目で見る管理の最近のブログ記事
棚や置場における物の“整頓”方法の1つで、在庫や仕掛りの必要最低量・最大量がわかるように、壁等に赤のテープや塗料で印をつける。これを赤ラインという。この表示により、ひと目で不足か過剰かが識別可能となる。看板作戦の量表示の一環でもある。
"どこに、何を、いくつ"置くかを記入した看板で、各置場に掲示される。看板作戦の"場所表示"の1つ。工程間の仕掛置場はもちろん、外注業者が納入する際にも目印となる。(図9)
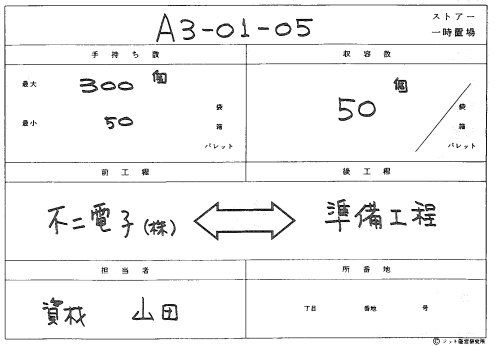
図9 ●記入例『ジャストインタイム生産革命指導マニュアル』、p.660より
物の置き場所を明示かつ区分けするために引く。
在庫品や治工具類等の置場における品目別の区分け、棚の定位置、台車置場、仕掛品置場等のほか、作業台の上にも線引きする。
一方これらの置場線は、改革・改善によって変わる可能性もあるので、アクリル板等の長持ちするものより、はがしやすいテーピングが適している。(写真3)
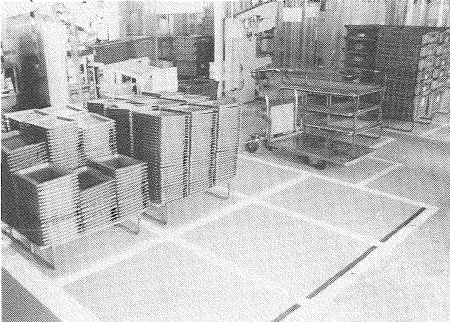
写真3 置場線
関連用語: ペンキ作戦
機械設備の稼働状況を示すアンドンのことをいう。通常、正常に稼働している時は緑色の「運転中」が点灯している。何らかの異常が起きると、作業者が現場監督者に知らせる"呼び出しボタン"を押し、黄色のアンドンが点灯する。さらにその異常の原因を表すボタンを押すと、それに該当する赤色のアンドンが点灯しラインが停止する。(図17)
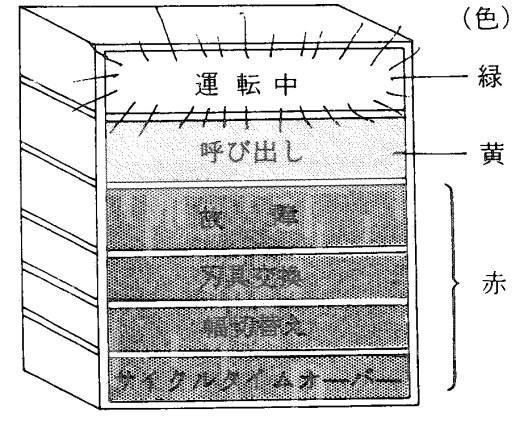
図17 稼働アンドン
JIT生産方式の機能の1つであり、ジャストインタイムを実現し維持するための道具として位置づけられる。一方そのシステムの特異さから「かんばん」だけが独り歩きし、JIT生産方式の代名詞ととらえられがちだが、これはあくまで俗称である。
「かんばん」は、物品目を表示する看板的機能と、その生産情報つまり作業指示を行う伝票的機能とをあわせもつ。よって置場表示である"漢字"の「看板」と区別し、"ひらがな"で表記する。従来の生産情報システムとしてはMRP、統計的在庫管理手法の発注点方式が上げられるが、いずれも安定需要下における予測法であり、情報だけが先行する傾向が見られる。もちろん情報源は"顧客の要求"であるが、工程・業者別に生産計画を立てるため、実際には各々の作業進度が異なり、滞留在庫や欠品等が発生する。また通常、前工程優先の「押し込み生産」の形をとり、たとえ需要変動があっても、一旦作成された生産計画によって造られた仕掛りは"ムダ"となって残る。
これに対し、かんばんでは後工程が"必要な物を、必要な時に、必要なだけ"前工程から引き取る「引っ張り生産」を原則とする。"顧客の要求"をもとにした生産計画によりまず最終工程が作業する。その造った分(引き取りかんばん)を前工程に"引き取り"情報として伝える。前工程は引き取られた分(仕掛けかんばん)だけ補充生産する。つまり後工程の作業進度により生産するため、常に生産計画=実績情報であり、"情報の流れ"と実際の"物の流れ"が一致することになる。
その各工程・業者間における情報交換の道具が「かんばん」で、必ず物についてまわる。いい換えれば「かんばん無しでは物を造れない・運べない」仕組みとなる。品目・数量・作業指示等が明記され、物の流れに沿って存在する。また「かんばんの在る所に"仕掛り"在り」といわれ、かんばん枚数はすなわち仕掛りの量であり、生産の現状を知り現場改革をする手がかりともなり「目で見る管理」としても有効である。
そしてかんばん1枚のロット数および枚数を最少限にし、発行・回収を細分化することが、計画変更に対応しJIT生産を維持する決め手となる。
ルールとしては、①後工程引き取り、②引き取り分前工程生産、③100%良品、④生産の平準化、⑤現物表示、⑥改革ニーズ発見の道具、の6つにまとめられる。
ちなみにかんばんはプレート形である必要はなく、箱、台車、等さまざまな形で応用できる。(図20)
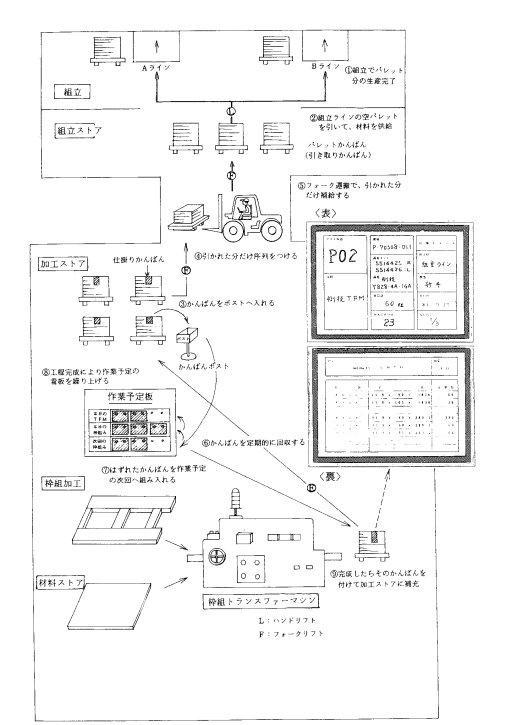
図20 組立と加工でのかんばん運用例
関連用語: 後工程はお客様
物を表示するための道具であり、5Sの看板作戦では、"どこに(場所表示)、何が(品目表示)、いくつ(量表示)"あるか、誰が見てもひと目でわかるように、物の置き方を標準化し、置場を整頓するために用いられる。むろん、生産活動に"要る物"が、その対象であり、もっとも効率よく"決められた場所に(定位)、決められた物を(定品)、決められた量だけ(定量)"の3定が原則となる。
看板の種類には、所表示・番地表示等の置場看板と棚品目表示・物品目表示、最大・最小量表示等があげられる。
またこの看板は"漢字"で書き、"ひらがな"の「かんばん」と区別する。「立て看板」「表示看板」「3定看板」とも呼ばれる。(写真5)
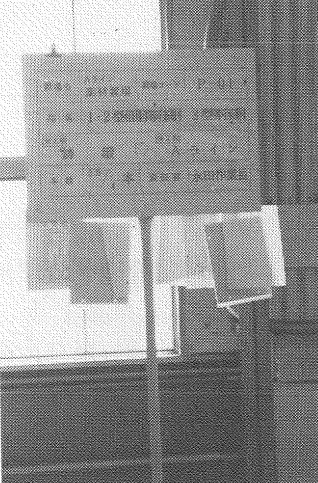
写真5 看板