ペンキ作戦における"線引き"の1種で、危険地区に注意をうながすためのもの。通常、黄色と黒の斜め線を交互に引くことから、「虎マーク」とか「タイガーマーク」と呼ばれる。
通路に機械の一部がはみ出ていたり、パイプが横切っている箇所や、エレベータの昇降口や階段の第1段目等につけられる。
作業者がひと目で感知できる「目で見る整頓」であると同時に、安全管理における危険予知の面でも重要である。(図88)
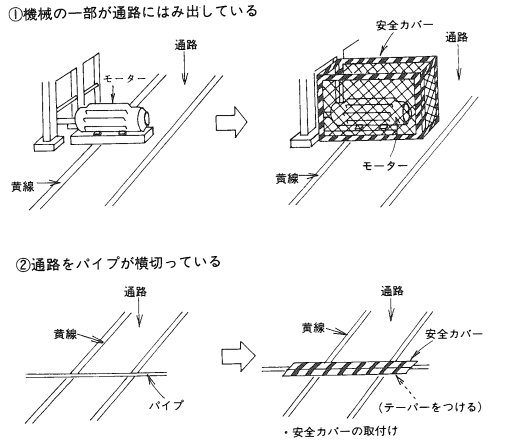
図88 タイガーマーク
関連用語: ペンキ作戦
ペンキ作戦における"線引き"の1種で、危険地区に注意をうながすためのもの。通常、黄色と黒の斜め線を交互に引くことから、「虎マーク」とか「タイガーマーク」と呼ばれる。
通路に機械の一部がはみ出ていたり、パイプが横切っている箇所や、エレベータの昇降口や階段の第1段目等につけられる。
作業者がひと目で感知できる「目で見る整頓」であると同時に、安全管理における危険予知の面でも重要である。(図88)
図88 タイガーマーク
関連用語: ペンキ作戦
定期的にもしくはあまり生産・出荷されない品目で、長期間使われず保管されることから、休眠部品、眠り在庫、スリーピングストックとも呼ばれる。季節製品に用いる部品や、特注部品、高額部品、サービス部品等がこれにあたる。ただし、使用頻度によっては通常の生産活動において不要在庫品とされ、現場から離して置場を設ける。
なお、不要在庫品の中でも再使用不可の死蔵品とは区別し対処する。
関連用語: 死蔵品
品種や工程内容が変わる際生じる段取り作業のことをいう。プレスの金型、成形やドリル等の治工具の取り替え、精密切削加工や化学装置の基準調整、変更それに組立部品や部材の切り替え、製造前の作業内容確認や掃除もこれに含まれる。
段取り替えは、従来熟練技能者が時間をかけて行うものという固定観念があって、その煩わしさからまとめて造ろうとするダンゴ生産に陥ってしまう傾向がある。しかし、この作業に要する時間の短縮や工数の低減、作業の標準化等の"段取り改革・改善"はJIT実現の決め手にもなっている。
以下がその手順とポイントである。
①段取り作業の分析
段取りの仕組みを明らかにする→段取り替え実績表、段取り作業分析表→オモテ化
②段取り替えのムダ取り
段取り作業は通常、「内段取り」「外段取り」「ムダ」の3つに分けられる→ムダ取り
③内段取りの外段取り化
④内段取り改革・改善→カセット方式、ボルトレス、並列段取り替え
⑤外段取り改革・改善→専用台車化、段取り工の設定、5Sのうち整理・整頓
段取り改革・改善の第一歩は現状の段取り作業を把握することから始まる。その分析内容を明記したものを「段取り作業分析表」という。個々の作業者の作業内容をできるだけ詳細に記入する。1つの作業に対して、改革案が複数になるようでは分析が甘い。ここでキーポイントとなるのは、段取り区分の分類である。「内取り」か、「外段取り」か、それとも「ムダ」か。区分を明確にすれば、改革内容も具体的に展開しやすい。たとえば、「ムダ」→「ムダ取り」、「内段取り」→「外段取り化」「ボルトレス」「カセット方式」「並列作業」等、「外段取り」→「5S」「専用台車化」「段取り工の設定」等。
さらに複数作業者の作業関連を観るためには「公開段取り時間表」を作成し、職場全体の段取り作業の改革を行う。(図93)
図93 ●記入例『ジャストインタイム生産革命指導マニュアル』、p.690より
看板掲示のあり方。とくに場所表示では、通路に対して直角に掲示するこの方法がとられる。看板が視界に入りやすく、置場を探すムダを最少限にする。
学校のクラス表示看板はその例。(図96)
図96 直角掲示
関連用語: 並行掲示
陳列とは、ただ単に、物が見た目に“きれい”に並べられていること。一見、整頓が行き届いているように見えるが、それだけでは、真の整頓とはいえない。
通行時の安全とスムーズな人・物の流れを維持するために、通路に矢印のマークで示される。通路は"右側通行""左側通行"どちらでもよいが、一般には左側通行が多い。(写真24)
写真24 通行線
関連用語: 方向線
治工具整頓の進化論の中で、最高に進展した段階を指す。治工具を使わなくてよい整頓。つまり、整頓そのものをなくしてしまうことである。
整頓をなくすための根源は、いま使っている治具や工具を使わないで、同じ作業ができる方法を考え出すこと。そのためには、「なぜ使っているのか」、そして「その治工具の本質的機能は何か」、さらに「その機能を満足させる他のやり方は...」等、治工具を使わなくてすむ方向で、いろいろ検討を加えること。そうすることによって、使っている治工具の本質機能が浮き彫りにされる。仮に"回す"ことが、その工具の機能だとしたら、工具を使わないで"回す"ことを考えてみる。そこでボルトやネジに、取手やハンドルの機能を付加すれば、工具を使わずに、しかも同じ機能が得られることになる。
もちろん、その前段として、治工具の共通化を図ってみるのも必要なことである。
治工具類を上から吊るして乱れない整頓を志向すること。つまり、治工具類を使用点の上にゴムやバランサーで吊るし、使い終わって手を離して一発で整頓を完了させる仕組みである。
使い終わった治工具は“戻る”という現象はあるが、人は“戻す”という行為をしていない。つまり、人の戻すという意識を取り去ってしまったので、乱れようがないということである。
ゼロ・ベース発想法に基づく7ゼロ生産の要素の1つ。
「変種変量生産」といういい方があるように、市場ニーズは日々めまぐるしく変化し、製造現場では"フレキシビリティ"=柔軟性が問われている。小回りが利く生産か否か、いい換えれば、"大よりも小""長よりも短"の中に利益を見い出す"スモールメリット"思考が求められている。
停滞ゼロは納期対応において"スモールメリット"を可能にする構想で、短納期化を目指し、その指標であるリードタイムの時間短縮を図る。
停滞とは、作業待ちの状態にある時をいい、運搬待ち、納入・出荷待ち、入出庫待ち、加工待ち、組立待ち、検査待ち等々、工場内には多くの停滞が蔓延している。また同時に「物を停めて置いておくこと」となり、物は在庫として存在する。在庫は概して欠品・納期遅れを避けるための問題解決策として正当化されるが、あくまで暫定的な改善であって、納期は厳守されるがまた欠品・遅れが再発しかねない。"待ち"はムダな時間の経過となり、結局リードタイムをむやみに長くし需要変動に対応できず、さらに過剰在庫を生み出す悪循環を招く。
「なぜ、物は停滞するのか。停滞がなくても、物は造れる」を信念に物の停滞時間をゼロにする。すなわち在庫ゼロにした物造りの必要最短時間、つまり時間のムダゼロ化を徹底し生産方法を組み直す。かつ納期遅れゼロであってこそ顧客の短納期ニーズに応える真のリードタイム、真の納期対応といえる。
そこで停滞ゼロはリードタイムの意識改革から始まる。
●リードタイムとロットは比例する→1個流し(→流動数曲線)
●顧客リードタイム=∑全部門(受注から納入まで)リードタイム→全社的推進
●製造リードタイム=∑正味加工時間
※正味加工時間(ワーク1個に付加価値をつけるのにかかる作業、加工着手から完成品になるまでの所要稼働時間)(→タクトタイム)
また受注後に製造する受注生産が前提であり、その低コスト化・短納期化が可能となる。ルール化としてはもちろん、5Sが基本となり、具体的仕組み作りは、図97に示したとおり。
こうした納期対応力は企業のもつ統合力にもつながる。自社内にとどまらず、外注・購入業者を巻き込んだ"体★たい★の改革"が望ましい。
図97 停滞ゼロへのアプローチ
改革前の姿と改革後の姿を、同一地点から写真撮影することをいい、具体的には、整理・整頓等の結果を定点撮影し、改革状態を確認することに活用される。
伝票を整頓する場合も、その基本事項はすべて文書と同様であるが、現在の会計制度では、伝票がそのまま帳簿の代替となり、その整理の仕方ひとつで会計業務に大きな影響を与える。このため、文書ニーズと伝票ニーズの違いを詳細に検討する必要がある。
〈違い1〉分類がより細かく、かつ一層の構造化が図れ、拡張性に富んでいる
〈違い2〉複写タイプのものが多く、紙質がやわらかく、薄いものが多い
〈違い3〉伝票は文書よりも流通性が大きく、一時保管といったことが頻繁に行われる
〈違い4〉流通性が大きいため、取り出しが正確にかつ迅速に行われる
〈違い5〉保管の完全性が要求される
以上のような伝票の特徴をとらえて、これに合った分類および保管方法を検討すればよい。その代表例に勘定科目別分類(図101)などがある。
図101 勘定科目別分類
また、一時的な保管で、枚数の少ない伝票はフォルダーを机上でファイルして保管し、多い場合はサイドキャビネットを脇に置いて、体のわずかな動きで取り出しができるようにするのも1つの方法である。
全国の土地のほとんどが、所と番地で表示され、誰でも地図でその場所を指し示すことができるように、物の置場の場所表示にもこの方法が適用される。
図102に示した場所表示法で見ると、AやBが所表示であり、これは工場でただ1つの名前となる。これに対して、1、2、3の縦の数字は番地表示である。このように、所番地をはっきり明示した工場では、新しく入ってきたパートの作業者に「A32の棚」と指定するだけで、目的の棚に行くことができるように、誰でも、目で見てわかるようにすることが大切となる。
図102 所番地表示
このような所番地による場所表示は、棚だけに使うだけではなく、倉庫や工場全体にもこの所番地(ロケーション)を適用するのが望ましい。とくに大物を扱う一品受注生産の工場では、棟内の所番地表示は必須となる。この棟内の所番地は、横と縦の所番地表示によって決まってくる。
全社的5S活動。「部品置場の看板は5Sのスタッフが作るものだ」、「5Sは5S推進チームの仕事なので…」等と各職場の人が考えているようでは、5Sの維持・発展は難しい。
まず、5Sは職場の1人ひとりが守り抜く気持ちをもつことがもっとも大切。全員実行型の5Sであり、トータル5S、つまりTQC的いい方をすれば“T5S”である。そして、次に各人の業務の中に5Sを染み込ませて“5Sのライン化”を図っていくことが肝要である。
工場革新に対する全社の意識の徹底、高揚のために有効な手段となる。できれば、社長なら年2回から4回ぐらい、工場長であれば毎月1回、現場の5S状況を巡視して歩く。この時、5Sや改革きっぷ等を渡し、気がついたことを指摘する。ただし、全般的に現場は5Sや改革活動を通してトップとコミュニケーションをもつことを期待しているので、話し合いを中心に巡回を行う。
1970年代以降、製造業市場は消費者中心のマーケットイン思考が主流で、さらに「売れる(売れた)物を造る時代」といえ、多品種少量生産がニーズとなっている。7ゼロ生産はその生き残り戦略・工場革命として、JIT生産を実現するためのもので、企業イノベーションの本質的発想転換を提言している。
従来のIE、提案制度、小集団活動、統計的品質管理等の手法は、あくまで現状を肯定したうえの分析で、部分的に"善★よ★く改める"いわば「改善アプローチ」の低減発想法となる。たとえば、大ロット生産を小ロット化するようなもので、"見かけの効率化"を施したにすぎない。これに対し、7ゼロ生産では、現状を全面的に否定し"革★あらた★に改める"「改革アプローチ」とし、JITの"徹底したムダ取り"を基本とする"ゼロ・ベース発想法"で企業の再構築を図る。具体的には次の要素があげられる。
①切り替えゼロ(Products)←多品種化
「なぜ、切り替えをするのか。切り替えなしでも物は造れる」
②在庫ゼロ(Inventory)←問題表面化
「なぜ、在庫がたまるのか。在庫なしでも物は造れる」
③ムダゼロ(Cost)←コスト削減
「付加価値以外はすべてムダ。ムダ作業なしで、物は造れる」
④不良ゼロ(Quality)←品質保証
「なぜ、不良が出るのか。製品は不良なしで、必ず造れる」
⑤故障ゼロ(Maintenance)←生産保全
「なぜ、お前は止まるのか。機械設備は故障なしで、働き続けられる」
⑥停滞ゼロ(Delivery)←短納期化
「なぜ、物は停滞するのか。停滞がなくても、物は造れる」
⑦災害ゼロ(Safety)←安全第一
「赤チン、唾つけ絶滅。事故・災害は、必ずなくせる」
ゆえに各々の頭文字をとり「PICQMDS(ピックエムディーエス)」とも呼ばれる。
手順としてはまず、これら7項目を問題として認識し、上記に表した言葉どおり「なぜ(WHY)」の疑問から"真因の追求"をし、意識改革していくことが第一歩。そして図105の「5つの指針」にある"流れ"を念頭に対策を練る。この際5Sが基礎となることはいうまでもない。
図105
また、改革の相乗効果をうながすためにも実績評価は欠かせない。トップダウンで全社的経営目標を設け、結果は部課別・ライン別、月または年次でその推移をグラフ化し掲示することも大切であり、さらなる課題の叩き台とする。その指標項目には「9つの指標」があげられる。(図106)
あとは"3現3即3徹"の行動あるのみ。
図106