不良の出ない仕組みを「ポカヨケ」と呼ぶのに対し、作業者がポカッとしていてミスを犯しても、ケガや事故が起こらないような仕組みを「安全のポカヨケ」という。どんなにルール化を徹底しても人はミスをする。またどんなに生産性が上がっても、品質が向上したとしても、安全無き発展はありえない。安全第一を実現するうえでも、この仕組み作りは重要である。
より安全を期すとすれば、「人離し」が究極の安全におけるポカヨケといえよう。
保全・安全の最近のブログ記事
改良保全とは、Corrective Maintenance の略で故障が発生した際、二度と同じ故障を起こさないように、設備自体の体質改革をすることである。このために、設備の劣化を少なくして、信頼性を向上させるほかに、日常点検がやりやすいように設備自体を変えたりする。
給油は機械設備の保全3要素の1つ。JITによる給油の基本は、機械を正常にかつ効率的に稼働させるために、「必要な油質を、必要な補給時期に、必要な補給量だけ」供給することである。この油質、補給時期、補給量の管理をスムーズに行うには、目で見る管理であることが大切で、「給油ルートの色別整頓」や、「給油かんばん」は有効である。もちろんこの作業時には、油モレや油質の濁り、給油口の清掃等の点検も忘れてはならない。(図23、図24)
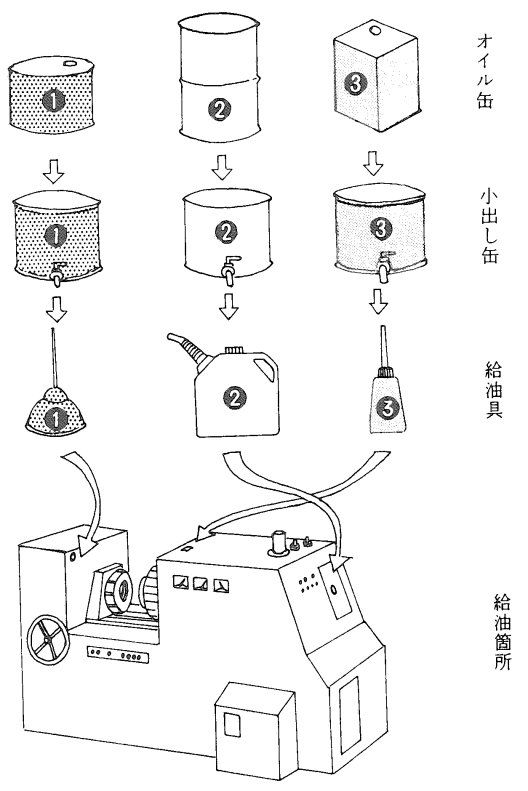
図23 油の色別整頓
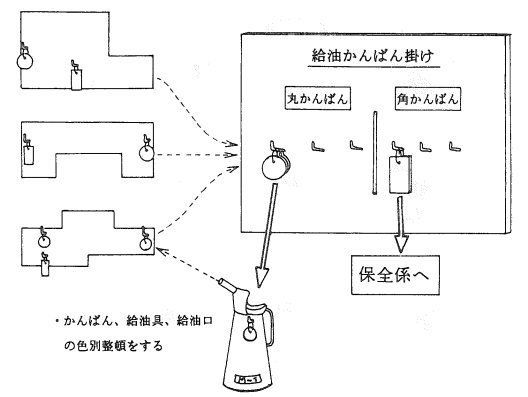
図24 給油かんばん
関連用語: 油の整頓
JITの提唱する7ゼロの1つ「災害ゼロ」のうち、"人の安全"を目標とするキャッチフレーズであり、「ケガゼロ」とも呼ばれる。災害ゼロは当然であるが"ゼロでなくてはならない"ゼロ・ベースを基本とする。「事故ゼロ」も同じである。
安全はすべてに優先する。安全な作業が行われはじめて、生産性・品質の向上が成り立つといってもよい。
事故ゼロを達成するためには次の改革が必要である。(図64)
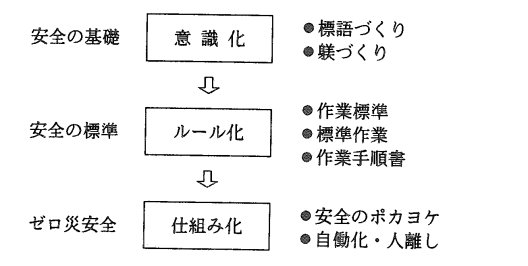
図64 意識化・ルール化・仕組み化
①事故は概して人に起因するものである。標準以外の作業をしたり、保全活動(TPM)をおろそかにしていたり...。安全な生産の流れを把握し、5Sや指差呼称など、ルールを守る習慣化を徹底する。それは全社的に推進しなければならない。→意識化
②安全を守る第一原則は標準作業を守ることである。まず、その指標である作業の標準をつくり、標準作業の指導書・要領書に作業の手順と安全を確保するための注意事項を示す(目で見る管理)。→ルール化
③どんなに意識化・ルール化しても人はミスを犯すものである。そこで万一ミスを犯してもケガや事故につながらないように、機械設備自体に「安全のポカヨケ」等の仕組みを取り入れる。→仕組み化
関連用語: ケガゼロ
JIT生産を“流れの分断”なく進めるには、より徹底した生産保全活動が要求される。生産は作業者、点検・保全は保全係といった個別的な考え方では、いくら保全管理を充実しても、いっこうに改革されない。
機械設備の稼働ぶりを一番把握しているのは作業者である。1人ひとりの作業者が、生産の一環として保全のSTK(清掃・点検・給油)を習慣化する。これを自主保全という。
機械設備が正常に稼働しているか、故障が発生していないか否かをチェックすることをいう。保全活動の3つの習慣の1つ。点検は決して作業の時間外に行うものではなく、標準作業の一環として位置づけなくてはならない。日常点検は清掃と合わせた毎日の清掃点検業務に組み込み、それを補う形で定期点検を行う。
流れ生産はサラサラと"清流"のごとくラインが流れてはじめて、JITの物造りが生きてくる。そのためには、機械設備の故障ゼロは大前提である。保全とは、機械設備が故障しないようにすることで、その"可動率"を高めることにもつながる。
故障はなぜ起きるのか。機械の"劣化"が進んでいるからである。ゆえにこの劣化をより早期に発見することが保全の課題といえる。取り組みの形としては4つの基本がある。(図129)
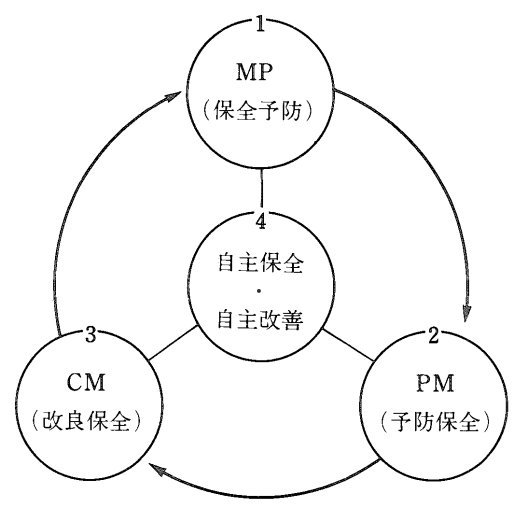
図129 故障ゼロ・不良ゼロの生産保全サイクル
●MP(保全予防)...可動率の高い設備計画(劣化防止しやすい機械設備等)
●PM(予防保全)...日常の自主保全・自主改善の推進
●CM(改良保全)...設備自体の体質改善
●自主保全・自主改善...作業レベルでの保全
また保全活動には清掃の習慣(S)、点検の習慣(T)、給油の習慣(K)、の3つの習慣STKが大切である。
機械設備の保全作業が実施される過程を明記したもの。機械の保全すべき箇所に貼り出す。保全の目で見る管理の1つである。(図130)
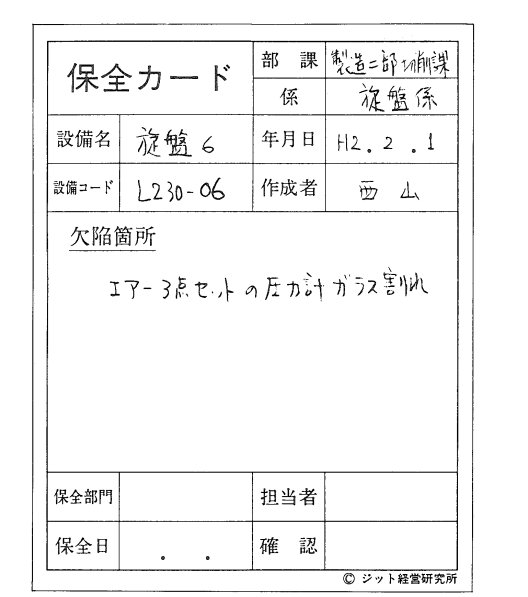
図130 ●記入例『5S指導マニュアル』、p.452より