生産とはどんな形をとるにしても、顧客ニーズがあってこそ利益を生む。いい換えれば製品を買ってもらわなければ製造業は成り立たない。世の中は多品種少量・変種変量がさらに細分化しつつあり、「売れた物を造る」買い手市場のマーケットイン思考が必須となってくる。
この考え方を製造現場における工程間の流れにまで取り入れたのが「引っ張り生産」。「後工程はお客様」はそのキャッチフレーズで、お客(後工程)がストア(前工程)で買った分だけ仕入れるスーパーマーケット方式の仕組みをいう。
生産計画は最終後工程のみに手配される。その生産結果を前工程は知らされ依頼を受けはじめて作業することができる。つまり後工程が造らないかぎり、前工程は造れない。また生産計画は常に実績情報として前に流れ、かつその時点での顧客ニーズと等しく、後工程には常に"お客様"が介在する。これはすなわちムダゼロで「必要な物を、必要な時に、必要なだけ造る」JIT生産の実現をも意味する。
ちなみにこの情報を流す道具が「かんばん」である。
一方、前工程からの「押し込み生産」では、生産計画は各工程ごとに手配され"工程独立生産"となるため、その実績が一律とはなりにくく、工程間に真の"お客様"情報が流れない。
意職改革: 2008年1月アーカイブ
意識改革とは、人の意識つまり人の頭の中を変えることをいう。いままで経験や知識をベースとした固定観念や古い意識を捨てることから始まる。
上からの改革とは、「JIT生産」のようにあるべき理想像を掲げ、これに現状を合わせていくやり方で、上から下を引っ張り上げる型であり、トップアップ型という。上からの改革は、トップアップ型の改革といえる。
関連用語: 下からの改革
「働く」という言葉は、人それぞれの仕事観によっても個人差がある。その考えは、必ずしも実質的利益に結び付くとはかぎらない。一応就業8時間を費やせば、"働いた"と感じる人もいれば、"汗"が労働の証★あかし★と考える人もいる。単に時間だけを費やす考えは、"動かず"であり、汗をかくだけは"動き"でこれら両方ともムダといえる。「働く」とは付加価値をつけ、実質的利益を生み出すことをいう。これに対し「動かず」とか「動き」とは付加価値をつけない作業のこと。たとえば次のようなことがある。
●重い部品を運ぶ
●作業を終えた部品を数える
●床に積んである部品を台車に載せる
●後工程に渡すために、部品をビニール袋に入れている
●前工程からもらった部品を、ビニール袋から出している
●今日の仕事が終わったので、得意気に明日の分を造っているこのように作業といわれる中には、「動かず」「動き」それに「働き」の3つがあり、「動かず」「動き」の2つをムダといい、「動き」のみが付加価値となる。つまり人が動いて働きになるの意味がある。
関連用語: 働き
作業は"動き"といわれるムダと"働き"といわれる付加価値と、2つからなり、動きをしていることを「動く」と呼ぶ。作業の中で動くことが多ければムダが多いことであり、これをなくすか少なくすることが必要となる。
関連用語: 働く
"遅れ"とは「必要な時に間に合わないこと」で、生産の作業遅れ・納期遅れ等を指すわけだが、これはJITの定義に反するばかりか、対外的な信用度の問題となり企業存続の致命傷ともなりかねない。
「遅れゼロ」はゼロ・ベース発想法による"納期保証"の構想で、あらかじめ定められた生産時間の基準つまり顧客要求に基づくタクトタイム、リードタイム、納期等を遵守すること、すなわち"ジャスト イン タイム"を意味する。これは人の心構えに大方寄与するといえ、意識化が第一の課題。5Sの躾づくりの徹底が決め手となる。また「停滞ゼロ」の必要十分条件としてとらえられる。
関連用語: 停滞ゼロ
改革の手順は、まず現場に立ち「なぜなんだろう?」という疑問をもち、大いに悩んでチエを出し葛藤(コンフリクト)が始まる。
そして情熱をたくわえ、改革を実践していく。
このように疑問をもち、葛藤し、情熱をつくり、改革していく周期的な手順を改革サイクルという。(図11)
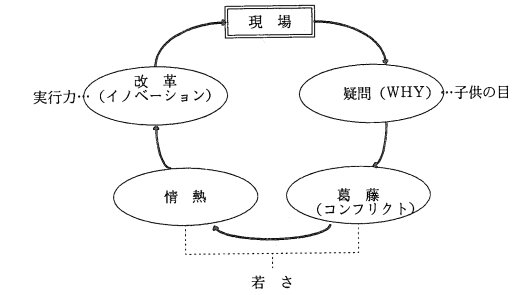
図11 改革サイクル
関連用語: 革新のスパイラル回路
生産工程を物の流れからとらえると、「停滞」「運搬」「加工」「検査」に分けられる。つまりモノ造りは加工だけから成り立たつわけではない。リードタイムの内訳として加工にかかる時間は秒単位である。ハイスピードで高価な機械を導入しても大した変革にはならない。顧客の短納期要求に応えるためには、まず「停滞」の回数・時間を無くすかもしくは大幅に短縮することがキーポイントとなる。
購入した材料を倉庫に在庫する=停滞。材料を倉庫から作業場に運ぶ=運搬。前のロットが終わるまで待つ=停滞。数秒の加工。次の工程に運搬されるまでの待ち=停滞。製品倉庫に運ばれる=運搬。さらには大ロットであればあるほど、作業場が離れていればなおさら、停滞のムダがふくれ上がる。停滞は運搬のムダも助長する。製造リードタイムを短くするにはこの停滞を排除して、加工(カコウ)→運搬(ウンパン)→加工(カコウ)→運搬(ウンパン)の"カウカウ生産"にしなくてはならない。(図15)
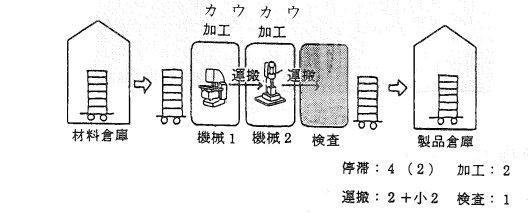
図15 カウカウ生産
関連用語: テカテウ生産
企業革新(イノベーション)をしていく時の疑問意識、葛藤、情熱、改革のスパイラル回路をいう。
関連用語: 改革サイクル
材料を製品にするには、いくつかの加工をつける必要がある。このことを加工度といい、製品にすることを加工の度合いを上げる、つまり加工度を上げるという。
1品種大ロットといっても、資本運用の面から限度がある。そこで目安となるのが経済ロット。金利、保険、税金、保管費、陳腐化費用等の「在庫維持費用」と、製造事務作業費、機械段取り費、材料ロス、取り外し費用等からなる「段取り費用」とのバランスを考慮し、その総費用が最少になるような数量をいう。しかし大ロット前提の経済ロットは得策とはいいがたい。
工場では多くの部品を扱う。そのうえ多品種少量の時代、さまざまに部品が変わる。こういった品種の切り替えに対応し、在庫投資を抑え、経営資本の回転率や利益率を向上させるには、できるだけ小ロット体制が望ましい。製造リードタイムを短くすることも肝要で、小回りのきくモノ造りが要求される。ある単一工程だけを考えるのではなく、工場全体、また販売も含めた会社全体を考えた時、より小さなロットが経済的ロットといえる。(図26)
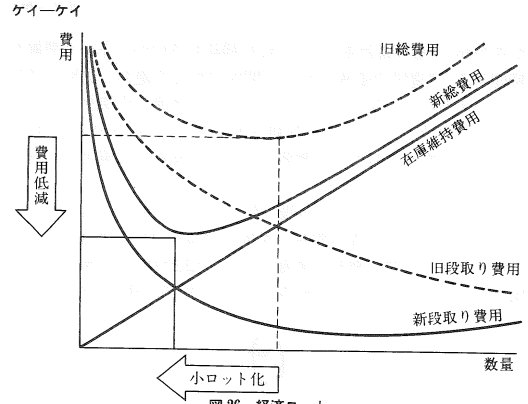
図26 経済ロット
JIT改革とは、いい換えれば"現場"改革のことである。机上での改革は空論にすぎない。まず、現場に入って実践することから始まる。「JITとは...」と理論を話すことでもなく、それを聞くことでもない。また、「整理・整頓」等のポスターを書くことでもなく、現場を単に見て回ることでもない。現場改革とは現場に出て、Doit、「やる」ことである。
関連用語: 体の改革
5WHY1HOWの略。
改革の第一歩は、現状の異常や問題に「ナゼ?」(WHY)という疑問を投げかけることである。疑問をもったら、徹底して"真因の追求"をする。1つの単純な疑問にとどまらず、それを次々に展開させていく。
1WHY「部品を運んでいるなー? ナゼ?」(運搬のムダ)
2WHY「置場が離れているからだ。ナゼかな?」(置場のムダ)
3WHY「機械が離れているからだ。でもナゼ?」(レイアウトのムダ)
4WHY「職場が別だからな。でもナゼだろう?」(組織のムダ)
5WHY「ずっと前に決めたままだ」(固定観念)
1HOW「それじゃ機械をつなげよう」
機械をライン化し、組織を変更するといった改革をすることで、ムダゼロ、少人化が実現する。5W1Hは問題の真因を見つけ、これを解決することで、二度とムダが発生しないための重要なアプローチである。
真の改革がうまくできない、いわゆる「なぜするのか?」という疑問意識がもてない人のための道具。5回の「なぜ?(WHY)」を繰り返し、最後に「どのように改革するのか(HOW)」が記入できるシート。(図49)
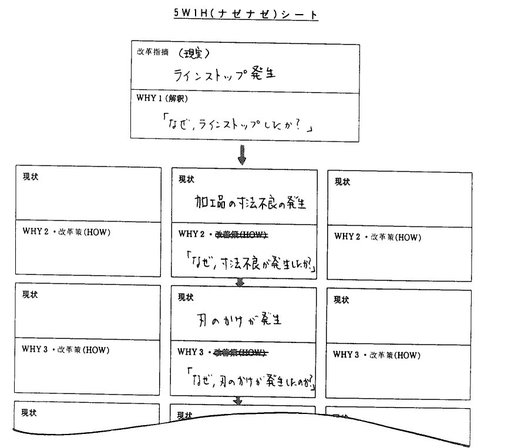
図49 ●記入例『ジャストインタイム生産革命指導マニュアル』、p.637より
関連用語: 5W1H
下からの改革とは、徹底した現状分析を基礎として、レベルアップを図っていく型で、そのやり方は、下から上へ向かって押し上げていく。これをボトムアップ型という。これは改革というよりむしろ改善で終わる場合が多い。下からの改革は、ボトムアップ型の改革といえよう。
関連用語: 上からの改革
ジャスト イン タイムとはJust In Timeであり略してJIT(ジット)などと呼ばれる。これは「必要な物を、必要な時に、必要なだけ生産・供給する」ことをいい、物が“ちょうど間に合う”ことを意味する。
しかし、これは一般にわかりやすいジャスト イン タイムの定義で、真の意味は「徹底したムダ取りの思想と技術」である。
ジャスト イン タイムとは、その訳のとおり"ちょうど間に合う"ことを指し、ちょうど間に合うように生産することをジャスト イン タイム生産と呼ぶ。つまり「必要な物を、必要な時に、必要なだけ生産・供給する」となる。
またジャスト イン タイム(Just In Time)は略してJITと書き、「ジット」と呼びJIT生産ということもある。いずれにせよジャスト イン タイム生産は、①意識改革、②5S、③流れ生産、④平準化、⑤標準作業の手順をもち、「徹底したムダ取りの思想と技術」を表す。
関連用語: JIT生産方式
これは、顧客リードタイムの正しいあり方をいう。
顧客リードタイムとは、顧客が注文してから、品物を受け取るまでを指し、通常、品物を造るための時間(製造リードタイム)とでき上がった製品を顧客に運ぶ時間(輸送リードタイム)の合計を意味する。
しかし顧客は「欲しい物を、欲しい時に、欲しいだけ」要求する。そのニーズに応えようとして製品在庫をもつ。見かけ上、顧客リードタイムは製品を倉庫から運ぶ輸送リードタイムだけとなる。これを"見かけのリードタイム"という。
こうすることで、一見顧客にはうまく対応したように見えてしまう。しかし、工場では、製造リードタイムが長過ぎることや在庫があふれていることの問題意識が薄れてしまい、やがて市場への変化対応力を弱める結果となる。見かけだけで対応せずに、また製品在庫をもたずに"真のリードタイム"を短縮することが企業のより強い体質をつくることになる。(図71)
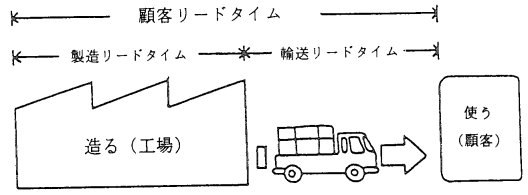
図71 真のリードタイム
関連用語: 見かけのリードタイム、リードタイム
設備改革とは、道具としての機械設備を変えることである。これは、機械設備を新規導入したり、自働化ラインへの改造といったことが一般的であるが、JITでは以下のような12の設備導入の条件がある。
設備導入12の条件
条件1 いまの数字で儲ること
条件2 1個流しに徹すること
条件3 スピードよりもタクトタイムを重視
条件4 専用汎用化
条件5 小型で、いつでも移動できること
条件6 誰もが扱えて、かつ人が離れられること
条件7 投入・取り出しが一致していること
条件8 検査機能がついていること
条件9 良品・不良品のカウントができること
条件10 保全がしやすいこと
条件11 汚れが出ないこと
条件12 異常を知らせること
関連用語: 設備導入12の条件
機械設備はあくまで生産の"道具"であり、生産の仕組み・方式に応じて導入することが大切である。JIT生産においても、例外ではなく、意識改革・作業改革を前提とした次の12の条件を掲げることができる。
①いまの数字で儲かること→顧客要求高=産出高=真の能率、短期原価償却の設計
②1個流しに徹すること→流れ生産、全体の能率、ムダゼロ
③スピードよりもタクトタイムを重視→平準化、標準作業
④専用汎用化→専用ライン、安価
⑤小型で、いつでも移動できること→ライン化、キャスター作戦
⑥誰もが取り扱えて、かつ人が離れられること→標準化、多工程持ち、立ち作業、人離し
⑦投入・取り出しが一致していること(I/O一致)→入れ入れ作業
⑧検査機能がついていること→自働化、ポカヨケ
⑨良品・不良品のカウントができること→ポカヨケ
⑩保全がしやすいこと→点検、可動率
⑪汚れの出ないこと→5S
⑫異常を知らせること→アンドン
関連用語: 設備改革
全品を検査すること。“不良を出さない100%”の品質保証を維持するためには、全数検査が望ましい。そのやり方としては、“不良を見つける検査”ではなく、“不良をつくらない源流検査”を心がけるべきである。いくら全数検査でも、検査要員を増員したり、手間がかかるようでは結局やり切れない。そこで“抜取検査”で手抜きということになってしまう。
ポカヨケ、自働化、流れ生産等をフルに活用して工程に全数検査を組み込み、「全品良品を最低のコストで造る」ことが大切である。
関連用語: 抜取検査
材料はいくつもの工程を経て製品となる。この全体の流れを生産といい、その流れにムダがなく、スムーズな状態であることが能率アップにつながる。1人の作業者、1台の機械だけで、個々の能率を上げても、つまった流れでは全体の能率が下がってしまう。これを"個々の能率"と呼び、流れを乱す原因ともなる。1作業者や1機械、1工程だけの能率を考えるのではなく、製品ごとに1台何分何秒で造るのかを割り出す(タクトタイム)。これに合わせて、流れの各工程は作業をしていき、その中で全体の能率を上げていくことが主要となる。
関連用語: 個々の能率
多品種対応には、1台でなんでもこなす高価な汎用機は不適である。ムダな機能はすべて取り除いた、安価な機械で、使う時は、専用機の効率を、モデルチェンジ時には、それに追随できる汎用性を備えた機械を“専用汎用機”という。
ゼロ・ベース発想法に基づく7ゼロ生産の要素の1つ。
「変種変量生産」といういい方があるように、市場ニーズは日々めまぐるしく変化し、製造現場では"フレキシビリティ"=柔軟性が問われている。小回りが利く生産か否か、いい換えれば、"大よりも小""長よりも短"の中に利益を見い出す"スモールメリット"思考が求められている。
停滞ゼロは納期対応において"スモールメリット"を可能にする構想で、短納期化を目指し、その指標であるリードタイムの時間短縮を図る。
停滞とは、作業待ちの状態にある時をいい、運搬待ち、納入・出荷待ち、入出庫待ち、加工待ち、組立待ち、検査待ち等々、工場内には多くの停滞が蔓延している。また同時に「物を停めて置いておくこと」となり、物は在庫として存在する。在庫は概して欠品・納期遅れを避けるための問題解決策として正当化されるが、あくまで暫定的な改善であって、納期は厳守されるがまた欠品・遅れが再発しかねない。"待ち"はムダな時間の経過となり、結局リードタイムをむやみに長くし需要変動に対応できず、さらに過剰在庫を生み出す悪循環を招く。
「なぜ、物は停滞するのか。停滞がなくても、物は造れる」を信念に物の停滞時間をゼロにする。すなわち在庫ゼロにした物造りの必要最短時間、つまり時間のムダゼロ化を徹底し生産方法を組み直す。かつ納期遅れゼロであってこそ顧客の短納期ニーズに応える真のリードタイム、真の納期対応といえる。
そこで停滞ゼロはリードタイムの意識改革から始まる。
●リードタイムとロットは比例する→1個流し(→流動数曲線)
●顧客リードタイム=∑全部門(受注から納入まで)リードタイム→全社的推進
●製造リードタイム=∑正味加工時間
※正味加工時間(ワーク1個に付加価値をつけるのにかかる作業、加工着手から完成品になるまでの所要稼働時間)(→タクトタイム)
また受注後に製造する受注生産が前提であり、その低コスト化・短納期化が可能となる。ルール化としてはもちろん、5Sが基本となり、具体的仕組み作りは、図97に示したとおり。
こうした納期対応力は企業のもつ統合力にもつながる。自社内にとどまらず、外注・購入業者を巻き込んだ"体★たい★の改革"が望ましい。
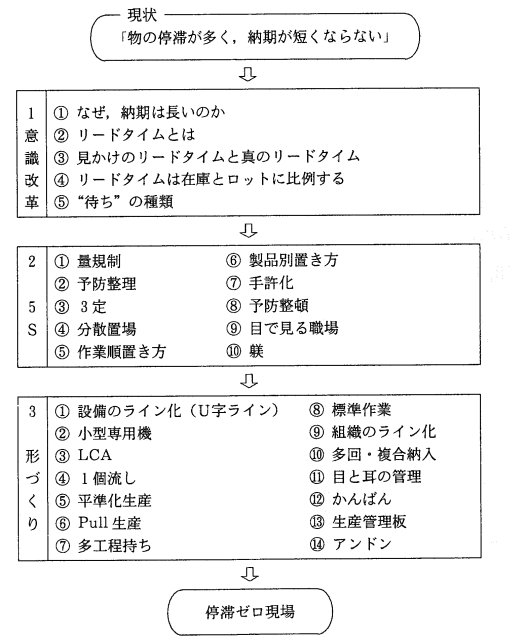
図97 停滞ゼロへのアプローチ
在庫は悪である。在庫の山は過剰な物の「停滞」である。一般の工場では、この停滞(テイタイ)→加工(カコウ)→停滞(テイタイ)→運搬(ウンパン)の四拍子で進行する"テカテウ生産"が多い。停滞回数・時間が多ければ多いほど、製造リードタイムを引き延ばし、在庫を増やし、かつ多くのムダをつくり上げる。まず停滞をなくすことが必須。それができなければ一歩譲って、必要最少限に抑えることである。(図98)
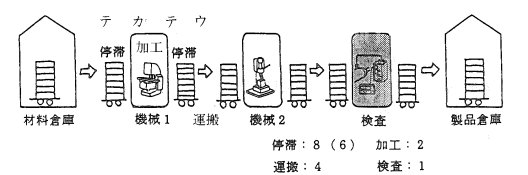
図98 テカテウ生産
関連用語: カウカウ生産
“過剰在庫”はムダのキワメツキ。一方“過少在庫”では欠品を起こす。そこで生まれたのが“適正在庫”という考え方。
たとえば、販売目標を基本とした場合、次の式で適正在庫を算出する。
適正在庫高=年間売上高/商品回転率
年間売上高4,000万円、商品回転率16回転だとすると、4,000÷16=250万円 1回転当たりの在庫周期は 365÷16=23日 となり、適正在庫は金額で250万、日数で23日分ということになる。しかし、環境はめまぐるしく変化し、年間売上高、商品回転率も市場に合わせて大きく変動する。式から得られた数字はあくまでも目安にすぎない。“見かけの適正”とでもいえる。
確かに、売上高とか在庫回転率といった経営指標は大切である。しかし、なんの努力もせずに“適正”といった言葉を乱用し、この数字をかたくなに守っていれば「会社は安泰だ!」といった安易な考え方、つまり、その在庫を正しいとするなら、それ以上の工場革新は望めない。
販売が本当に求めているものは“在庫”ではなく、“欠品をなくす”こと。このためには在庫で逃げず、業務の改革が必要である。“適正在庫”と問われたら、即座に「それはゼロである」と答える気構えが必要となる。
1970年代以降、製造業市場は消費者中心のマーケットイン思考が主流で、さらに「売れる(売れた)物を造る時代」といえ、多品種少量生産がニーズとなっている。7ゼロ生産はその生き残り戦略・工場革命として、JIT生産を実現するためのもので、企業イノベーションの本質的発想転換を提言している。
従来のIE、提案制度、小集団活動、統計的品質管理等の手法は、あくまで現状を肯定したうえの分析で、部分的に"善★よ★く改める"いわば「改善アプローチ」の低減発想法となる。たとえば、大ロット生産を小ロット化するようなもので、"見かけの効率化"を施したにすぎない。これに対し、7ゼロ生産では、現状を全面的に否定し"革★あらた★に改める"「改革アプローチ」とし、JITの"徹底したムダ取り"を基本とする"ゼロ・ベース発想法"で企業の再構築を図る。具体的には次の要素があげられる。
①切り替えゼロ(Products)←多品種化
「なぜ、切り替えをするのか。切り替えなしでも物は造れる」
②在庫ゼロ(Inventory)←問題表面化
「なぜ、在庫がたまるのか。在庫なしでも物は造れる」
③ムダゼロ(Cost)←コスト削減
「付加価値以外はすべてムダ。ムダ作業なしで、物は造れる」
④不良ゼロ(Quality)←品質保証
「なぜ、不良が出るのか。製品は不良なしで、必ず造れる」
⑤故障ゼロ(Maintenance)←生産保全
「なぜ、お前は止まるのか。機械設備は故障なしで、働き続けられる」
⑥停滞ゼロ(Delivery)←短納期化
「なぜ、物は停滞するのか。停滞がなくても、物は造れる」
⑦災害ゼロ(Safety)←安全第一
「赤チン、唾つけ絶滅。事故・災害は、必ずなくせる」
ゆえに各々の頭文字をとり「PICQMDS(ピックエムディーエス)」とも呼ばれる。
手順としてはまず、これら7項目を問題として認識し、上記に表した言葉どおり「なぜ(WHY)」の疑問から"真因の追求"をし、意識改革していくことが第一歩。そして図105の「5つの指針」にある"流れ"を念頭に対策を練る。この際5Sが基礎となることはいうまでもない。
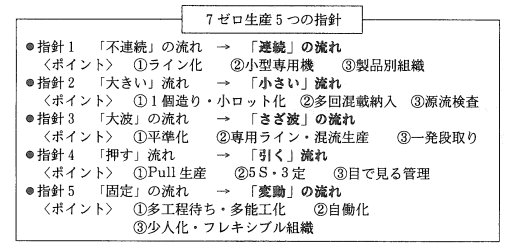
図105
また、改革の相乗効果をうながすためにも実績評価は欠かせない。トップダウンで全社的経営目標を設け、結果は部課別・ライン別、月または年次でその推移をグラフ化し掲示することも大切であり、さらなる課題の叩き台とする。その指標項目には「9つの指標」があげられる。(図106)
あとは"3現3即3徹"の行動あるのみ。
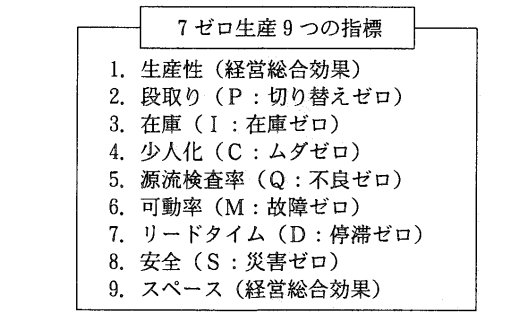
図106
製造会社を運営していくために必要な要素は9つに分類される。それは、人(Man)、物(Material)、設備(Machine)、金(Money)、方法(Method)、販売(Marketing)、経営(Management)、技術(Engineering)、情報(Information)の9つである。それぞれの頭文字(7MとEとI)を、とって7MEIという。改革はこの9つの観点から検討していく。なかでも製造現場でとくに必要なものは、人、物、設備、方法、情報の4M1Iの5つ。具体的には、「作業指示(情報)を受けて、部品や材料(物)を払い出し、ある機械設備(設備)にかけて、作業者(人)が、標準作業(方法)に従って物を造る」ということ。(図107)
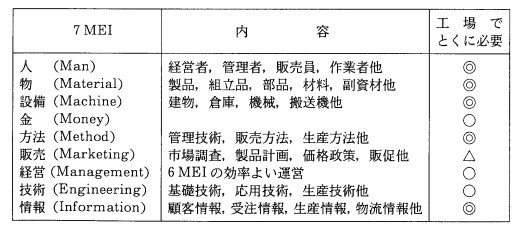
図107 7MEI
関連用語: 4M1I
「ジドウカ」には「自動化」と「自働化」の2とおりがある。前者は"自ら動く"こと、単純に作業を"機械化"することを意味する。この場合、不良が出ても機械には判断できず人の閑視(Looking)を必要とする。つまり人件費と設備費の二重のコストがかかってしまうことになる。後者は"自ら働く"こと、不良のチェックができる働く機械を意味する。つまり、「ニンベンのついた自働化」は3つの機能がある。
①人離し...加工運動のすべてを機械に任せる。人と機械を離す→人件費カット
②不良の出ない仕組み...人がいなくても機械だけで付加価値がつけられる→働く機械
③もう1つの自働化...加工部門の自働化を組立部門やラインにまで応用する
関連用語: 自働化
生産されたロットごとにその一部を抜き取って検査し、推計学を応用して、仕切り全体の合格・不合格を判断すること。この方法は手間がかからず合理的と勘違いされやすいが、生産者側だけに都合のよい"手抜き"検査で、全品良品は保証できない。品質保証とは不良ゼロが基本にあり、そのことから流れに組み込んだ全数検査のほうが望ましい。
関連用語: 全数検査
生産理念の1つ。生産者中心の考え方で、"造りやすい物を、造りやすい時に、造りやすいだけ"生産することをいう。そこでは顧客の経済性、合理性、利便性等が無視される。市場が造り手市場、売り手市場の場合、多く見られる。
関連用語: マーケットイン
多品種少量・短納期生産時代の消費者中心の生産理念。"必要な物を、必要な時に、必要なだけ"生産することを基本とし、生産のすべてのことに消費者を意識していく。たとえば、ロット生産よりも1個流し、ダンゴ生産よりも平準化生産、抜取検査よりも全数検査等がこの例である。
関連用語: プロダクトアウト
現場で問題点を改善する時、真因を追求せずに表向きだけの処置をすることをいう。それを「見かけの改善」とか「小手先の改善」と呼ぶ。
たとえば、「山積みになった仕掛在庫を棚を作って整頓する」とする。見かけは確かにスッキリ、問題は解決したかに思えるが、在庫を認めるばかりか、在庫のムダは増え続ける一方となる。(図134)
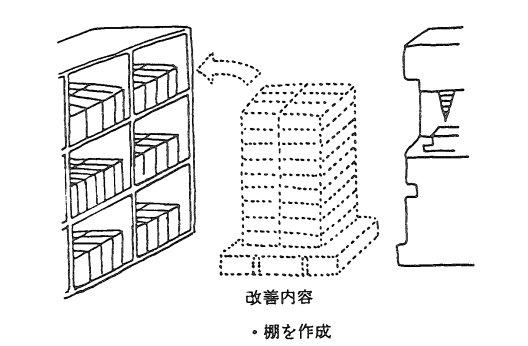
図134 見かけの改善
関連用語: 真の改善
能率とか生産性は次の式で算出される。
能率(生産性)=産出高(生産高)/投入高(人員)
①投入高が一定の時、産出高を増やせば、生産性は向上する
②産出高が一定の時、投入高を減らせば、生産性は向上する
③産出高を増やしかつ投入高を減らせば、生産性は向上する
しかし①の場合、式による数字は必ずしも実質的能率アップとはならない。「10人で200個生産」が「10人で250個生産」になったとする。数字は確かに生産性向上を表しているが、顧客の要求が200個だとすれば、50個は造り過ぎ、在庫のムダとなる。机上の方式は空論。これを「見かけの能率」という。(図135)
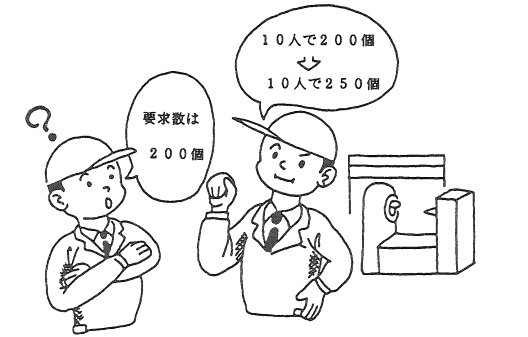
図135 見かけの能率
関連用語: 真の能率
製造現場では、「作業指示(情報)を受けて、部品や材料(物)を払い出し、機械設備(設備)にかけて、作業者が一定の標準作業(方法)に従って物を造る」ことを基本としている。つまり、製造現場における物造りに必要なことは、人(Man)、物(Material)、設備(Machine)、方法(Method)、情報(Information)の5つ、略して4M1I。
これらをどのように改革・改善するかがポイントとなり、次の点がテーマとなる。
人→躾、基礎教育、多工程持ち
物→源流管理
設備→ポカヨケ、全員参加の生産保全
方法→流れ作業と標準作業
情報→目で見る管理
関連用語: 7MEI
英語でLead Time と書き、生産を指図する時間・目安と意訳する。元来納期計算に使われる用語で、納期から着手日を算出するための1要素を形成し、「先行日数・時間」「手番」とも呼ばれる。一般には、タクトタイムやピッチ等を総じて、さらには生産過程のあらゆる業務にかかる「所要時間」の意味で定着している。つまり、オーダーを受注後作業を開始・終了しオーダーを納入するまでの期間として求められる。
各工程ごとには、製造リードタイム、販売リードタイム、購買・外注リードタイム、設計リードタイム、ペーパーリードタイム、物流リードタイム等に分けられるが、ここで問題となるのが、「顧客リードタイム」のとらえ方である。顧客から注文をもらい製品の納入が完了するまでの期間の設定で、これによって"納期対応"の仕方が異なる。たとえば、家電品等の見込生産では販売予測により製品に立ち上げてから受注を待つので、物流リードタイムが顧客リードタイムとなる。一方、受注生産では注文後に製造するので、全工程の総リードタイムが顧客リードタイムである。しかし、前者は予測間違いをすると欠品・過剰在庫を起こし、後者はキャンセルや納期変更に対処できかねない。
ゆえに、JITの顧客リードタイムは次のように定義する。
●全体の能率が真の能率→顧客リードタイム=∑全工程リードタイム
●リードタイムの時間短縮・短納期化→停滞ゼロ
またリードタイムは通常、生産計画において部品表に提示され、その品種ごとに品目・製品(使用する品目の関連)・管理(全製造工程の関連)の基準で表すが、市場の急変に追随するためにはより細分化した立案が望まれる。つまり、1個単位でリードタイムを算出し、顧客の要求量に応じた納期変更を可能にする。●予定開始日=納期-(1個当たりのリードタイム×顧客要求数+停滞ゼロ)
※リードタイム=∑正味加工時間(全工程の総稼働時間)
「必要な時」に顧客を満足させ(Customer Satisfaction)、工場の"ムダ取り"も同時に実現することができはじめて"真のリードタイム"が成り立つ。
関連用語: 停滞ゼロ、タクトタイム、真のリードタイム、見かけのリードタイム
作業のムダを取らずに「生産高だけを多くしろ」というやり方である。当然、仕事量が増えるため、作業を速くするしかない。作業者とて人間、スピードアップにも限度がある。造れなければ残業となる。ムダを取らずに生産高を増やすことは、労働を強化することにつながる。(図149)
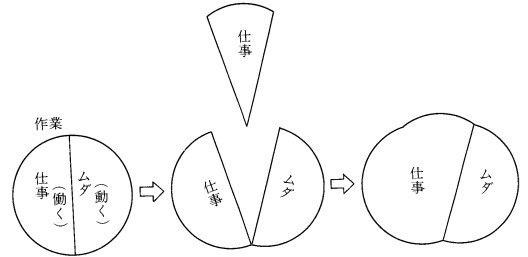
図149 労働強化
関連用語: 労働密度の向上
作業=動き(ムダ)+働き(付加価値)。労働密度の向上とは「働く」比率、つまり付加価値比率の向上を意味する。それにはまず、ムダ取りから始める。ムダゼロに近づけば近づくほど、作業の本質である付加価値の範囲が自然に増え、生産高も向上する。(図150)
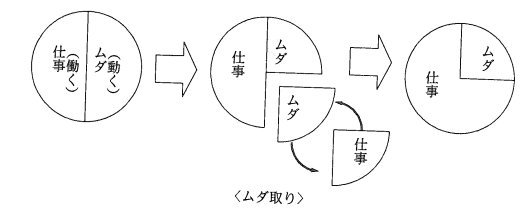
図150 労働密度の向上(能率向上)
関連用語: 労働強化
改革に抵抗はつきもの。それらは概して人のもつ"固定観念"としてはびこり、以下の例があげられる。題して「JIT生産革命抵抗の10項目」。
①そんなものは役立たない!
②確かにそうだが、我々は違う!
③案としては立派だが...。
④これ以上、コストは下がらない!
⑤我々だって、いつもそうしているよ!
⑥他人の勧めでやるのはイヤだ!
⑦コストを下げれば、品質は落ちる!
⑧うまくいっているではないか? なんで変えるのか?
⑨そんなものはダメだ! 我々は20年前にやったことがある。
⑩我々は、そのことについて一番よく知っている。
これはゼネラルエレクトリック社(GE)でマイルズがVA/VEを実施した時出てきた"抵抗"群である。
JIT改革ではまず、抵抗を一掃する人の"意識改革"を何よりも先決と考える。
JIT・CIMとは、定められた価格と品質の製品を所定の数量、期日に合わせ、もっとも経済的にかつ柔軟に開発、生産、販売をするために、物的システム(機械設備、設備配置、生産・供給方法、物の流し方等ハードな面での総合体系)と、管理システム(組織、制度、手続き、管理技術、情報の流し方等ソフトな面での総合体系)を改革、統合化し、融合化して駆使することである。このことにより、人(Man)、物(Material)、設備(Machine)、情報(Information)、資本(Money)の4M1Iをもっとも有効に活用する企業システムである。
製造業における生産テーマで、Products(品種)、Quality(品質)、Cost(価格)、Delivery(納期)、Safety(安全)の5つの頭文字をとったもの。これは、多品種少量・短納期生産時代のキャッチフレーズとして次のように解釈される。
「顧客の望む品物(P=多品種)を、よい品質(Q=高品質)で、安く(C=低コスト・市場価格)、速く(D=短納期)、かつ安全(S=安全第一)に提供、サービスする」
従来から、QCD「よい品質の物を、安く、速く」の3要素は叫ばれてきたが、これはあくまで単に物を"造れば売れる"大量生産時代のプロダクトアウトの思考を基礎にしている。そこで新たにPSの2要素を加味し、"売れる(売れた)物を造る"マーケットインのサービス業的発想への転換を示唆する。
また、これらをゼロ・ベース発想法で展開させ、P=品種切り替えゼロ、Q=不良ゼロ、C=ムダゼロ、D=停滞ゼロ、S=災害ゼロとし、さらに在庫ゼロ=I(Inventory)、故障ゼロ=M(Maintenance)をプラスした7ゼロを提唱するPICQMDS(ピックエムディーエス)へとつなげる。
関連用語: 7ゼロ生産