目で見る管理: 2008年1月アーカイブ
棚や置場における物の“整頓”方法の1つで、在庫や仕掛りの必要最低量・最大量がわかるように、壁等に赤のテープや塗料で印をつける。これを赤ラインという。この表示により、ひと目で不足か過剰かが識別可能となる。看板作戦の量表示の一環でもある。
"どこに、何を、いくつ"置くかを記入した看板で、各置場に掲示される。看板作戦の"場所表示"の1つ。工程間の仕掛置場はもちろん、外注業者が納入する際にも目印となる。(図9)
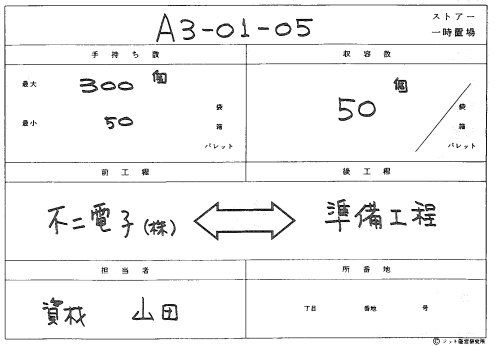
図9 ●記入例『ジャストインタイム生産革命指導マニュアル』、p.660より
物の置き場所を明示かつ区分けするために引く。
在庫品や治工具類等の置場における品目別の区分け、棚の定位置、台車置場、仕掛品置場等のほか、作業台の上にも線引きする。
一方これらの置場線は、改革・改善によって変わる可能性もあるので、アクリル板等の長持ちするものより、はがしやすいテーピングが適している。(写真3)
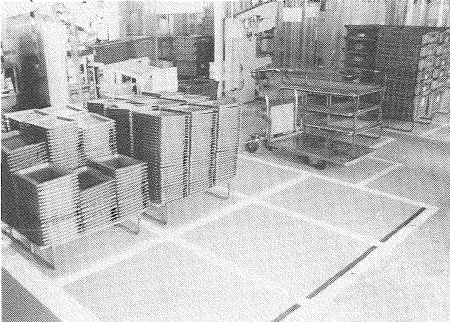
写真3 置場線
関連用語: ペンキ作戦
機械設備の稼働状況を示すアンドンのことをいう。通常、正常に稼働している時は緑色の「運転中」が点灯している。何らかの異常が起きると、作業者が現場監督者に知らせる"呼び出しボタン"を押し、黄色のアンドンが点灯する。さらにその異常の原因を表すボタンを押すと、それに該当する赤色のアンドンが点灯しラインが停止する。(図17)
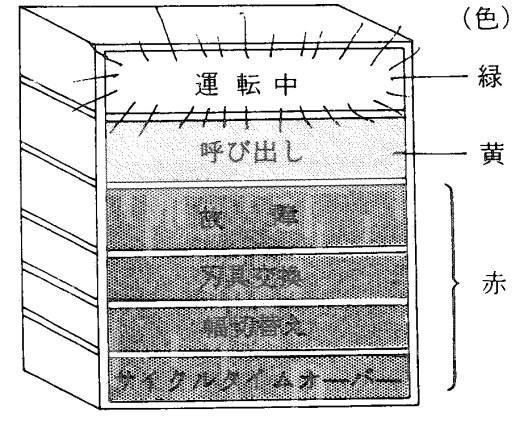
図17 稼働アンドン
JIT生産方式の機能の1つであり、ジャストインタイムを実現し維持するための道具として位置づけられる。一方そのシステムの特異さから「かんばん」だけが独り歩きし、JIT生産方式の代名詞ととらえられがちだが、これはあくまで俗称である。
「かんばん」は、物品目を表示する看板的機能と、その生産情報つまり作業指示を行う伝票的機能とをあわせもつ。よって置場表示である"漢字"の「看板」と区別し、"ひらがな"で表記する。従来の生産情報システムとしてはMRP、統計的在庫管理手法の発注点方式が上げられるが、いずれも安定需要下における予測法であり、情報だけが先行する傾向が見られる。もちろん情報源は"顧客の要求"であるが、工程・業者別に生産計画を立てるため、実際には各々の作業進度が異なり、滞留在庫や欠品等が発生する。また通常、前工程優先の「押し込み生産」の形をとり、たとえ需要変動があっても、一旦作成された生産計画によって造られた仕掛りは"ムダ"となって残る。
これに対し、かんばんでは後工程が"必要な物を、必要な時に、必要なだけ"前工程から引き取る「引っ張り生産」を原則とする。"顧客の要求"をもとにした生産計画によりまず最終工程が作業する。その造った分(引き取りかんばん)を前工程に"引き取り"情報として伝える。前工程は引き取られた分(仕掛けかんばん)だけ補充生産する。つまり後工程の作業進度により生産するため、常に生産計画=実績情報であり、"情報の流れ"と実際の"物の流れ"が一致することになる。
その各工程・業者間における情報交換の道具が「かんばん」で、必ず物についてまわる。いい換えれば「かんばん無しでは物を造れない・運べない」仕組みとなる。品目・数量・作業指示等が明記され、物の流れに沿って存在する。また「かんばんの在る所に"仕掛り"在り」といわれ、かんばん枚数はすなわち仕掛りの量であり、生産の現状を知り現場改革をする手がかりともなり「目で見る管理」としても有効である。
そしてかんばん1枚のロット数および枚数を最少限にし、発行・回収を細分化することが、計画変更に対応しJIT生産を維持する決め手となる。
ルールとしては、①後工程引き取り、②引き取り分前工程生産、③100%良品、④生産の平準化、⑤現物表示、⑥改革ニーズ発見の道具、の6つにまとめられる。
ちなみにかんばんはプレート形である必要はなく、箱、台車、等さまざまな形で応用できる。(図20)
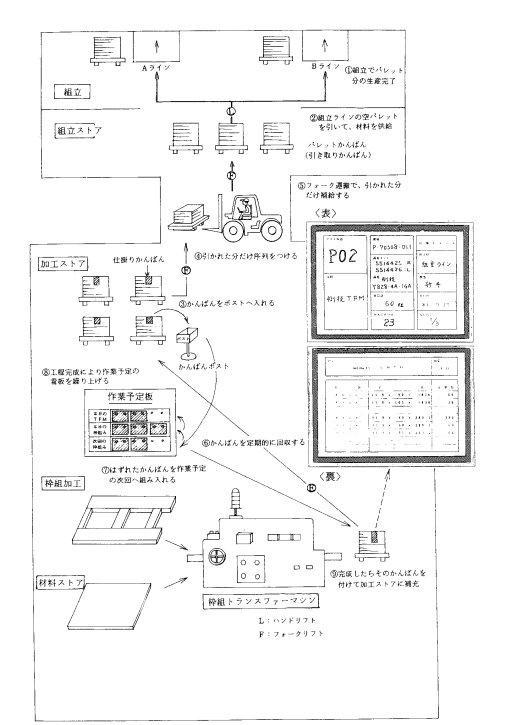
図20 組立と加工でのかんばん運用例
関連用語: 後工程はお客様
物を表示するための道具であり、5Sの看板作戦では、"どこに(場所表示)、何が(品目表示)、いくつ(量表示)"あるか、誰が見てもひと目でわかるように、物の置き方を標準化し、置場を整頓するために用いられる。むろん、生産活動に"要る物"が、その対象であり、もっとも効率よく"決められた場所に(定位)、決められた物を(定品)、決められた量だけ(定量)"の3定が原則となる。
看板の種類には、所表示・番地表示等の置場看板と棚品目表示・物品目表示、最大・最小量表示等があげられる。
またこの看板は"漢字"で書き、"ひらがな"の「かんばん」と区別する。「立て看板」「表示看板」「3定看板」とも呼ばれる。(写真5)
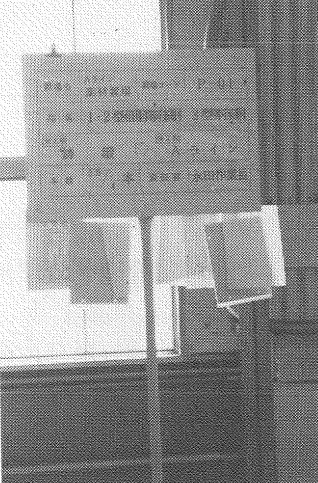
写真5 看板
必要最低限の在庫量。在庫は多過ぎても少な過ぎても生産に支障が生じる。最小在庫量を下回っていれば、補充をし常に適正在庫を維持しなくてはならない。またこの量表示は数字で表すよりも、置場や棚にテープや塗料で印をつけたりして、ひと目で識別できることが望ましい。
関連用語: 最大在庫
必要最大限の在庫量。過剰な在庫はムダの権化、適正在庫の最大在庫量を超えないような規制と表示は不可欠である。この量規制の方法としては、置場や棚の大きさ・スペースを制限すること、量表示には「赤ライン」等で印をつける色別整頓等があげられる。数字を書面で示すより、現場で即識別できるほうが在庫管理しやすい。
関連用語: 最小在庫
不良再発防止のために、不良現品を"みせしめ"にすることをいう。計数による品質管理では、数字と原因をグラフで表す、不良パレート図が作成されるが、この項目・層別ごとに現品を添えて展示する。問題を顕在化する「目で見る管理」の1方法である。(図59)
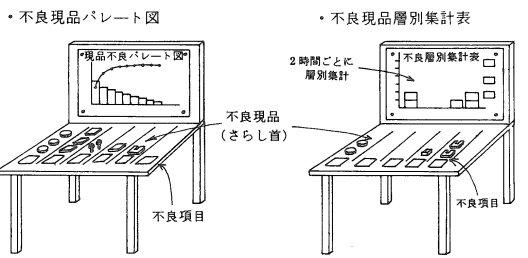
図59 さらし首
作業進度を把握するためのアンドンで、比較的タクトが長い組立工程で用いられる。作業の進行過程を何等分(通常10等分)かにし、順にNo.をつけ、アンドンとそのNo.とを対応させる。No.1の作業を進行中の場合は、No.1のアンドンが点灯する。これにはもちろん、"同じ動作で、同じ時間に、同じ品質の物を造れる"という標準化が前提にある。
またコンベアラインの進度No.の切り替え検知には"リミットスイッチ"が用いられ、手渡しラインでは"タイマー"が使用される。(図68)
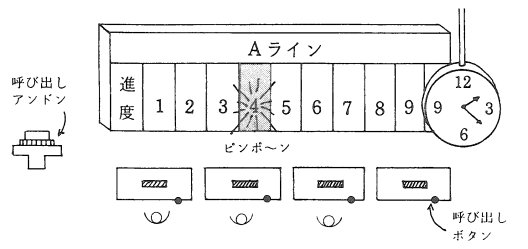
図68 手渡しラインの進度アンドン
ラインにおける稼働状況を知らせるための表示板で、生産予定数・実績数とその比率のほか、ライン停止の原因、改革対策、生産計画への影響などを1時間単位で記入する。
標準化した計画数量を維持し、たとえ作業遅れが生じても即対策を講じるためには、常に生産状況を把握しなければならない。この場合、目で見る生産状況である「生産管理板」は有効である。またこれは管理部門よりも、実際の作業現場に置かれる(通常、ラインの最終工程)。(図75)
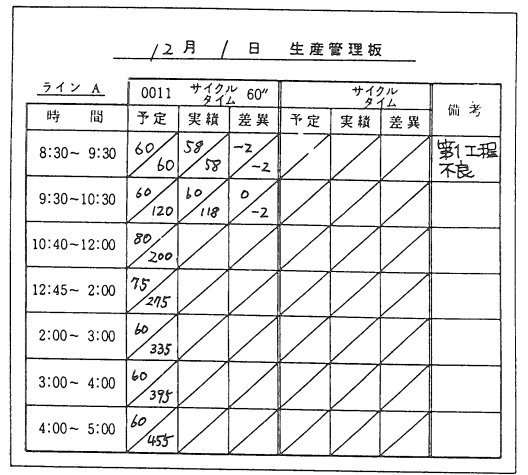
図75 生産管理板
工場内のスペースを有効に使うためには、スムーズな物の流れを考慮した各場所の位置決めをし、かつ安全が確保されていなくてはならない。その規制手段として用いられるのが、「線引き」である。一般の道路に見られるように、スペースに"線を引く"ことで表示する。通路と作業区を分ける「区画線」、扉の「開閉線」、通行の流れを示す「方向線」、置き場所を区分けする「置場線」、危険信号の「タイガーマーク」等があげられる。
また「線引き」には通常ペンキを用いることから、「ペンキ作戦」と呼ばれる。また、テープを貼ったり、アクリル板を線状に切り接着したりする。色については、はっきりとわかるように目立つものが望ましく、黄線や白線が適する。幅は5~10cmぐらい。(図87)
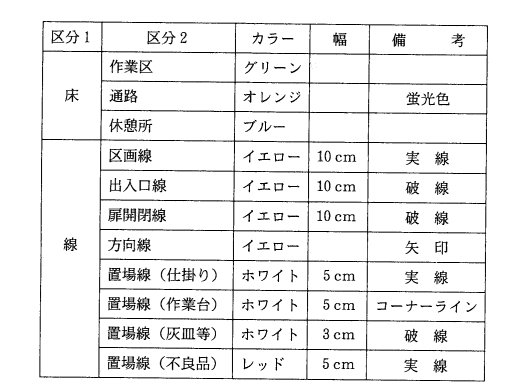
図87 ペンキ作戦での線引き例
漢字の「看板」のことで、「表示看板」とか「3定看板」ともいう。看板とは物の表示であり、またそれが誰でもひと目で見てわかるように置かれなくてはならない。そこで"看板を立てて"置くことから、こう呼ばれる。(写真22)
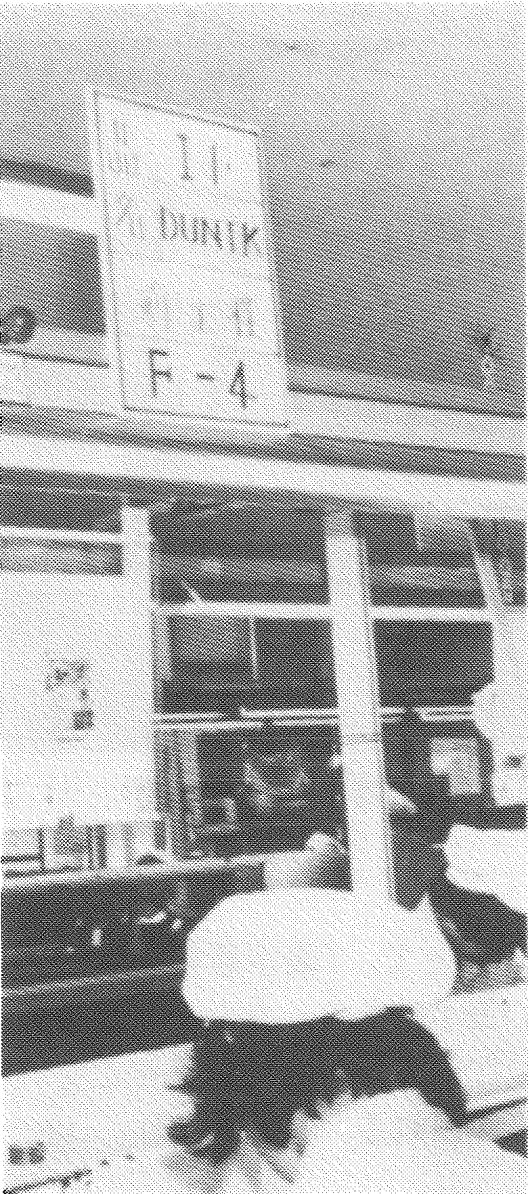
写真22 工程表示立て看板
通行時の安全とスムーズな人・物の流れを維持するために、通路に矢印のマークで示される。通路は"右側通行""左側通行"どちらでもよいが、一般には左側通行が多い。(写真24)
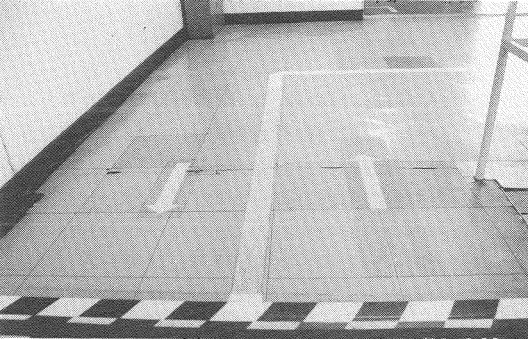
写真24 通行線
関連用語: 方向線
比較的短い組立ラインでよく使われるアンドンの方法に「飛行機方式」がある。スチュワーデスを呼び出すコール・ボタンと類似することからこう呼ばれる。仕組みは次のとおり。
部品請求やトラブルが発生した工程で作業者が呼び出しボタンを押すと、水すまし、現場監督者に知らせるラインアンドン(タクシー方式)とその座席を示す工程アンドン(ハイヤー方式)が点灯する(通常、黄色)。引き続きライン停止ボタンを押すと、ラインストップを意味する赤色のアンドンが点灯する。対処が完了すればアンドンは消される。
関連用語: 異常アンドン
5Sは一般に赤札作戦から始める。まず、日々の生産活動に不必要な物を現場から追い出し、本当に必要な物だけを現場に残す。そして、これら必要な物を使いやすい形で配置し、物の表示をハッキリさせるために看板作戦を行う。
この看板作戦とほぼ同時期に、床や通路を明確にするために実施されるのがペンキ作戦である。
まず、工場を大きく"歩く場所"と"作業する場所"の区分けをする。前者を「通路」、後者を「作業区」と呼ぶ。この通路と作業区をハッキリ分ける線のことを「区画線」といい、分ける線や位置の線等、線を引くことを「線引き」という。
通路と作業区を分ける区画線が最初の線引きとなる。いきなり線引きする前に、まず作業区の位置決め、通路の確保をしなければならない。
作業区は、U字ライン作業での作業性を考慮し、かつ部品の位置等も考えて位置決めをする。また、通路は安全性を第一とし、かつ部品供給がスムーズに行えるよう配慮する。
よく床面が凸凹で、レベル出しができていない工場を見かけるが、この際、床面の補修工事をして、レベル出しくらいはきちんとできるようにしなければならない。
通路は、作業区の位置決めにもよるが、曲げたり、コーナーが多過ぎるのはなるべく避ける。折れたり曲がったりすると必ず衝突事故が発生する。とくにフォーク運搬をする工場では、レイアウト時に十分考慮する必要がある。
線引きは、一般にペンキを用いるが、テープやアクリル板でもよい。とくにアクリル板は、大板を購入してライン幅に切り、裏に接着剤をつけて区画線に使用するとペンキのようにはげたりせず、テープのようにはがれず、かつ水ぶきで簡単に元のきれいな色に戻る。しかも値段が安いというメリットもあるので、今後の区画線の材料の主役となりうる。
色については、通路や区画線は暗くなってもハッキリして、かつ浮かび上がるような色がよい。そこで、①作業区...グリーン、②通路...オレンジ(蛍光色)、③区画線...イエローとするとよい。
また、区画線の幅は5~10cmとする。3cmでは心細いし、普通の工場で15cmはでしゃばりすぎる。一般には7cmがよく使われる。
半導体のような小物を扱う屋内の工場では、5cmもしくは7cmとし、重機のような大物を扱う屋外的工場では、クレーン等からでもハッキリわかるように少し太目の15cmとする。こうして引かれた区画線は、重機工場等では命を守る"命線"となる。そこで、合わせて「命線を踏まない横切らない運動」を展開するとよい。
また、各自の工場で、線引きについての標準を決めるのも方策だ。通路を歩いていて、急に扉やドアが開いて、ぶつかりそうになった経験を持つ人も多いはず。これもKY(危険予知)の安全性重視から、破線で扉の開閉線を引き、歩行者に注意を呼びかけるのもペンキ作戦の工夫の1つである。
部品供給係のことをいう。置場と工程間を、部品を運搬して回ることから、水上を旋回する“水すまし”にたとえられる。
目で見る管理の道具の1つでミスゼロをうながすための作業者の自主管理板のことをいう。
普通、縦軸を時間、横軸を日付とし表を作成。1時間単位で後工程から不良やミスに関する情報を受け、その結果を作業者自身が表に印をつける。これを1ヵ月続け、月例会等で先月のデータと比較し、翌月の目標を立てる。(図137)
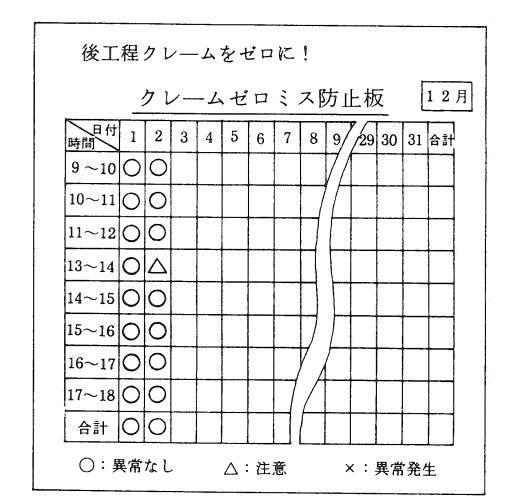
図137 ミス防止板
"目(視覚)"により正常・異常がわかる仕組みで問題を顕在化させる「目で見る管理」に対して、"耳(聴覚)"にうったえて、問題を明らかにし対処できるようにした仕組みを「耳で聞く管理」という。
たとえば、組立ラインでピッチを守るためのリズムづくりに用いられる「ピッチブザー」や「ピッチ音」、検査の良否の判定に使う「検査ブザー」や「検査音」があげられる。
関連用語: 目で見る管理