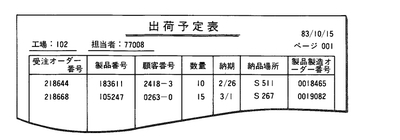
関連用語: 出荷管理
受注オーダーの中から、近い期日に出荷が予定されているオーダーを対象として出荷計画を行う。これには、出荷予定表が用いられる。この出荷予定表を基に、次のように出荷計画が進められる。
●製品製造オーダーの確認:受注オーダーと関連する製品製造オーダーの作業状況をチェックし、出荷が可能か否かを確認する。
●顧客情報の確認:顧客に対する納入日、納入数、納入場所などの確認を行い、出荷指図書を作成する。
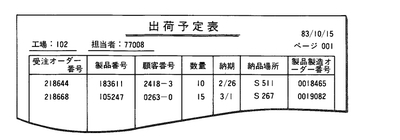
関連用語: 出荷管理
Shipping Control
製品製作の進捗により、顧客への引渡し日を確認して、出荷のための準備を行い、出荷の指示をする。出荷管理の機能は大きく、出荷計画と出荷検査とに分けられる。
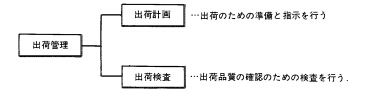
製品製作の進捗により、顧客への引渡し日を確認して、出荷のための準備を行い、出荷の指示をする。出荷管理の機能は大きく、出荷計画と出荷検査とに分けられる。
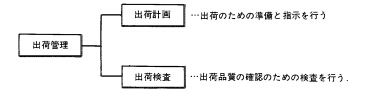
Backlog of Orders
バックログなどともいわれ、顧客から注文を受けた製品の数量あるいは金額に対して、まだ出荷していない残りの数量または金額のことをいう。受注残には、受注オーダー番号や製品番号、納期、数量などのほかに、現在組立中であるとか、出荷計画中であるとかいったオーダー状況が付与される。
関連用語: 出荷管理
バックログなどともいわれ、顧客から注文を受けた製品の数量あるいは金額に対して、まだ出荷していない残りの数量または金額のことをいう。受注残には、受注オーダー番号や製品番号、納期、数量などのほかに、現在組立中であるとか、出荷計画中であるとかいったオーダー状況が付与される。
関連用語: 出荷管理
Job Order
顧客から受けた注文を基に作成したオーダーを指す。普通、注文書を確認し請書を送付した時点で受注オーダーが作成される。受注オーダーの作成方法には、2通りの考え方がある。1つは、顧客からの注文、つまり顧客オーダーと1対1の形で受注オーダーを作成する場合と、顧客オーダーを工場の製造単位にまとめたり、分解したりして受注オーダーを作成する場合がある。前者は、受注生産型のタイプで後者は見込生産型の企業に多く見られる。
このオーダーには、製品、納期、数量のほかに顧客仕様やオプションなどが指定されており、これを基にして組立計画が編成される。
関連用語: オーダー
顧客から受けた注文を基に作成したオーダーを指す。普通、注文書を確認し請書を送付した時点で受注オーダーが作成される。受注オーダーの作成方法には、2通りの考え方がある。1つは、顧客からの注文、つまり顧客オーダーと1対1の形で受注オーダーを作成する場合と、顧客オーダーを工場の製造単位にまとめたり、分解したりして受注オーダーを作成する場合がある。前者は、受注生産型のタイプで後者は見込生産型の企業に多く見られる。
このオーダーには、製品、納期、数量のほかに顧客仕様やオプションなどが指定されており、これを基にして組立計画が編成される。
関連用語: オーダー
Customer Lead Time
顧客がある品物を販売店やセールスマンなどに注文した時から、その品物が顧客に渡るまでの時間あるいは期間のことである。したがって、顧客の目的とする品物が店頭に品揃えされている場合の顧客リードタイムは、その品物を包装して顧客に手渡すまでのわずかな時間である。しかし、店頭にない場合は、その品物を工場に発注するため、顧客リードタイムには梱包や輸送の時間を含むことになる。また、特注品などは、顧客仕様に合わせてつくるので、梱包、輸送の時間のほかに、製造や部品、材料の手配などの時間が含まれるため、数ヵ月に及ぶこともある。
製造および販売側にとって、顧客リードタイムを短くすることは、顧客に対するサービス向上につながり、販売戦略上の重要な要素となる。
関連用語: リードタイム
顧客がある品物を販売店やセールスマンなどに注文した時から、その品物が顧客に渡るまでの時間あるいは期間のことである。したがって、顧客の目的とする品物が店頭に品揃えされている場合の顧客リードタイムは、その品物を包装して顧客に手渡すまでのわずかな時間である。しかし、店頭にない場合は、その品物を工場に発注するため、顧客リードタイムには梱包や輸送の時間を含むことになる。また、特注品などは、顧客仕様に合わせてつくるので、梱包、輸送の時間のほかに、製造や部品、材料の手配などの時間が含まれるため、数ヵ月に及ぶこともある。
製造および販売側にとって、顧客リードタイムを短くすることは、顧客に対するサービス向上につながり、販売戦略上の重要な要素となる。
関連用語: リードタイム
Delivery Date
顧客からの注文情報の1つであり、顧客に製品(商品)を受け渡さねばならない納入期限または納入期日のことをいう。顧客オーダーの納期として設定される。この納期は、普通、営業サイドの情報として記録され、工場では、顧客納期を基に工場サイドの納期を設定する。これは、出荷の作業日数や輸送日数を考慮する場合もあるし、また複数の顧客オーダーを工場の製作単位に合わせてまとめることもあるからである。この受注オーダーにつけられた納期は、工場納期を示すことになる。
関連用語: 納期
顧客からの注文情報の1つであり、顧客に製品(商品)を受け渡さねばならない納入期限または納入期日のことをいう。顧客オーダーの納期として設定される。この納期は、普通、営業サイドの情報として記録され、工場では、顧客納期を基に工場サイドの納期を設定する。これは、出荷の作業日数や輸送日数を考慮する場合もあるし、また複数の顧客オーダーを工場の製作単位に合わせてまとめることもあるからである。この受注オーダーにつけられた納期は、工場納期を示すことになる。
関連用語: 納期
Customer Order
顧客から注文を受けた時に作成されるオーダーで、顧客の注文情報である。商品番号や納期、数量のほかに、顧客番号や注文を受けた担当者の番号などが付与される。受注管理では、この顧客オーダーを基に、工場の製造単位である受注オーダーを作成して、生産計画へ引き渡す。
関連用語: オーダー
顧客から注文を受けた時に作成されるオーダーで、顧客の注文情報である。商品番号や納期、数量のほかに、顧客番号や注文を受けた担当者の番号などが付与される。受注管理では、この顧客オーダーを基に、工場の製造単位である受注オーダーを作成して、生産計画へ引き渡す。
関連用語: オーダー
顧客または販売部門からの引合情報を基に、引合のあった製品の数量、納期について、生産可能か、あるいは納入可能かを検討し、いついつまでに納入できるか否かを回答することをいう。納入可能となった場合には、通常、予約や受注として登録され、在庫や資源への引当が行われる。
関連用語: 受注管理
関連用語: 受注管理
Lot Sizing ロットサイジング
MRPは、製品の必要量を基に、部品や素材の正味所要量を参照する。しかし、この所要量そのままでは発注や製造に適さない場合がある。ロットまとめとは、コストダウンや作業効率を考えて、算出された正味所要量をあるまとまった量にして、手配することである。
ロットまとめの種類には、期間を考慮してまとめる方法と数量によりまとめる方法とに大きく分けられる。前者には"固定期間まとめ"があり、一般に、需要が不規則で比較的高価な品目などはこれに適する。後者には"固定数量まとめ"や"経済発注量まとめ"などがあり、比較的需要が安定している品目などに適用される。その他、ロットまとめには図に示すような種類がある。
関連用語: MRP
MRPは、製品の必要量を基に、部品や素材の正味所要量を参照する。しかし、この所要量そのままでは発注や製造に適さない場合がある。ロットまとめとは、コストダウンや作業効率を考えて、算出された正味所要量をあるまとまった量にして、手配することである。
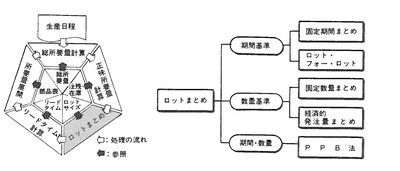
関連用語: MRP
Lot for Lot
ロットまとめの1つの方法で、素正味発注量(DOQ:Discrete Order Quantity)などとも呼ばれ、各期間に発生した正味所要量をそのままオーダー数量とする。これは主に、高価な品目や断続的に要求が発生する品目によく使われる。また、固定期間まとめで1期間を指定した時と同じになる。
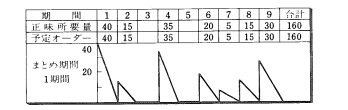
関連用語: ロットまとめ
ロットまとめの1つの方法で、素正味発注量(DOQ:Discrete Order Quantity)などとも呼ばれ、各期間に発生した正味所要量をそのままオーダー数量とする。これは主に、高価な品目や断続的に要求が発生する品目によく使われる。また、固定期間まとめで1期間を指定した時と同じになる。
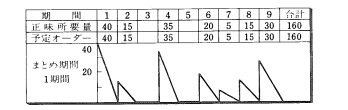
関連用語: ロットまとめ
Level by Level
"レベルごとに"という意味で、普通"レベル・バイ・レベルの展開"として使われる。通常、共通品はいろいろな製品に使われ、またその使われるレベルもまちまちである。しかし、ある品目が、いろいろな製品や何段ものレベルに使われ、展開では何度となく現われたとしても、総所要量計算や正味所要量計算それにロットまとめなどの一連のMRP処理は、1品目につき1度だけ行えばよい。このことからMRPの所要量展開はレベル・バイ・レベルの展開でなければならない。たとえば、図の品目bは、レベル1と2に使われているが、レベル・バイ・レベルの展開では、レベル1で展開された品目bはレベル2の品目bと一緒に所要量計画が行われる。
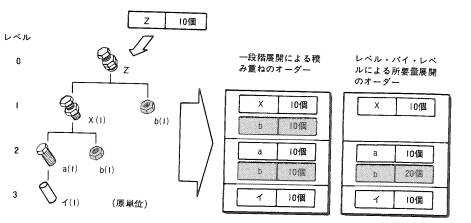
関連用語: 所要量展開、レベルテーブル、ローレベルコード、アクティビティ・チエーン
"レベルごとに"という意味で、普通"レベル・バイ・レベルの展開"として使われる。通常、共通品はいろいろな製品に使われ、またその使われるレベルもまちまちである。しかし、ある品目が、いろいろな製品や何段ものレベルに使われ、展開では何度となく現われたとしても、総所要量計算や正味所要量計算それにロットまとめなどの一連のMRP処理は、1品目につき1度だけ行えばよい。このことからMRPの所要量展開はレベル・バイ・レベルの展開でなければならない。たとえば、図の品目bは、レベル1と2に使われているが、レベル・バイ・レベルの展開では、レベル1で展開された品目bはレベル2の品目bと一緒に所要量計画が行われる。
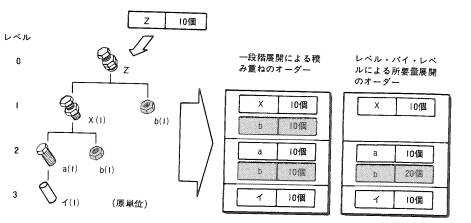
関連用語: 所要量展開、レベルテーブル、ローレベルコード、アクティビティ・チエーン
Level Table
MRPをレベル・バイ・レベルつまり、レベルの小さなものから順に実行するための管理用のテーブルである。レベルテーブルの縦方向は、ローレベルの最大値分だけ確保する。これは製品構成の深さなどとも呼ばれる。また横方向は同じレベルの品目点数分だけ必要になる。これは製品構成の深さに対して広がりとも呼ばれ、この広がりがいくつになるかを設定することは難しい。そこで一般的には横の広がりについては、アクティビティ・チェーンという方法を用いて管理する。いま、アクティビティ・チェーンを考慮しないとしたら、レベルテーブルには図のように各品目が設定され、レベルの小さな品目、たとえばレベル1のP、Xなどから順にMRPが実行される。
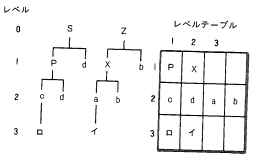
関連用語: 所要量展開、アクティビティ・チェーン、ローレベルコード
MRPをレベル・バイ・レベルつまり、レベルの小さなものから順に実行するための管理用のテーブルである。レベルテーブルの縦方向は、ローレベルの最大値分だけ確保する。これは製品構成の深さなどとも呼ばれる。また横方向は同じレベルの品目点数分だけ必要になる。これは製品構成の深さに対して広がりとも呼ばれ、この広がりがいくつになるかを設定することは難しい。そこで一般的には横の広がりについては、アクティビティ・チェーンという方法を用いて管理する。いま、アクティビティ・チェーンを考慮しないとしたら、レベルテーブルには図のように各品目が設定され、レベルの小さな品目、たとえばレベル1のP、Xなどから順にMRPが実行される。
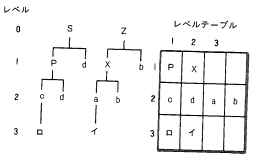
関連用語: 所要量展開、アクティビティ・チェーン、ローレベルコード
Calculating Lead Time 先行計算、手番計算
オーダーの納期を基に、リードタイムを用いて購買オーダーであれば発注の予定日、製造オーダーであれば製造指示の予定日となるオーダーの予定開始日を算出することをリードタイム計算という。このリードタイム計算の方法には大きく2通りある。1つは固定リードタイム計算であり、他方は変動リードタイム計算である。
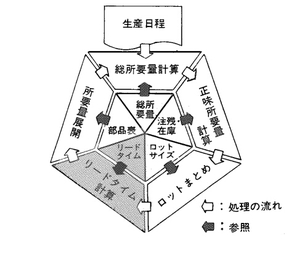
関連用語: 固定リードタイム計算、変動リードタイム計算
オーダーの納期を基に、リードタイムを用いて購買オーダーであれば発注の予定日、製造オーダーであれば製造指示の予定日となるオーダーの予定開始日を算出することをリードタイム計算という。このリードタイム計算の方法には大きく2通りある。1つは固定リードタイム計算であり、他方は変動リードタイム計算である。
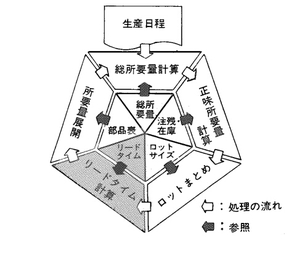
関連用語: 固定リードタイム計算、変動リードタイム計算
Planned Release Date
購買オーダーであれば発注の予定日であり、製造オーダーであれば製造指示の予定日に該当する。従属需要品目のオーダーについて、その予定開始日の設定はMRPのリードタイム計算により行われる。
関連用語: リードタイム計算
購買オーダーであれば発注の予定日であり、製造オーダーであれば製造指示の予定日に該当する。従属需要品目のオーダーについて、その予定開始日の設定はMRPのリードタイム計算により行われる。
関連用語: リードタイム計算
期間数量まとめやPPBにおいて、端数まるめが行われた場合の、正味所要量とまるめられた予定オーダーとの差を余剰数という。この余剰数は、以降の期間の正味所要量へ引当てられる。
たとえば、図の期間1の予定オーダーの数量は当初、55個であったが、まるめることによって60個となり、5個の余剰数が発生する。ここで余剰数の引当計算を行わない場合、期間4の予定オーダーは正味所要量35個がまるめられて40個となるが、余剰数の引当計算を行うことにより、期間3の余剰数5個は期間4の正味所要量35個に引当てられ、その予定オーダーは30個となる。
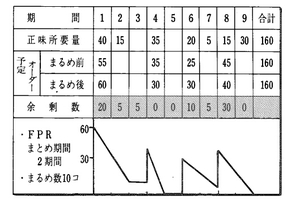
関連用語: 端数まるめ
たとえば、図の期間1の予定オーダーの数量は当初、55個であったが、まるめることによって60個となり、5個の余剰数が発生する。ここで余剰数の引当計算を行わない場合、期間4の予定オーダーは正味所要量35個がまるめられて40個となるが、余剰数の引当計算を行うことにより、期間3の余剰数5個は期間4の正味所要量35個に引当てられ、その予定オーダーは30個となる。
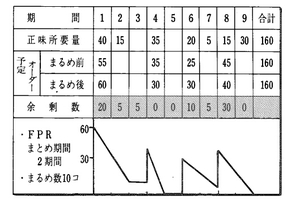
関連用語: 端数まるめ
リードタイム計算の1つの手法で、ロットの大きさにより、リードタイムを変動させる方法である。一般には、品目に設定された段取や移動などの時間は固定として捉え、1個当たりの実作業時間を用いて、次の式により求める。
変動リードタイムは、ロット・フォー・ロットや固定期間まとめのように、たえず設定されたオーダーの所要量が変動する場合には有効である。
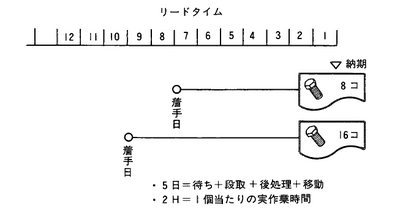
関連用語: リードタイム計算
予定開始日=納期-〔(待ち+段取+後処理+移動)+オーダーの所要量×1個当たりの実作業時間〕
変動リードタイムは、ロット・フォー・ロットや固定期間まとめのように、たえず設定されたオーダーの所要量が変動する場合には有効である。
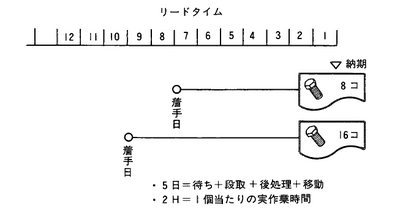
関連用語: リードタイム計算
Failure Rate
上位の品目をつくる際に、部品や素材が不良となる割合を示す。不良率は、あくまでも上位品目との関係によって決まるものであって、部品や素材の種類によって決まるものではない。このような意味において、不良率は製品構成(P/S)に設定する場合が多い。また、所要量展開における、不良率を考慮した下位品目の所要量の算出は、次式で求めることができる。
関連用語: 所要量計算
上位の品目をつくる際に、部品や素材が不良となる割合を示す。不良率は、あくまでも上位品目との関係によって決まるものであって、部品や素材の種類によって決まるものではない。このような意味において、不良率は製品構成(P/S)に設定する場合が多い。また、所要量展開における、不良率を考慮した下位品目の所要量の算出は、次式で求めることができる。
下位品目所要量=上位品目所要量×原単位×1/1-不良率
関連用語: 所要量計算
Yield
ある品目をつくった際、その中に含まれる良品の割合をいい、通常、製造数に対する良品数の比率で示される。
また、歩留を材料の面で考えると原材料生産性となり、次の式で表現される。
歩留そのものは、品目自体についての良品の割合である。このため、一般的には、品目(P/M)の項目として設定される。
関連用語: 所要量計算
ある品目をつくった際、その中に含まれる良品の割合をいい、通常、製造数に対する良品数の比率で示される。
歩留=良品数/製造数
また、歩留を材料の面で考えると原材料生産性となり、次の式で表現される。
原材料生産性=生産量/原材料使用量
歩留そのものは、品目自体についての良品の割合である。このため、一般的には、品目(P/M)の項目として設定される。
関連用語: 所要量計算
Allocation
正味所要量計算 製品や部品をつくるためのオーダーやサービス部品などの要求に対し、必要な部品または原材料などの品目を必要な分だけあらかじめ確保することである。一般に、"引当(ひきあて)"という場合、2つの解釈がある。1つは引当てられた品目数量を確保し、他の要求に対し流用しない方法で"確定引当"という。また、他方は、単に数量があるかないかの確認を行うだけのやり方で"予備引当"と呼ぶ。
MRPにおける在庫引当は、この予備引当に当たり、すでに在庫されている数量とまだ納入されていない発注残への引当を行う。これは、正味所要量計算ともいわれる。
関連用語: 発注残
正味所要量計算 製品や部品をつくるためのオーダーやサービス部品などの要求に対し、必要な部品または原材料などの品目を必要な分だけあらかじめ確保することである。一般に、"引当(ひきあて)"という場合、2つの解釈がある。1つは引当てられた品目数量を確保し、他の要求に対し流用しない方法で"確定引当"という。また、他方は、単に数量があるかないかの確認を行うだけのやり方で"予備引当"と呼ぶ。
MRPにおける在庫引当は、この予備引当に当たり、すでに在庫されている数量とまだ納入されていない発注残への引当を行う。これは、正味所要量計算ともいわれる。
関連用語: 発注残
期間を固定した"まとめ"方や、PPBなどは、まとめられた数量がそのたびごとに変化する。これを発注や製造指示に適した形に補正する必要が出てくる。この補正を、一般にロットの端数まるめという。まるめることによって発生した余剰数は、次の必要数に引当られる。このことで、正味所要量に近い形で予定オーダーの数量が決定する。
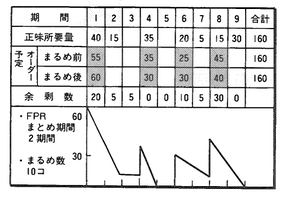
関連用語: ロットまとめ
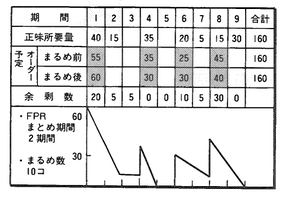
関連用語: ロットまとめ
Bucket
MRP計画表で示された1つひとつの期間を指す。"バケットの大きさ"といった場合には、1期間の大きさを表わし、この大きさをどのくらいまたは何日に設定するかで、MRPの計画の細かさが決まってくる。
一般的には、バケットの大きさは3日から1週間くらいで、かつ計画期間は、3ヵ月から6ヵ月くらいである。仮にバケットの大きさを3日とし、3ヵ月の計画期間とした時、毎月の稼働日を22日に設定すると、22バケット必要になる。このバケット数は、MRPの処理時間に関連するため、必要期間内で設定する方がよい。バケットの大きさの決定要因としては、製造指示のサイクルや実績収集の度合など、購買や製造の管理の細かさによる。
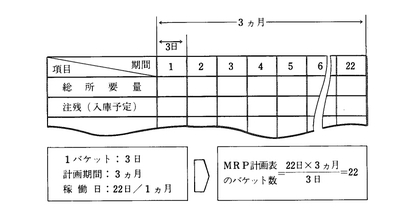
関連用語: MRP計画表
MRP計画表で示された1つひとつの期間を指す。"バケットの大きさ"といった場合には、1期間の大きさを表わし、この大きさをどのくらいまたは何日に設定するかで、MRPの計画の細かさが決まってくる。
一般的には、バケットの大きさは3日から1週間くらいで、かつ計画期間は、3ヵ月から6ヵ月くらいである。仮にバケットの大きさを3日とし、3ヵ月の計画期間とした時、毎月の稼働日を22日に設定すると、22バケット必要になる。このバケット数は、MRPの処理時間に関連するため、必要期間内で設定する方がよい。バケットの大きさの決定要因としては、製造指示のサイクルや実績収集の度合など、購買や製造の管理の細かさによる。
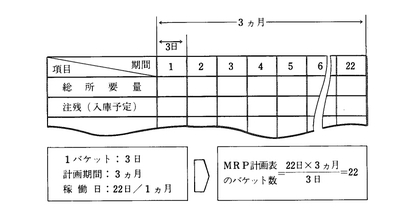
関連用語: MRP計画表
Regeneration リジェネレーション
MRPの運用方法には、前回の計画に対する変更分のみを入力する方法と、毎回すべての生産計画を入力するやり方の2通りがある。前者は、正味変更といわれ、後者を日程再計画と呼ぶ。日程再計画はリジェネレーションなどとも称され、前回立案した計画をまったく白紙にもどして、もう1度すべての生産計画を入力してMRPを実行する方法である。たとえば、図の例では、前回の生産計画と異なる部分は、製品Zの期間6の所要量が15個から25個に変更になっただけである。しかし、日程再計画では、この所要量を25個に直してすべての生産計画を新たに入力する。
このやり方は、運用方法が比較的手軽なことから、多くの企業が採用している。また、このやり方は生産計画のすべてを対象として再度やり直すため、前回の間違いが累積されず、維持するデータ量が少なくて済む反面、1回当たりのMRPにかなり多くの処理時間を費やすことになる。したがって、MRPの運用サイクルは、週単位のような比較的長い期間がとられることが多い。
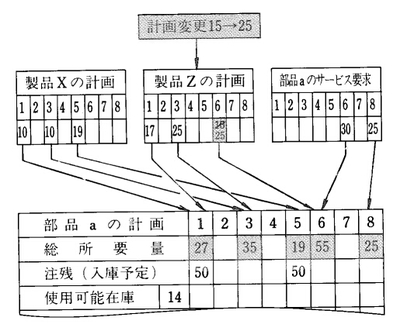
反意語: 正味変更
MRPの運用方法には、前回の計画に対する変更分のみを入力する方法と、毎回すべての生産計画を入力するやり方の2通りがある。前者は、正味変更といわれ、後者を日程再計画と呼ぶ。日程再計画はリジェネレーションなどとも称され、前回立案した計画をまったく白紙にもどして、もう1度すべての生産計画を入力してMRPを実行する方法である。たとえば、図の例では、前回の生産計画と異なる部分は、製品Zの期間6の所要量が15個から25個に変更になっただけである。しかし、日程再計画では、この所要量を25個に直してすべての生産計画を新たに入力する。
このやり方は、運用方法が比較的手軽なことから、多くの企業が採用している。また、このやり方は生産計画のすべてを対象として再度やり直すため、前回の間違いが累積されず、維持するデータ量が少なくて済む反面、1回当たりのMRPにかなり多くの処理時間を費やすことになる。したがって、MRPの運用サイクルは、週単位のような比較的長い期間がとられることが多い。
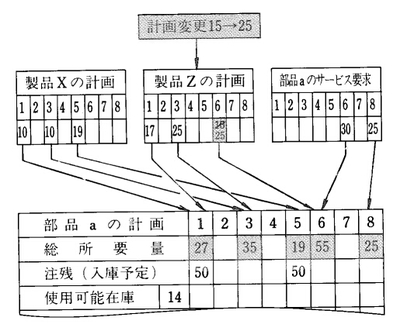
反意語: 正味変更
Order Cancel オーダーキャンセル
MRPによる勧告の1つで、オーダーキャンセルともいわれる。これは何らかの理由で、すでに手配済となっているオーダーを取消す場合に用いられる。たとえば、図のような部品aの計画に対して、製品Zの期間3が20個、期間6が15個キャンセルされたとすると、部品aの期間3の総所要量は15個となり、期間6の総所要量は0となる。このような状態の時、期間5にある総所要量19個は、期間4の使用可能在庫22個でまかなうことができる。このため、期間5の注残50個は、その期間を納期とする必要性がなくなり、期間6、期間7へと順次納期調整が行われ、結果的に部品aの計画期間内では不要なオーダーであることが判別する。このように注残や仕掛となっているオーダーの中止をする勧告を取消という。
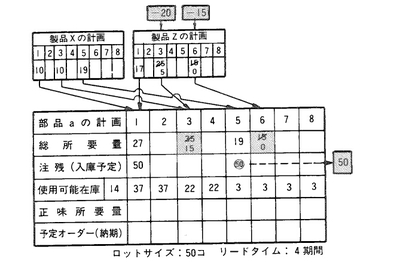
関連用語: 勧告
MRPによる勧告の1つで、オーダーキャンセルともいわれる。これは何らかの理由で、すでに手配済となっているオーダーを取消す場合に用いられる。たとえば、図のような部品aの計画に対して、製品Zの期間3が20個、期間6が15個キャンセルされたとすると、部品aの期間3の総所要量は15個となり、期間6の総所要量は0となる。このような状態の時、期間5にある総所要量19個は、期間4の使用可能在庫22個でまかなうことができる。このため、期間5の注残50個は、その期間を納期とする必要性がなくなり、期間6、期間7へと順次納期調整が行われ、結果的に部品aの計画期間内では不要なオーダーであることが判別する。このように注残や仕掛となっているオーダーの中止をする勧告を取消という。
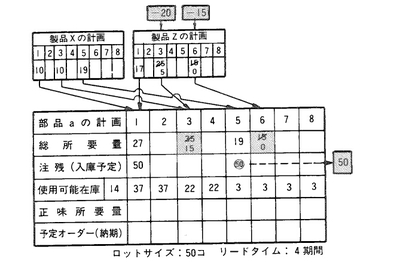
関連用語: 勧告
Order
一般に手配とは、ものの調達や生産を円滑にするために、各必要事項の準備を行うことをいう。情報システムのデータ名称として"手配"という場合には、購買や製造に必要なオーダー情報を集めたもので、オーダー番号、品番、納期、所要量、オーダー状況などの項目をもっている。
一般に手配とは、ものの調達や生産を円滑にするために、各必要事項の準備を行うことをいう。情報システムのデータ名称として"手配"という場合には、購買や製造に必要なオーダー情報を集めたもので、オーダー番号、品番、納期、所要量、オーダー状況などの項目をもっている。
所要量展開の1機能で、一段階所要量展開で、展開され算出された子品目の所要量をレベルの小さな順に1品目ずつ取り出す機能をいう。取り出された所要量は、正味所要量計算やロットまとめなどのMRPの一連の手配計画が行われる。
次に品目Aの子品目の所要量を抽出する例を示す。この例では、最初の抽出依頼により、レベルテーブルのgを参照し、これを基に品目gに登録されている所要量20個をまず抽出する。この時、gの抽出は終了したので、品目gのアクティビティ・チェーンに登録されているfをレベルテーブルに登録しておく。抽出された品目gの所要量は総所要量計算、正味所要量計算が行われ、gの予定オーダがつくられる。この品目gの計画が終了すると次は品目fの抽出が始まる。これも品目gと同じようにレベルテーブルを参照して所要量を抽出する。このようにして、以降も同様の手順で抽出のあるたびに、レベルテーブルの小さなレベルに登録されている品目から順に、その所要量を抽出して、MRPの一連の計画を行う(次頁図参照)。
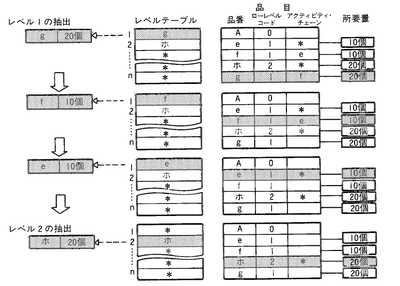
関連用語: 所要量展開、一段階所要量展開
次に品目Aの子品目の所要量を抽出する例を示す。この例では、最初の抽出依頼により、レベルテーブルのgを参照し、これを基に品目gに登録されている所要量20個をまず抽出する。この時、gの抽出は終了したので、品目gのアクティビティ・チェーンに登録されているfをレベルテーブルに登録しておく。抽出された品目gの所要量は総所要量計算、正味所要量計算が行われ、gの予定オーダがつくられる。この品目gの計画が終了すると次は品目fの抽出が始まる。これも品目gと同じようにレベルテーブルを参照して所要量を抽出する。このようにして、以降も同様の手順で抽出のあるたびに、レベルテーブルの小さなレベルに登録されている品目から順に、その所要量を抽出して、MRPの一連の計画を行う(次頁図参照)。
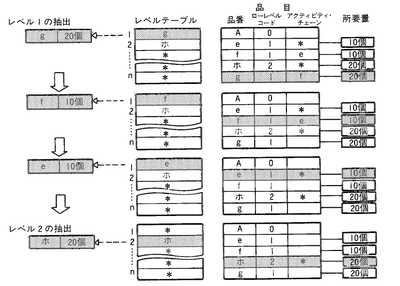
関連用語: 所要量展開、一段階所要量展開
Damper
MRPを運用していくうえで計画に対する変更は必ず発生する。この変更には、計画をまったくだめにしてしまうような大きな変更から、ほとんど計画には影響しない小さな変更まである。しかし、何らかの歯止めがなければ、MRPはすべての変更を受入れて新しい計画を編成してしまう。ダンパーとは、計画にほとんど影響しない小さな変更の場合、MRPの再計画をしないように吸収してしまうことをいう。一般に変更は、納期と数量によって行われ、これに対応してダンパーも期間による吸収と数量による吸収とがあり、前者を期間ダンパー、後者を数量ダンパーという。期間ダンパーは、納期の前後それぞれ何日以内、数量ダンパーはオーダー数量の上下それぞれ何個以内の変更であれば、MRPの再計画は行われない。
関連用語: 期間ダンパー、数量ダンパー
MRPを運用していくうえで計画に対する変更は必ず発生する。この変更には、計画をまったくだめにしてしまうような大きな変更から、ほとんど計画には影響しない小さな変更まである。しかし、何らかの歯止めがなければ、MRPはすべての変更を受入れて新しい計画を編成してしまう。ダンパーとは、計画にほとんど影響しない小さな変更の場合、MRPの再計画をしないように吸収してしまうことをいう。一般に変更は、納期と数量によって行われ、これに対応してダンパーも期間による吸収と数量による吸収とがあり、前者を期間ダンパー、後者を数量ダンパーという。期間ダンパーは、納期の前後それぞれ何日以内、数量ダンパーはオーダー数量の上下それぞれ何個以内の変更であれば、MRPの再計画は行われない。
関連用語: 期間ダンパー、数量ダンパー
Calculating Gross Requirements
MRPの計画機能のうち、最初に行われる計算である。これは、MRP計画表を使って、手配計画をしようとしている品目が要求されている数量を期間別に捉え、これらをまとめて総所要量を算出する。仮に、図のような製品X、Zの生産計画と部品aのサービス要求がある場合、部品aの総所要量は図のように求められる。また、総所要量計算によって期間別にまとめられた総所要量は、次に在庫や注残への引当をする正味所要量計算の機能へと引き継がれる。
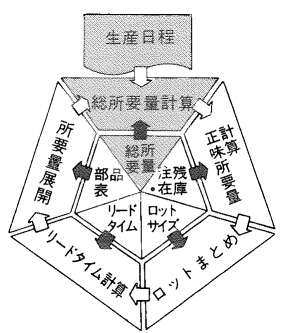
関連用語: 資材所要量計画
MRPの計画機能のうち、最初に行われる計算である。これは、MRP計画表を使って、手配計画をしようとしている品目が要求されている数量を期間別に捉え、これらをまとめて総所要量を算出する。仮に、図のような製品X、Zの生産計画と部品aのサービス要求がある場合、部品aの総所要量は図のように求められる。また、総所要量計算によって期間別にまとめられた総所要量は、次に在庫や注残への引当をする正味所要量計算の機能へと引き継がれる。
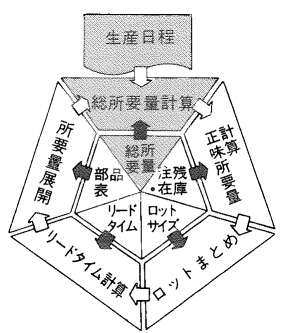
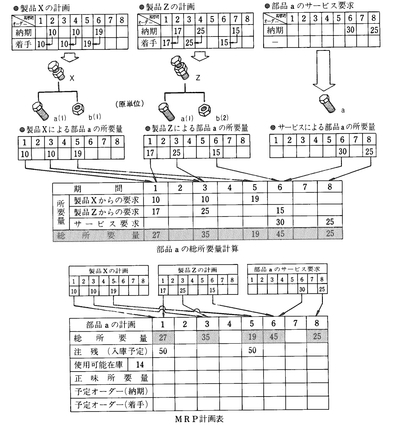
Gross Requirements
各品目ごとの要求量を所要量という。これには、上位品目をつくるための部品として要求されるものや、サービスパーツとして要求されるものがある。そして、これらの所要量を期間ごとにまとめたものを総所要量という。
関連用語: 総所要量計算
各品目ごとの要求量を所要量という。これには、上位品目をつくるための部品として要求されるものや、サービスパーツとして要求されるものがある。そして、これらの所要量を期間ごとにまとめたものを総所要量という。
関連用語: 総所要量計算
Requirements Explosion
MRPの1機能で、作成されたオーダーを基に部品表を参照して子品目に展開し、各々の品目の所要量の算出を行う。 所要量展開の機能は、大きく一段階展開機能と抽出機能とに分けられる。一段階展開機能では、部品展開をしながら子品目の所要量を計算し、その結果をローレベルコードの順に登録する。また、抽出機能では、ローレベルコードの上から順に登録されている品目を抜き出す。これら2つの機能は、互いに対となって動作し、レベルテーブル、アクティビティ・チェーンを用いて、レベル・バイ・レベルの展開を行う。
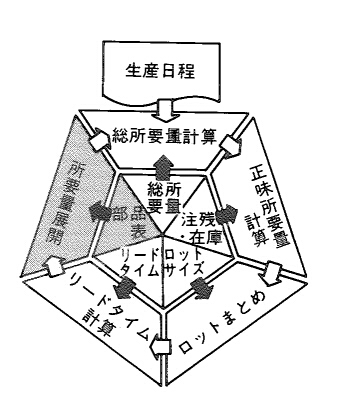
関連用語: 資材所要量計画
MRPの1機能で、作成されたオーダーを基に部品表を参照して子品目に展開し、各々の品目の所要量の算出を行う。 所要量展開の機能は、大きく一段階展開機能と抽出機能とに分けられる。一段階展開機能では、部品展開をしながら子品目の所要量を計算し、その結果をローレベルコードの順に登録する。また、抽出機能では、ローレベルコードの上から順に登録されている品目を抜き出す。これら2つの機能は、互いに対となって動作し、レベルテーブル、アクティビティ・チェーンを用いて、レベル・バイ・レベルの展開を行う。
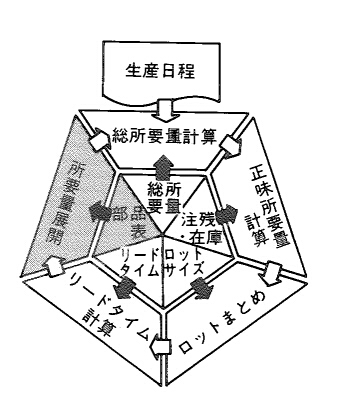
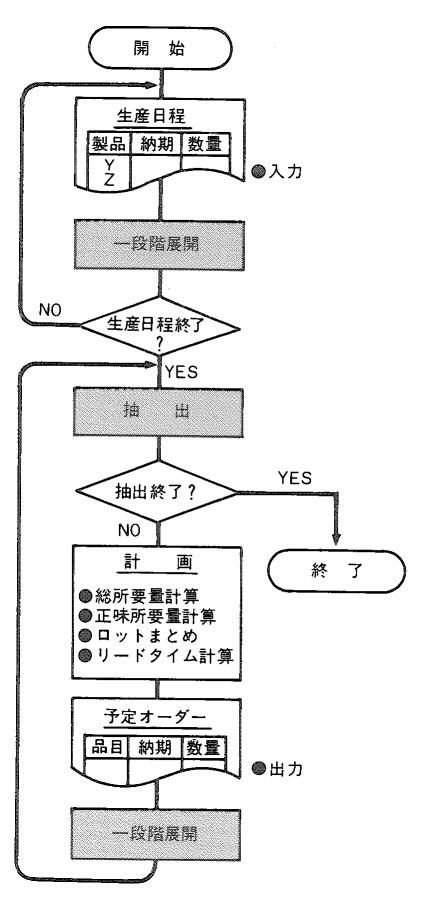
Pegged Requirements
ペギングともいわれ、製品、組立品、部品、原材料といった製品の構成にそって、これらのオーダー間の関連を保っておくことをいう。このことで、次のような対処が可能となる。
●納期遅れなどの問題が発生したオーダーが、どの製品オーダーに影響を与えるかがわかる。
●設計変更の影響するオーダーが把握できる。
●分割納入や先送りなどの指示がしやすい。
●在庫や注残の引当状況を確認する。
また、所要量結合のもち方には、一段階所要量結合と完全所要量結合がある。
ペギングともいわれ、製品、組立品、部品、原材料といった製品の構成にそって、これらのオーダー間の関連を保っておくことをいう。このことで、次のような対処が可能となる。
●納期遅れなどの問題が発生したオーダーが、どの製品オーダーに影響を与えるかがわかる。
●設計変更の影響するオーダーが把握できる。
●分割納入や先送りなどの指示がしやすい。
●在庫や注残の引当状況を確認する。
また、所要量結合のもち方には、一段階所要量結合と完全所要量結合がある。
Calculating Requirements
所要量展開の1機能で、上位品目の必要数より該当品目がどれだけ必要なのかを計算によって求めることをいう。所要量計算の対象となる品目は従属需要品目であり、上位品目の所要量と該当品目の原単位を基に計算される。
次式は、該当品目の不良率を考慮した場合の所要量計算式である。
この式での上位品目の所要量とは、展開前の品目のオーダー数量で、これに製品構成に設定されている原単位を乗じて、子品目の所要量を算出する。なお、不良率は製品構成に設定する例が多い。
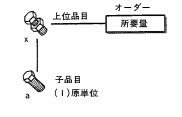
関連用語: 一段階所要量展開
所要量展開の1機能で、上位品目の必要数より該当品目がどれだけ必要なのかを計算によって求めることをいう。所要量計算の対象となる品目は従属需要品目であり、上位品目の所要量と該当品目の原単位を基に計算される。
次式は、該当品目の不良率を考慮した場合の所要量計算式である。
所要量=上位品目の所要量×原単位×1/1-不良率
この式での上位品目の所要量とは、展開前の品目のオーダー数量で、これに製品構成に設定されている原単位を乗じて、子品目の所要量を算出する。なお、不良率は製品構成に設定する例が多い。
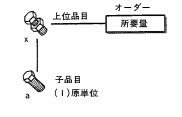
関連用語: 一段階所要量展開
Requirements
リクワイアメントともいわれ、広義では、上位品目からの要求量を指す。この意味で、総所要量や正味所要量それにオーダー数量も所要量といえる。狭義での所要量は、所要量計算により求められた必要量を示す。これは、MRPの1機能である総所要量計算へと引継がれる。
関連用語: 所要量計算
リクワイアメントともいわれ、広義では、上位品目からの要求量を指す。この意味で、総所要量や正味所要量それにオーダー数量も所要量といえる。狭義での所要量は、所要量計算により求められた必要量を示す。これは、MRPの1機能である総所要量計算へと引継がれる。
関連用語: 所要量計算
Net Change、ネットチェンジ
MRPの運用方法には、毎回すべての生産計画を入力するやり方と、前回からの変更分のみを入力する方法の2通りがある。前者は、日程再計画といわれ、後者は正味変更と呼ばれる。
正味変更は、ネットチェンジなどとも称され、前回の計画に対し、その後変更が発生した差異分のみがMRPの対象となる。たとえば、図の例では、製品Zの生産計画の期間6の所要量15個が25個に変更された場合、前回計画した所要量15個との差異分+10個のみが正味変更としてMRPに入力される。このやり方は、今後のMRP運用の方法として多くの企業で現在検討されている。
これは、処理のたびにすべての計画を入力する日程再計画に比べ、変更の発生した部分だけの計画を行うため、1回当たりのMRP処理時間が短くて済み、頻繁にMRPを実行することが可能となる。日程再計画では、日々の変更や計画追加を一定期間ためておいて、月に1回ないしは週に1回MRP処理をするのが一般的である。正味変更のように毎日実行することは、時間の面で難しい。多品種少量でかつ多発する計画変更に迅速に対応していくには正味変更は非常に適している。しかし、すべての計画をやり直すことはしないため、間違いが累積されたり、維持するデータ量が多く、また運用の方法が難しいなど、検討すべき事項も多い。
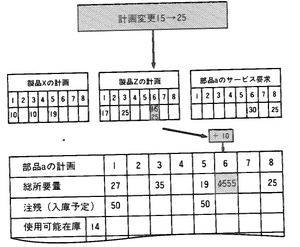
反意語: 日程再計画
MRPの運用方法には、毎回すべての生産計画を入力するやり方と、前回からの変更分のみを入力する方法の2通りがある。前者は、日程再計画といわれ、後者は正味変更と呼ばれる。
正味変更は、ネットチェンジなどとも称され、前回の計画に対し、その後変更が発生した差異分のみがMRPの対象となる。たとえば、図の例では、製品Zの生産計画の期間6の所要量15個が25個に変更された場合、前回計画した所要量15個との差異分+10個のみが正味変更としてMRPに入力される。このやり方は、今後のMRP運用の方法として多くの企業で現在検討されている。
これは、処理のたびにすべての計画を入力する日程再計画に比べ、変更の発生した部分だけの計画を行うため、1回当たりのMRP処理時間が短くて済み、頻繁にMRPを実行することが可能となる。日程再計画では、日々の変更や計画追加を一定期間ためておいて、月に1回ないしは週に1回MRP処理をするのが一般的である。正味変更のように毎日実行することは、時間の面で難しい。多品種少量でかつ多発する計画変更に迅速に対応していくには正味変更は非常に適している。しかし、すべての計画をやり直すことはしないため、間違いが累積されたり、維持するデータ量が多く、また運用の方法が難しいなど、検討すべき事項も多い。
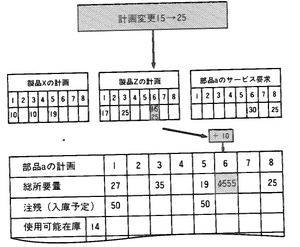
反意語: 日程再計画
Calculating Net Requirements
正味所要量計算は、MRPの計画機能の中の1機能である。これは、MRP計画表を使って求められた総所要量を基に、在庫や注残への引当を行い、正味所要量を算出する。この所要量は、手配をするために以降ロットまとめへと引き継がれる。正味所要量は、次に示す計算手順によって求まる。たとえば、下図の例で期間6の総所要量45個に対し、期間5の使用可能在庫は33個しか補充できず、12個分の手配が必要となる。これは正味所要量として設定される。
正味所要量計算手順
①引当可能在庫(t)=注残(t)+使用可能在庫(t-1)
②正味所要量(t)=引当可能在庫(t)-総所要量(t)
③正味所要量(t)が負の時は、その絶対値が該当期間の正味所要量となる。逆に正味所要量(t)が正の時は、総所要量(t)はすべて引当できたため、正味所要量は発生せず、使用可能在庫として扱われる。
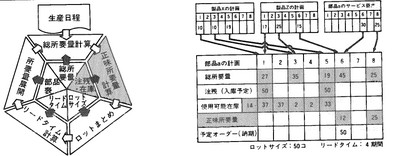
関連用語: 使用可能在庫、注残
正味所要量計算は、MRPの計画機能の中の1機能である。これは、MRP計画表を使って求められた総所要量を基に、在庫や注残への引当を行い、正味所要量を算出する。この所要量は、手配をするために以降ロットまとめへと引き継がれる。正味所要量は、次に示す計算手順によって求まる。たとえば、下図の例で期間6の総所要量45個に対し、期間5の使用可能在庫は33個しか補充できず、12個分の手配が必要となる。これは正味所要量として設定される。
正味所要量計算手順
①引当可能在庫(t)=注残(t)+使用可能在庫(t-1)
②正味所要量(t)=引当可能在庫(t)-総所要量(t)
③正味所要量(t)が負の時は、その絶対値が該当期間の正味所要量となる。逆に正味所要量(t)が正の時は、総所要量(t)はすべて引当できたため、正味所要量は発生せず、使用可能在庫として扱われる。
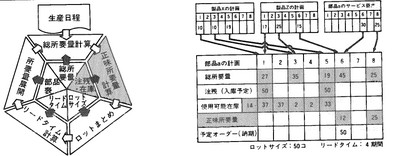
関連用語: 使用可能在庫、注残
あるオーダーからみて、そのオーダーがつくられる源泉となった上位品目のオーダーをいう。この上位オーダーのうち、最上位に当たるオーダー(最上位品目のオーダー)を最上位オーダーといい、直接上位のオーダーを親オーダーと呼ぶ。各オーダーには、(自分の)オーダー番号のほかに、最上位オーダー番号が付与され、オーダー関連がとられている。
関連用語: オーダー関連
関連用語: オーダー関連
Material Requirements Planning MRP
従属需要品目に対し、"必要なものを、必要なときに、必要なだけ"手配するための計画をいう。これは、一般にMRP(Material Requirements Planning)と呼ばれ、「アメリカ生産・在庫管理協会:APICS(American Production and Inventory Control Society)」の提唱により近年急速に普及してきた資材計画の手法である。詳細はMRPを参照。
従属需要品目に対し、"必要なものを、必要なときに、必要なだけ"手配するための計画をいう。これは、一般にMRP(Material Requirements Planning)と呼ばれ、「アメリカ生産・在庫管理協会:APICS(American Production and Inventory Control Society)」の提唱により近年急速に普及してきた資材計画の手法である。詳細はMRPを参照。
リードタイム計算の1つのやり方で、品目に設定したリードタイムを固定のものと考え、次の式によりオーダーの納期から予定開始日を求める方法である。
関連用語: リードタイム計算
予定開始日=納期-(リードタイム+安全リードタイム)
関連用語: リードタイム計算
Fixed Period Requirements FPR
FPR(Fixed Period Requirements)ともいわれるロットまとめの1手法で、各品目ごとにロットにまとめる期間を何期間分かを定め、その期間内の正味所要量の合計をオーダー数量とする方法である。これは、まとめの基準値も設定しやすく、また段取替えや発注回数を減らせるため、一般的によく使われている方法である。ただし、数量が変動するため、能力との調整を必要とする場合もある。また、まとめる期間の先頭(図の例では期間3)に正味所要量が発生していない場合には、その期間をとばして、次の期間を先頭にしてまとめる。
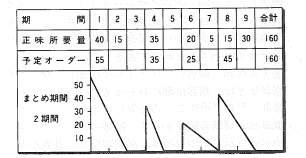
関連用語: ロットまとめ、LFL
FPR(Fixed Period Requirements)ともいわれるロットまとめの1手法で、各品目ごとにロットにまとめる期間を何期間分かを定め、その期間内の正味所要量の合計をオーダー数量とする方法である。これは、まとめの基準値も設定しやすく、また段取替えや発注回数を減らせるため、一般的によく使われている方法である。ただし、数量が変動するため、能力との調整を必要とする場合もある。また、まとめる期間の先頭(図の例では期間3)に正味所要量が発生していない場合には、その期間をとばして、次の期間を先頭にしてまとめる。
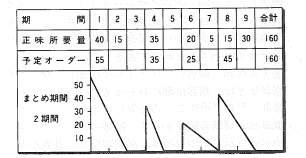
関連用語: ロットまとめ、LFL
Physical Unit
直接上位(親)の品目を1単位つくるのに必要とされる数量または重量や長さ、面積などである。これは上位品目と下位品目の関連で決まる情報であることから通常、部品表を表現する時に使われる製品構成マスターに設定される。これは員数などとも呼ばれ、MRPの所要量計算や出庫数量の算出などに用いられる。計算は、上位品目の必要量に該当品目の原単位を乗じて、各品目の要求量を算出する。また、長期間動いていない在庫の活用を図る場合にも原単位は使われる。これは、下位品目の在庫数を原単位で除することで、上位品目の製作可能数が算出される。
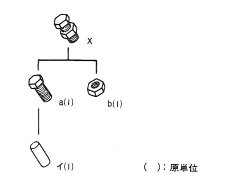
関連用語: 所要量計算
直接上位(親)の品目を1単位つくるのに必要とされる数量または重量や長さ、面積などである。これは上位品目と下位品目の関連で決まる情報であることから通常、部品表を表現する時に使われる製品構成マスターに設定される。これは員数などとも呼ばれ、MRPの所要量計算や出庫数量の算出などに用いられる。計算は、上位品目の必要量に該当品目の原単位を乗じて、各品目の要求量を算出する。また、長期間動いていない在庫の活用を図る場合にも原単位は使われる。これは、下位品目の在庫数を原単位で除することで、上位品目の製作可能数が算出される。
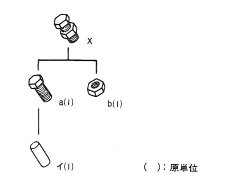
関連用語: 所要量計算
Economic Lot Size、EOQ、経済的発注量
品目は必要になったつど、必要数だけが発注(内作品の場合は作業指示)されるとは限らない。多くの場合、その品目に要する発注費(内作品の場合は段取などの準備費)と、在庫として維持する費用とのバランスの基で、発注量(内作品の場合は製造数量)が決められる。この発注量は、一般にロットとかロットサイズなどと呼ばれる。経済的ロットサイズとは、Economic Lot Sizeを略してELSなどとも呼ばれ、相反する発注費用と在庫維持費用とのバランスを考慮し、その総費用が最小となるような数量をいう。たとえば、図で示すようにロットを大きくすればするほど、平均在庫水準は増し、在庫維持費用も一定の比率で上昇する。しかし、運搬費用や段取費用は多くの数量に割り振られるため、1単位当りの発注費用は下降する。一方、ロットを小さくすればするほど、平均在庫水準は減り、在庫維持費用は下降する。しかし、これに反して1単位当りの発注費用は上昇する。このような発注費用と在庫維持費用との総費用が最小となる点が最も経済的なロットということになる。経済的ロットサイズはEOQ(Economic Order Quantity:経済発注量)ともいわれ、右の式で求められる。
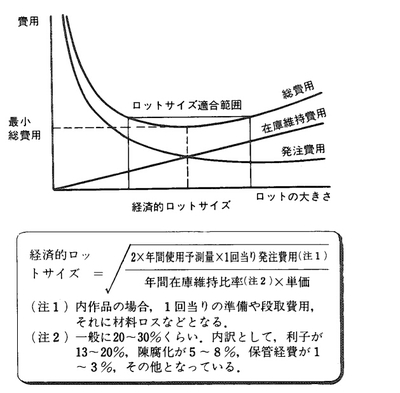
関連用語: ロットまとめ
品目は必要になったつど、必要数だけが発注(内作品の場合は作業指示)されるとは限らない。多くの場合、その品目に要する発注費(内作品の場合は段取などの準備費)と、在庫として維持する費用とのバランスの基で、発注量(内作品の場合は製造数量)が決められる。この発注量は、一般にロットとかロットサイズなどと呼ばれる。経済的ロットサイズとは、Economic Lot Sizeを略してELSなどとも呼ばれ、相反する発注費用と在庫維持費用とのバランスを考慮し、その総費用が最小となるような数量をいう。たとえば、図で示すようにロットを大きくすればするほど、平均在庫水準は増し、在庫維持費用も一定の比率で上昇する。しかし、運搬費用や段取費用は多くの数量に割り振られるため、1単位当りの発注費用は下降する。一方、ロットを小さくすればするほど、平均在庫水準は減り、在庫維持費用は下降する。しかし、これに反して1単位当りの発注費用は上昇する。このような発注費用と在庫維持費用との総費用が最小となる点が最も経済的なロットということになる。経済的ロットサイズはEOQ(Economic Order Quantity:経済発注量)ともいわれ、右の式で求められる。
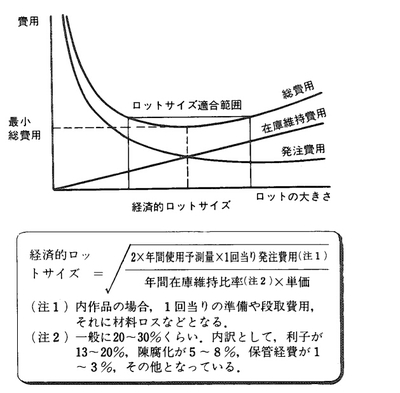
関連用語: ロットまとめ
Economic Order Quantity EOQ、経済的ロットサイズ
発注量を多くして、発注回数を少なくすれば、発注費用は減少するが、在庫量が増え、在庫維持費用が増大する。この逆に、在庫維持費用を抑えるために、発注量を少なくして、発注回数を増やすと、発注費用が増大する。経済発注量とは、Economic Order Quantityを略してEOQとも呼ばれ、このように相反する発注費用と在庫維持費用とのバランスを考慮し、その総費用が最小となるような最適数量をいう。MRPにおけるロットまとめの1手法としての経済的発注量では、事前に、各品目ごとの経済的発注量を算出してEOQ値として品目に登録しておく。MRPの実行に際しては、このEOQ値を基に、固定数量まとめと同じ方法でロットまとめが行われる。EOQ値の算定方法は経済的ロットサイズを、ロットまとめのやり方は、固定数量まとめをそれぞれ参照。
関連用語: ロットまとめ、固定数量まとめ
発注量を多くして、発注回数を少なくすれば、発注費用は減少するが、在庫量が増え、在庫維持費用が増大する。この逆に、在庫維持費用を抑えるために、発注量を少なくして、発注回数を増やすと、発注費用が増大する。経済発注量とは、Economic Order Quantityを略してEOQとも呼ばれ、このように相反する発注費用と在庫維持費用とのバランスを考慮し、その総費用が最小となるような最適数量をいう。MRPにおけるロットまとめの1手法としての経済的発注量では、事前に、各品目ごとの経済的発注量を算出してEOQ値として品目に登録しておく。MRPの実行に際しては、このEOQ値を基に、固定数量まとめと同じ方法でロットまとめが行われる。EOQ値の算定方法は経済的ロットサイズを、ロットまとめのやり方は、固定数量まとめをそれぞれ参照。
関連用語: ロットまとめ、固定数量まとめ
Order Timing Damper
小さな納期変更に対してMRPシステムが再計画をしないように変更を吸収することで、ダンパーの1つの方法である。これは、オーダーの納期の前後何日以内の変更であれば、変更されたオーダーの時期の再計画をしない方法で、細かな変更でも敏感に対応しようとするMRP機能に制限を与えるしくみを指す。一般的に、納期を早めた変更に対しては、納期遅れまたは欠品を防ぐためにMRPでの再計画を行う。これに対し納期を遅らせた変更は、欠品などの心配はなく、能力面での余裕があれば、MRPで細かな再計画は行わない。
関連用語: ダンパー
小さな納期変更に対してMRPシステムが再計画をしないように変更を吸収することで、ダンパーの1つの方法である。これは、オーダーの納期の前後何日以内の変更であれば、変更されたオーダーの時期の再計画をしない方法で、細かな変更でも敏感に対応しようとするMRP機能に制限を与えるしくみを指す。一般的に、納期を早めた変更に対しては、納期遅れまたは欠品を防ぐためにMRPでの再計画を行う。これに対し納期を遅らせた変更は、欠品などの心配はなく、能力面での余裕があれば、MRPで細かな再計画は行わない。
関連用語: ダンパー
あるオーダーからみて、そのオーダーがつくられる直接の源泉となった親品目のオーダーをいう。各オーダーには、自分のオーダー番号のほかに親オーダー番号が付与され、オーダー関連がとられている。また、所要量結合によりオーダー関連をとる方法もある。
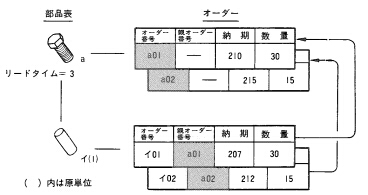
関連用語: 所要量結合
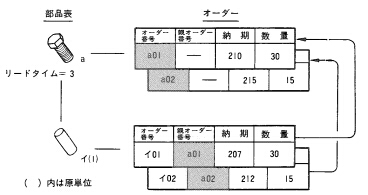
関連用語: 所要量結合
Order Status
オーダーの状況には、大きく分けて、予定、確定予定、確定および完了などがあり、それぞれ変更の影響度に応じて設定されている。
● 予定オーダー:生産計画を基にMRPは長期(数ヵ月)にわたって、組立品や部品、それに原材料の計画を行う。この時作成されたオーダーの状況はすべて"予定"である。予定ということは、計画変更が発生した時、無条件に変更しても全く影響がないことを意味する。
● 確定予定オーダー:MRPでつくられた予定オーダーのうち、短期(1ヵ月程度先まで)のオーダーは、製造オーダーであれば、製造工程管理の対象として工程ごとの能力計画が行われ、購買オーダーや外注オーダーであれば、購買管理の対象として業者や単価の設定が行われる。この時、オーダーの状況は、予定から計画済、すなわち"確定予定"となる。確定予定となったオーダーは、非常に信頼性の高いオーダーであり、変更があれば、業者や工程に対し影響が生じることを意味する。
● 確定オーダー:確定予定オーダーは、実際の発注もしくは作業指示により、発行済、すなわち"確定"オーダーとなる。この段階での変更は、業者や現場に大きな影響を及ぼすことになる。したがって、確定オーダーの変更は原則として認められず、また、仮りに許すとすれば、相当に大きなペナルティを支払うことを意味する。
● 完了オーダー:検収や製造実績収集によって終了したオーダーは、確定から"完了"に変えられる。この完了となったオーダーは、オーダーの役目を果たしたとして削除され、在庫に反映される。
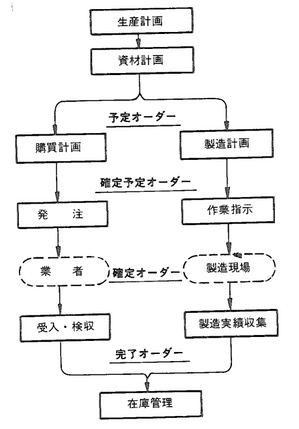
オーダーの状況には、大きく分けて、予定、確定予定、確定および完了などがあり、それぞれ変更の影響度に応じて設定されている。
● 予定オーダー:生産計画を基にMRPは長期(数ヵ月)にわたって、組立品や部品、それに原材料の計画を行う。この時作成されたオーダーの状況はすべて"予定"である。予定ということは、計画変更が発生した時、無条件に変更しても全く影響がないことを意味する。
● 確定予定オーダー:MRPでつくられた予定オーダーのうち、短期(1ヵ月程度先まで)のオーダーは、製造オーダーであれば、製造工程管理の対象として工程ごとの能力計画が行われ、購買オーダーや外注オーダーであれば、購買管理の対象として業者や単価の設定が行われる。この時、オーダーの状況は、予定から計画済、すなわち"確定予定"となる。確定予定となったオーダーは、非常に信頼性の高いオーダーであり、変更があれば、業者や工程に対し影響が生じることを意味する。
● 確定オーダー:確定予定オーダーは、実際の発注もしくは作業指示により、発行済、すなわち"確定"オーダーとなる。この段階での変更は、業者や現場に大きな影響を及ぼすことになる。したがって、確定オーダーの変更は原則として認められず、また、仮りに許すとすれば、相当に大きなペナルティを支払うことを意味する。
● 完了オーダー:検収や製造実績収集によって終了したオーダーは、確定から"完了"に変えられる。この完了となったオーダーは、オーダーの役目を果たしたとして削除され、在庫に反映される。
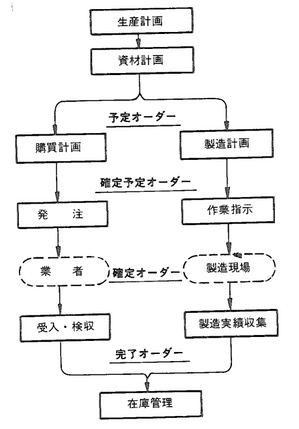
ある品目のオーダーと、その品目を構成する下位品目のオーダーとの関連をとることをいい、構成品からみれば、親品目や上位品目のオーダーとの関連を指す。オーダー関連をとるために、各オーダーには、(自分の)オーダー番号のほかに、親オーダー番号や上位オーダー番号が設定される。一般にオーダー関連をとるには、所要量結合を用いる。
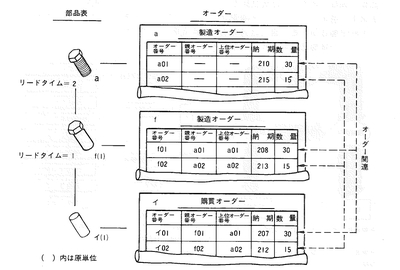
関連用語: 所要量結合
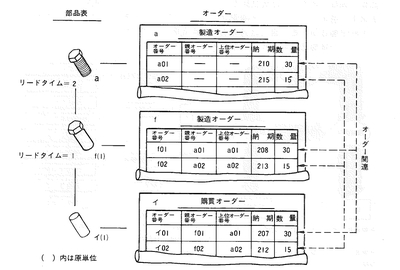
関連用語: 所要量結合
Order 手配
製品、組立品、部品など、それぞれの品目をつくったり、買ったりする場合、その品目、納期、業者または製造係などで固有に識別できるように設定した指示や手配を示す。通常、オーダーには識別コードとしてオーダー番号がつけられ、製造品目であれば製造指示書、購入品目であれば注文書として手配される。
オーダーの種類は、各品目の手配内容によって図1に示すように分けられる。
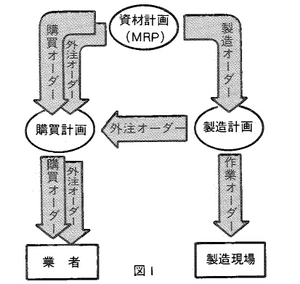
● 製造オーダー:製造品目に必要なオーダーで、自社内で製造する内作オーダーと外注業者で製造する外注オーダーとに分けられる。なお、内作オーダーは、製造工程単位に展開されて作業オーダーとなる。
● 購買オーダー:購入品目に必要なオーダーで、品目、納期、所要量のほかに業者に関する情報や単価、納入情報などを付して手配される。
● 外注オーダー:外注オーダーには、あらかじめ品目単位で外注として設定されているものと、製造計画後に能力などの関係で、外注として決まるものがある。普通、前者は品目外注といい、後者は工程外注という。いずれにしても、通常の手配情報のほかに業者情報が付加されて手配される。
● 作業オーダー:製造オーダーのうち内作オーダーを、必要な工程の単位に分けたオーダーである。
また、生産管理の各機能から捉えると、扱うオーダーは図2のように分けることができる。
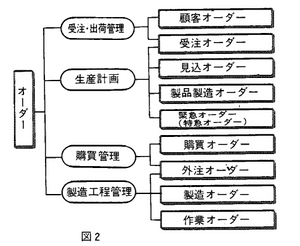
関連用語: オーダー状況
製品、組立品、部品など、それぞれの品目をつくったり、買ったりする場合、その品目、納期、業者または製造係などで固有に識別できるように設定した指示や手配を示す。通常、オーダーには識別コードとしてオーダー番号がつけられ、製造品目であれば製造指示書、購入品目であれば注文書として手配される。
オーダーの種類は、各品目の手配内容によって図1に示すように分けられる。
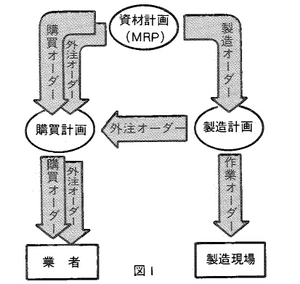
● 製造オーダー:製造品目に必要なオーダーで、自社内で製造する内作オーダーと外注業者で製造する外注オーダーとに分けられる。なお、内作オーダーは、製造工程単位に展開されて作業オーダーとなる。
● 購買オーダー:購入品目に必要なオーダーで、品目、納期、所要量のほかに業者に関する情報や単価、納入情報などを付して手配される。
● 外注オーダー:外注オーダーには、あらかじめ品目単位で外注として設定されているものと、製造計画後に能力などの関係で、外注として決まるものがある。普通、前者は品目外注といい、後者は工程外注という。いずれにしても、通常の手配情報のほかに業者情報が付加されて手配される。
● 作業オーダー:製造オーダーのうち内作オーダーを、必要な工程の単位に分けたオーダーである。
また、生産管理の各機能から捉えると、扱うオーダーは図2のように分けることができる。
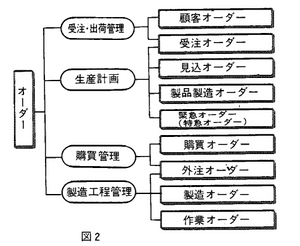
関連用語: オーダー状況
De-expedite デクスペダイト
MRPによる勧告の1つで、デクスペダイトともいわれる。これは、何らかの理由で、すでに手配済となっているオーダーの納期を遅らせる場合に用いられる。たとえば、図のような部品aの計画に対して、製品Zの期間3の受注数20個がキャンセルされたとすると、部品aの期間3の総所要量は15個になり、期間5の注残50個は、期間5になくてもよいことになる。つまり、期間4の使用可能在庫22個で、期間5の総所要量19個をまかなうことができるからである。このことから、期間5の注残50個の納期を期間6にした方がよりタイムリーとなる。このように、注残とか仕掛の納期を遅らせるような勧告を延期という。
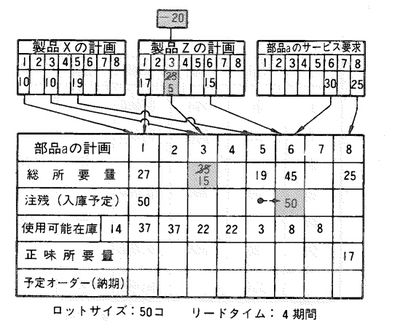
関連用語: 勧告
MRPによる勧告の1つで、デクスペダイトともいわれる。これは、何らかの理由で、すでに手配済となっているオーダーの納期を遅らせる場合に用いられる。たとえば、図のような部品aの計画に対して、製品Zの期間3の受注数20個がキャンセルされたとすると、部品aの期間3の総所要量は15個になり、期間5の注残50個は、期間5になくてもよいことになる。つまり、期間4の使用可能在庫22個で、期間5の総所要量19個をまかなうことができるからである。このことから、期間5の注残50個の納期を期間6にした方がよりタイムリーとなる。このように、注残とか仕掛の納期を遅らせるような勧告を延期という。
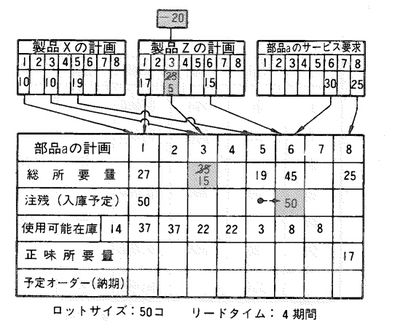
関連用語: 勧告
Single Pegging 単純所要量結合
単純所要量結合とかシングルペギングともいわれ、あるオーダーとその一段階上位のオーダーの関連をもつ方法をいう。この方法では、下位のオーダーから直接、製品のオーダーを知ることはできない。製品のオーダーを知るには、1段、1段、上位のオーダーを調べる必要がある。
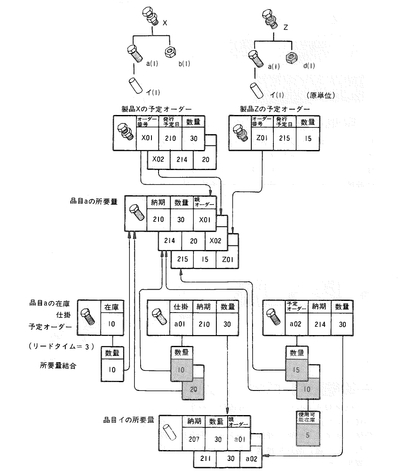
単純所要量結合とかシングルペギングともいわれ、あるオーダーとその一段階上位のオーダーの関連をもつ方法をいう。この方法では、下位のオーダーから直接、製品のオーダーを知ることはできない。製品のオーダーを知るには、1段、1段、上位のオーダーを調べる必要がある。
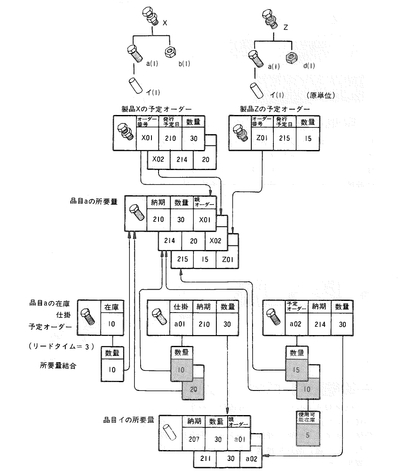
Activity Chain
活動チェーンなどとも呼ばれ、MRPをレベル・バイ・レベルに実行するために、各レベルごとの展開された品目のつながりを管理するためのものである。このチェーンは通常、品目に設定され、レベルテーブルが製品構成の深さを管理するのに対し、製品構成の横の広がりを管理する。
図は、レベルテーブルとアクティビティ・チェーンの関連を示している。ここでは、製品Aの下位品目e、f、gがすべてローレベルコード1で、品目ホだけがレベル2と仮定する。まず、部品eが展開される。レベルテーブルには、初期値として"*"が登録されている。この"*"を展開された品目eのアクティビティ・チェーンに登録し、レベルテーブルの1レベル目に品目eを登録する。次に品目fが展開される。やはりローレベルコードは1である。レベルテーブルに登録されている"e"を品目fのアクティビティ・チェーンに移し、品目fをレベルテーブルに登録する。このようにして、アクティビティ・チェーンの設定とレベルテーブルの登録を繰返すことにより展開は進められる。
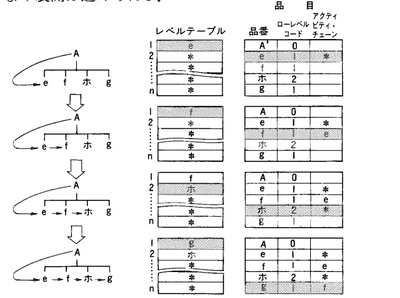
この展開で、レベル1の品目が連鎖(チェーニング)しているか否かを確認してみる。まず、レベルテーブルのレベル1には"g"が登録されている。次に品目gのアクティビティ・チェーンには部品fが登録されており、品目fには部品eが、品目eには連鎖の終了を示す"*"が設定されており、g→f→e→終了("*")とつながっていることになる。このことで、MRPに必要なレベル・バイ・レベルの所要量展開が可能になる。
関連用語: 所要量展開、レベルテーブル、ローレベルコード
活動チェーンなどとも呼ばれ、MRPをレベル・バイ・レベルに実行するために、各レベルごとの展開された品目のつながりを管理するためのものである。このチェーンは通常、品目に設定され、レベルテーブルが製品構成の深さを管理するのに対し、製品構成の横の広がりを管理する。
図は、レベルテーブルとアクティビティ・チェーンの関連を示している。ここでは、製品Aの下位品目e、f、gがすべてローレベルコード1で、品目ホだけがレベル2と仮定する。まず、部品eが展開される。レベルテーブルには、初期値として"*"が登録されている。この"*"を展開された品目eのアクティビティ・チェーンに登録し、レベルテーブルの1レベル目に品目eを登録する。次に品目fが展開される。やはりローレベルコードは1である。レベルテーブルに登録されている"e"を品目fのアクティビティ・チェーンに移し、品目fをレベルテーブルに登録する。このようにして、アクティビティ・チェーンの設定とレベルテーブルの登録を繰返すことにより展開は進められる。
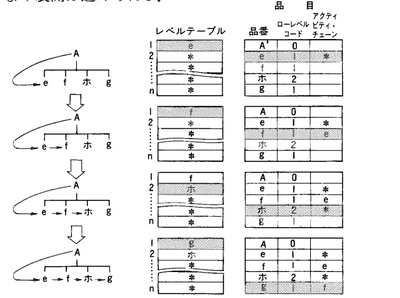
この展開で、レベル1の品目が連鎖(チェーニング)しているか否かを確認してみる。まず、レベルテーブルのレベル1には"g"が登録されている。次に品目gのアクティビティ・チェーンには部品fが登録されており、品目fには部品eが、品目eには連鎖の終了を示す"*"が設定されており、g→f→e→終了("*")とつながっていることになる。このことで、MRPに必要なレベル・バイ・レベルの所要量展開が可能になる。
関連用語: 所要量展開、レベルテーブル、ローレベルコード
MRPを実行する際に用いる計画表である。この表の横方向は"期間"を表わしており、各企業により期間の大きさ(通常、日数で表現される)は異なる。一方、縦方向には、MRPに必要な項目が処理の手順通り上から順に並んでいる。
●総所要量:上位の品目やサービス部品として要求された量を期間ごとにまとめたもの。
●注残(入庫予定):購入品であれば、注文済オーダーを示し、内作品であれば、製造指示済オーダーを示す。この数量が設定されている期間には、入庫される予定である。
●使用可能在庫:各期間ごとに使うことが可能である在庫数を示している。また、現在庫は期間1の左側に表示される。
●正味所要量:総所要量から、注残と使用可能在庫を差引いた後の必要量を示す。ここに示された数量は引当後のもので手配を必要とする。
●予定オーダー(納期):ロットまとめをして作成されたオーダーを示す。数量が設定されている期間が納期となる。
●予定オーダー(着手):納期で示されたオーダーのリードタイム計算をして、着手日を決め、その期間に数量を設定する。
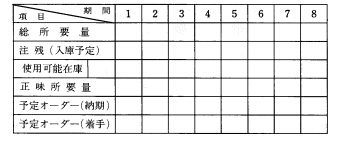
関連用語: MRP
●総所要量:上位の品目やサービス部品として要求された量を期間ごとにまとめたもの。
●注残(入庫予定):購入品であれば、注文済オーダーを示し、内作品であれば、製造指示済オーダーを示す。この数量が設定されている期間には、入庫される予定である。
●使用可能在庫:各期間ごとに使うことが可能である在庫数を示している。また、現在庫は期間1の左側に表示される。
●正味所要量:総所要量から、注残と使用可能在庫を差引いた後の必要量を示す。ここに示された数量は引当後のもので手配を必要とする。
●予定オーダー(納期):ロットまとめをして作成されたオーダーを示す。数量が設定されている期間が納期となる。
●予定オーダー(着手):納期で示されたオーダーのリードタイム計算をして、着手日を決め、その期間に数量を設定する。
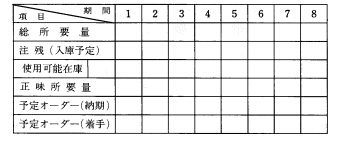
関連用語: MRP
Part Period Balancing
EOQと同様に発注費用と在庫維持費用との関係で費用が最小となるようにまとめる方法である。しかし、オーダーの数量やまとめる期間数も変動させてロットにまとめるため、EOQが需要の一定した品目に適するのに対し、需要が不安定な品目にも有効である。この方法では、PP(Part-Period)値という基本単位が用いられる。これは、1個の部品を1期間在庫した時1PPとなり、各期間で算出されたPP値を期間ごとに累積したものが累積PP値となる。
累積の在庫維持費用が発注費用をオーバーする時に、予定オーダーの数量が設定される。このような計算を容易にするためにEPP(Economic Part-Period)値というロットまとめの基準値が使われる。これは、累積PP値が発注費用を超える値であり、次の式によって求められる。
PPB法におけるロットのまとめ方は、図に示すように、累積PP値がEPP値を超えた1期間前までの期間でまとめる方法である。
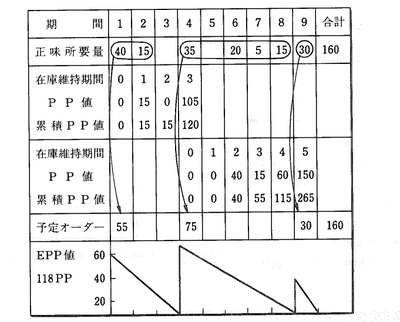
関連用語: ロットまとめ
EOQと同様に発注費用と在庫維持費用との関係で費用が最小となるようにまとめる方法である。しかし、オーダーの数量やまとめる期間数も変動させてロットにまとめるため、EOQが需要の一定した品目に適するのに対し、需要が不安定な品目にも有効である。この方法では、PP(Part-Period)値という基本単位が用いられる。これは、1個の部品を1期間在庫した時1PPとなり、各期間で算出されたPP値を期間ごとに累積したものが累積PP値となる。
累積の在庫維持費用が発注費用をオーバーする時に、予定オーダーの数量が設定される。このような計算を容易にするためにEPP(Economic Part-Period)値というロットまとめの基準値が使われる。これは、累積PP値が発注費用を超える値であり、次の式によって求められる。

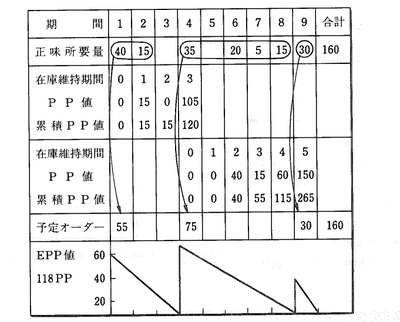
関連用語: ロットまとめ
Material Requirements Planning 資材所要量計画
Material Requirements Planningの略で、一般に資材所要量計画といわれる。MRPは、1970年「アメリカ生産・在庫管理協会」、略称APICS(American Production and Inventory Control Society)の提唱により、急速にその活用が広まった資材計画の1手法である。この方法では、図に示すように、立案された製品レベルの生産計画を基に、組立品、部品、原材料などの従属需要品目について"必要なものを(品目)、必要なときに(納期)、必要なだけ(所要量)"購買したり、製造したりするための手配計画を行う。このように、従属需要品目の手配計画を作成するために、MRPは大きく3つの情報を必要とする。
● 生産計画:製品やサービスパーツなど独立需要品目の生産計画で、基準生産計画とかMaster Production Schedule を略してMPSとか呼ばれる。MRPはこの計画を基に従属需要品目の計画を行う。
● 部品表:独立需要品目から従属需要品目へ、従属需要品目の中でも組立品から原 P.45 材料へと使用品目の洗い出し(展開)が必要となる。このために部品表は用いられる。なお、部品表には、原単位、リードタイム、ロットサイズなど資材計画に必要な基礎情報が設定されていなければならない。
● 在庫・注残:算出された各従属需要品目の所要量を基に正味所要量を算出するために現在庫、注残、仕掛などの在庫・注残情報を必要とする。
このような情報を基に、MRPは次の5つの機能を実行して、従属需要品目の手配計画を行う。
● 総所要量計算:各々の従属需要品目の要求されている量を、ある期間単位にまとめて、期間別の総所要量を算出する。
● 正味所要量計算:算出された総所要量を基に在庫や注残への引当を行い、期間別に必要な正味所要量を算出する。
● ロットまとめ:算出された期間別の正味所要量を基に、品目に設定されているロットサイズを用いて、手配に最も適した数量にまとめる。
● リードタイム計算:ロットまとめされた数量の納期からリードタイムを差引き、その発注日または着手日を算出し、オーダーを作成する。
● 所要量展開:部品表を用いて作成したオーダーの下位品目へと展開し、製品構成に設定されている原単位を参照して、展開された品目の所要量を算出する。
この5つの機能を上位品目から順に、レベル・バイ・レベルですべての従属需要品目について行い、最下位の品目の処理が終了した段階でMRPは終了する。
Material Requirements Planningの略で、一般に資材所要量計画といわれる。MRPは、1970年「アメリカ生産・在庫管理協会」、略称APICS(American Production and Inventory Control Society)の提唱により、急速にその活用が広まった資材計画の1手法である。この方法では、図に示すように、立案された製品レベルの生産計画を基に、組立品、部品、原材料などの従属需要品目について"必要なものを(品目)、必要なときに(納期)、必要なだけ(所要量)"購買したり、製造したりするための手配計画を行う。このように、従属需要品目の手配計画を作成するために、MRPは大きく3つの情報を必要とする。

● 部品表:独立需要品目から従属需要品目へ、従属需要品目の中でも組立品から原 P.45 材料へと使用品目の洗い出し(展開)が必要となる。このために部品表は用いられる。なお、部品表には、原単位、リードタイム、ロットサイズなど資材計画に必要な基礎情報が設定されていなければならない。
● 在庫・注残:算出された各従属需要品目の所要量を基に正味所要量を算出するために現在庫、注残、仕掛などの在庫・注残情報を必要とする。
このような情報を基に、MRPは次の5つの機能を実行して、従属需要品目の手配計画を行う。
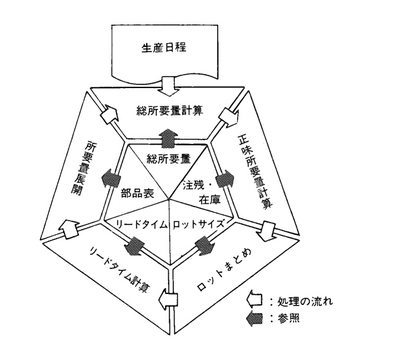
● 正味所要量計算:算出された総所要量を基に在庫や注残への引当を行い、期間別に必要な正味所要量を算出する。
● ロットまとめ:算出された期間別の正味所要量を基に、品目に設定されているロットサイズを用いて、手配に最も適した数量にまとめる。
● リードタイム計算:ロットまとめされた数量の納期からリードタイムを差引き、その発注日または着手日を算出し、オーダーを作成する。
● 所要量展開:部品表を用いて作成したオーダーの下位品目へと展開し、製品構成に設定されている原単位を参照して、展開された品目の所要量を算出する。
この5つの機能を上位品目から順に、レベル・バイ・レベルですべての従属需要品目について行い、最下位の品目の処理が終了した段階でMRPは終了する。
Lot for Lot ロット・フォー・ロット
Lot for Lotの略で、各期間に発生した正味所要量をそのままオーダー数量とするロットまとめの1手法である。これは主に、高価な品目や断続的に要求される品目に使われる。詳細はロット・フォー・ロットを参照。
関連用語: ロットまとめ
Lot for Lotの略で、各期間に発生した正味所要量をそのままオーダー数量とするロットまとめの1手法である。これは主に、高価な品目や断続的に要求される品目に使われる。詳細はロット・フォー・ロットを参照。
関連用語: ロットまとめ
普通"れいにゅう"とか"もどしいれ"などといわれ、いったん倉庫から出庫された在庫品が、良品にもかかわらず次のような理由で返庫されることを指す。
関連用語: 計画外入出庫
●誤って出庫数を多く払出した場合。このような場合、戻入は計画外入庫として処理される。
●実際の不良率より見積りの不良率の方が高い場合。
●数量カットや中断などのオーダー変更が発生した場合。
●出庫後に緊急の計画変更が発生した場合。
関連用語: 計画外入出庫
一般に倉庫以外で管理している在庫を示す。たとえば、倉庫から払出された在庫品が仕掛品として作業場に置いてある場合とか、倉庫では管理せずに製造現場での管理対象品目として床などに置いてある在庫を指す。これに対し、倉庫で管理されている在庫を倉庫在庫と称す。
関連用語: 在庫
関連用語: 在庫
自動入出庫
入出庫は、伝票を使うやり方と使わないやり方に分けられる。一般に前者は実入出庫といい、後者はみなし入出庫とか自動入出庫と呼ばれている。みなし入出庫は、入出庫伝票を使わないが、あたかも使ったとみなして処理する方法で、伝票を使うやり方の簡便法である。部品や材料を払出してから上位品目や製品ができるまでのリードタイムが比較的短い場合に適用可能となる。
この方法は、みなし入庫とみなし出庫に分けられる。みなし入庫は、実績報告により入庫したとみなすやり方である。たとえば、購買品であれば、納入され検収されたならば、検収イコール入庫とみなして在庫に加算する。また、内作品であれば、製造報告表での完成数量を入庫とみなす。
みなし出庫の場合も同じである。上位品目の完成数量を基に、下位品目が、それに必要な量だけ出庫され、使われたとみなして在庫から引き落とす。たとえば、図の製造報告表の製品Zの完成数量10個を基に、品目Zは10個が入庫されたとみなし、品目aとbは部品表を使って所要量10個と20個が各々算出され、あたかもその数量が出庫されたとみなして処理する。
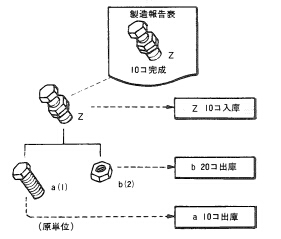
反意語: 実入出庫
入出庫は、伝票を使うやり方と使わないやり方に分けられる。一般に前者は実入出庫といい、後者はみなし入出庫とか自動入出庫と呼ばれている。みなし入出庫は、入出庫伝票を使わないが、あたかも使ったとみなして処理する方法で、伝票を使うやり方の簡便法である。部品や材料を払出してから上位品目や製品ができるまでのリードタイムが比較的短い場合に適用可能となる。
この方法は、みなし入庫とみなし出庫に分けられる。みなし入庫は、実績報告により入庫したとみなすやり方である。たとえば、購買品であれば、納入され検収されたならば、検収イコール入庫とみなして在庫に加算する。また、内作品であれば、製造報告表での完成数量を入庫とみなす。
みなし出庫の場合も同じである。上位品目の完成数量を基に、下位品目が、それに必要な量だけ出庫され、使われたとみなして在庫から引き落とす。たとえば、図の製造報告表の製品Zの完成数量10個を基に、品目Zは10個が入庫されたとみなし、品目aとbは部品表を使って所要量10個と20個が各々算出され、あたかもその数量が出庫されたとみなして処理する。
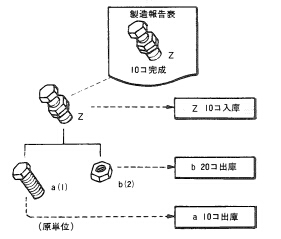
反意語: 実入出庫
在庫品は、倉庫にのみ存在するとは限らない。まして共通品であれば、いくつかの工程で使われるため、各工程に払出されて、床在庫となっていることもある。保有在庫とは、ある品目が倉庫や工程に限らず、工場全体として保有している在庫をいう。
図に示すように保有在庫は、現在庫と仕掛在庫とに大きく分けられる。これは、倉庫への入庫により、現在庫の未引当在庫に加算され、当該品目の出庫計画により、引当済在庫へ移動する。そして実際に出庫されると、在庫は倉庫で管理されていた引当済在庫から仕掛在庫へ移され、現場管理の対象になる。
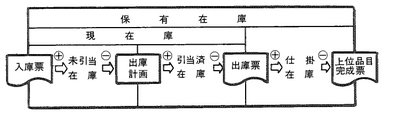
関連用語: 在庫
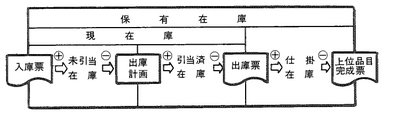
関連用語: 在庫
Receive/Issue 実入出庫
購買品や外注品における在庫品は、調達されると入庫され、生産活動で必要となった時に出庫される。また、内作品の中での在庫品は、作業が完了すると入庫される。このように入出庫とは、倉庫へのものの出し入れを示し、大きく2つの観点で捉えることができる。1つは、計画面での捉え方で、計画通りに行う入出庫と予定していなかった入出庫とに分けられる。前者は計画入出庫と呼び、後者は計画外入出庫という。また、伝票を使うか否かで2つに分けることもできる。伝票を使う入出庫を実入出庫といい、伝票を使わないがあたかも使ったごとくみなして処理をするみなし入出庫とがある。
反意語: みなし入出庫
購買品や外注品における在庫品は、調達されると入庫され、生産活動で必要となった時に出庫される。また、内作品の中での在庫品は、作業が完了すると入庫される。このように入出庫とは、倉庫へのものの出し入れを示し、大きく2つの観点で捉えることができる。1つは、計画面での捉え方で、計画通りに行う入出庫と予定していなかった入出庫とに分けられる。前者は計画入出庫と呼び、後者は計画外入出庫という。また、伝票を使うか否かで2つに分けることもできる。伝票を使う入出庫を実入出庫といい、伝票を使わないがあたかも使ったごとくみなして処理をするみなし入出庫とがある。
反意語: みなし入出庫
Fixed Size Ordering System 発注点手法
統計的在庫管理手法の代表的なもので、在庫が発注点に達した時に発注することから、一般には発注点手法などとも呼ばれている。
定量発注法は需要に対し、次のような特徴をもっている。
●個々の品目の需要に関連性はなく、各々独立して管理される。
●需要は継続的で、季節変動の少ないもの。
●比較的頻繁に出庫される。
●消費の割合はほぼ一定で、その需要は平均値付近で変動している。
●在庫はやや多くなる。
このようなことからこの発注法は、需要が安定していて、比較的安価な品目、すなわち、B品目とかC品目でかつ独立需要品目の在庫管理に向いている。
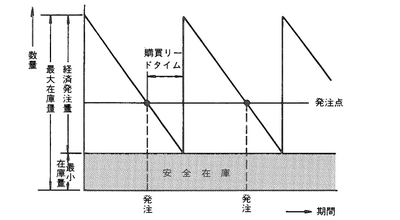
定量発注法のしくみは、基準在庫量の最大と最小とを定、在庫が徐々に減少して、発注点(ROP:Reorder Pointまたは略してOPなどという)に到達した時に、経済発注量(EOQ:Economic Order Quantity)で注文する。
発注点の設定方法は、次の手順で行う。
①各品目の消費実績を決める。
②経済発注量(EOQ)を決める。
③品目別に購買業者を決め、購買リードタイムを決める。
④需要の変動、納期のバラツキ、品切損失などを考慮して安全在庫を決める。
⑤安全在庫量に購買リードタイム内での消費量を加えて発注点を決める。
関連用語: 在庫管理手法
統計的在庫管理手法の代表的なもので、在庫が発注点に達した時に発注することから、一般には発注点手法などとも呼ばれている。
定量発注法は需要に対し、次のような特徴をもっている。
●個々の品目の需要に関連性はなく、各々独立して管理される。
●需要は継続的で、季節変動の少ないもの。
●比較的頻繁に出庫される。
●消費の割合はほぼ一定で、その需要は平均値付近で変動している。
●在庫はやや多くなる。
このようなことからこの発注法は、需要が安定していて、比較的安価な品目、すなわち、B品目とかC品目でかつ独立需要品目の在庫管理に向いている。
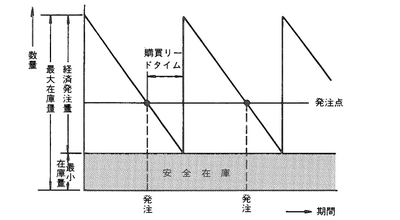
定量発注法のしくみは、基準在庫量の最大と最小とを定、在庫が徐々に減少して、発注点(ROP:Reorder Pointまたは略してOPなどという)に到達した時に、経済発注量(EOQ:Economic Order Quantity)で注文する。
発注点の設定方法は、次の手順で行う。
①各品目の消費実績を決める。
②経済発注量(EOQ)を決める。
③品目別に購買業者を決め、購買リードタイムを決める。
④需要の変動、納期のバラツキ、品切損失などを考慮して安全在庫を決める。
⑤安全在庫量に購買リードタイム内での消費量を加えて発注点を決める。
関連用語: 在庫管理手法
Fixed Period Ordering System
在庫管理手法の1つで、定期的に発注をするが、その発注量は毎回異なるやり方で、定期不足量発注法などとも呼ばれる。
定期発注法には、次のような特徴がある。
●定期的に発注する。
●発注量はそのつど異なる。
●需要変動が割合に大きくても対応可能。
●季節変動にも比較的対応できる。
●発注点手法に比べて在庫量が減る。
●主にA品目に向いている。
●リードタイムが長くてもよい。
●事務の手数がかかる。
また、この方式での毎回の注文量は、右の式によって求められる。
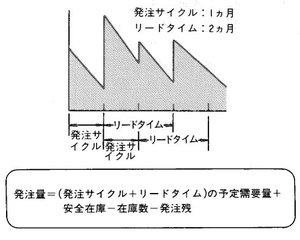
関連用語: 在庫管理手法
在庫管理手法の1つで、定期的に発注をするが、その発注量は毎回異なるやり方で、定期不足量発注法などとも呼ばれる。
定期発注法には、次のような特徴がある。
●定期的に発注する。
●発注量はそのつど異なる。
●需要変動が割合に大きくても対応可能。
●季節変動にも比較的対応できる。
●発注点手法に比べて在庫量が減る。
●主にA品目に向いている。
●リードタイムが長くてもよい。
●事務の手数がかかる。
また、この方式での毎回の注文量は、右の式によって求められる。
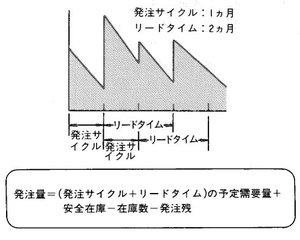
関連用語: 在庫管理手法
期末のみとか6ヵ月に1回といった一定の期限を定めて行う棚卸を指す。この場合、対象とする品目は、倉庫および工程を含めた一斉棚卸を指す場合が多い。これに対し、全品目一律に棚卸をせずに、各品目の重要度別に循環して在庫数を調査する方法を循環棚卸という。
関連用語: 棚卸
関連用語: 棚卸
棚卸資産の期末評価をする場合、時価もしくは取得原価のいずれか低い方で評価する方法である。棚卸資産の評価方法には、先入先出法や後入先出法などの原価主義系列に属するものと、低価法のように低価主義系列に属するものとがある。また、低価法には、評価切下げを行った後の価額を次期期首棚卸品の取得原価とみなす“切放し低価法”と、取得原価と期末時価を比較する“洗替え低価法”がある。
棚卸資産評価および出庫金額算定の手法の1つで、異なる単価の在庫品を受入れても、その単価の和を単純に受入回数で乗して平均単価を計算する方法である。右に単純平均法の例を示す。この例では1日から24日までに受入れた単価の合計が900円で受入回数が4回であり、平均受入単価は225円である。この平均単価に残高40個を掛けると棚卸資産9,000円となる。
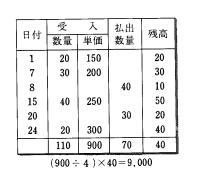
関連用語: 平均原価法
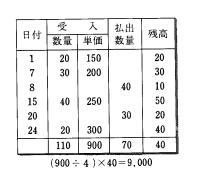
関連用語: 平均原価法
Stocktaking
棚卸は、"たなおろし"と称し、在庫品の入出庫と保管状況を調べ、その数量や品質をチェックして、資産内容を明らかにすると同時に、その管理状態の適否を判定し、より適正化するために行われる。ある時期にすべての品目の棚卸を1度に行う場合、これを定期棚卸とか一斉棚卸などという。これに対し、毎日とか1週間とかの期間を決めて順次棚卸をしていく方法を循環棚卸と呼ぶ。また、実際に倉庫にある在庫品の数量を調べて行う場合、これを現品棚卸とか実地棚卸とかいい、棚札や在庫記録により在庫品の数量を算定する方法を帳簿棚卸と呼ぶ。このような倉庫棚卸に対し、倉庫から払出され、工程に仕掛となっている在庫の棚卸を仕掛棚卸という。仕掛在庫は動きが活発なため、循環棚卸ではその動きを的確に捉えることが難しい。このため一般に、一斉棚卸が採用される。
普通、棚卸というと、たいていは期に1度か2度行う定期棚卸の場合が多い。それも、工場の全品目を対象とした一斉棚卸である。ABC分析によりランク付けされたC品目は、期に1~2回の棚卸でよいとしても、A品目はもっと頻繁にチェックをして管理すべきである。このことから最近"サイクルカウンティング(Cycle Counting)"と呼ばれる循環棚卸のやり方が注目を集めている。これはA品目は重点管理をし、C品目は手抜管理をすることを意味している。
棚卸は、"たなおろし"と称し、在庫品の入出庫と保管状況を調べ、その数量や品質をチェックして、資産内容を明らかにすると同時に、その管理状態の適否を判定し、より適正化するために行われる。ある時期にすべての品目の棚卸を1度に行う場合、これを定期棚卸とか一斉棚卸などという。これに対し、毎日とか1週間とかの期間を決めて順次棚卸をしていく方法を循環棚卸と呼ぶ。また、実際に倉庫にある在庫品の数量を調べて行う場合、これを現品棚卸とか実地棚卸とかいい、棚札や在庫記録により在庫品の数量を算定する方法を帳簿棚卸と呼ぶ。このような倉庫棚卸に対し、倉庫から払出され、工程に仕掛となっている在庫の棚卸を仕掛棚卸という。仕掛在庫は動きが活発なため、循環棚卸ではその動きを的確に捉えることが難しい。このため一般に、一斉棚卸が採用される。
普通、棚卸というと、たいていは期に1度か2度行う定期棚卸の場合が多い。それも、工場の全品目を対象とした一斉棚卸である。ABC分析によりランク付けされたC品目は、期に1~2回の棚卸でよいとしても、A品目はもっと頻繁にチェックをして管理すべきである。このことから最近"サイクルカウンティング(Cycle Counting)"と呼ばれる循環棚卸のやり方が注目を集めている。これはA品目は重点管理をし、C品目は手抜管理をすることを意味している。
Sleeping Stock スリーピングストック
休眠部品とかスリーピングストックまたは眠り在庫などともいわれ、倉庫などに在庫されているが、長期間使われていない品物を指す。これは生産や出荷のチャンスを逃したもので、季節変動や循環変動のある品目に多く見られる。しかし生産部品として、またサービス部品として機能的にも十分使えることができる品物をいう。これに対し、設計変更で生産が中止になり、2度と使うことのなくなった品物や腐食などで機能しなくなった品物を死蔵品とかデッドストックと呼ぶ。
関連用語: 死蔵品
休眠部品とかスリーピングストックまたは眠り在庫などともいわれ、倉庫などに在庫されているが、長期間使われていない品物を指す。これは生産や出荷のチャンスを逃したもので、季節変動や循環変動のある品目に多く見られる。しかし生産部品として、またサービス部品として機能的にも十分使えることができる品物をいう。これに対し、設計変更で生産が中止になり、2度と使うことのなくなった品物や腐食などで機能しなくなった品物を死蔵品とかデッドストックと呼ぶ。
関連用語: 死蔵品
Policy Inventory Item
製品をつくるうえで次のような理由により、企業として積極的かつ政策的に見込で手配し、在庫する品目を指す。
● 納入リードタイムを短くするために設定した在庫:これは、組立品や半組立品などがその主なものとなり、中間仕込品とか緩衝部品などと呼ばれている。
● 投機買い、政策買いの在庫:これは、原材料レベルの品目に多く見られる。価格変動の激しいものや、また本来リードタイムは非常に長いが年間契約をして、より短くかつ少しでも安く調達しようとする場合。
● サービスのための在庫:アフターパーツとか補用品とか呼ばれるもので、納品された製品の修理などに使われる品目。これは要求に対し、比較的迅速に対応するために在庫されている。
● 部品の共通化を図る在庫:これは普通、いろいろな製品に使われることから、共通品とか標準品などと呼ばれている。工場での品目の管理点数を減らしたり、また、ある程度まとまった量で生産できるため、生産の能率も向上する。
● 季節変動や生産ピークを緩和するための在庫:工場の能力は1年を通じて、それほど大きく変動しない。しかし、需要は大きく変動することがある。生産の過負荷を平準化するため、あらかじめ先行して生産を行う場合に、在庫が発生する。
このような政策在庫品に対し、生産上の都合でたまる在庫を一般在庫品とか消極的在庫品などと呼ぶ。
関連用語: 在庫品
製品をつくるうえで次のような理由により、企業として積極的かつ政策的に見込で手配し、在庫する品目を指す。
● 納入リードタイムを短くするために設定した在庫:これは、組立品や半組立品などがその主なものとなり、中間仕込品とか緩衝部品などと呼ばれている。
● 投機買い、政策買いの在庫:これは、原材料レベルの品目に多く見られる。価格変動の激しいものや、また本来リードタイムは非常に長いが年間契約をして、より短くかつ少しでも安く調達しようとする場合。
● サービスのための在庫:アフターパーツとか補用品とか呼ばれるもので、納品された製品の修理などに使われる品目。これは要求に対し、比較的迅速に対応するために在庫されている。
● 部品の共通化を図る在庫:これは普通、いろいろな製品に使われることから、共通品とか標準品などと呼ばれている。工場での品目の管理点数を減らしたり、また、ある程度まとまった量で生産できるため、生産の能率も向上する。
● 季節変動や生産ピークを緩和するための在庫:工場の能力は1年を通じて、それほど大きく変動しない。しかし、需要は大きく変動することがある。生産の過負荷を平準化するため、あらかじめ先行して生産を行う場合に、在庫が発生する。
このような政策在庫品に対し、生産上の都合でたまる在庫を一般在庫品とか消極的在庫品などと呼ぶ。
関連用語: 在庫品
Cycle Counting サイクルカウンティング
一般に行われている棚卸は、期末だけとか、6ヵ月に1~2度行う期末棚卸や定期棚卸で、かつ全品目を1度に行うことから一斉棚卸などとも呼ばれている。循環棚卸は、サイクルカウンティングとも呼ばれ、ある決められた点数の品目を毎日とか3日に1回とかのサイクルを決めて、順次棚卸をしていくやり方である。
この棚卸では、各棚や各区画を決めて、順番に棚卸を行う方法もあるが、一般的には、ABC分析を使った重点管理の方法がとられる。ABC分析による循環棚卸では、図のように在庫品をA、B、Cにクラス分けしてA品目は在庫投資が最小になるよう重点管理をする。このために、たとえば毎月棚卸を実行し、一方C品目は欠品を起こさない程度の手抜管理でよいため、期末棚卸だけに限るなどのやり方である。このように重要品目の在庫精度を高めることは、MRPの計画精度を高めるうえでも必要なことである。
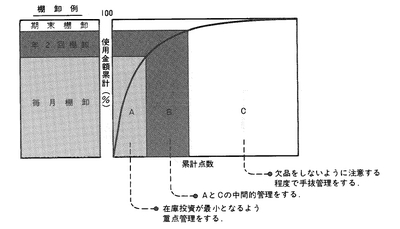
関連用語: 棚卸
一般に行われている棚卸は、期末だけとか、6ヵ月に1~2度行う期末棚卸や定期棚卸で、かつ全品目を1度に行うことから一斉棚卸などとも呼ばれている。循環棚卸は、サイクルカウンティングとも呼ばれ、ある決められた点数の品目を毎日とか3日に1回とかのサイクルを決めて、順次棚卸をしていくやり方である。
この棚卸では、各棚や各区画を決めて、順番に棚卸を行う方法もあるが、一般的には、ABC分析を使った重点管理の方法がとられる。ABC分析による循環棚卸では、図のように在庫品をA、B、Cにクラス分けしてA品目は在庫投資が最小になるよう重点管理をする。このために、たとえば毎月棚卸を実行し、一方C品目は欠品を起こさない程度の手抜管理でよいため、期末棚卸だけに限るなどのやり方である。このように重要品目の在庫精度を高めることは、MRPの計画精度を高めるうえでも必要なことである。
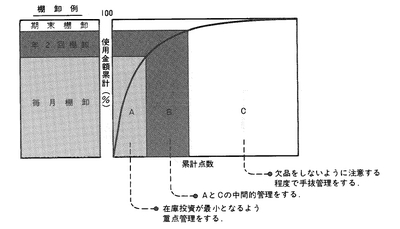
関連用語: 棚卸
Issue
通常、在庫品は生産活動でそのものが必要になった時に、倉庫から出される。出庫とは、ものを倉庫から出す行為を示す。出庫には、出庫伝票を使う方法と、伝票を使わない方法がある。前者は実出庫とか単に出庫といい、後者はみなし出庫とか自動出庫などと呼ぶ。
次に、出庫票の例を示す。
関連用語: 実入出庫
反意語: みなし出庫
みなし入出庫
入出庫は、伝票を使うやり方と使わないやり方に大きく分けることができる。一般に前者は実入出庫といい、後者はみなし入出庫と呼ぶ。自動入出庫とは、このみなし入出庫のことを指し、伝票を使わずに、上位品目の完成をもって自動的に下位品目が出庫され、上位品目が入庫したとする方法である。
入出庫は、伝票を使うやり方と使わないやり方に大きく分けることができる。一般に前者は実入出庫といい、後者はみなし入出庫と呼ぶ。自動入出庫とは、このみなし入出庫のことを指し、伝票を使わずに、上位品目の完成をもって自動的に下位品目が出庫され、上位品目が入庫したとする方法である。
Receive/Issue 入出庫
在庫管理を行ううえで入出庫処理は欠かすことができない。この入出庫のやり方として、実際に入出庫伝票を用いて品物の倉入、倉出を行う方法と、検収または作業完了の伝票でもって、あたかも入出庫が発生したとみなす方法がある。実入出庫とは、この前者の方法で、実際の伝票によりものの出し入れを行うことである。
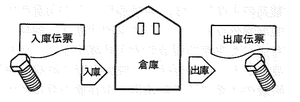
在庫管理を行ううえで入出庫処理は欠かすことができない。この入出庫のやり方として、実際に入出庫伝票を用いて品物の倉入、倉出を行う方法と、検収または作業完了の伝票でもって、あたかも入出庫が発生したとみなす方法がある。実入出庫とは、この前者の方法で、実際の伝票によりものの出し入れを行うことである。
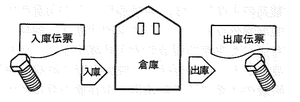
Physical Inventory Counts 現品棚卸
現品棚卸とか実棚などとも呼ばれ、実際に倉庫内に存在する在庫数を調査し、これに単価を乗じて、在庫高を算出する方法である。これに対して、帳簿上での棚卸を帳簿棚卸という。一般に実地棚卸は、図に示すような現品札を用いて行われ、半分が切り取られて棚卸処理に使われ、もう半分は現品に残して、棚卸済の目印とする。実地棚卸には倉庫の在庫品を扱う倉庫棚卸と工程や外注先へ払い出されているものを対象とした仕掛棚卸がある。実地棚卸を行う場合、物の動きを止めることが必要になることが多く、特に仕掛棚卸も含め実地棚卸を行う時は生産ライン、さらに工場全体を止めることもある。
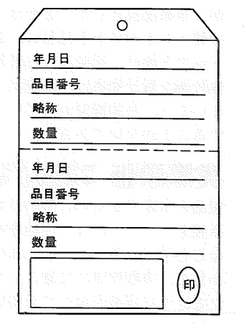
関連用語: 棚卸
現品棚卸とか実棚などとも呼ばれ、実際に倉庫内に存在する在庫数を調査し、これに単価を乗じて、在庫高を算出する方法である。これに対して、帳簿上での棚卸を帳簿棚卸という。一般に実地棚卸は、図に示すような現品札を用いて行われ、半分が切り取られて棚卸処理に使われ、もう半分は現品に残して、棚卸済の目印とする。実地棚卸には倉庫の在庫品を扱う倉庫棚卸と工程や外注先へ払い出されているものを対象とした仕掛棚卸がある。実地棚卸を行う場合、物の動きを止めることが必要になることが多く、特に仕掛棚卸も含め実地棚卸を行う時は生産ライン、さらに工場全体を止めることもある。
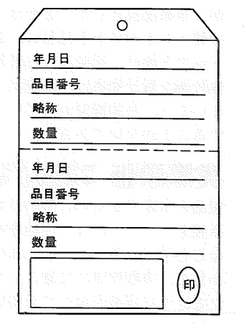
関連用語: 棚卸
Dead Stock デッドストック
倉庫などに在庫されているが、設計変更の発生や製品の生産中止などにより、2度と使われることがなくなった品目とか、保管状況が悪く腐食などで、本来の機能が発揮できなくなった品物を指す。これは、一般にデッドストックなどともいわれ、品物が再び使われることがないことを示している。これに対し、長期間使われないが、生産部品として、またはサービス部品として使う可能性もあり、機能的にも十分使うことができる品目は、滞留品、休眠部品とか眠り在庫およびスリーピングストックと呼び、死蔵品とは区別される。
無計画な設計変更は、死蔵品をどんどん増やすことになる。このため、死蔵化させないよう、長期間使われていない在庫品をいちはやく見つけ、これを積極的に活用することが大切である。
関連用語: 滞留品
倉庫などに在庫されているが、設計変更の発生や製品の生産中止などにより、2度と使われることがなくなった品目とか、保管状況が悪く腐食などで、本来の機能が発揮できなくなった品物を指す。これは、一般にデッドストックなどともいわれ、品物が再び使われることがないことを示している。これに対し、長期間使われないが、生産部品として、またはサービス部品として使う可能性もあり、機能的にも十分使うことができる品目は、滞留品、休眠部品とか眠り在庫およびスリーピングストックと呼び、死蔵品とは区別される。
無計画な設計変更は、死蔵品をどんどん増やすことになる。このため、死蔵化させないよう、長期間使われていない在庫品をいちはやく見つけ、これを積極的に活用することが大切である。
関連用語: 滞留品
In Process Stocktaking
工程や外注先へ払い出されている在庫品や非在庫品の数量を調査し、その仕掛在庫高を算出することである。これに対し、倉庫での在庫品の棚卸を倉庫棚卸という。
関連用語: 棚卸
工程や外注先へ払い出されている在庫品や非在庫品の数量を調査し、その仕掛在庫高を算出することである。これに対し、倉庫での在庫品の棚卸を倉庫棚卸という。
関連用語: 棚卸
In Process Inventory
保有在庫の内数で実際に倉庫から払い出され、上位品目を製造するために工程で在庫すること、またはその在庫数を示す。一般には外注業者も外注工程として捉え、支給品を仕掛在庫として把握する。
関連用語: 保有在庫
保有在庫の内数で実際に倉庫から払い出され、上位品目を製造するために工程で在庫すること、またはその在庫数を示す。一般には外注業者も外注工程として捉え、支給品を仕掛在庫として把握する。
仕掛在庫=保有在庫-現在庫
関連用語: 保有在庫
First-in First-out FIFO
棚卸資産評価および出庫単価算定方法の1つで、先に入庫したものから順に出庫されるものとして計算する方法である。これは、列車がトンネルを通過するようなもので、トンネルが倉庫で、列車を在庫品に例えることができる。つまり、先に入った列車(在庫品)は先にトンネル(倉庫)を出ることになる。この方法での利点は、棚卸資産の評価が常に新しい原価で算出されることにある。 次に、先入先出法の例を示す。
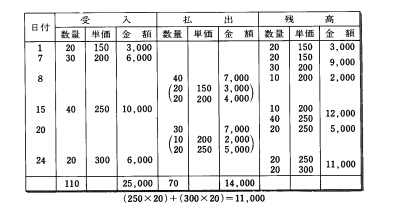
関連用語: 原価法
棚卸資産評価および出庫単価算定方法の1つで、先に入庫したものから順に出庫されるものとして計算する方法である。これは、列車がトンネルを通過するようなもので、トンネルが倉庫で、列車を在庫品に例えることができる。つまり、先に入った列車(在庫品)は先にトンネル(倉庫)を出ることになる。この方法での利点は、棚卸資産の評価が常に新しい原価で算出されることにある。 次に、先入先出法の例を示す。
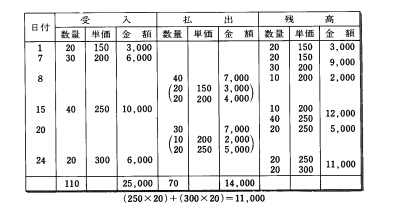
関連用語: 原価法
Inventory Goods
生産を営むうえで工場は数多くの品目を扱う。これらの品目を在庫の観点から捉えると、倉庫を経由する品目と、工程から工程へ直接送られる品目とがある。一般に前者を在庫品といい、後者を非在庫品と呼ぶ。仮に倉庫に保管されてなく、工程のわきなどに置いてあっても、そのものを計画に引当るよう管理していれば、これも在庫品として扱う。また、在庫品は、大きく2つのパターンに分けられる。1つは経営の意志が込められ、政策上積極的("在庫を多くもつ"という意味ではない)に在庫するものと、製造内部の事情で、なんとはなしに在庫されてしまうものとがある。前者は政策在庫品といい、後者は一般在庫品という。
政策在庫品と一般在庫品の主な特徴を次に示す。
■政策在庫品
生産を営むうえで工場は数多くの品目を扱う。これらの品目を在庫の観点から捉えると、倉庫を経由する品目と、工程から工程へ直接送られる品目とがある。一般に前者を在庫品といい、後者を非在庫品と呼ぶ。仮に倉庫に保管されてなく、工程のわきなどに置いてあっても、そのものを計画に引当るよう管理していれば、これも在庫品として扱う。また、在庫品は、大きく2つのパターンに分けられる。1つは経営の意志が込められ、政策上積極的("在庫を多くもつ"という意味ではない)に在庫するものと、製造内部の事情で、なんとはなしに在庫されてしまうものとがある。前者は政策在庫品といい、後者は一般在庫品という。
政策在庫品と一般在庫品の主な特徴を次に示す。
■政策在庫品
●顧客への納入リードタイムを短くするために設定した在庫。■一般在庫品
●投機買い、政策買いの在庫。
●サービスのための在庫。
●部品の共通化を図る在庫。
●季節変動や生産ピークを緩和するための在庫。
●工程能力のアンバランスによる在庫。
●段取替えをいやがる在庫。
●引当が忘れられている在庫。
●月いち(デカンショ)生産による在庫。
●古い基準値(ロットサイズ、リードタイム)を使っているために発生する在庫。前記のような事項をまとめ、その特徴を表にして示す。
関連用語: 品目
在庫管理手法を発注の観点から捉えると、定量発注法と定期発注法の2つに分けることができる。このどちらの方式も安全在庫を常備する点においては同じである。しかし、発注量と発注時期についてみると、定量発注法は、一定の量を発注するが、その時期は不定であり、発注点を基準にすることから発注点手法などとも呼ばれている。これに対し、定期発注法では、一定の時期を決めておいて、その時期に発注するが、発注量は不定である。これらはまた、統計的在庫管理手法とも呼ばれ、発注の基準となる量や期間を、過去の使用実績を基に設定し運用・管理する方法である。この管理手法の主な特徴は、管理対象となっている品目を個々独立に管理することにある。
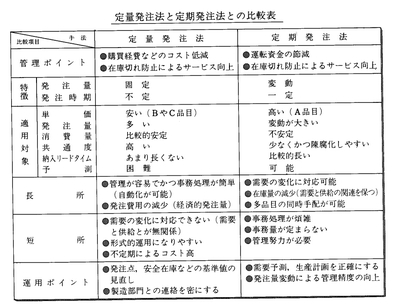
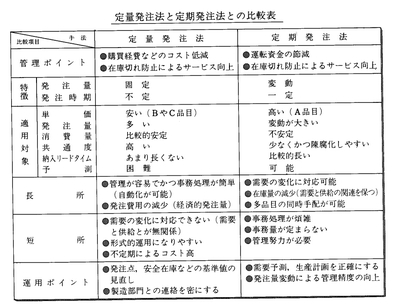
Inventory
倉庫として管理されている場所に品物を保管することを在庫といい、在庫されている品目を在庫品と呼ぶ。また、在庫の管理は、実際に倉庫にある実在庫と帳簿上での帳簿在庫とで行われるのが一般的である。なお、MRPの計画精度を上げるには、実在庫と帳簿在庫のくい違いを少なくする必要がある。この実際と帳簿との差異数量を少なくすること、つまり在庫精度を上げることが重要となる。
倉庫として管理されている場所に品物を保管することを在庫といい、在庫されている品目を在庫品と呼ぶ。また、在庫の管理は、実際に倉庫にある実在庫と帳簿上での帳簿在庫とで行われるのが一般的である。なお、MRPの計画精度を上げるには、実在庫と帳簿在庫のくい違いを少なくする必要がある。この実際と帳簿との差異数量を少なくすること、つまり在庫精度を上げることが重要となる。
Service Ratio
製品や部品それに材料の要求に対して、どの程度対応できるかという満足度のことである。これは、一般に品切率の逆数として示され、次の式で表わされる。
関連用語: 定量発注法
製品や部品それに材料の要求に対して、どの程度対応できるかという満足度のことである。これは、一般に品切率の逆数として示され、次の式で表わされる。
サービス率=出庫量/要求量
関連用語: 定量発注法
MRPで計画されたオーダーに基づく入出庫を計画入出庫といい、計画入出庫以外の入出庫を計画外入出庫と称する。計画外入出庫には次のようなものがある。
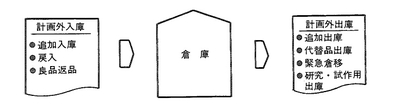
■計画外入庫
反意語: 計画入出庫
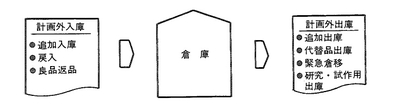
■計画外入庫
●追加入庫:製造オーダー、外注オーダーにおいて、当初の見込より不良が少なく、計画されていた所要量よりも多く入庫するような場合。■計画外出庫
●戻入:不良率の見積値が高い時や出庫後に緊急の設計変更が入った場合などに、すでに工程に払い出されている品目を返庫するようなことをいう。
●良品返品:サービス部品などのオーダーや数量の間違いで返庫されるような場合。
●追加出庫:すでに計画オーダーに基づいて出庫された品目の不良が予定より多く発生したり、製造オーダーが変更されて所要量が増えたりした場合に、この不足を補うために行う出庫を示す。
●代替品出庫:"だいたいひん"出庫とか"だいがえひん"出庫などという。これは、使用予定の品目に欠品を生じた時や旧品目の在庫を使い切る以前に設計変更が実施された場合などに、予定出庫品目を出庫せずに代替品を出庫することである。
●緊急倉移:計画に反映できずに緊急に発生した倉庫間移送。
●研究・試作用出庫:設計部門の研究・試作のための出庫。
反意語: 計画入出庫
多くの場合、製造企業は複数の倉庫をもっている。また、工場を複数もっている場合も少なくない。倉移とは、"くらうつし"と称し、倉庫間の在庫品の移動を示す。工場内に複数の倉庫があり、在庫品が分散している場合、必要に応じて移動することを一般に倉庫間移送といい、工場間で在庫品を移動する場合を工場間移送といい、これらを総称して倉移と呼ぶ。また、MRPにより倉移を計画し、これに基づいて移送することを計画倉移とか自動倉移といい、計画以外に発生する倉移を計画外倉移とか緊急倉移などという。
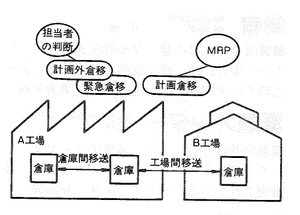
関連用語: 計画外入出庫
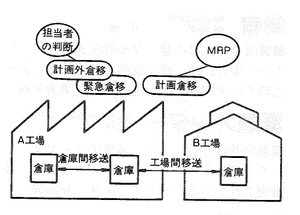
関連用語: 計画外入出庫
棚卸資産評価や出庫金額算出の手法の1つで、異なる単価の在庫品を受入れても、その単価に数量を加重して計算する方法である。たとえば、右の図の受入単価は、1日、7日、15日、24日それぞれが異なっている。この場合、加重平均法では、受入総金額25,000を受入総数量110で除して、これに残高40を掛けて棚卸資産9091を算出する。
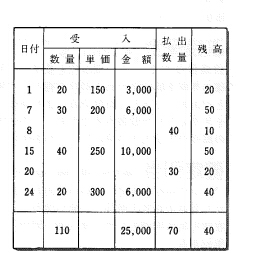
(25,000÷110)×40=9091
関連用語: 平均原価法
Moving Average
棚卸資産評価や出庫金額算出の手法の1つで、月末とか期末とかの棚卸の時に計算するのではなく、在庫品を受入れるたびに、その時点での単価を算出する方法である。
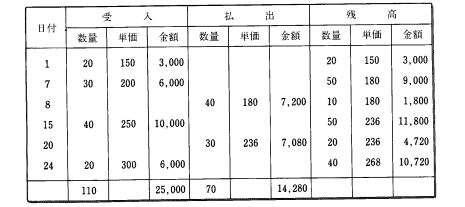
関連用語: 平均原価法
棚卸資産評価や出庫金額算出の手法の1つで、月末とか期末とかの棚卸の時に計算するのではなく、在庫品を受入れるたびに、その時点での単価を算出する方法である。
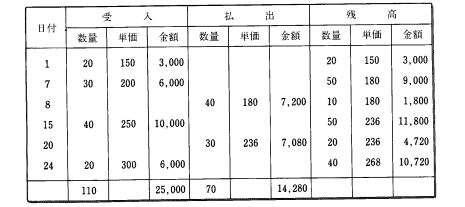
40×268=10,720
関連用語: 平均原価法
Simultaneous Stocktaking
ある時期に、倉庫や工程それに外注先などにある、あらゆる品目を一度に棚卸することをいう。これに対し、倉庫だけの棚卸を倉庫棚卸といい、工程や外注先の棚卸を仕掛棚卸という。
関連用語: 棚卸
ある時期に、倉庫や工程それに外注先などにある、あらゆる品目を一度に棚卸することをいう。これに対し、倉庫だけの棚卸を倉庫棚卸といい、工程や外注先の棚卸を仕掛棚卸という。
関連用語: 棚卸
Safety Stock
SS(Safety Stock)などとも略され、発注から入庫までの期間、いわゆる購買リードタイムの間に予想される消費量と実際との誤差を考慮して、ある一定のサービス水準を保証しようとするものである。図1で示したごとく、発注から入庫までの購買リードタイムの間の消費量に変動がある。この変動にどの程度対応するかといったサービスの度合、つまりサービス率でもって安全在庫量が決まる。一般に、サービス率は安全係数に変換されており、安全在庫量は次の式によって求められる。

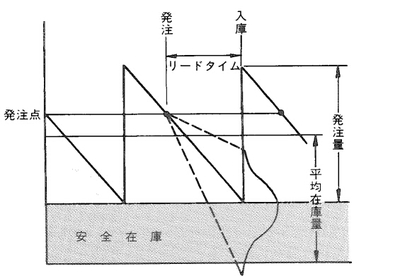
また、MRPにおいて安全在庫は、引当計算(正味所要量計算)の対象とする場合としない場合がある。対象とする場合は、安全在庫も現在庫の一部として、そのまま引当計算を行い、最初に作成された予定オーダーに安全在庫量を加える方法がとられる(図2)。これに対し、引当計算の対象としない場合は、現在庫から安全在庫を差引き、この結果を使用可能在庫として計算を行う。(図3)。
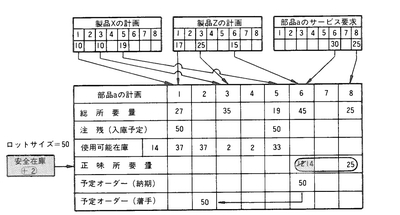
関連用語: 在庫
SS(Safety Stock)などとも略され、発注から入庫までの期間、いわゆる購買リードタイムの間に予想される消費量と実際との誤差を考慮して、ある一定のサービス水準を保証しようとするものである。図1で示したごとく、発注から入庫までの購買リードタイムの間の消費量に変動がある。この変動にどの程度対応するかといったサービスの度合、つまりサービス率でもって安全在庫量が決まる。一般に、サービス率は安全係数に変換されており、安全在庫量は次の式によって求められる。

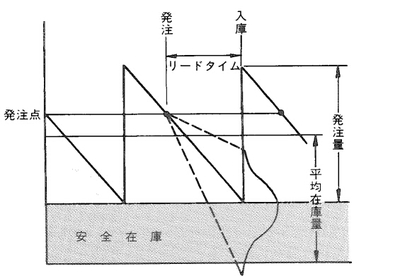
図1 誤差の正規分布
また、MRPにおいて安全在庫は、引当計算(正味所要量計算)の対象とする場合としない場合がある。対象とする場合は、安全在庫も現在庫の一部として、そのまま引当計算を行い、最初に作成された予定オーダーに安全在庫量を加える方法がとられる(図2)。これに対し、引当計算の対象としない場合は、現在庫から安全在庫を差引き、この結果を使用可能在庫として計算を行う。(図3)。
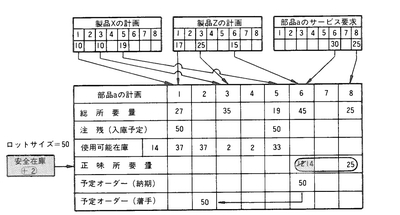
図3 引当計算の対象としない場合
関連用語: 在庫
Last-in First-out
棚卸資産評価や出庫金額算定の手法の1つで、後に入庫したものから順に出庫されるものとして計算する方法である。これは、タクシーとお客のようなもので、タクシーが倉庫で数人のお客を在庫品に例えることができる。つまり、あとから乗車したお客(在庫品)が、先に乗車したお客よりも早くタクシー(倉庫)を出ることになる。この方法では、当初入庫された在庫品は余り動かないため、ある程度一定した棚卸額が維持されることになる。
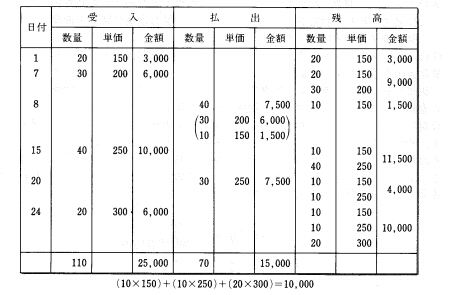
関連用語: 原価法
棚卸資産評価や出庫金額算定の手法の1つで、後に入庫したものから順に出庫されるものとして計算する方法である。これは、タクシーとお客のようなもので、タクシーが倉庫で数人のお客を在庫品に例えることができる。つまり、あとから乗車したお客(在庫品)が、先に乗車したお客よりも早くタクシー(倉庫)を出ることになる。この方法では、当初入庫された在庫品は余り動かないため、ある程度一定した棚卸額が維持されることになる。
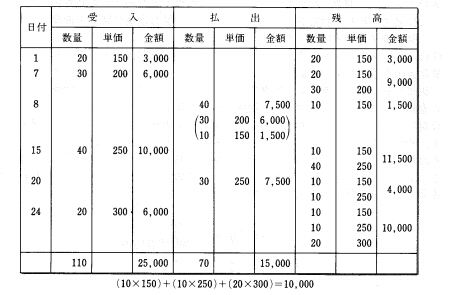
関連用語: 原価法
購買業者や外注業者が受注した品目を納入する際、受注時に指示された数量を1度に納入せず、何回かに分けて納入することである。また、発注側で、あるまとまった数量で注文し、製造作業に合わせて分納指示する場合もある。
関連用語: 受入
関連用語: 受入
品目は単一工程でつくられるとは限らない。通常いくつかの工程を経てつくられる。品目外注は、ある品目をつくり上げる複数の工程をまとめて一貫して外注することをいう。また、外注業者が製品まで一貫してつくる場合もある。これも品目外注の1つであるが、この場合、とくに製品外注とか一貫外注、完成品外注または外製などと呼んでいる。これは、専門的な設備や技術を必要とし、自社にこれらがない場合や原価引下げ、さらに外注下請業者の育成などのために行われるもので、部品表設定の時に政策的に行われる。このことから、品目外注については、MRPの計画がなされたならば、次に購買品の購買計画と同様に外注計画を行う必要がある。
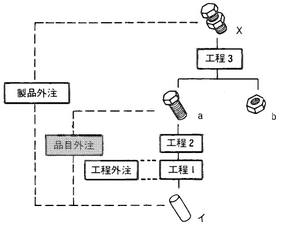
関連用語: 外注
反意語: 工程外注
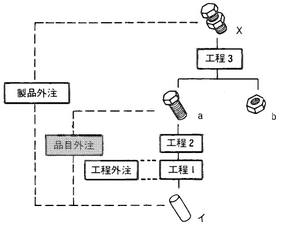
関連用語: 外注
反意語: 工程外注
Planned Release Date
オーダーが発注されるべき期日のことである。発注するオーダーが外注オーダーの場合には、その発注予定日に支給品を出庫する必要がある。また、予定に対して、実際に業者へ発注した日を発注日という。各オーダーの発注がオーダー単位に行われる場合は、発注予定日と発注日は同じになる。しかし、一般には一定期間のオーダーをまとめて発注する方法がとられるため、発注予定日と発注日は一致しないことがある。
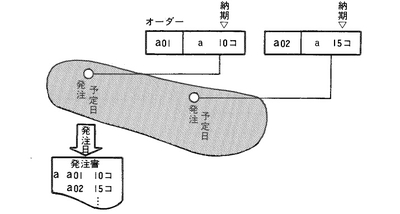
関連用語: 発注
オーダーが発注されるべき期日のことである。発注するオーダーが外注オーダーの場合には、その発注予定日に支給品を出庫する必要がある。また、予定に対して、実際に業者へ発注した日を発注日という。各オーダーの発注がオーダー単位に行われる場合は、発注予定日と発注日は同じになる。しかし、一般には一定期間のオーダーをまとめて発注する方法がとられるため、発注予定日と発注日は一致しないことがある。
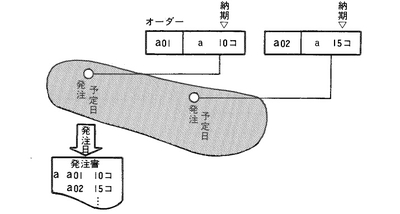
関連用語: 発注
一般に納入残といった場合、品物の発注か受注かの立場によってその解釈が異なる。発注の立場からみると、業者に発注した品目が、そのオーダーの発注量に満たないで納入された時、発注量に対し不足した未納入数量のことを納入残といい、発注残を意味する。一方、受注の立場においては、注文を受けたオーダーの受注量に対し、いまだ納入できないでいる数量のことを納入残といい、受注残を示す。
関連用語: 受入
関連用語: 受入
支給品のある外注品を外注業者に発注する時、自社から支給するのではなく、その支給品を購買先から直接、外注業者に送ることを直送といい、その時の支給品を直送品という。また、業者から直接、自社の製造工程へ納入される品目を直送品という場合もある。
関連用語: 支給品
関連用語: 支給品
Direct Sending
支給品のある外注品を外注業者に発注する時、その支給品を自社から支給するのではなく、その支給品を購買先から直接、外注業者に送ることをいう。また、購買品や外注品を納入する場合、その品目を使用する工程へ直接納入することを直送と呼ぶこともある。この場合、伝票処理は自社へ一担納入された時と同様に取扱うのが一般的である。
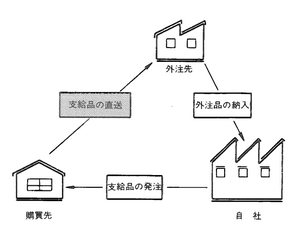
関連用語: 購買計画
支給品のある外注品を外注業者に発注する時、その支給品を自社から支給するのではなく、その支給品を購買先から直接、外注業者に送ることをいう。また、購買品や外注品を納入する場合、その品目を使用する工程へ直接納入することを直送と呼ぶこともある。この場合、伝票処理は自社へ一担納入された時と同様に取扱うのが一般的である。
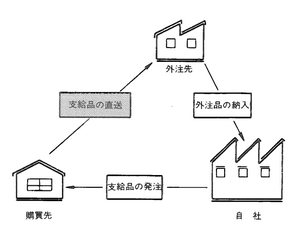
関連用語: 購買計画
Traveling Inspection
検査を検査場所で分類した時の1つの方法で、購買品や外注品の受入検査を自社で行わず、購買業者や外注業者などの発注先に行って実施する検査のことである。これは、自社に検査設備をもたない場合や、次工程が外注の場合などに行われる。
関連用語: 検査
検査を検査場所で分類した時の1つの方法で、購買品や外注品の受入検査を自社で行わず、購買業者や外注業者などの発注先に行って実施する検査のことである。これは、自社に検査設備をもたない場合や、次工程が外注の場合などに行われる。
関連用語: 検査
通常であれば、製品は自社の工場でつくられる。しかし、自社の能力では間に合わない時や、自社技術では難しいとか、原価面で他社の方が安い場合などに、外注業者に製作依頼をすることがある。この時、依頼品目をつくるのに必要な部品や素材を自社から外注業者に対して提供することを支給といい、業者に払い出す部品や素材を支給品という。
支給には、支給品を無償で提供する場合と、有償で提供する場合とがある。一般に前者の方法を無償支給といい、後者を有償支給と呼ぶ。また、外注業者に対する支給品の扱いについては、自社から支給する場合と、購買品などの支給品をその購入先の業者から直接支給する場合とがある。前者を直接払出といい、後者を直送と呼ぶ。
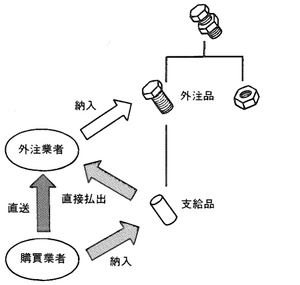
関連用語: 支給品、購買計画
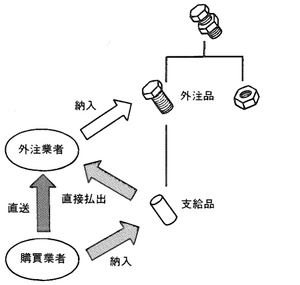
関連用語: 支給品、購買計画
Purchasing Planning
MRPで計画された購買品および外注品について、発注数の見直し、発注業者の選定、注文単価の設定、業者納期の指定、検査予定日の決定などの作業を行う。また、各業者への発注量が能力をオーバーしていないかどうかのチェックも行う。外注品については、外注先および外注品の種類によって支給する必要のある品目があり、そのための支給品の払出計画も行う。
MRPで計画された購買品および外注品について、発注数の見直し、発注業者の選定、注文単価の設定、業者納期の指定、検査予定日の決定などの作業を行う。また、各業者への発注量が能力をオーバーしていないかどうかのチェックも行う。外注品については、外注先および外注品の種類によって支給する必要のある品目があり、そのための支給品の払出計画も行う。
業者から納入された品目を検査して、受入可能となったものを代金支払いの対象として計上するための作業である。MRPシステムにおいて、検収されたオーダーは“完了”となり、注残把握から解除される。
Raw Materials
原材料とは、原料と材料の双方を意味するものである。原料とは、加工をすることによって形や質が変わるものであり、材料とは、そのままの質で製品や部品に使われるものである。物をつくる工場において原材料は、その生産工程で最初に扱われる資材であり、購入部品などと同様に製品を表現する部品表上では最下位に位置する品目である。
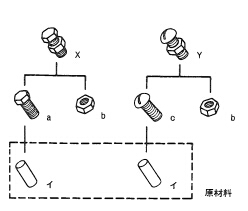
関連用語: 購買品
原材料とは、原料と材料の双方を意味するものである。原料とは、加工をすることによって形や質が変わるものであり、材料とは、そのままの質で製品や部品に使われるものである。物をつくる工場において原材料は、その生産工程で最初に扱われる資材であり、購入部品などと同様に製品を表現する部品表上では最下位に位置する品目である。
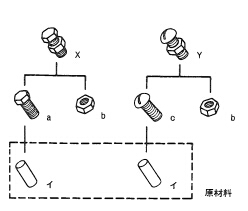
関連用語: 購買品
Subcontract Order
製造品目に必要なオーダーのうち、外注業者で製造する場合のオーダーをいう。これには、品目単位であらかじめ外注が決まっている場合と、工程単位で外注に指示される場合とがある。外注オーダーには、品目、工程、納期、所要量のほかに、購買オーダーと同様、業者に関する情報や単価、納入情報などが付される。
関連用語: オーダー
製造品目に必要なオーダーのうち、外注業者で製造する場合のオーダーをいう。これには、品目単位であらかじめ外注が決まっている場合と、工程単位で外注に指示される場合とがある。外注オーダーには、品目、工程、納期、所要量のほかに、購買オーダーと同様、業者に関する情報や単価、納入情報などが付される。
関連用語: オーダー
Subcontract
下請会社や関連会社に対して作業を依頼することをいう。この外注の方式には、品目単位に一括して発注する品目外注と、一部の工程作業を発注する工程外注の2つの方法がある。
下請会社や関連会社に対して作業を依頼することをいう。この外注の方式には、品目単位に一括して発注する品目外注と、一部の工程作業を発注する工程外注の2つの方法がある。
Acceptance
MRPなどにより計画された購買オーダーや外注オーダーを基に、取引業者からの納品物を受け取ることをいう。ここでは、発注したオーダーの納期や数量など発注時の条件と相違ないかを確認すると同時に、分納が発生する場合にはそのための処置を行う。
MRPなどにより計画された購買オーダーや外注オーダーを基に、取引業者からの納品物を受け取ることをいう。ここでは、発注したオーダーの納期や数量など発注時の条件と相違ないかを確認すると同時に、分納が発生する場合にはそのための処置を行う。
同じ材料を用い、同じ工程から複数の製品を生産する場合に適用される原価計算で、石灰からコークス、タールなどを生産する企業などがこれを用いる。この原価計算では、連産品別の製造原価を決める等価比率の適切な設定が重要となる。
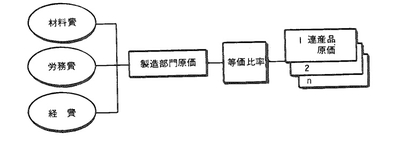
関連用語: 総合原価計算
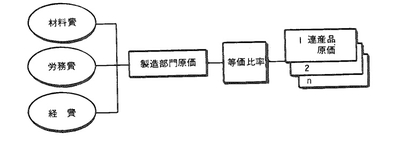
関連用語: 総合原価計算
ある特定の品目に注目した時、その品目自体の内部原価にその構成品としての加工や購入の原価である外部原価を加えたものを累積原価という。たとえば、製品Xの内部原価は労務費の10円であり、製品Xの外部原価は部品aの加工費15円と部品b、材料イの材料費12円である。この時、製品Xの累積原価は、材料費が12円、労務費が25円となり、製品原価として37円となる。
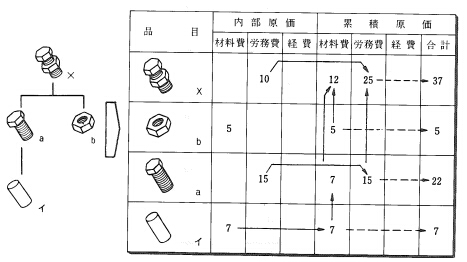
このように各品目の累積原価は、組立品や部品それに原材料などそれぞれの品目に登録されている内部原価を積上げることにより算出される。これは一般に、製品別標準原価計算もしくは原価積上げなどといわれている。
コンピュータでこの累積原価を算出するには、部品表の品目に、原価情報として内部原価の欄と累積原価の欄を設ける。この各々の原価欄の明細項目として材料費、労務費、経費の欄をもつ。外注の扱い品目の多い工場では、外注加工費を別項として設定する。また、内部原価の欄を標準原価と当座標準原価とに大きく分けて、それぞれに原価要素をもたせることもある。いずれにせよ、累積原価は、見積書作成原価変更、標準原価計算などに使われる。
関連用語: 内部原価と外部原価
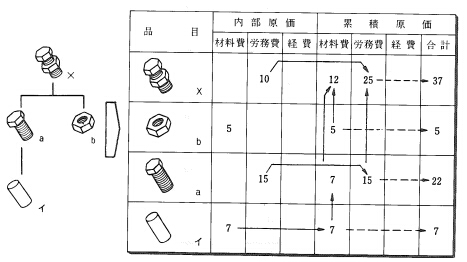
このように各品目の累積原価は、組立品や部品それに原材料などそれぞれの品目に登録されている内部原価を積上げることにより算出される。これは一般に、製品別標準原価計算もしくは原価積上げなどといわれている。
コンピュータでこの累積原価を算出するには、部品表の品目に、原価情報として内部原価の欄と累積原価の欄を設ける。この各々の原価欄の明細項目として材料費、労務費、経費の欄をもつ。外注の扱い品目の多い工場では、外注加工費を別項として設定する。また、内部原価の欄を標準原価と当座標準原価とに大きく分けて、それぞれに原価要素をもたせることもある。いずれにせよ、累積原価は、見積書作成原価変更、標準原価計算などに使われる。
関連用語: 内部原価と外部原価
Variable Cost
製品の生産量や販売量に応じて、一定期間における総額が比例的に変動する原価をいう。つまり、変動費は、製品の生産に直接関連することから、製品原価とか直接原価、それに限界利益に対して限界原価などとも呼ばれる。 変動費は、その変動の割合によって、次の3つに分けられる。
● 比例費:生産・販売量に正比例して変動する。
● 逓増費:生産・販売量に応じて変動するが、その割合が変動以上になる。
● 逓減費:生産・販売量に応じて変動するが、その割合が変動以下になる。
関連用語: 費用構成
製品の生産量や販売量に応じて、一定期間における総額が比例的に変動する原価をいう。つまり、変動費は、製品の生産に直接関連することから、製品原価とか直接原価、それに限界利益に対して限界原価などとも呼ばれる。 変動費は、その変動の割合によって、次の3つに分けられる。
● 比例費:生産・販売量に正比例して変動する。
● 逓増費:生産・販売量に応じて変動するが、その割合が変動以上になる。
● 逓減費:生産・販売量に応じて変動するが、その割合が変動以下になる。
関連用語: 費用構成
Standard Cost Accounting
科学的、統計的方法で、かつ能率の尺度となり得る標準消費量や標準価格を用いて行う原価計算をいう。これは、実際消費量や実際価格を用いた実際原価計算が財務会計に役立つのに対し、原価管理を徹底し、経営の効率化を図るために行われる。標準原価計算を行うには、まず標準原価を設定することから始まる。標準原価は、その適用の期間と目標の高さから区分すると、当座標準原価、基準標準原価それに理論標準原価の3つに分けることができる。また、直接材料費、直接労務費、製造間接費について各々次のように標準を設定する。
このような標準原価の関連は図のようになり、このうち標準原価計算により、主に物量標準を対象として原価管理が行われる。
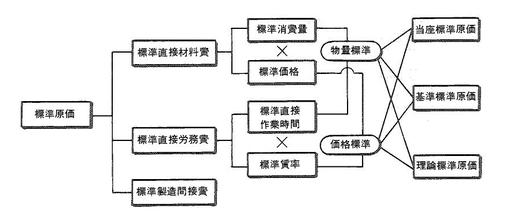
関連用語: 原価計算
科学的、統計的方法で、かつ能率の尺度となり得る標準消費量や標準価格を用いて行う原価計算をいう。これは、実際消費量や実際価格を用いた実際原価計算が財務会計に役立つのに対し、原価管理を徹底し、経営の効率化を図るために行われる。標準原価計算を行うには、まず標準原価を設定することから始まる。標準原価は、その適用の期間と目標の高さから区分すると、当座標準原価、基準標準原価それに理論標準原価の3つに分けることができる。また、直接材料費、直接労務費、製造間接費について各々次のように標準を設定する。
標準直接材料費=標準消費量×標準価格
標準直接労務費=標準直接作業時間×標準賃率
標準製造間接費:固定予算または変動予算のいずれかで計上
このような標準原価の関連は図のようになり、このうち標準原価計算により、主に物量標準を対象として原価管理が行われる。
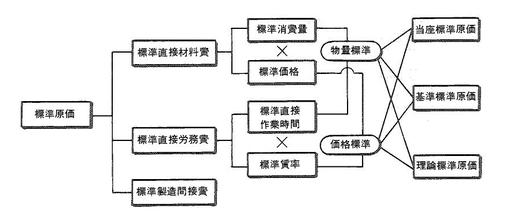
関連用語: 原価計算
Standard Cost
科学的、統計的方法で、かつ能率の尺度となり得る標準消費量や標準価格を用いて計算された原価をいう。これは、事前原価であり、正常な状態を前提とした実体原価である。
標準原価には、次の種類がある。
● 当座標準原価:現実的標準原価を指し、通常発生する仕損や減耗、遊休時間などのロス率を含んだ、達成可能な原価目標を示す。また、この原価は、実際に即した標準原価であり、一事業年度内に材料費や労務費に大きな変動が生じた場合、随時改訂され、予算の基礎や棚卸の評価に使われる。このため標準原価は予算原価とか予定原価と呼ばれる。
● 基準標準原価:正常的標準原価を指し、いったん立てた原価を次年度以降も継続して使用し、将来の原価動向を把握するための基礎として用いる。
● 理論標準原価:理想的標準原価を指し、努力目標として、理論的に達成可能な最高の操業度、最大の能率により計算された最低の原価を示す。これは仕損、減耗、ロス率など過去の値からすべて取り除いた値を使用する。
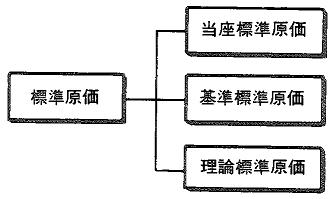
関連用語: 費用構成
科学的、統計的方法で、かつ能率の尺度となり得る標準消費量や標準価格を用いて計算された原価をいう。これは、事前原価であり、正常な状態を前提とした実体原価である。
標準原価には、次の種類がある。
● 当座標準原価:現実的標準原価を指し、通常発生する仕損や減耗、遊休時間などのロス率を含んだ、達成可能な原価目標を示す。また、この原価は、実際に即した標準原価であり、一事業年度内に材料費や労務費に大きな変動が生じた場合、随時改訂され、予算の基礎や棚卸の評価に使われる。このため標準原価は予算原価とか予定原価と呼ばれる。
● 基準標準原価:正常的標準原価を指し、いったん立てた原価を次年度以降も継続して使用し、将来の原価動向を把握するための基礎として用いる。
● 理論標準原価:理想的標準原価を指し、努力目標として、理論的に達成可能な最高の操業度、最大の能率により計算された最低の原価を示す。これは仕損、減耗、ロス率など過去の値からすべて取り除いた値を使用する。
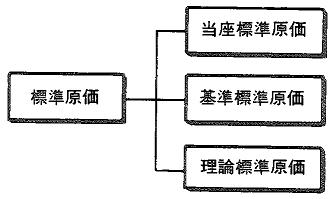
関連用語: 費用構成
受注生産の場合、製品の販売価格は、一般にその製品を製造し、販売するのに消費された費用、つまり総原価に適切な利潤を加えて決定される。また、見込生産の場合、製品の販売価格は普通市場価格によって決定される。このため適切な利潤を引いた残りが投入でき得る総原価ということになる。
このように受注生産、見込生産において、原価に対する考え方が異なるにしても、製品販売価格からみた費用構成は、いずれも概念的に同じであり、図のようになる。製品の費用構成の基本は製造原価であり、これは直接費と間接費とに分けられる。製造直接費は、直接材料費、直接労務費、直接経費から成り、これに光熱費、治工具費、保全費、設計、購買、福利厚生などの製造間接費を加えると製造原価となる。これに広告宣伝費、販売員給与などの販売費及び一般管理費を加えて総原価となる。
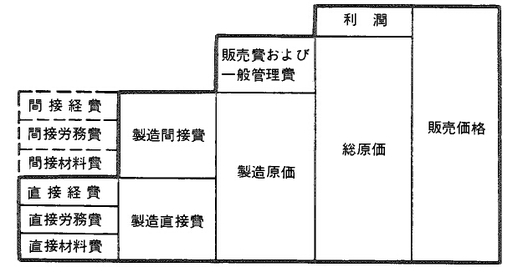
このように受注生産、見込生産において、原価に対する考え方が異なるにしても、製品販売価格からみた費用構成は、いずれも概念的に同じであり、図のようになる。製品の費用構成の基本は製造原価であり、これは直接費と間接費とに分けられる。製造直接費は、直接材料費、直接労務費、直接経費から成り、これに光熱費、治工具費、保全費、設計、購買、福利厚生などの製造間接費を加えると製造原価となる。これに広告宣伝費、販売員給与などの販売費及び一般管理費を加えて総原価となる。
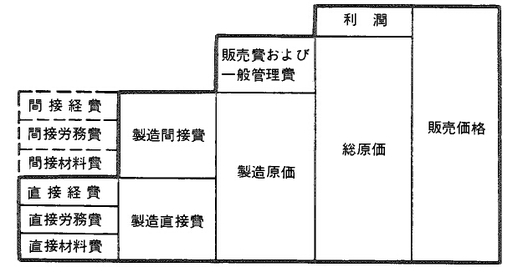
品目の原価は内部原価と外部原価とに分けることができる。製品を構成しているある特定の品目の原価に注目した時、その品目を製造するために消費する原価とその品目の構成品、つまり子品目での加工および購入に要する原価とに分かれる。前者を内部原価と称し、後者を外部原価といい、内部と外部の両原価を合わせて、その品目の累積原価という。
図で示す製品Xは、組立品aとbを使用して組立てられる。この場合、製品Xの内部原価はXの組立に要した費用であり、外部原価は、原単位および不良率を考慮した組立品aの加工費と部品bの買入部品費それに材料イの主要材料費の合計となる。また、製品Xの累積原価は、この内部原価と外部原価の和によって求められる。 このように各品目の原価を内部原価と外部原価とに分けて管理することにより、より細かな原価の分析ができ、また原価変更に対しても原価積上げが簡単になることから、その影響把握も容易になる。
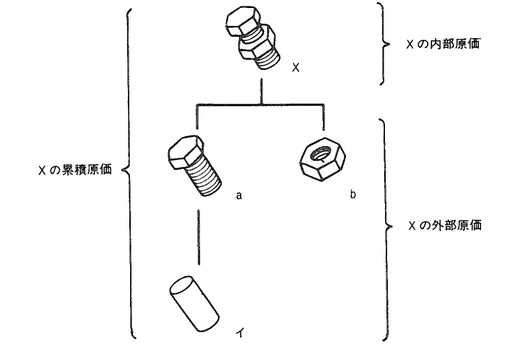
関連用語: 費用構成
図で示す製品Xは、組立品aとbを使用して組立てられる。この場合、製品Xの内部原価はXの組立に要した費用であり、外部原価は、原単位および不良率を考慮した組立品aの加工費と部品bの買入部品費それに材料イの主要材料費の合計となる。また、製品Xの累積原価は、この内部原価と外部原価の和によって求められる。 このように各品目の原価を内部原価と外部原価とに分けて管理することにより、より細かな原価の分析ができ、また原価変更に対しても原価積上げが簡単になることから、その影響把握も容易になる。
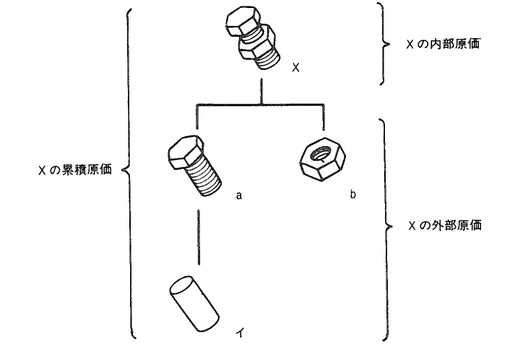
関連用語: 費用構成
品目の原価は内部原価と外部原価とに分けることができる。内部原価とは、ある品目を製造または購入するための原価を示す。内部原価の内容には、材料費、労務費、経費、外注加工費、間接費がある。この例を図示する。このように各品目ごとに内部原価をもつことで、原価変更による影響把握などが容易になる。
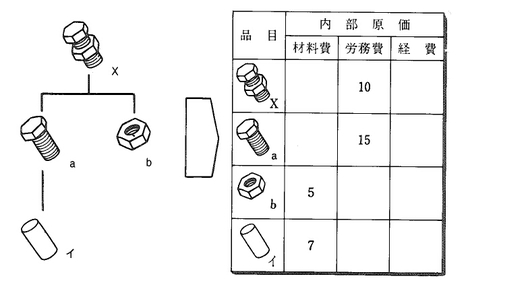
関連用語: 内部原価と外部原価
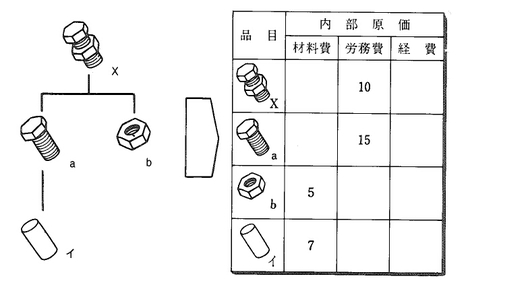
関連用語: 内部原価と外部原価
製紙業、製鉄業、製材業などのように、同じ種類の製品を同じ原材料、同じ工程を使って連続的に生産する企業で用いられる原価計算である。この原価計算は、製品のクラス別の原価を分割する基準、つまり等価比率を正確に求めることが重要となる。
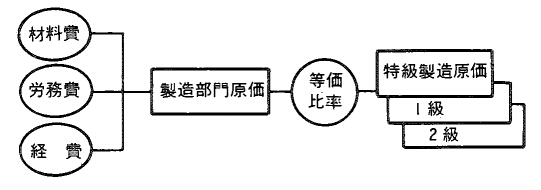
関連用語: 総合原価計算
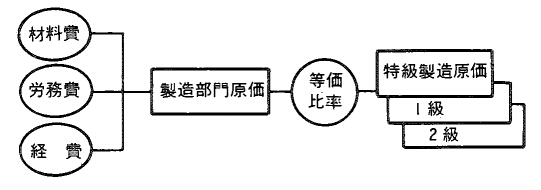
関連用語: 総合原価計算
Direct Cost
製造原価をその形態から捉えると直接費と間接費とに分けられる。直接費とは、製品の製造に消費した物量のうち、計測し得るものについての原価であり、直接材料費、直接労務費、直接経費に分けることができる。
関連用語: 費用構成
製造原価をその形態から捉えると直接費と間接費とに分けられる。直接費とは、製品の製造に消費した物量のうち、計測し得るものについての原価であり、直接材料費、直接労務費、直接経費に分けることができる。
関連用語: 費用構成
Direct Material Cost
製造原価の直接費に含まれる費用で、製品の製造に直接消費される材料費である。これは大きく、製品の主要部分となる主要材料費と、購入されてそのまま製品に組み付けられる買入部品費とに分けることができる。
関連用語: 直接費
製造原価の直接費に含まれる費用で、製品の製造に直接消費される材料費である。これは大きく、製品の主要部分となる主要材料費と、購入されてそのまま製品に組み付けられる買入部品費とに分けることができる。
関連用語: 直接費
Direct Costing
全部原価計算が製造に費やしたすべての原価を単位原価の対象とするのに対し、部分原価計算としての直接原価計算では、変動費のみを製品にかかわらせて、単位原価を計算する方法である。このことから、直接原価計算とは製品の生産と販売との関係で原価を変動費と固定費に分け、製品の原価を変動費だけで計算し、固定費は期間原価として捉え、その総原価を対象期間の収益に対応させる原価計算である。 この原価計算は、全部原価計算などと比べると簡単であるだけでなく、予算、利益、原価の各々の計画と管理に対する資料がたやすく得られる利点がある。しかし、計算の対象が変動費だけであるため、財務会計上、調整計算が必要となる。
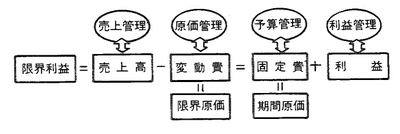
関連用語: 原価計算
全部原価計算が製造に費やしたすべての原価を単位原価の対象とするのに対し、部分原価計算としての直接原価計算では、変動費のみを製品にかかわらせて、単位原価を計算する方法である。このことから、直接原価計算とは製品の生産と販売との関係で原価を変動費と固定費に分け、製品の原価を変動費だけで計算し、固定費は期間原価として捉え、その総原価を対象期間の収益に対応させる原価計算である。 この原価計算は、全部原価計算などと比べると簡単であるだけでなく、予算、利益、原価の各々の計画と管理に対する資料がたやすく得られる利点がある。しかし、計算の対象が変動費だけであるため、財務会計上、調整計算が必要となる。
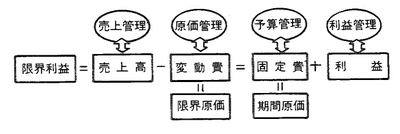
関連用語: 原価計算
Direct Expense
製造原価の直接費に含まれる費用で、特定の製品の製造原価として直課させる原価を直接経費と呼ぶ。しかし、製造原価の経費の多くは間接費で、場合によっては外注加工費や設計費などが直接経費として扱われる。
関連用語: 直接費
製造原価の直接費に含まれる費用で、特定の製品の製造原価として直課させる原価を直接経費と呼ぶ。しかし、製造原価の経費の多くは間接費で、場合によっては外注加工費や設計費などが直接経費として扱われる。
関連用語: 直接費
セメント業、製氷業、製麺業、電球製造業などのように、単一の製品を単一の工程で反復連続的に生産している企業で用いられる原価計算である。この原価計算では、一定期間を対象として計算が行われ、その方法は、単一工程総合原価計算と工程別総合原価計算とに分けられる。
単一工程総合原価計算では、単一製品を単一工程で製造する工場に適用されるもので、一定期間に発生した費用をその期間に製造した製品数で除して製品1単位当りの製造原価を算出する。また、工程別総合原価計算は、単一製品を複数の工程で製造する工場に適用される方法である。この場合、各工程で発生した共通費の配賦が必要となる。これらのいずれの原価計算でも、仕掛品の評価が製造原価に大きく左右する。このため、現品管理や在庫管理を充実させるとともに、的確な棚卸を行い、適正な仕掛評価をすることが重要となる。
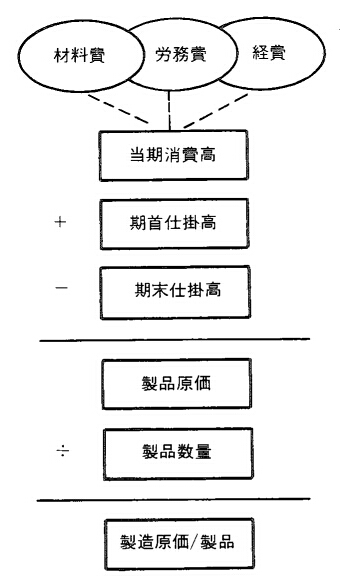
関連用語: 総合原価計算
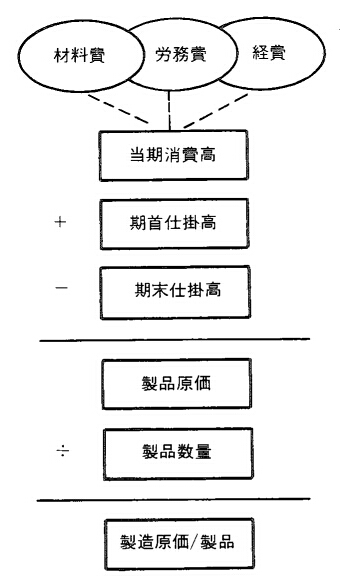
関連用語: 総合原価計算
Full Costing
原価は、原価計算の範囲やその対象の違いによって全部原価と部分原価とに分けられる。実際原価計算や標準原価計算などは、製品の生産や販売によって発生するすべての原価を一括して計算する。このような原価計算を全部原価計算と称する。これに対し一部の原価で計算する方法を部分原価計算といい、直接原価計算がこれに当たる。財務会計上は、全部原価計算が用いられるが、売上高と利益とが必ずしも比例しないため、原価管理には直接原価計算の方が向いている。
全部原価計算の手順は、実際原価計算や標準原価計算と同じで、まず原価を直接費と間接費とに分け、次に製造部門と補助部門に分類して集計し、最後に製品に直課または賦課して単位原価を計算する。
関連用語: 原価計算
原価は、原価計算の範囲やその対象の違いによって全部原価と部分原価とに分けられる。実際原価計算や標準原価計算などは、製品の生産や販売によって発生するすべての原価を一括して計算する。このような原価計算を全部原価計算と称する。これに対し一部の原価で計算する方法を部分原価計算といい、直接原価計算がこれに当たる。財務会計上は、全部原価計算が用いられるが、売上高と利益とが必ずしも比例しないため、原価管理には直接原価計算の方が向いている。

関連用語: 原価計算
製品の生産量や販売量に応じて、一定期間における総額が変動する費用である。しかし、変動費と比べると比例的な変動はなく、固定費との中間的な費用である。このことから準変動費を準固定費と呼ぶこともある。
関連用語: 費用構成
関連用語: 費用構成
Actual Cost Method 原価計算
製品の生産完了後、生産過程の中で消費された実際消費量と実際取得価格による事後原価計算をいう。この原価計算は、製品、半製品、仕掛品について、生産過程で発生した実際の製造原価を計算することから、財務諸表作成のために適した原価計算である。財務会計上、製品原価の計算は原則として実際原価で行う。しかし、材料費の計算では予定価格、労務費の計算では予定賃率、間接費の計算では予定配賦率というように、一部予定価格を使って計算することもある。 実際原価計算は、決算報告には必要でも、実際原価を妥当なものとして採用するため、基準となる実際原価や不良率の原因が判別しにくい面がある。このため、原価管理を重要視するには、標準原価計算との併用が必要である。実際原価計算の計算手順は、費目別原価計算、部門別原価計算、製品別原価計算の順で行われる。
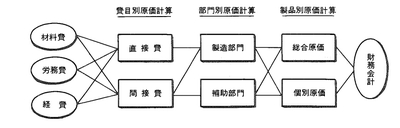
製品の生産完了後、生産過程の中で消費された実際消費量と実際取得価格による事後原価計算をいう。この原価計算は、製品、半製品、仕掛品について、生産過程で発生した実際の製造原価を計算することから、財務諸表作成のために適した原価計算である。財務会計上、製品原価の計算は原則として実際原価で行う。しかし、材料費の計算では予定価格、労務費の計算では予定賃率、間接費の計算では予定配賦率というように、一部予定価格を使って計算することもある。 実際原価計算は、決算報告には必要でも、実際原価を妥当なものとして採用するため、基準となる実際原価や不良率の原因が判別しにくい面がある。このため、原価管理を重要視するには、標準原価計算との併用が必要である。実際原価計算の計算手順は、費目別原価計算、部門別原価計算、製品別原価計算の順で行われる。
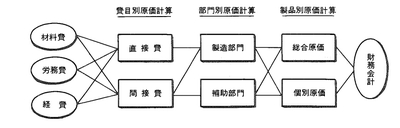
Actual Cost
製品を生産するために実際に要した消費量および実際の取得価格によって計算した原価をいう。これは、実績資料を基にして計算されるため、過去原価とか事後原価などと呼ばれる。しかし、実際の原価であっても、異常な消費量とか取得価格は除かれて、実際原価には算入しない。また、実際の消費量によって計算した原価は、たとえ予定価格を用いても実際原価とみなされる。
関連用語: 費用構成
製品を生産するために実際に要した消費量および実際の取得価格によって計算した原価をいう。これは、実績資料を基にして計算されるため、過去原価とか事後原価などと呼ばれる。しかし、実際の原価であっても、異常な消費量とか取得価格は除かれて、実際原価には算入しない。また、実際の消費量によって計算した原価は、たとえ予定価格を用いても実際原価とみなされる。
関連用語: 費用構成
Job Order Cost System
1つひとつ違う製品を製造指図書によって生産するような生産形態、つまり個別受注生産形態で使われる計算方法である。製造命令として発行された各製品の製造指図書に従って、各費用を直接費と間接費に分ける。このうち直接費は各製造指図書ごとに原価集計し、間接費は一定の基準に従って配賦計算を行い、各製造指図書ごとの製品原価に加算して製品原価を計算する。 個別原価計算は、個別に製品の原価計算を行うため、各注文に対しての採算について的確な判断が可能となり、以降の原価見積の基礎資料ともなり得る。しかし、製品個別に計算を行うため、多くの時間と経費がかかり、配賦の基準や配賦計算自体の信頼性に疑問をもたれやすい。
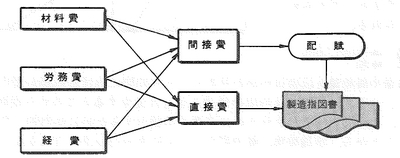
関連用語: 原価計算
1つひとつ違う製品を製造指図書によって生産するような生産形態、つまり個別受注生産形態で使われる計算方法である。製造命令として発行された各製品の製造指図書に従って、各費用を直接費と間接費に分ける。このうち直接費は各製造指図書ごとに原価集計し、間接費は一定の基準に従って配賦計算を行い、各製造指図書ごとの製品原価に加算して製品原価を計算する。 個別原価計算は、個別に製品の原価計算を行うため、各注文に対しての採算について的確な判断が可能となり、以降の原価見積の基礎資料ともなり得る。しかし、製品個別に計算を行うため、多くの時間と経費がかかり、配賦の基準や配賦計算自体の信頼性に疑問をもたれやすい。
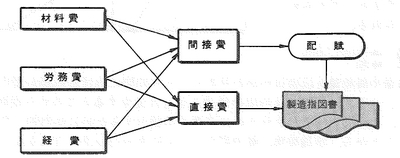
関連用語: 原価計算
Fixed Cost
製品の生産量や販売量とは直接かかわりなく、一定期間における総額が変化しない原価をいう。つまり、固定費は時間の経過とともに発生するところから期間原価と呼ばれたり、生産や販売活動を行うのに必要な準備をするために必然的に発生する費用であることから、準備費用、能力費用、とくにキャパシティコストなどとも呼ばれる。
製品の生産量や販売量とは直接かかわりなく、一定期間における総額が変化しない原価をいう。つまり、固定費は時間の経過とともに発生するところから期間原価と呼ばれたり、生産や販売活動を行うのに必要な準備をするために必然的に発生する費用であることから、準備費用、能力費用、とくにキャパシティコストなどとも呼ばれる。
部品加工業や製薬業などのように、同じ製品を数工程で連続的に生産する企業で用いられる原価計算である。この原価計算では、各工程別の当期消費高と期首、期末の仕掛高から完了品原価を求める。この計算のポイントは、複数の工程で共通に使われる工程共通費の配賦を合理的に行うことにある。
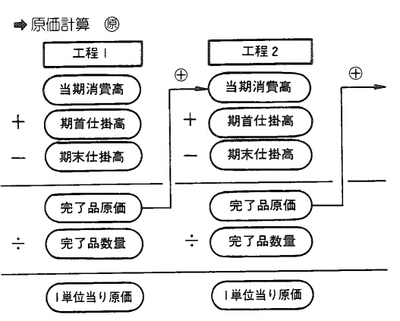
関連用語: 原価計算
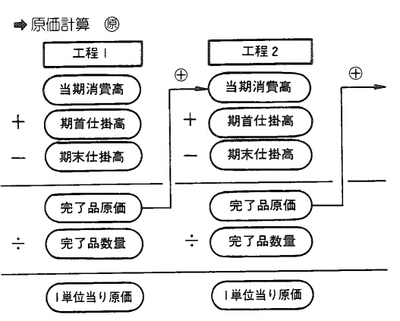
関連用語: 原価計算
Cost Variances
製品を生産するために実際に要した実際原価と、目標として設定した標準原価との差異を分析することで、管理に有効な原価情報が得られる。原価差異は、目的に応じて、次の3つに分けることができる。
直接材料費差異
直接労務費差異
製造間接費差異
直接材料費差異の原因として、市場価格の変動や価格折衝の失敗それに材料どりの悪さなどが考えられる。また直接労務費差異は期中でベースアップが起こったり標準賃率を無視した要員配置などにより発生する。これは、直接経費差異についても同じことがいえる。このように、原価差異を分析して、その主要となる原因を見つけ出し、以降の管理活動に役立てる。
関連用語: 実際原価、標準原価
製品を生産するために実際に要した実際原価と、目標として設定した標準原価との差異を分析することで、管理に有効な原価情報が得られる。原価差異は、目的に応じて、次の3つに分けることができる。
直接材料費差異
価格差異=実際消費量×(標準価格-実際価格)
数量差異=標準価格×(標準消費量-実際消費量)
直接労務費差異
賃率差異=実際作業時間×(標準賃率-実際賃率)
時間差異=標準賃率×(標準作業時間-実際作業時間)
製造間接費差異
操業度差異=(標準作業時間×標準間接費率)-標準作業時間に対する許容予算額
予算差異=標準作業時間に対する許容予算額-実際間接費
直接材料費差異の原因として、市場価格の変動や価格折衝の失敗それに材料どりの悪さなどが考えられる。また直接労務費差異は期中でベースアップが起こったり標準賃率を無視した要員配置などにより発生する。これは、直接経費差異についても同じことがいえる。このように、原価差異を分析して、その主要となる原因を見つけ出し、以降の管理活動に役立てる。
関連用語: 実際原価、標準原価
Cost Accounting
製造業での製品原価を計算することを指し、材料費に加工に要した費用を加える一連の手続をいう。
原価計算は、次の目的に従って行われる。
● 財務会計目的:財務諸表作成に必要な資料の作成。
● 予算管理目的:予算の編成や統制に必要な資料の作成。
● 価格算定目的:製品の販売価格を決定するために必要な資料の作成。
● 経営計画目的:利益計画、経営計画に必要な資料の作成。
● 原価管理目的:原価管理に必要な資料の作成。
このように原価計算は、その目的によって各種のものがあるが、企業の業種や業態それに原価の算定基準やその対象範囲から捉えると、次のように分けられる。
● 企業の業種・業態:総合原価計算、個別原価計算
● 原価の算出基準:実際原価計算、標準原価計算
● 原価の対象範囲:全部原価計算、直接原価計算
● 制度外の原価計算:特殊原価調査
原価計算を目的別にみると、このような各種の原価計算は次のように用いられる。
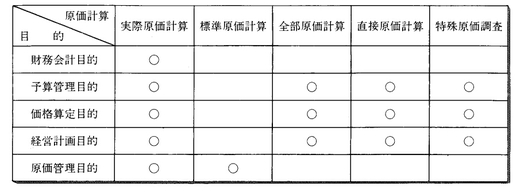
製造業での製品原価を計算することを指し、材料費に加工に要した費用を加える一連の手続をいう。
原価計算は、次の目的に従って行われる。
● 財務会計目的:財務諸表作成に必要な資料の作成。
● 予算管理目的:予算の編成や統制に必要な資料の作成。
● 価格算定目的:製品の販売価格を決定するために必要な資料の作成。
● 経営計画目的:利益計画、経営計画に必要な資料の作成。
● 原価管理目的:原価管理に必要な資料の作成。
このように原価計算は、その目的によって各種のものがあるが、企業の業種や業態それに原価の算定基準やその対象範囲から捉えると、次のように分けられる。
● 企業の業種・業態:総合原価計算、個別原価計算
● 原価の算出基準:実際原価計算、標準原価計算
● 原価の対象範囲:全部原価計算、直接原価計算
● 制度外の原価計算:特殊原価調査
原価計算を目的別にみると、このような各種の原価計算は次のように用いられる。
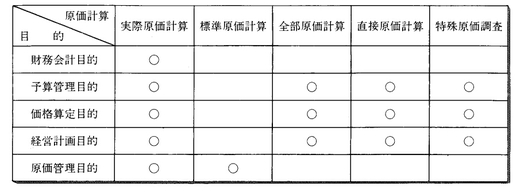
鋳物製造業、電気機器製造業などのように、異なる種類の製品を連続的に生産している企業で用いられる原価計算である。組別総合原価計算では、原価計算期間の総製造原価を組直接費と組間接費とにあらかじめ分けて、組直接費は、それぞれの組の製造オーダーに直接賦課し、組間接費は一定の基準で各組に配賦する。
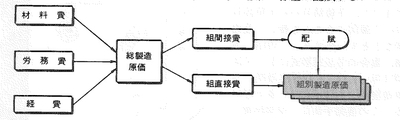
関連用語: 総合原価計算
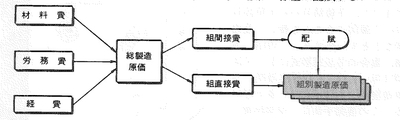
関連用語: 総合原価計算
Indirect Labor Cost
製造原価の間接費に含まれる費用で、2種類以上の製品の製造に従事している作業員への賃金を指し、倉庫部門、保全部門などの間接作業賃金や間接工の賃金などが含まれる。
関連用語: 間接費
製造原価の間接費に含まれる費用で、2種類以上の製品の製造に従事している作業員への賃金を指し、倉庫部門、保全部門などの間接作業賃金や間接工の賃金などが含まれる。
関連用語: 間接費
Overhead Cost
製造原価をその形態から捉えると直接費と間接費とに分けられる。間接費とは、個個の製品に直接的にどのくらい消費されたか、計量することができにくい原価であるか、もしくは計量することが実際に困難な原価であり、間接材料費、間接労務費、間接経費に分けることができる。
関連用語: 費用構成
製造原価をその形態から捉えると直接費と間接費とに分けられる。間接費とは、個個の製品に直接的にどのくらい消費されたか、計量することができにくい原価であるか、もしくは計量することが実際に困難な原価であり、間接材料費、間接労務費、間接経費に分けることができる。
関連用語: 費用構成
Indirect Material Cost
製造原価の間接費に含まれる費用で、製品の製造に際し、間接的または補助的に消費される材料であり、補助材料費、工場消耗品費、消耗工具備品費から成る。具体的に、補助材料費とは、燃料、油脂、塗料、薬品、包装材などがあり、工場消耗品には潤滑油などがあり、いずれも間接的、補助的に消費される。また、消耗工具備品費とは、耐用年数1年未満の工具や器具、備品などの消費額を示す。
関連用語: 間接費
製造原価の間接費に含まれる費用で、製品の製造に際し、間接的または補助的に消費される材料であり、補助材料費、工場消耗品費、消耗工具備品費から成る。具体的に、補助材料費とは、燃料、油脂、塗料、薬品、包装材などがあり、工場消耗品には潤滑油などがあり、いずれも間接的、補助的に消費される。また、消耗工具備品費とは、耐用年数1年未満の工具や器具、備品などの消費額を示す。
関連用語: 間接費
品目の原価は、内部原価と外部原価とに分けることができる。外部原価とは、ある品目に注目した時、その品目の構成品での加工および購入に要する原価合計を示す。たとえば、図のように製品Xからみた外部原価は品目a、b、イの各々の内部原価の合計であり、品目aからみた外部原価は材料イの原価が外部原価となる。ある品目の外部原価に内部原価を加えるとその品目の累積原価となり、製品別標準原価計算において使われる。
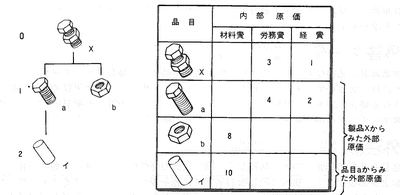
反意語: 内部原価
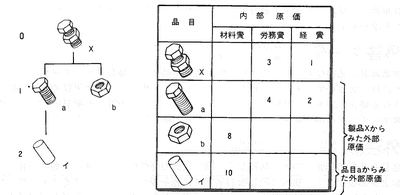
反意語: 内部原価
Paper Lead Time
販売計画が提示されてから、実際の製造指示や発注が行われるまでの期間をいう。この期間に販売部門との調整、生産能力の検討そして生産や資材計画の立案などの作業がある。これらの作業は机上で行われることから、これに要する期間を"ペーパーリードタイム"という。
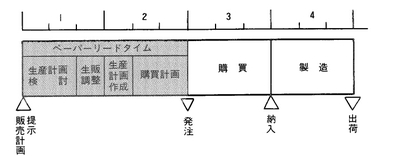
関連用語: リードタイム
販売計画が提示されてから、実際の製造指示や発注が行われるまでの期間をいう。この期間に販売部門との調整、生産能力の検討そして生産や資材計画の立案などの作業がある。これらの作業は机上で行われることから、これに要する期間を"ペーパーリードタイム"という。
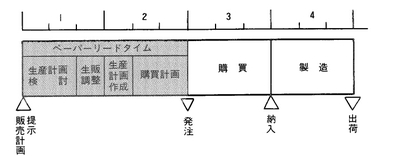
関連用語: リードタイム
展開手法
単に"部品展開"と称した場合は、いろいろな解釈ができる。このため、その場での使い方によって、その意味はかなり異なってくる。一般的にいって、この言い方は生産管理システムの部品や材料の所要量計算を指すことが多い。特に、サマリー部品表を用いての所要量計算にはよく使われる。また、部品表の展開手法を指す場合には、次の3種類の展開手法の総称として用いることが多い。
● 一段階展開:直接1段階下位(子)か、あるいは上位(親)の品目を検索する。
● 多段階展開:下位または上位のすべての品目をレベル別に検索する。
● 集合展開:下位または上位のすべての品目を検索して、同一部品を1つに集約する。
また、展開の方向によっても、その方法は異なる。普通、上位品目から下位品目へ展開することを正展開といい、逆に下位品目から上位品目を展開することを逆展開という。このような展開を実行するには、ストラクチャ部品表が必要になる。またコンピュータシステムでは、部品表管理を一元化するためにデータベースが一般的に使われている。展開手法を参照。
関連用語: 部品表
単に"部品展開"と称した場合は、いろいろな解釈ができる。このため、その場での使い方によって、その意味はかなり異なってくる。一般的にいって、この言い方は生産管理システムの部品や材料の所要量計算を指すことが多い。特に、サマリー部品表を用いての所要量計算にはよく使われる。また、部品表の展開手法を指す場合には、次の3種類の展開手法の総称として用いることが多い。
● 一段階展開:直接1段階下位(子)か、あるいは上位(親)の品目を検索する。
● 多段階展開:下位または上位のすべての品目をレベル別に検索する。
● 集合展開:下位または上位のすべての品目を検索して、同一部品を1つに集約する。
また、展開の方向によっても、その方法は異なる。普通、上位品目から下位品目へ展開することを正展開といい、逆に下位品目から上位品目を展開することを逆展開という。このような展開を実行するには、ストラクチャ部品表が必要になる。またコンピュータシステムでは、部品表管理を一元化するためにデータベースが一般的に使われている。展開手法を参照。
関連用語: 部品表
Change Based on Date
設計変更の実施時期を日付で指定する方法である。即時に変更が必要な場合は、その日を変更実施日として指定する。また、材料や治工具が使えるようになるまでとか、旧部品の在庫を考慮するなどして、変更実施までにある程度の期間を必要とする場合は、設計変更が可能となるであろう日を推定している。
図は、部品bを83年11月10日まで使い、11月11日以降、部品dを使う例である。このような設計変更の開始(From)、終了(To)の情報は部品表の中の製品構成に設定される。MRPでは、算出された所要量の作業着手日と設定された設変情報とを見比べて、着手日の時期に該当する品目を選択する。日付による設変は、その考え方および対処が簡単なことから、設変方法として、最も多く採用されている。
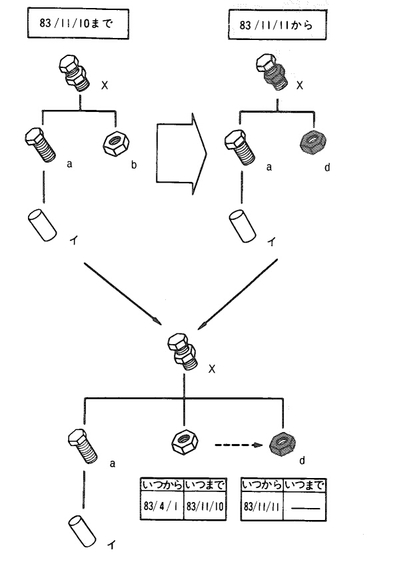
関連用語: 設計変更
設計変更の実施時期を日付で指定する方法である。即時に変更が必要な場合は、その日を変更実施日として指定する。また、材料や治工具が使えるようになるまでとか、旧部品の在庫を考慮するなどして、変更実施までにある程度の期間を必要とする場合は、設計変更が可能となるであろう日を推定している。
図は、部品bを83年11月10日まで使い、11月11日以降、部品dを使う例である。このような設計変更の開始(From)、終了(To)の情報は部品表の中の製品構成に設定される。MRPでは、算出された所要量の作業着手日と設定された設変情報とを見比べて、着手日の時期に該当する品目を選択する。日付による設変は、その考え方および対処が簡単なことから、設変方法として、最も多く採用されている。
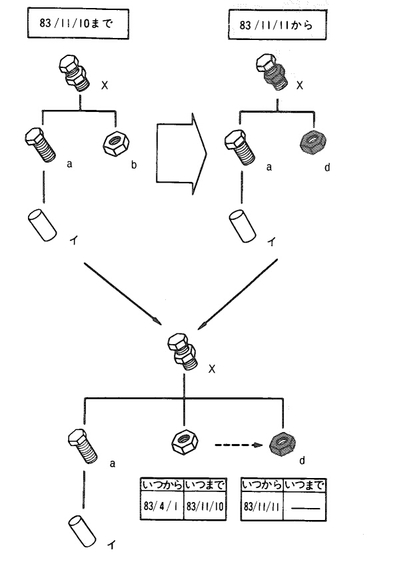
関連用語: 設計変更
図面の改訂によりつけられる一連の番号であり、これにより該当図面の改訂数および最新の図面状況などを管理する。
部品展開
部品表(B/M:Bill of Materials)を用いての展開手法は2つの面から捉えることができる。1つは展開形式からみた場合であり、他方は展開方向からの観点である。展開形式は、ストラクチャ部品表のレベルをどのように捉えて展開するかの違いにより、一段階展開、多段階展開、集合展開の3つに分けられる。一段階展開は当該品目の1段階上位(親)または下位(子)の品目を展開し、多段階展開は、多段階上位または下位の品目を展開する方法である。また、集合展開は上位または下位のすべての品目をローレベルコードの順に展開する。
一方、展開方向は、当該品目の下位方向、つまり子とか孫とかを検索する正展開と、反対の上位方向、たとえば親とかその上位とかを捜す逆展開とに分けられる。正展開は、当該品目の構成品が何かを示し、逆展開は、当該品目がどのような品目に使われているかを示している。
このような展開形式と展開方向の組合せにより、一般的には右に示す6種類の展開手法がある。部品展開を参照。

関連用語: 部品表
部品表(B/M:Bill of Materials)を用いての展開手法は2つの面から捉えることができる。1つは展開形式からみた場合であり、他方は展開方向からの観点である。展開形式は、ストラクチャ部品表のレベルをどのように捉えて展開するかの違いにより、一段階展開、多段階展開、集合展開の3つに分けられる。一段階展開は当該品目の1段階上位(親)または下位(子)の品目を展開し、多段階展開は、多段階上位または下位の品目を展開する方法である。また、集合展開は上位または下位のすべての品目をローレベルコードの順に展開する。
一方、展開方向は、当該品目の下位方向、つまり子とか孫とかを検索する正展開と、反対の上位方向、たとえば親とかその上位とかを捜す逆展開とに分けられる。正展開は、当該品目の構成品が何かを示し、逆展開は、当該品目がどのような品目に使われているかを示している。
このような展開形式と展開方向の組合せにより、一般的には右に示す6種類の展開手法がある。部品展開を参照。

関連用語: 部品表
Check Digit
あらかじめ定められたコードを基に何らかの作業を行う場合、そのコードが正しいか否かを判別するための検査数字である。これはコードの各桁の数字を加工してチェックディジットを定め、これをコードに付加して1つのコードとして用いる。たとえば、コードが、"3152"のチェックディジットをモジュラス11の方法で求めるには、右のように計算する。このように"3152"というコードはチェックディジット6が付加されて"31526"が正式のコードとなる。MRPシステムの中で、コンピュータ処理のキーとなる項目、たとえば品目番号などは、誤った処理を避けるためにも、チェックディジット付きのコードにし、その入力時にコードチェックをする必要がある。
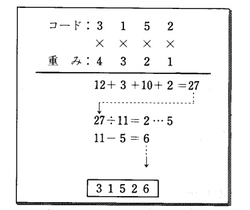
あらかじめ定められたコードを基に何らかの作業を行う場合、そのコードが正しいか否かを判別するための検査数字である。これはコードの各桁の数字を加工してチェックディジットを定め、これをコードに付加して1つのコードとして用いる。たとえば、コードが、"3152"のチェックディジットをモジュラス11の方法で求めるには、右のように計算する。このように"3152"というコードはチェックディジット6が付加されて"31526"が正式のコードとなる。MRPシステムの中で、コンピュータ処理のキーとなる項目、たとえば品目番号などは、誤った処理を避けるためにも、チェックディジット付きのコードにし、その入力時にコードチェックをする必要がある。
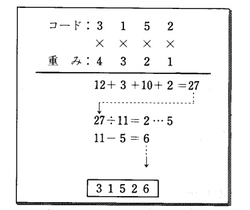
Unit Cost
購買品では購入価格を指し、外注品では、外注加工費を示す。単価情報は、"何の品物を、どこの業者で購入するといくらである"といったように品目と業者との関連で決まるデータである。一般的には、発注量や発注時期によっても単価が変わるため、量や時期を分けて単価を設定している。
関連用語: 技術データ
購買品では購入価格を指し、外注品では、外注加工費を示す。単価情報は、"何の品物を、どこの業者で購入するといくらである"といったように品目と業者との関連で決まるデータである。一般的には、発注量や発注時期によっても単価が変わるため、量や時期を分けて単価を設定している。
関連用語: 技術データ
Indented Bill of Materials
多段階正部品表と多段階逆部品表とがあり、一般に"多段階部品表"といった場合は、多段階正部品表を指す。また、多段階逆部品表は多段階逆展開部品表とか多段階逆展開表などといわれる。 次に多段階部品表の例を示す。
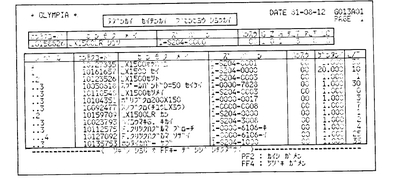
関連用語: 部品表
多段階正部品表と多段階逆部品表とがあり、一般に"多段階部品表"といった場合は、多段階正部品表を指す。また、多段階逆部品表は多段階逆展開部品表とか多段階逆展開表などといわれる。 次に多段階部品表の例を示す。
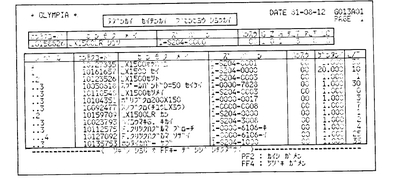
関連用語: 部品表
Indented Bill of Materials
多段階部品表ともいわれ、指定された品目の下位品目を、その構成に従ってレベル別に表示した部品表であり、類似品の設計、生産改善や製品原価の検討、製品の製造計画などに用いられる。図の例では、品目Xを指定した場合に、子品目のaがまず表示され、次に品目aの子品目イが表示される。このように多段階正部品表では、指定された品目の構成に従ってレベル別に各品目を表示する。 この部品表を作成するには、多段階展開の手法が使われ、ストラクチャ構造の部品表を上(製品)から下(材料)へ向けて、1段1段検索していく。部品表の表示には、通常レベルの番号が表示される。
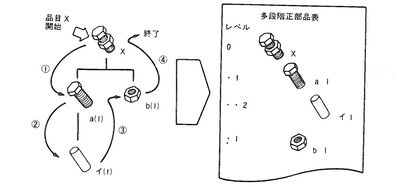
関連用語: 部品表
反意語: 多段階逆部品表
多段階部品表ともいわれ、指定された品目の下位品目を、その構成に従ってレベル別に表示した部品表であり、類似品の設計、生産改善や製品原価の検討、製品の製造計画などに用いられる。図の例では、品目Xを指定した場合に、子品目のaがまず表示され、次に品目aの子品目イが表示される。このように多段階正部品表では、指定された品目の構成に従ってレベル別に各品目を表示する。 この部品表を作成するには、多段階展開の手法が使われ、ストラクチャ構造の部品表を上(製品)から下(材料)へ向けて、1段1段検索していく。部品表の表示には、通常レベルの番号が表示される。
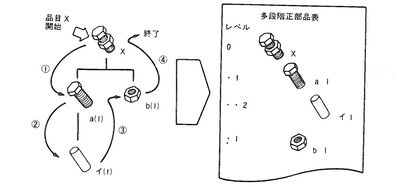
関連用語: 部品表
反意語: 多段階逆部品表
Indented Where-used Bill of Materials
多段階逆展開部品表ともいわれ、指定された品目の上位品目を、その構成に従ってレベル別に表示した部品表であり、部品の標準化、設変、原価変更による製品影響度および欠品の影響検討などに用いられる。図の例では、品目イを指定した場合にその親品目aがまず表示され、続いて品目aの親品目Xが表示される。また品目イは共通に使われているため、品目cも同様に表示される。 多段階逆部品表を作成するには、展開手法の中の多段階逆展開が使われる。この手法では、主に上位品目を捜し出すための親捜しの関連を中心に使い、ストラクチャ構造の部品表を下(材料)から上(製品)へ向けて、1段1段検索していく。多段階部品表は、正・逆部品表ともレベル表示をするのが普通である。逆部品表では、このレベル0に表示された品目が展開依頼品目で、最大レベル(図の例ではレベル2)に表示された品目が製品である。
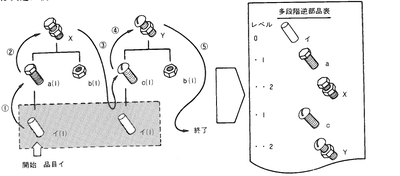
関連用語: 部品表
反意語:多段階正部品表
多段階逆展開部品表ともいわれ、指定された品目の上位品目を、その構成に従ってレベル別に表示した部品表であり、部品の標準化、設変、原価変更による製品影響度および欠品の影響検討などに用いられる。図の例では、品目イを指定した場合にその親品目aがまず表示され、続いて品目aの親品目Xが表示される。また品目イは共通に使われているため、品目cも同様に表示される。 多段階逆部品表を作成するには、展開手法の中の多段階逆展開が使われる。この手法では、主に上位品目を捜し出すための親捜しの関連を中心に使い、ストラクチャ構造の部品表を下(材料)から上(製品)へ向けて、1段1段検索していく。多段階部品表は、正・逆部品表ともレベル表示をするのが普通である。逆部品表では、このレベル0に表示された品目が展開依頼品目で、最大レベル(図の例ではレベル2)に表示された品目が製品である。
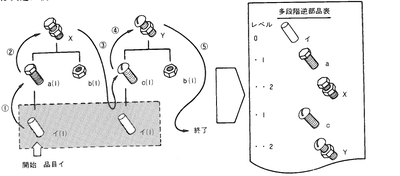
関連用語: 部品表
反意語:多段階正部品表
Engineering Change Number
設計変更は各部門から数多く発生する。これら1つひとつの設計変更に対し、ユニークな番号を付与することで他の設計変更と区別し、設計変更の影響把握や設計変更の通知といった一連の設計変更管理が円滑に行えるようになる。設計変更に対してつけられたこのユニークな番号を設計変更番号、略して設変番号という。
関連用語: 設計変更
設計変更は各部門から数多く発生する。これら1つひとつの設計変更に対し、ユニークな番号を付与することで他の設計変更と区別し、設計変更の影響把握や設計変更の通知といった一連の設計変更管理が円滑に行えるようになる。設計変更に対してつけられたこのユニークな番号を設計変更番号、略して設変番号という。
関連用語: 設計変更
Engineering Change 設変
一般に設計変更は、略して設変("せっぺん"もしくは"せつへん")と呼ばれたり、Engineering Changeを略して"EC"などと呼ばれている。
設計変更の理由には、次のようなことが考えられる。
● 製品改良:VE活動などにより、原価を低減するために機能の見直しや材料の変更などが行われる。
● 技術改善:製造手順の改善や設備の改良などで、従来設定されていた品目が不要になることもある。
● 安全性への対処:製品に何らかの欠陥が発生し、安全性への対処として変更される。これは通常、すぐに変更が行われる。
● 部品表の誤り修正:登録された部品表には、設計の誤りや、入力ミスもあり、ただちに修正する必要がある。 変更内容には、材質とか原価のように、品目そのものの内容を変更する場合と原単位のような製品構成の変更とに大きく分けられる。変更は、設計部門を中心として、生産技術や購買部門などの要求により発生し、その影響把握と変更時期を決めるために、設計変更会議が開かれる。設計や生産技術部門は、部品の変更がどのような製品に影響するかを調べ、その範囲を明確にしておく、また、購買や製造部門は、注残や在庫の状況を把握し、最少の費用で変更できるよう、その時期を決定する。変更の時期は、一般に次の4つの方法により実施されている。
● 即時変更:欠陥部品の変更など安全性にかかわる時には、即時に変更が行われる。
● 在庫消化後:現在もっている在庫を使い切った後に変更実施を行う方法。
● 日付指定:変更時期を日付により指定する方法。これは通常、"いつから(開始)"、"いつまで(終了)"というように品目の有効期間を示す場合が多い。
● 一連番号指定:"何番から(開始)"、"何番まで(終了)"というように、製品の一連番号を指定することで、有効となる製品の号機範囲を示す方法。
設計変更の実施に際し、各部門の確認と連携を保つために、図のような設計変更通知表が配布される。
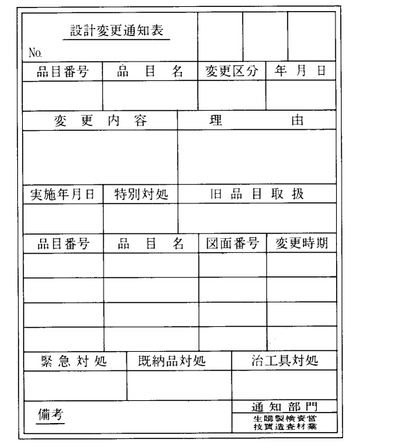
一般に設計変更は、略して設変("せっぺん"もしくは"せつへん")と呼ばれたり、Engineering Changeを略して"EC"などと呼ばれている。
設計変更の理由には、次のようなことが考えられる。
● 製品改良:VE活動などにより、原価を低減するために機能の見直しや材料の変更などが行われる。
● 技術改善:製造手順の改善や設備の改良などで、従来設定されていた品目が不要になることもある。
● 安全性への対処:製品に何らかの欠陥が発生し、安全性への対処として変更される。これは通常、すぐに変更が行われる。
● 部品表の誤り修正:登録された部品表には、設計の誤りや、入力ミスもあり、ただちに修正する必要がある。 変更内容には、材質とか原価のように、品目そのものの内容を変更する場合と原単位のような製品構成の変更とに大きく分けられる。変更は、設計部門を中心として、生産技術や購買部門などの要求により発生し、その影響把握と変更時期を決めるために、設計変更会議が開かれる。設計や生産技術部門は、部品の変更がどのような製品に影響するかを調べ、その範囲を明確にしておく、また、購買や製造部門は、注残や在庫の状況を把握し、最少の費用で変更できるよう、その時期を決定する。変更の時期は、一般に次の4つの方法により実施されている。
● 即時変更:欠陥部品の変更など安全性にかかわる時には、即時に変更が行われる。
● 在庫消化後:現在もっている在庫を使い切った後に変更実施を行う方法。
● 日付指定:変更時期を日付により指定する方法。これは通常、"いつから(開始)"、"いつまで(終了)"というように品目の有効期間を示す場合が多い。
● 一連番号指定:"何番から(開始)"、"何番まで(終了)"というように、製品の一連番号を指定することで、有効となる製品の号機範囲を示す方法。
設計変更の実施に際し、各部門の確認と連携を保つために、図のような設計変更通知表が配布される。
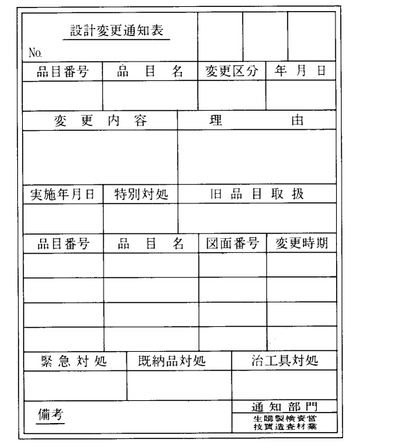
Engineering Bill of Materials
部品表は通常、まず設計部門が機能設計を行い、次いで生産部門が生産設計を行ってつくられる。設計部門がつくる部品表を設計部品表という。設計部品表は機能や品質が基本となっており、実際にものをつくる際の加工方法や加工手順などはあまり考慮されないのが普通である。しかし、近年、設計に対する考え方は拡大している。生産や品質の安定化を図る一方で、顧客ニーズを的確に捉え、製品の企画を支援するといった、いわば生産全体の効率化の要となっている。また、顧客ニーズの多様化と短納期への対応から、大量生産のような生産設計重視型の考え方は次第に少なくなってきている。このことから、敏捷でかつ小回りのきくように、機能設計と生産設計を一体化し、同一グループまたはプロジェクト形式での設計を考慮する必要がある。
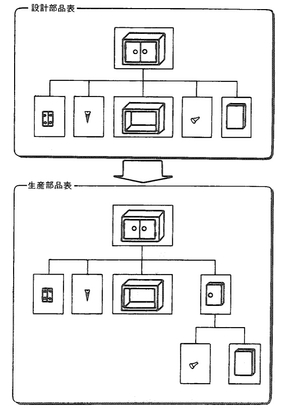
関連用語: 部品表
部品表は通常、まず設計部門が機能設計を行い、次いで生産部門が生産設計を行ってつくられる。設計部門がつくる部品表を設計部品表という。設計部品表は機能や品質が基本となっており、実際にものをつくる際の加工方法や加工手順などはあまり考慮されないのが普通である。しかし、近年、設計に対する考え方は拡大している。生産や品質の安定化を図る一方で、顧客ニーズを的確に捉え、製品の企画を支援するといった、いわば生産全体の効率化の要となっている。また、顧客ニーズの多様化と短納期への対応から、大量生産のような生産設計重視型の考え方は次第に少なくなってきている。このことから、敏捷でかつ小回りのきくように、機能設計と生産設計を一体化し、同一グループまたはプロジェクト形式での設計を考慮する必要がある。
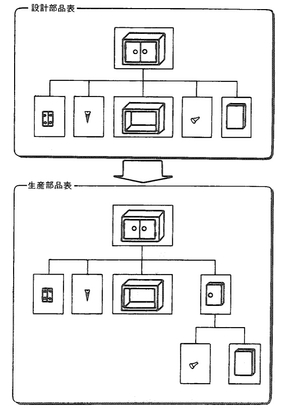
関連用語: 部品表
Manufacturing Lead Time
製品、組立品、部品などを、それぞれ一段下位の品目から製造するために、製造オーダーが発行されてから完成するまでの期間をいう。その構成要素は、品目を製造するために必要な各工程での時間、つまり工程リードタイムと各工程間の運搬時間である。これは、MRPの中で内作品についてのリードタイム計算に用いられる。
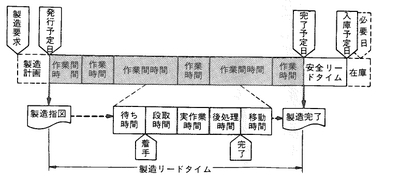
関連用語: リードタイム
製品、組立品、部品などを、それぞれ一段下位の品目から製造するために、製造オーダーが発行されてから完成するまでの期間をいう。その構成要素は、品目を製造するために必要な各工程での時間、つまり工程リードタイムと各工程間の運搬時間である。これは、MRPの中で内作品についてのリードタイム計算に用いられる。
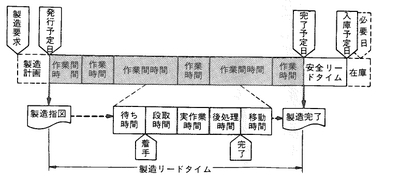
関連用語: リードタイム
Production Bill of Materials
部品表は、通常まず設計部門が機能設計を行い、次いで生産部門が生産設計を行ってつくられる。設計部門でつくられた設計部品表を基に、生産部門がつくる部品表を生産部品表という。ここでは、実際にものをつくる際の詳細な加工方法や手順、経済性などが基本となる。したがって、設計部品表にない品目を追加したり、生産に不要な品目を除いたりする作業が行われる。従来の少品種多量生産においては、このような部品表のつくり方が中心であったが、多品種少量生産、短納期生産が要求される今日の企業においては、設計部門で機能設計および生産設計を行い、生産部品表までつくり上げてしまうことが求められている。
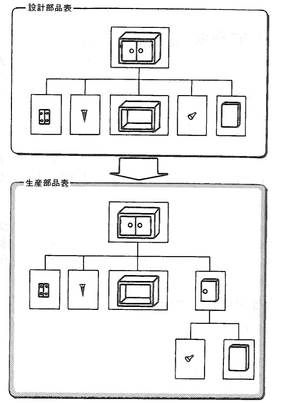
関連用語: 部品表
部品表は、通常まず設計部門が機能設計を行い、次いで生産部門が生産設計を行ってつくられる。設計部門でつくられた設計部品表を基に、生産部門がつくる部品表を生産部品表という。ここでは、実際にものをつくる際の詳細な加工方法や手順、経済性などが基本となる。したがって、設計部品表にない品目を追加したり、生産に不要な品目を除いたりする作業が行われる。従来の少品種多量生産においては、このような部品表のつくり方が中心であったが、多品種少量生産、短納期生産が要求される今日の企業においては、設計部門で機能設計および生産設計を行い、生産部品表までつくり上げてしまうことが求められている。
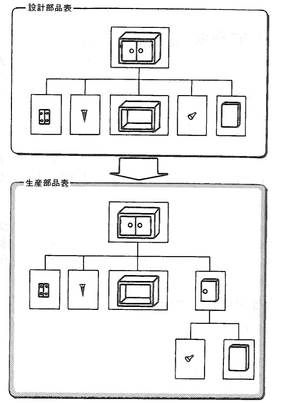
関連用語: 部品表
Spare Bill of Materials
通常は製品に組み込まれる部品であっても、それがスペア部品(サービス部品)としても使用されることを考慮して作成された部品表である。ある製品の一部が壊れ、顧客からスペア部品の要求が発生した場合には、通常、顧客が要求したその部品だけでなく、それに付帯する他の部品まで要求する場合が多い。このような時、顧客に供給される部品は、それらすべてが必要となり、しかもスペア部品に組み込まれて供給されるのではなく、それぞれ単体で出荷されることになる。このような要件を考慮してスペア部品が設定されている部品表をスペア部品表という。
関連用語: 部品表
通常は製品に組み込まれる部品であっても、それがスペア部品(サービス部品)としても使用されることを考慮して作成された部品表である。ある製品の一部が壊れ、顧客からスペア部品の要求が発生した場合には、通常、顧客が要求したその部品だけでなく、それに付帯する他の部品まで要求する場合が多い。このような時、顧客に供給される部品は、それらすべてが必要となり、しかもスペア部品に組み込まれて供給されるのではなく、それぞれ単体で出荷されることになる。このような要件を考慮してスペア部品が設定されている部品表をスペア部品表という。
関連用語: 部品表
Drawing
図面を製造過程から捉えると2つに分けられる。1つは、製品の組立に必要な組立図または略して組図と呼ばれるもので、もう1つは、部品の加工方法を中心に説明されている加工図または工作図である。いずれにせよ、これらの図面には、誰もが組立や加工が可能なように、製造に必要な項目がすべて記入されている必要がある。このようにして作成された図面は、生産管理システムの核である部品表の基礎として使われる。
生産管理の情報システム面で、"図面"という場合は、技術データとしての図面マスターを指す。図面マスターには、図面番号、版数、関連品目番号、設計変更番号などが記録されており、作業指示を行う際の出図指示などに用いる。
関連用語: 技術データ
図面を製造過程から捉えると2つに分けられる。1つは、製品の組立に必要な組立図または略して組図と呼ばれるもので、もう1つは、部品の加工方法を中心に説明されている加工図または工作図である。いずれにせよ、これらの図面には、誰もが組立や加工が可能なように、製造に必要な項目がすべて記入されている必要がある。このようにして作成された図面は、生産管理システムの核である部品表の基礎として使われる。
生産管理の情報システム面で、"図面"という場合は、技術データとしての図面マスターを指す。図面マスターには、図面番号、版数、関連品目番号、設計変更番号などが記録されており、作業指示を行う際の出図指示などに用いる。
関連用語: 技術データ
Product Structure B/M
部品の加工や製品の組立順序を意識して、親品目と子品目の関連を保ちながら、製品の構成を表現した部品表である。たとえば、図のサマリー部品表で示されている製品Zのストラクチャ部品表は、親品目と子品目、さらに子品目と孫品目といった形で製品の構成を示すように関連付けられる。このようなストラクチャ部品表は、設計変更の影響把握や品目別原価計算、それに購入品や内作品の所要量計算などに使われる。
この部品表は、サマリー部品表に比べ、その創成段階では製品の構成を意識してつくらねばならないが、MRPや設計変更、それに原価管理などほとんどの生産業務に役立つばかりでなく、部品表の一元管理が可能となる。現在、部品表をコンピュータ化する場合、一般的にはDBMS(Data Base Management System)やB/M(Bill of Materials)プロセッサと呼ばれる管理システムが、ストラクチャ部品表の維持・管理を行う。この場合、品目と製品構成という2つのマスターでもって運用され、一段階、多段階および集合の各部品表を表示することができる。

関連用語: 部品表
反意語: サマリー部品表
部品の加工や製品の組立順序を意識して、親品目と子品目の関連を保ちながら、製品の構成を表現した部品表である。たとえば、図のサマリー部品表で示されている製品Zのストラクチャ部品表は、親品目と子品目、さらに子品目と孫品目といった形で製品の構成を示すように関連付けられる。このようなストラクチャ部品表は、設計変更の影響把握や品目別原価計算、それに購入品や内作品の所要量計算などに使われる。
この部品表は、サマリー部品表に比べ、その創成段階では製品の構成を意識してつくらねばならないが、MRPや設計変更、それに原価管理などほとんどの生産業務に役立つばかりでなく、部品表の一元管理が可能となる。現在、部品表をコンピュータ化する場合、一般的にはDBMS(Data Base Management System)やB/M(Bill of Materials)プロセッサと呼ばれる管理システムが、ストラクチャ部品表の維持・管理を行う。この場合、品目と製品構成という2つのマスターでもって運用され、一段階、多段階および集合の各部品表を表示することができる。

関連用語: 部品表
反意語: サマリー部品表
Summarized Bill of Materials
集合正部品表と集合逆部品表とがあり、一般に"集合部品表"といった場合は、集合正部品表を指す。また、集合逆部品表は"集合逆展開表"などといわれることもある。
関連用語: 部品表
集合正部品表と集合逆部品表とがあり、一般に"集合部品表"といった場合は、集合正部品表を指す。また、集合逆部品表は"集合逆展開表"などといわれることもある。
関連用語: 部品表
Summarized Explosion
指定された品目の下位品目を、レベル・バイ・レベル(ローレベルコードに従って)上から下に順々に展開することで、集合正部品表の作成やMRPの展開ロジックとして使われる。図の例では、品目Zの展開を要求した場合、まず品目Zのデータが検索され、次に、子捜しを使って製品構成Z-Xを参照して(①)、親捜しにより子品目Xが参照され(②)、所要量が作成される。次に、製品構成Z-bを参照し(③)、その子品目であるbが参照され(④)、bの所要量がつくられる。
次は、1レベル目の所要量の抽出である。品目Xのローレベルコードは1レベルであるため所要量が抽出され、子品目a、bに展開されて、その各々の所要量がつくられる。しかし、1レベル目の品目bのローレベルコードはレベル2のため、この段階では抽出されない。このようにして1レベル目の展開と抽出は終わり、次に2レベル目の所要量の抽出を行う。まず品目aの所要量が抽出され、下位品目の展開が行われ、その後、品目bの抽出が行われる。この時レベル1で展開された品目bの所要量とレベル2で展開された所要量とが一緒に抽出される。
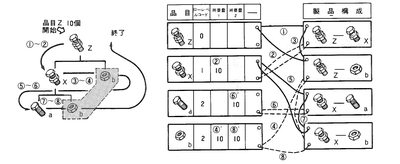
関連用語: 集合展開
反意語: 集合逆展開
指定された品目の下位品目を、レベル・バイ・レベル(ローレベルコードに従って)上から下に順々に展開することで、集合正部品表の作成やMRPの展開ロジックとして使われる。図の例では、品目Zの展開を要求した場合、まず品目Zのデータが検索され、次に、子捜しを使って製品構成Z-Xを参照して(①)、親捜しにより子品目Xが参照され(②)、所要量が作成される。次に、製品構成Z-bを参照し(③)、その子品目であるbが参照され(④)、bの所要量がつくられる。
次は、1レベル目の所要量の抽出である。品目Xのローレベルコードは1レベルであるため所要量が抽出され、子品目a、bに展開されて、その各々の所要量がつくられる。しかし、1レベル目の品目bのローレベルコードはレベル2のため、この段階では抽出されない。このようにして1レベル目の展開と抽出は終わり、次に2レベル目の所要量の抽出を行う。まず品目aの所要量が抽出され、下位品目の展開が行われ、その後、品目bの抽出が行われる。この時レベル1で展開された品目bの所要量とレベル2で展開された所要量とが一緒に抽出される。
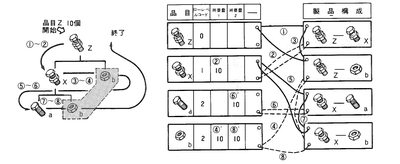
関連用語: 集合展開
反意語: 集合逆展開
Product Summary B/M
サマリー部品表の意味は大きく2通りに分けられる。1つは、パーツリストとしての集合部品表を示す場合と、他方B/M(Bill of Materials)としてのデータを集約した部品表そのものを指す場合がある。"サマリー部品表"とか"サマリー型の部品表"とかいう時は、一般に後者を指す場合が多く、それは部品の加工や製品の組立順序にとらわれず、ある品目をつくる時に必要となる部品や原材料を一覧表の形でまとめた部品表である。これに対して、部品の加工や組立順序を考慮した部品表をストラクチャ部品表という。たとえば、図で示すように、本来製品Zは、組立品Xと部品bから成り、組立品Xは部品aとbから成るのであるが、サマリー部品表では、これらのレベルを無視して製品Zの基に部品や原材料を集約してもつ。これは、ストラクチャ部品表の簡便的方法で、原価計算や購入手配などに用いられる。
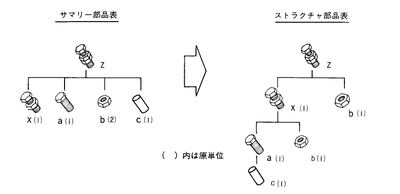
関連用語: 部品表、集合部品表
反意語: ストラクチャ部品表
サマリー部品表の意味は大きく2通りに分けられる。1つは、パーツリストとしての集合部品表を示す場合と、他方B/M(Bill of Materials)としてのデータを集約した部品表そのものを指す場合がある。"サマリー部品表"とか"サマリー型の部品表"とかいう時は、一般に後者を指す場合が多く、それは部品の加工や製品の組立順序にとらわれず、ある品目をつくる時に必要となる部品や原材料を一覧表の形でまとめた部品表である。これに対して、部品の加工や組立順序を考慮した部品表をストラクチャ部品表という。たとえば、図で示すように、本来製品Zは、組立品Xと部品bから成り、組立品Xは部品aとbから成るのであるが、サマリー部品表では、これらのレベルを無視して製品Zの基に部品や原材料を集約してもつ。これは、ストラクチャ部品表の簡便的方法で、原価計算や購入手配などに用いられる。
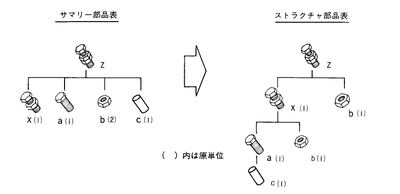
関連用語: 部品表、集合部品表
反意語: ストラクチャ部品表
Final Assembly Bill of Materials
顧客ニーズの多様化に合わせるために、オプションやバリアントが設定される。たとえば、ボルトとナットを組み合わせて1つの製品となる場合でも、ボルトやナットは1種類とは限らず、数種類用意することで顧客ニーズの多様化に対応しようとする。しかし、顧客の仕様に従って、そのつど製品をつくっていては、オプションの組合せによって、部品表は莫大な数となってしまい、管理は複雑で経済的にも得策でない。
計画部品表をつくる時に最終組立品目を選び出し、これを基に、オプションやバリアントを考慮してつくられる部品表を、最終組立部品表という。
関連用語: 部品表
顧客ニーズの多様化に合わせるために、オプションやバリアントが設定される。たとえば、ボルトとナットを組み合わせて1つの製品となる場合でも、ボルトやナットは1種類とは限らず、数種類用意することで顧客ニーズの多様化に対応しようとする。しかし、顧客の仕様に従って、そのつど製品をつくっていては、オプションの組合せによって、部品表は莫大な数となってしまい、管理は複雑で経済的にも得策でない。
計画部品表をつくる時に最終組立品目を選び出し、これを基に、オプションやバリアントを考慮してつくられる部品表を、最終組立部品表という。
関連用語: 部品表
Change Based on Quantity
安全性への対処のような緊急度が要求される設計変更以外は、通常、在庫を使い切った時点で変更が実施される。この方法を在庫消化による設変といい、普通、新品目を旧品目の子品目として登録し、旧品目の製品構成に在庫指定の設変であることを示す区分と変更を実施する在庫数とを指定して対処する。たとえば、図の場合、旧品目は部品bであり、その子品目として、新部品dが登録される。 MRPでは、部品bの所要量計画を行い、在庫引当の結果、在庫数が10個になった時期以降の計画は、部品dの所要量計画として行われる。新品目を旧品目の下位に位置付けた部品表は、実際の品目の構成とは違ったものである。これは、MRPシステムが在庫数で設計変更を行うための簡便法である。設計変更が実施されたなら、不要となった旧部品をはずして、本来の品目の構成にもどす必要がある。
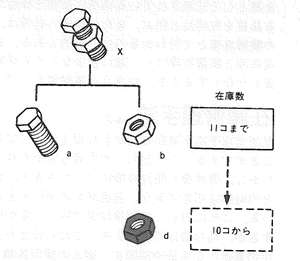
関連用語: 設計変更
安全性への対処のような緊急度が要求される設計変更以外は、通常、在庫を使い切った時点で変更が実施される。この方法を在庫消化による設変といい、普通、新品目を旧品目の子品目として登録し、旧品目の製品構成に在庫指定の設変であることを示す区分と変更を実施する在庫数とを指定して対処する。たとえば、図の場合、旧品目は部品bであり、その子品目として、新部品dが登録される。 MRPでは、部品bの所要量計画を行い、在庫引当の結果、在庫数が10個になった時期以降の計画は、部品dの所要量計画として行われる。新品目を旧品目の下位に位置付けた部品表は、実際の品目の構成とは違ったものである。これは、MRPシステムが在庫数で設計変更を行うための簡便法である。設計変更が実施されたなら、不要となった旧部品をはずして、本来の品目の構成にもどす必要がある。
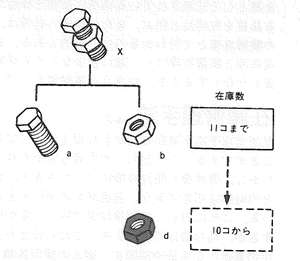
関連用語: 設計変更
部品表(B/M:Bill of Materials)は、2つのマスターデータから成る。1つは品目マスターで、もう1つは製品構成マスターである。この品目と製品構成だけでは、親品目と子品目の関連を示す部品表はつくれない。これら2つのマスターの関係付けが必要になる。通常、部品表をつくるには、品目と製品構成の間に、2つの関連付けが必要になる。1つは自分の子供、つまり下位品目を捜すための関係付けであり、他方は、自分の親である上位品目を捜すための関係付けである。一般に前者を子捜しと呼び、後者を親捜しという。
子捜しとは、ある品目がどのような構成品目で成り立っているのかを示すための品目と製品構成の関連付けのことである。図のような部品表では、製品Xの下位品目はaとbであり、子捜しとして品目Xと製品構成X-a、X-bが関係付けられる。また、品目aは製品構成a-イと結ばれる。このようにして、他の品目も自分の子供を捜すための関係付けがなされる。
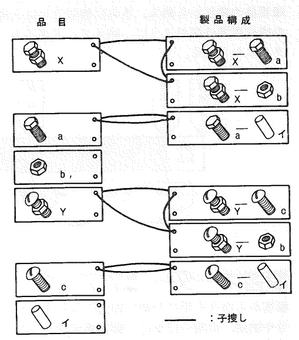
関連用語: 部品表、親捜し
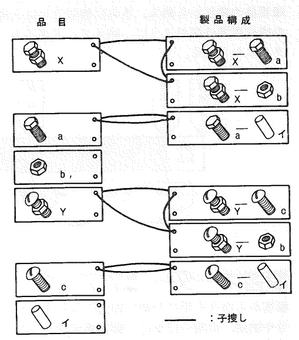
関連用語: 部品表、親捜し
Purchased Lead Time
購買品の発注から納入、さらに検収または入庫されるまでの時間のことである。その構成要素は図のように、納入リードタイム、受入リードタイムおよび検査リードタイムから成る。
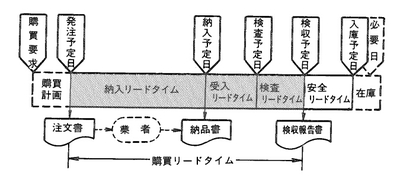
関連用語: リードタイム
購買品の発注から納入、さらに検収または入庫されるまでの時間のことである。その構成要素は図のように、納入リードタイム、受入リードタイムおよび検査リードタイムから成る。
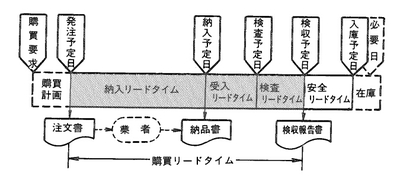
関連用語: リードタイム
一般に購買・外注という場合、業者と同じように購買品や外注品の購入先や外注先を指す場合が多い。生産管理の情報システム面において購買・外注とは、品目と業者の関連で決まる情報を1つにまとめたデータを指す。このデータ内容には、品目番号、業者番号、業者優先度、納入リードタイム、検査区分などがある。
関連用語: 技術データ
関連用語: 技術データ
Process Lead Time
工程において作業に着手し、その作業が完了するまでの時間をいい、一般的には、待ち時間、段取時間、実作業時間、後処理時間より構成される。
●待ち時間:作業が機械に割付けられるのを待っている時間。
●段取時間:機械が稼働できる状態にするための準備時間であり、オーダーの数量に関係なく発生する。
●実作業時間:実際に、その工程で作業を行う時間のことであり、オーダーの数量にほぼ比例して増大する。なお、実作業時間を求める計算式は、品目をある単位量製造する時に必要な単位時間とオーダー数量との関係で表わされる。
●後処理時間:作業の後処理(取りはずし、そうじなど)に必要な時間である。これは、次の作業の段取時間として捉える場合もある。
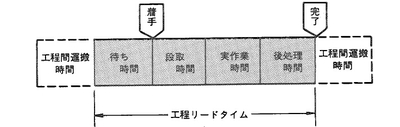
関連用語: 製造リードタイム
工程において作業に着手し、その作業が完了するまでの時間をいい、一般的には、待ち時間、段取時間、実作業時間、後処理時間より構成される。
●待ち時間:作業が機械に割付けられるのを待っている時間。
●段取時間:機械が稼働できる状態にするための準備時間であり、オーダーの数量に関係なく発生する。
●実作業時間:実際に、その工程で作業を行う時間のことであり、オーダーの数量にほぼ比例して増大する。なお、実作業時間を求める計算式は、品目をある単位量製造する時に必要な単位時間とオーダー数量との関係で表わされる。
実作業時間=(製造)オーダー数量/単位製造数量×単位作業時間
●後処理時間:作業の後処理(取りはずし、そうじなど)に必要な時間である。これは、次の作業の段取時間として捉える場合もある。
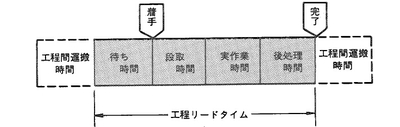
関連用語: 製造リードタイム
Inspection Lead Time
製造過程で行われる各種の検査に必要な時間や日数のことである。一般には、購買リードタイムや外注リードタイムの構成要素の1つであり、業者から納入され受付処理の済んだ購買品や外注品の受入検査に必要な時間である。ただし、すべての購入品、外注品に検査リードタイムが設定されるとは限らない。いわゆる"ノー検"と呼ばれる検査不要品は、検査リードタイムを考慮しなくてもよい。
関連用語: 購買リードタイム
製造過程で行われる各種の検査に必要な時間や日数のことである。一般には、購買リードタイムや外注リードタイムの構成要素の1つであり、業者から納入され受付処理の済んだ購買品や外注品の受入検査に必要な時間である。ただし、すべての購入品、外注品に検査リードタイムが設定されるとは限らない。いわゆる"ノー検"と呼ばれる検査不要品は、検査リードタイムを考慮しなくてもよい。
関連用語: 購買リードタイム
Combined Bill of Materials
部品表は一般的には、設計部門が機能設計を、次いで生産部門が生産設計を行ってつくられる。この時、それぞれの部門がつくる部品表は、設計部品表、生産部品表と呼ばれる。結合部品表とは、これら2つの部品表をまとめて、1つの部品表にしたもので、これにより一元的に部品表を管理することができる。この部品表には、それぞれの品目に、設計、生産、共通の区分がつけられ、区別できるように工夫されている。
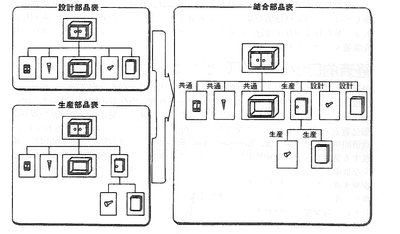
関連用語: 部品表
部品表は一般的には、設計部門が機能設計を、次いで生産部門が生産設計を行ってつくられる。この時、それぞれの部門がつくる部品表は、設計部品表、生産部品表と呼ばれる。結合部品表とは、これら2つの部品表をまとめて、1つの部品表にしたもので、これにより一元的に部品表を管理することができる。この部品表には、それぞれの品目に、設計、生産、共通の区分がつけられ、区別できるように工夫されている。
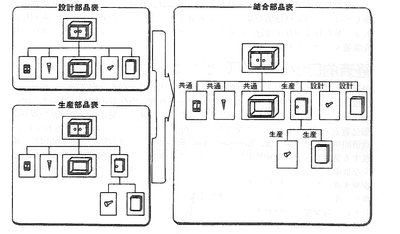
関連用語: 部品表
Planning Bill of Materials
需要予測や生産計画などにおいて、その計画をやりやすくするためにつくられる部品表である。図のように、扉やフレームなどが組み付けられて1つの製品となる場合、扉やフレームの種類が多いと、それに乗じて製品の種類はふくらみ、製品個々の計画を立てることは難しくなる。
このような場合には、扉やフレームをグループ化して、そのグループ単位で需要予測や生産計画を行うと便利である。したがって、この時、通常の部品表にはなかった計画のためだけの擬似的な品目(計画品目)が加えられたり、計画に不要なOP品目などが取り除かれたりする。このようにして、計画のためにつくられた部品表を計画部品表という。
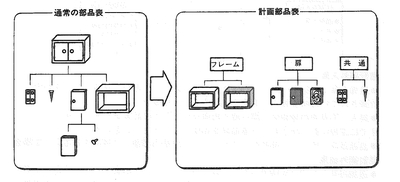
関連用語: 部品表
需要予測や生産計画などにおいて、その計画をやりやすくするためにつくられる部品表である。図のように、扉やフレームなどが組み付けられて1つの製品となる場合、扉やフレームの種類が多いと、それに乗じて製品の種類はふくらみ、製品個々の計画を立てることは難しくなる。
このような場合には、扉やフレームをグループ化して、そのグループ単位で需要予測や生産計画を行うと便利である。したがって、この時、通常の部品表にはなかった計画のためだけの擬似的な品目(計画品目)が加えられたり、計画に不要なOP品目などが取り除かれたりする。このようにして、計画のためにつくられた部品表を計画部品表という。
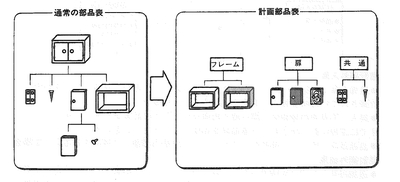
関連用語: 部品表
Supplier
購買品や外注品の購入先や外注先を示す。生産管理の情報システム面において業者という場合には、購入業者や外注業者に固有な情報を1つにまとめたデータを指す。このデータ内容には、業者番号、業者名称、住所、電話番号などが記録される。
関連用語: 技術データ
購買品や外注品の購入先や外注先を示す。生産管理の情報システム面において業者という場合には、購入業者や外注業者に固有な情報を1つにまとめたデータを指す。このデータ内容には、業者番号、業者名称、住所、電話番号などが記録される。
関連用語: 技術データ
Pseudo Bill of Materials
計画を行うために、設計や生産では実体として現われない擬似的な品目(擬似品目)を設定した部品表である。
擬似部品表の技法を用いた例として、次のような部品表がある。
● 計画部品表:予測や生産計画を容易に行うために、擬似品目(計画品目)が設定された部品表。
● ダミー部品表:同一の品目構成の管理とデータ量を減らすために、擬似品目(ダミー品目)が設定された部品表。
● キット部品表:小物部品をひとまとめにして取り扱うために、擬似品目(キット品目)が設定された部品表。
● オプション部品表:オプション部品をひとまとめにして取り扱うために、擬似品目(オプショングループ品目)が設定された部品表。
関連用語: 部品表
計画を行うために、設計や生産では実体として現われない擬似的な品目(擬似品目)を設定した部品表である。
擬似部品表の技法を用いた例として、次のような部品表がある。
● 計画部品表:予測や生産計画を容易に行うために、擬似品目(計画品目)が設定された部品表。
● ダミー部品表:同一の品目構成の管理とデータ量を減らすために、擬似品目(ダミー品目)が設定された部品表。
● キット部品表:小物部品をひとまとめにして取り扱うために、擬似品目(キット品目)が設定された部品表。
● オプション部品表:オプション部品をひとまとめにして取り扱うために、擬似品目(オプショングループ品目)が設定された部品表。
関連用語: 部品表
ある品目からみて、その品目がつくられる直接上位の品目のことをいう。専用品であれば、親品目は1つであるが、共通品の場合は、複数の親品目をもつことになる。たとえば、図のように素材イは共通品であり、その親品目は品目aとcになる。親品目を検索する場合は、子品目を指定して、一段階逆部品表を作成することで求められる。
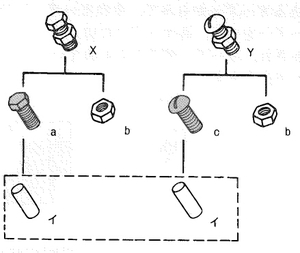
反意語: 子品目
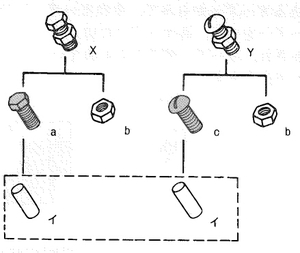
反意語: 子品目
Where-used Chain
通常、部品表をつくるには、品目と製品構成の間に、2つの関連付けが必要になる。1つは、自分の子供つまり下位品目を捜すための関係付けであり、他方は、自分の親である上位品目を捜すための関係付けである。前者は子捜しと呼び、後者を親捜しという。
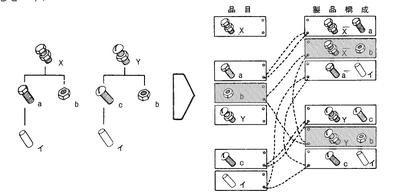
親捜しとは、ある品目がどのような上位品目に使われているかを示すための品目と製品構成の関連付けのことである。図のような品目の構成では、購入部品bは、製品XとYとに使われる。つまり親捜しは品目bと製品構成X-b、Y-bとが関係付けられる。同じように素材イや加工品aやcに対しても、自分の親を捜すための関係付けがなされる。
関連用語: 部品表、子捜し
通常、部品表をつくるには、品目と製品構成の間に、2つの関連付けが必要になる。1つは、自分の子供つまり下位品目を捜すための関係付けであり、他方は、自分の親である上位品目を捜すための関係付けである。前者は子捜しと呼び、後者を親捜しという。
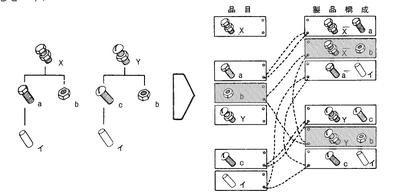
親捜しとは、ある品目がどのような上位品目に使われているかを示すための品目と製品構成の関連付けのことである。図のような品目の構成では、購入部品bは、製品XとYとに使われる。つまり親捜しは品目bと製品構成X-b、Y-bとが関係付けられる。同じように素材イや加工品aやcに対しても、自分の親を捜すための関係付けがなされる。
関連用語: 部品表、子捜し
Option Interrelationship Item
複数のオプション選択が行われる製品において、2つ以上のオプション部品の組み合せによって所要が決まる品目のことである。
関連用語: オプション
複数のオプション選択が行われる製品において、2つ以上のオプション部品の組み合せによって所要が決まる品目のことである。
関連用語: オプション
Option
製品の仕様を決定する際に顧客の機能選択が可能なようにするための概念であり、最終製品を決定する時、顧客が最終製品に組み込まれる製品や部品を指定するものである。ここで組み込まれる製品や部品は、個々に同一の特性をもったグループの中から選択される。
この概念を用いることで製品の多様化に対処することが可能になる。また、オプションに類似した概念に派系がある。オプションは、その選択が顧客にとって任意であるのに対し、派系では、その選択は必ず行われなければならない。
たとえば、自動車の場合、カーステレオはオプションであり、とくに顧客が不要と思えば選択する必要はないが、タイヤに関して選択が可能な場合、それはノーマルタイヤやラジアルタイヤのいずれにしろ選択が必須となる。このようなものは一般に派系という。
関連用語: 派系
製品の仕様を決定する際に顧客の機能選択が可能なようにするための概念であり、最終製品を決定する時、顧客が最終製品に組み込まれる製品や部品を指定するものである。ここで組み込まれる製品や部品は、個々に同一の特性をもったグループの中から選択される。
この概念を用いることで製品の多様化に対処することが可能になる。また、オプションに類似した概念に派系がある。オプションは、その選択が顧客にとって任意であるのに対し、派系では、その選択は必ず行われなければならない。
たとえば、自動車の場合、カーステレオはオプションであり、とくに顧客が不要と思えば選択する必要はないが、タイヤに関して選択が可能な場合、それはノーマルタイヤやラジアルタイヤのいずれにしろ選択が必須となる。このようなものは一般に派系という。
関連用語: 派系
General Inventory Goods
製品をつくるうえで、次の理由により、自然と在庫がたまってしまう品目を指す。これは、生産方式上、やむなくたまる在庫品で、経営からみて本質的になくてもよい在庫である。このことから、一般在庫品を消極的在庫品などともいう。
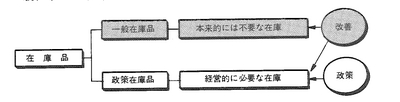
関連用語: 在庫品
製品をつくるうえで、次の理由により、自然と在庫がたまってしまう品目を指す。これは、生産方式上、やむなくたまる在庫品で、経営からみて本質的になくてもよい在庫である。このことから、一般在庫品を消極的在庫品などともいう。
● 能力のアンバランスによる在庫:前工程の能力が大きく、後工程の能力が小さい場合、水があふれるがごとく、自然と在庫ができてしまう。この一般在庫品に対し、経営上、積極的に在庫する品目を政策在庫と呼ぶ。
● 段取替えをいやがる在庫:段取にかなりの時間を費やすため、大ロットでしか作業をしない場合、その時に必要でないものまで、まとめてつくってしまい、これが在庫となる。
● 引当が忘れられている在庫:在庫の把握が適切でなかったり、また本来非在庫品なのだが在庫ができてしまい、計画作成時に引当の対象からはずされているような場合。
● 月末集中生産による在庫:月別の生産計画を立て、そのままの形で現場に指図している場合によく起こる。組立工程では、月の後半5日間くらいで追込み生産をする。このため、月の中旬から下旬にかけて、工場には組立部品が所狭しと在庫されている。
● 基準値の見直しを忘れている在庫:発注や製造の計画をする時に使用するリードタイムやロットの数量、それに不良率などの基準値を1度設定したままで、見直しを忘れている場合。このような時、ものが早く入ってきたり、また多くの不良を見込んで余分につくってしまい、在庫となってしまう。
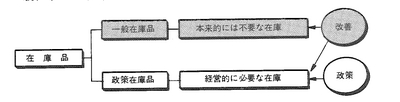
関連用語: 在庫品
Change Based on Serial Number
設計変更での旧品目と新品目の切替えを製品の製造番号、いわゆる製番や号機を指定して行う方法である。たとえば、図のような製品Xがあり、その子品目である部品aの設変を考えてみる。部品aの所要量はいま15個であるが、その内訳は製番X01から10個、X02から5個要求されている。仮に製番X02から部品aの代わりに部品eを使うとすれば、部品aの所要量は10個とし、部品eの所要量を5個とする必要がある。
このように、一連番号による設変では、各品目の所要量が、どの製番から要求されたものかを示す内訳が必要となる。これは一般に所要量結合といわれ、各品目の所要量の源泉を示すものである。しかし、このような所要量結合は、莫大なデータ量になり、小型コンピュータやオフィスコンピュータではこれを維持することは能力的に難しい。
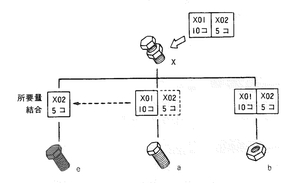
関連用語: 設計変更
設計変更での旧品目と新品目の切替えを製品の製造番号、いわゆる製番や号機を指定して行う方法である。たとえば、図のような製品Xがあり、その子品目である部品aの設変を考えてみる。部品aの所要量はいま15個であるが、その内訳は製番X01から10個、X02から5個要求されている。仮に製番X02から部品aの代わりに部品eを使うとすれば、部品aの所要量は10個とし、部品eの所要量を5個とする必要がある。
このように、一連番号による設変では、各品目の所要量が、どの製番から要求されたものかを示す内訳が必要となる。これは一般に所要量結合といわれ、各品目の所要量の源泉を示すものである。しかし、このような所要量結合は、莫大なデータ量になり、小型コンピュータやオフィスコンピュータではこれを維持することは能力的に難しい。
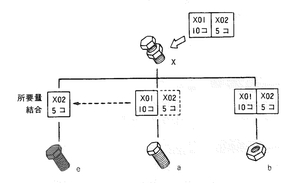
関連用語: 設計変更
Single Level Bill of Materials
指定された品目の直接一段階下位(子)の品目を表示した部品表であり、組立指示や支給品出庫、部品出庫に用いられる。図の例では、品目Xを指定した場合に、その子品目aとbの情報が表示される。また仮に、品目aが指定された時は、その子品目イが表示される。
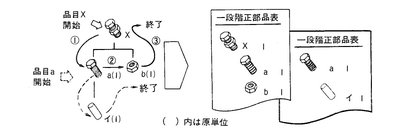
関連用語: 一段階部品表
指定された品目の直接一段階下位(子)の品目を表示した部品表であり、組立指示や支給品出庫、部品出庫に用いられる。図の例では、品目Xを指定した場合に、その子品目aとbの情報が表示される。また仮に、品目aが指定された時は、その子品目イが表示される。
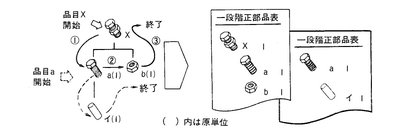
関連用語: 一段階部品表
Single Level Explosion
指定された品目の直接一段階下位(子)の品目を展開することで、一段階正部品表を作成する時に使う展開手法である。図の例では、品目Xの展開を要求した場合、まず品目Xのデータが検索され、次に子捜しにより製品構成X-aを展開(①)して、親捜しにより子品目aが参照(②)される。次に製品構成X-bから同様にして子品目bが参照される。
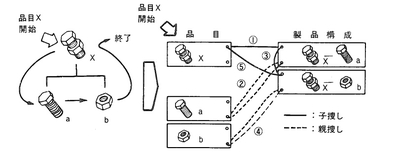
関連用語: 一段階展開
指定された品目の直接一段階下位(子)の品目を展開することで、一段階正部品表を作成する時に使う展開手法である。図の例では、品目Xの展開を要求した場合、まず品目Xのデータが検索され、次に子捜しにより製品構成X-aを展開(①)して、親捜しにより子品目aが参照(②)される。次に製品構成X-bから同様にして子品目bが参照される。
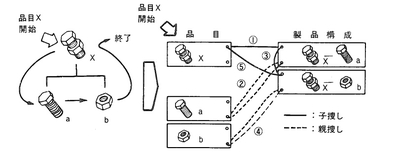
関連用語: 一段階展開
Single Level Explosion
一段階展開は、シングルレベル展開とか単一レベル展開などと呼ばれ、ある品目の一段下位の品目か、もしくは一段上位の品目を展開することをいう。これには、一段階正展開と一段階逆展開とがあり、前者は一段下位(子)品目を検索し、後者は一段上位(親)品目を検索する。一般に、"一段階展開"といった場合は、一段階正展開を指す。
関連用語: 展開手法
一段階展開は、シングルレベル展開とか単一レベル展開などと呼ばれ、ある品目の一段下位の品目か、もしくは一段上位の品目を展開することをいう。これには、一段階正展開と一段階逆展開とがあり、前者は一段下位(子)品目を検索し、後者は一段上位(親)品目を検索する。一般に、"一段階展開"といった場合は、一段階正展開を指す。
関連用語: 展開手法
Single Level Implosion
指定された品目の直接一段階上位(親)の品目を展開することで、一段階逆部品表を作成する時に使う展開手法である。
図の例では、品目bの逆展開を要求した場合、まず品目bのデータが検索され、次に親捜しを使って製品構成X-bを参照(①)して、子捜しにより親品目Xが展開(②)される。次に製品構成Y-bから同様にして親品目Yが展開される。
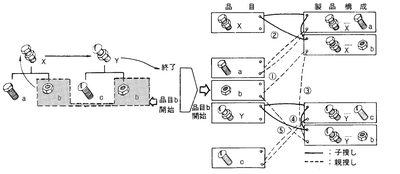
関連用語: 一段階展開
指定された品目の直接一段階上位(親)の品目を展開することで、一段階逆部品表を作成する時に使う展開手法である。
図の例では、品目bの逆展開を要求した場合、まず品目bのデータが検索され、次に親捜しを使って製品構成X-bを参照(①)して、子捜しにより親品目Xが展開(②)される。次に製品構成Y-bから同様にして親品目Yが展開される。
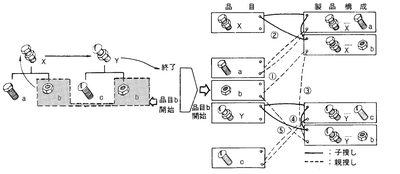
関連用語: 一段階展開
Single Level Where-used Bill of Materials
指定された品目の直接一段階上位(親)の品目を表示した部品表で、設計変更の影響把握、原価変更による上位品目原価影響度、それに部品の引当状況把握などに用いられる。図の例では、品目bを指定した場合にその親品目XとYの情報が表示される。また仮に品目イが指定された時は、その親品目aとcが表示される。
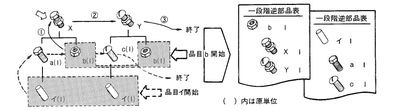
関連用語: 一段階部品表
指定された品目の直接一段階上位(親)の品目を表示した部品表で、設計変更の影響把握、原価変更による上位品目原価影響度、それに部品の引当状況把握などに用いられる。図の例では、品目bを指定した場合にその親品目XとYの情報が表示される。また仮に品目イが指定された時は、その親品目aとcが表示される。
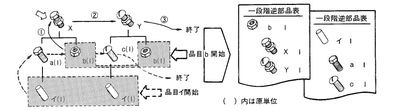
関連用語: 一段階部品表
Safety Lead Time リードタイム
各種リードタイムに対して、その変動する誤差を考慮して、安全分として設定するリードタイムのことである。一般には、内作品に対して、その製造の遅れを吸収するために製造リードタイムに付加される。また、購買品や外注品に対しては、業者の納期遅れの影響を最小にするために購買リードタイム、外注リードタイムに付加されて使われる。さらに、在庫の面からは、安全在庫の代わりとして用いられることもある。
各種リードタイムに対して、その変動する誤差を考慮して、安全分として設定するリードタイムのことである。一般には、内作品に対して、その製造の遅れを吸収するために製造リードタイムに付加される。また、購買品や外注品に対しては、業者の納期遅れの影響を最小にするために購買リードタイム、外注リードタイムに付加されて使われる。さらに、在庫の面からは、安全在庫の代わりとして用いられることもある。
ある工場長の話です。「MRPを導入したが、ちっともロットは小さくならないし、リードタイムも短くならない。どうしたものだろうか?」。 MRPさえ導入すれば、なにもかもうまくいくと思っていたのでしょう。従来とあまり変わらない現場を見て思わず相談に来たのです。これは大変な誤解です。 MRPはロットをしだいに小さくし、リードタイムを自然と縮める魔法の杖ではありません。あくまでコンピュータを使ったMRPという情報管理システムなのです。現場の意識を変え、管理レベルを向上し、より大きな効果を得るためには、企業体質を変えるための改善活動も並行して行う必要があります。まさに情報管理システムと現場システムは車の両輪のようなものなのです。
映画のセリフに「明日の事は?」「そんな先の事は分らない」というのがありました。このようなとき製造現場では担当者が経験を生かし、鋭いカンを働かせて仕事を進めてしまいます。これは普通、"思惑"とか"サバ"と言われ、工場の各部署でさかんに行なわれています。このため工場は"サバの大漁"となり、過大な在庫を抱えることになるわけです。"サバの生き腐り"を無くすには、誰にも分かる"明日の計画=MRP"が必要なのです。
"シングル段取"という言葉を最近よく聞きます。これは、"生産の流れ化"を実現する時に必ずぶつかるテーマなのです。「流れるようにものをつくりたい」といった要望の中での大きな障壁は、段取替えの時間が大きいことです。この時間を数分でできるようにしなければ、どうしても、「まとめてつくろう!」という気になります。段取改善に似たようなことを、歴史の中に見つけることができます。それは、織田・徳川の連合軍と武田軍とによる長篠の戦いです。このとき、連合軍を勝利に導いたものが鉄砲です。従来、玉込めなどの段取に時間のかかる鉄砲は、実践向きではなかったのです。しかし織田信長はその扱い方を一律にして、誰もが使えるようにし、かつ実戦では玉込時間を実質的にゼロにするために鉄砲隊を横3列に並べ順番に打たせました。つまり、標準化とゼロ段取を実践したのです。鉄砲が弓や刀に代わり、強力な武器として認められました。鉄砲のおかげで織田・徳川の連合軍が大勝利をおさめたことはいうまでもありません。このことでもわかるように、現場改善のちょっとした糸口は、ひょっとしたら歴史が教えてくれるかもしれません。
現場へ導入されたMRPシステムが、まったく使われていないケースをよく見かけます。システムは管理者のためだけではなくて、現場の人たちにも役立つものでなければなりません。そうでなければ、開発者が現場を説得したり、現場はそれを納得して受入れることができません。実によくできたもので、説得とは"得を説く"と書くし、納得とは"得を納める"と書きます。